Understand How Check Valves Work & What They Do
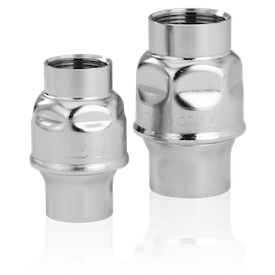
Figure 1: Check valve
A check valve allows liquid and air to flow in only one direction and prevents backflow. Check valves are inexpensive, effective, and easy solutions to the potential issues that a media backflow can cause. Backflow can cause serious issues like contamination of upstream media, damage to equipment, system inefficiency, increased maintenance costs, and regulatory compliance issues. For example, a sewer line will have a non-return valve to ensure that waste can leave a system (e.g., residential plumbing system) but cannot re-enter.
Table of contents
- How does a check valve work?
- Check valve types
- Check valve materials
- Selection criteria
- Applications
- Check valve symbols
- FAQs
View our online selection of check valves!
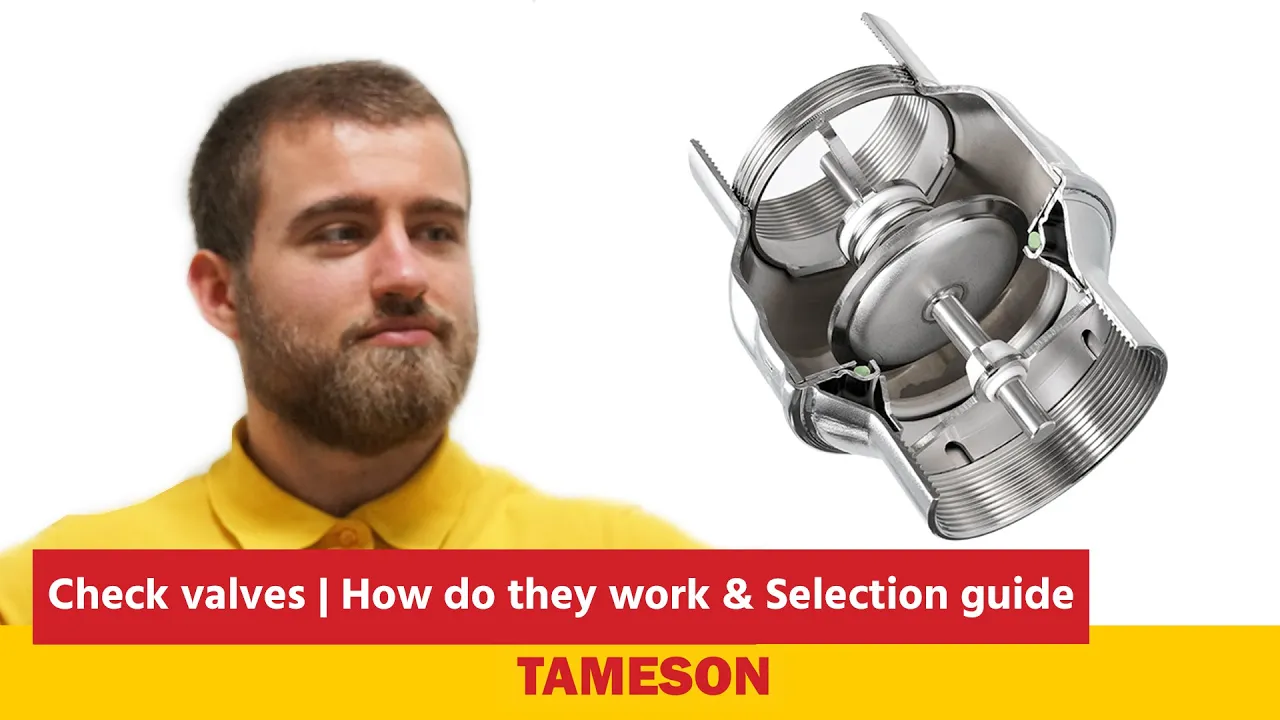
How does a check valve work?
Cracking pressure
A check valve requires a minimum pressure differential between the inlet and outlet to open, allowing media to flow through it. This minimum upstream pressure at which the valve opens is called the check valve's cracking pressure. The specific cracking pressure changes based on the valve design and size, so ensure that the system's pressure can generate the cracking pressure of the chosen check valve(s).
Closing
If the upstream pressure falls below the cracking pressure or there is back pressure (flow attempting to move from the outlet to the inlet), the one way check valve will close. Typically, check valves have a gate, ball, diaphragm, or disc pressed against a seal to close the valve and block flow. Gravity or a spring can assist in the closing process.
Installation orientation
As a one-way valve only allows flow in one direction, knowing the correct installation orientation is crucial. Typically, an arrow on the valve's housing indicates the flow direction. If there isn't an arrow, examine the valve to ensure it is installed in the intended flow direction. If the valve is installed backward, the media cannot move through the system, and the resulting pressure build-up can cause damage.
Normally open and normally closed check valves
A normally open check valve allows the medium to flow freely but shuts off the flow in case of backflow. A normally closed check valve prevents the flow of media through it until the cracking pressure builds up, at which point the valve opens.
Check valve types
There are various types of check valves, each designed to suit specific applications and optimize system performance. Below is a summary of the main types of check valves:
- Inline spring-loaded check valves: These valves use a spring mechanism to assist in closing. The spring ensures a quick response to changes in flow direction, minimizing backflow risk. They are compact, can be installed in any orientation, and are suitable for systems with low-pressure differentials.
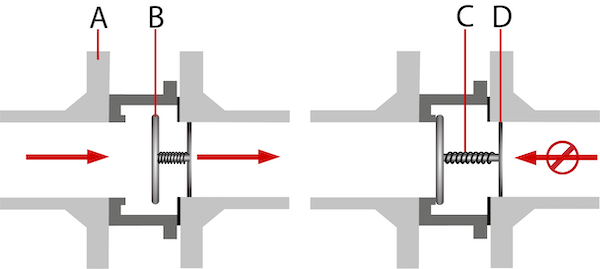
Figure 2: Spring-loaded in-line check valve open (left) and closed (right). The working components are the valve body (A), disc (B), spring (C), and guide (D).
- Swing check valves: Featuring a hinged disc that swings open with forward flow, these valves are simple in construction and suitable for large diameter pipes. They offer minimal flow resistance and a low pressure drop when fully open.
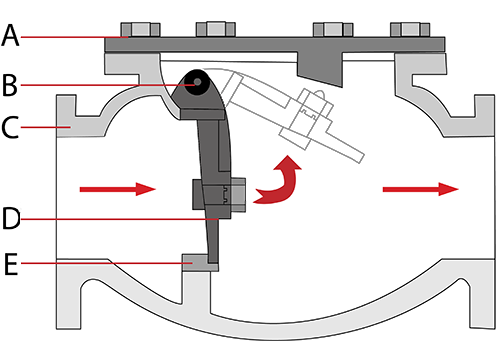
Figure 3: Swing check valve. Bolted bonnet (A), hinge or trunnion (B), valve body (C), disc (D), seal (E).
- Ball check valves: Utilizing a spherical ball as the closing mechanism, these valves are robust and self-cleaning. They can be installed vertically or horizontally, with gravity or a spring assisting in closing.
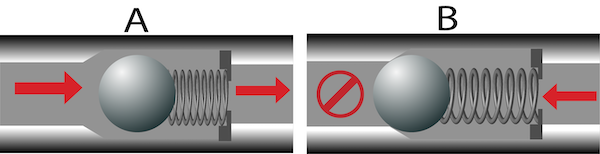
Figure 4: Spring-loaded ball check valve in the open position allowing flow (A), and in the closed position preventing backflow (B)
- Lift check valves: These valves have a disc or piston that lifts vertically to allow flow. They require horizontal installation for optimal performance and provide precise seating for enhanced sealing.
- Y-shape check valves: With an angled flow path resembling the letter "Y," these valves reduce turbulence and pressure drop, offering a more efficient flow compared to straight-through designs.
- Foot valves: Installed at the inlet of a suction line, foot valves prevent backflow and maintain pump prime. They include a strainer to filter debris and are available in various sizes to suit different systems.
- Sanitary check valves: Designed for applications requiring high hygiene levels, these valves feature smooth surfaces and minimal crevices to prevent contamination. They are commonly used in the food, beverage, pharmaceutical, and biotechnology industries.
Check valve materials
Stainless steel check valve
Stainless steel check valves are renowned for their superior resistance to corrosion, heat, and low temperatures, making them ideal for demanding environments. They exhibit excellent mechanical properties, including high strength and durability, contributing to their long service life. These valves are well-suited for applications involving high temperatures and pressures, such as in industrial processing, chemical plants, and oil and gas industries.
Stainless steel check valves are available in various grades, with 304 and 316 being the most common. Grade 316 stainless steel offers enhanced resistance to chlorides and other corrosive substances, making it suitable for marine and coastal applications.
While stainless steel check valves provide exceptional performance, they may not be the most cost-effective solution for applications that do not require such high durability or resistance. In such cases, alternative materials like PVC or brass may be more economical.
Key Features
- Corrosion resistance: Excellent resistance to a wide range of corrosive media, including acids, alkalis, and chlorides. See our chemical resistance guide to learn more.
- Temperature tolerance: Capable of withstanding extreme temperatures, both high and low from -25 °C to 200 °C (-13 °F to 392 °F).
- Mechanical strength: High strength and durability, suitable for high-pressure applications up to 64 bar (928 psi).
- Versatility: Available in various grades to meet specific application requirements.
Applications
- Industrial processing
- Chemical plants
- Oil and gas industries
- Marine and coastal environments
- High-temperature and high-pressure systems
PVC (Polyvinyl Chloride) check valve
PVC check valves are frequently used in irrigation and water management systems. They are corrosion-resistant to most corrosive media like seawater, acids, bases, chloride solutions, and organic solvents. However, they are not immune to aromatic and chlorinated hydrocarbons and typically have a max temperature resistance of around 60 °C (140 °F).
Key features
- Corrosion resistance: Excellent resistance to a wide range of corrosive media, including seawater, acids, bases, and chloride solutions.
- Temperature tolerance: Capable of withstanding temperatures up to 60 °C (140°F).
- Mechanical strength: Adequate strength for low to moderate pressure applications.
- Versatility: Suitable for a variety of water management and irrigation systems.
Applications
- Irrigation systems
- Water management systems
- Chemical processing involving non-aromatic and non-chlorinated hydrocarbons
- Wastewater treatment
Brass check valve
Brass check valves are excellent for air, water, oil, or fuel applications. However, they are not resistant to seawater, purified water, or chlorinated water. Compared to stainless steel, brass is less resistant to heat and corrosion and is typically used for applications with low pressure.
Key features
- Corrosion resistance: Moderate resistance to corrosion, but not suitable for seawater, purified water, or chlorinated water.
- Temperature tolerance: Limited temperature tolerance, generally suitable for low-temperature applications.
- Mechanical strength: Adequate strength for low-pressure applications.
- Versatility: Suitable for a variety of applications involving air, water, oil, or fuel.
Applications
- Low-pressure systems
- Domestic water systems
- Fuel lines
- Air compressors
Selection criteria
Check valves have the following criteria to consider when selecting one for an application:
- Material compatibility with the medium
- Line size for connection points
- Max pressure and cracking pressure requirement
- Installation orientation horizontal or vertical
- Envelope dimensions
- Accessibility needs for inspections and repairs
- Temperature (external and media)
Applications
Due to how check valves function, they are typically used for one of four different reasons in various applications:
- To protect equipment downstream from backflow damage
- To prevent contamination due to reverse flow
- To prevent siphoning
- To keep a vacuum seal
Due to their function, they are used in almost every industry. They are used on common household appliances, like dishwashers, washing machines, and wastewater lines. For industrial purposes, they are used on boilers, furnaces, gas systems, pumping applications, or vacuum systems. They are also frequently used as aquarium check valves on water and CO2 lines. Also, a miniature check valve is a popular choice where the space is limited, yet a reliable operation is essential. Two of the most common check valve applications are for water and air, which are discussed in more depth below.
Check valves for water
A water check valve is used in numerous water applications, like drinking water and wastewater. These valves are simply called one-way water valves. Plumbing check valves for drinking water applications ensure that no environmental media (outlet side of the valve) can enter the system with the safe, clean drinking water and contaminate it. For wastewater applications, they ensure that the wastewater cannot re-enter the system and cause an overflow or additional contamination. For water pumping applications, a foot valve is often used to ensure no debris enters the line and keep internal pressure for priming purposes. Sump pump check valves ensure that the discharged water does not come back into the sump pump with gravity when the pump is turned off.
Pneumatic check valve
A pneumatic check valve, or air check valve, allows airflow and prevents it from going out. They are often simply called one-way air valves. The most common application is for an air compressor. A pneumatic check valve allows the compressor to keep certain parts pressurized and other parts de-pressurized. They can be located on an air receiver, discharge pipe, or as a piston check valve on the piston compressor's inlet and outlet sides.
Check valve symbols
The P&ID symbol for check valves is shown in Figure 5.
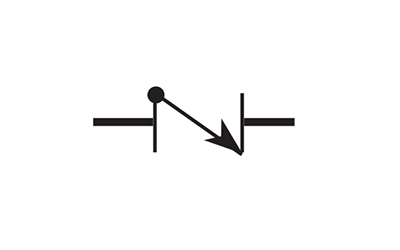
Figure 5: The check valve P&ID symbol points in the orientation that it allows the flow with a vertical line showing it doesn’t allow backflow.
Learn about other types of valves in our valve fundamentals article.
FAQs
What is a check valve?
A check valve is a unidirectional valve that passes fluid in one direction but prevents any flow in the opposite direction.
What is the purpose of a check valve?
The main purpose of a check valve in a system is to prevent backflow, which could damage equipment or contaminate media upstream.
What are common check valve problems?
Common check valve problems are noise, water hammer, vibration, reverse flow, sticking, leakage, and component wear/damage.
Will a check valve stop water hammer?
A check valve can prevent water hammer if it is fast-acting like a spring-actuated check valve. This prevents pressure surges, which create shock waves throughout the media.