Check Valve Applications
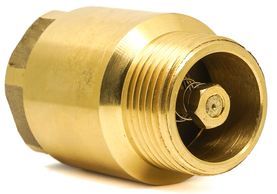
Figure 1: Check valve
Check valves, also known as non-return valves, are used to prevent the backflow of fluid in a pipeline. These valves are commonly installed in the operations where a fluid backflow can cause damage to the system making it inoperative. This article discusses the general applications of check valves.
Table of contents
- Check valve purpose
- Gas and oil check valve
- Check valves for standard devices
- HVAC check valves
- Steam check valves
- Sanitary check valves
View our online selection of check valves!
Check valve purpose
Check valves prevent backflow and ensure that the fluid flows only in one direction as seen in our youtube guide below. These valves are used for several reasons, including:
- Protection of equipment that can be affected by backflow, like strainers, flow meters, and control valves
- Checking pressure surges associated with hydraulic forces (like water hammer).
There are different types of check valves, each suited for specific applications. Common check valve applications are discussed in this article.
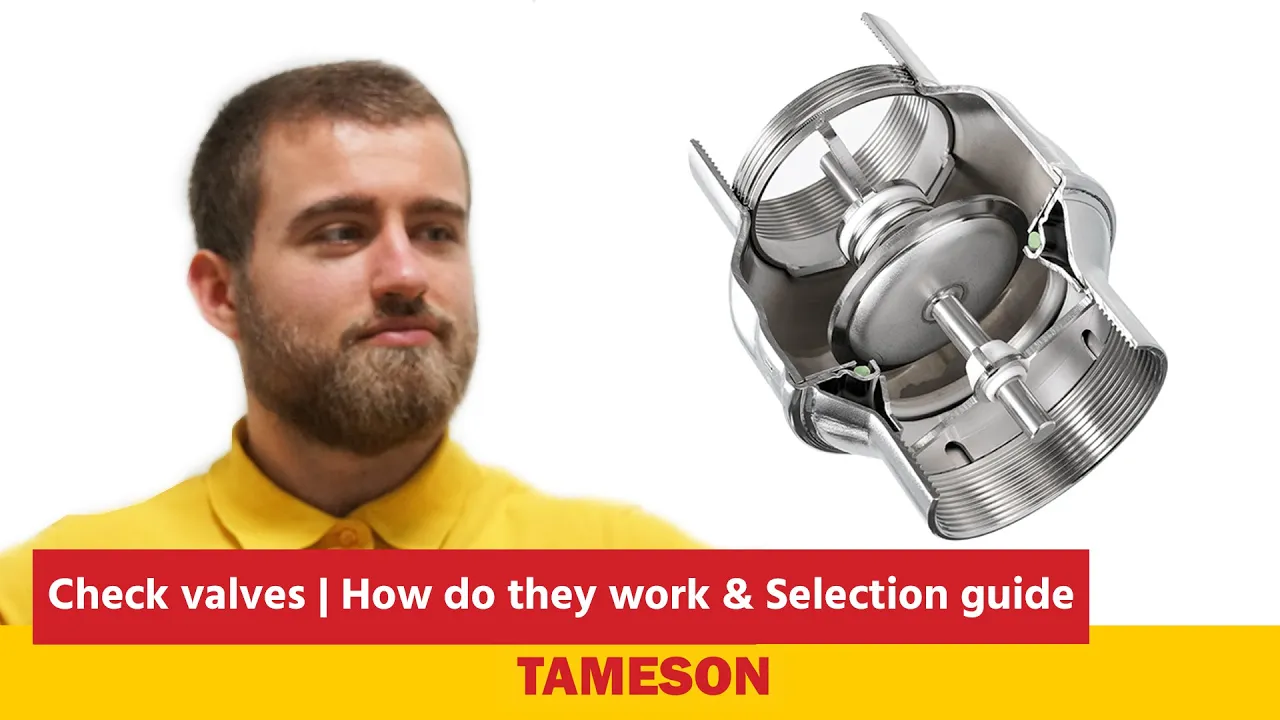
Gas and oil check valve
Millions of people worldwide depend on gas for commercial and residential energy requirements. Gas transmission networks consist of several interconnected systems like distribution pipelines, compressor and metering stations, storage facilities, and several other applications. Improper gas flow can lead to potentially hazardous problems like gas contamination, leakage, or even fires and explosions. Gas transmission specialists check valves regularly to bring down the occurrence of these problems.
One main application of check valves in the gas transmission field is compressor discharge. Reciprocating compressors are often used to move gas efficiently over long distances through pipelines. This flow must only be in one direction; hence check valves are designed into the pipeline systems to prevent the reverse flow. Other applications of check valves in the gas industry include:
- Hydraulic lines
- Airlines
- Pump discharge
- Pressure letdown
- Metering pumps and,
- Compressor inlet and discharge
Check valves are also used to prevent the backflow of fuel and oil in chemical plants. For maximum life and performance of the valve, choose materials like brass, aluminum, steel, or cast iron for the body and nitrile rubber for the sealing.
Read our article on oil and gas check valves to learn more.
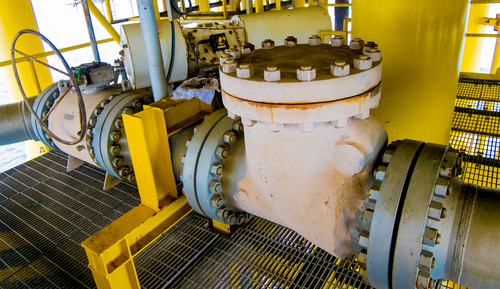
Figure 2: Check valve used in the oil and gas industry
Check valves for standard devices
The materials used for check valves for common equipment involving water like a washing machine, dishwasher, sinks, or fish tanks should be compliant with water. PVC, brass, or stainless steel can be chosen for the valve body parts and EPDM or PTFE for the seal material. Read our chemical resistance guide article for more details on the compatibility of materials with different media.
Washing machine check valve
A check valve is used in a washing machine to protect the drainage system from returning wastewater from the sewer back into the washing machine tank. This problem arises especially if the machine is not connected correctly to the sewer that causes the wastewater to enter the tank, spoil the laundry, and also increase the energy consumption significantly. A dishwasher check valve also performs the same function preventing the backflow of dirty water back into the dishwasher if the drain is clogged.
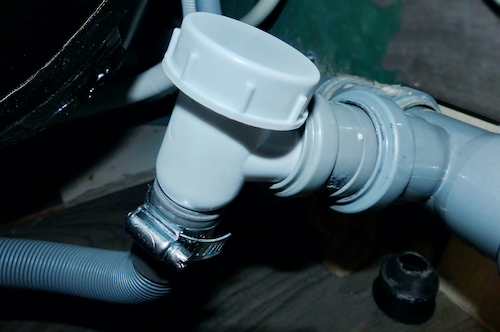
Figure 3: A check valve used for machine machines prevents the siphon effect.
Fish tank check valves
A check valve allows air to flow into the fish tank but prevents water from flowing in the opposite direction (out of the tank). This prevents water from siphoning out of the fish tank if the air pump stops running during a power failure. Water leakage from the airline tube can damage the air pump, flood the floor, or even lead to an electrical fire if the power strips sit in water.
Floor drain, sink, and hot tubs check valves
Floor drains are designed to efficiently direct water to a sewer or a municipal drain so that the floor stays dry and doesn’t flood. Check valves are usually used to seal off sewer water backing up the floor in case of an overloaded sewer. Water flows down through the drain once the sewer water begins to recede.
Sink check valves prevent the backflow of dirty water back into the sink from the sewer. Check valve sare also used when the level in a swimming pool changes. Hot tub check valves prevent water from flowing back into the swimming pool from the hot tub. Read our article on pool valves for more details.
HVAC check valves
An HVAC (Heating, ventilation, air conditioning) system provides a set of environmental conditions, which can be for residential or industrial purposes like a manufacturing process. Hence the system regulates room temperature, humidity, and air quality, thus providing comfortable working conditions within an industry.
The basic principle of air conditioning is to remove heat from one area, replace it with chilled air, and expel the hot, dry air into the atmosphere. A special fluid known as a refrigerant or coolant is used to exchange heat. The refrigerant is the actual carrier or medium of heat exchange between the external environment and the internal components.
The main purpose of a check valve in an air conditioning system is to prevent the loss of the system’s cooling efficiency when the system stops functioning. When the compressor stops working, the high-pressure and high-temperature steam within the compressor may flow back into the evaporator, thus reducing the cooling efficiency of the system. A check valve ensures no backflow happens from the compressor to the evaporator. A refrigerant check valve is commonly used for large size and medium-sized air conditioning and refrigeration units. Read our article on solenoid valves for HVAC-R for an in-depth description of an air conditioning and refrigeration cycle.
Steam check valves
Lift check valves swing check valves, wafer check valves, and disk check valves are commonly used in steam, condensate, and liquid systems. Ball check valves, diaphragm check valves, and tiling disk check valves are mainly suitable for liquid media and may be used in condensate systems. Stainless steel is a popular choice for making the body of a check valve working on steam. The main applications of check valves involving steam are discussed below:
- Boiler feedlines: A check valve prevents boiler water from being forced back into the feedline and storage tank when the feed pump stops functioning. Also, a disk check valve with a soft seat and heavy-duty spring can be installed in a boiler feed line to prevent the flow under gravity when the feed pump is turned off.
- Steam traps: Check valves are inserted after a steam trap to prevent condensate backflow that can eventually flood the steam space. The check valve also controls the steam trap from being damaged by any possible hydraulic shocks along the condensate line.
- Hot water circuits: Check valves are installed after each pump to prevent backflow through the pump when it is turned off.
- Blending: A common blending application is mixing hot and cold water to yield blended water. A check valve should be installed on the hot water line and cold water lines to prevent the backflow along these lines, which can lead to water contamination.
- Pipeline fitting protection: Check valves are used to protect equipment like flow meters and control valves that can be potentially damaged by reverse flow. Check valves also prevent the contents of strainers from being settled in upstream pipework due to the effect of reverse flowing fluid.
- Multiple boiler applications: A check valve is installed at the outlet of each boiler to prevent steam from flowing into boilers that may be on hot standby.
- Blowdown-vessels: A wafer check valve is commonly installed on each blowdown line when a blowdown vessel obtains blowdown from more than one boiler. This blocks the blowdown from one boiler from flowing back into another.
- Flash vessels: A check valve is installed at a flash vessel’s flash steam outlet. This prevents the steam from any make-up valve from flowing back into the flash vessel. Check valves are also installed after steam traps that drain the flash vessel.
Sanitary check valves
Sanitary check valves are used In manufacturing processes involving high hygiene standards to prevent pipeline backflow contamination. Sanitary check valves differ from conventional check valves in their design and materials, and these valves are used for applications requiring clean and sterile processing. Stainless steel 304 or 316 is commonly used to design the sanitary check valve parts that come in direct contact with the medium. The seat is widely made of FDA-approved materials like EPDM, silicon, or Viton, and PTFE is used for unique seat designs. This is because stainless steel is non-toxic, corrosion-resistant, and the material does not leach into the medium it lets through. The common features of sanitary check valves are:
- Easy cleaning
- Crack-free, and,
- Polished contact surfaces.
Sanitary check valves are commonly used in food, dairy, pharmaceutical, medical, and chemical industries.
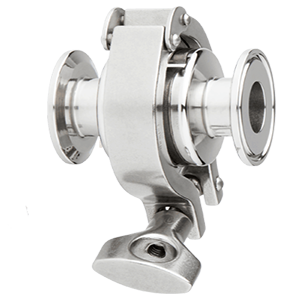
Figure 4: A stainless steel sanitary check valve.