Sanitary Check Valves
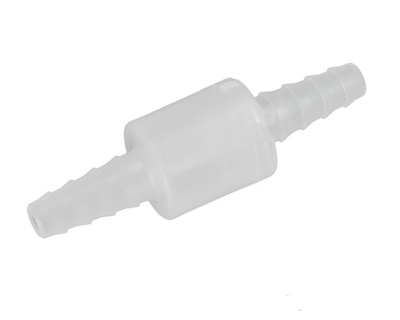
Figure 1: Polypropylene FDA-approved check valve
Sanitary check valves stop backflow, preventing cross contamination in manufacturing processes that need high hygiene standards. The primary differences between sanitary check valves and ordinary check valves lie in their design and materials.
- Sanitary check valves are specifically designed for applications that require clean or sterile processing. They are ideal for use in the dairy, food, pharmaceutical, medical, and chemical industries.
- These valves typically feature easy-to-clean, crevice-free, and polished contact surfaces. The components of the valve that come into contact with the medium are non-toxic and resistant to corrosion.
- Sanitary check valves are employed for various purposes, like evacuating process lines of residual products (often in conjunction with a pressurized air source), venting air from piping systems, and some models facilitating clean-in-place (CIP) operations.
View our online selection of check valves!
Sanitary spring check valves
Sanitary check valves are typically spring-loaded. Spring-loaded check valves incorporate a disc, ball, or shutter mechanism that halts fluid flow in a pipe. The spring mechanism assists in creating a positive shutoff by providing the necessary closing pressure. These valves are commonly used in process lines where maintaining a secure seal is essential. Read our check valve overview article for more information on the working, design, and types of check valves.
Selection criteria
- Material compatibility: Choose materials that are compatible with the fluids and chemicals present in the system. This ensures durability and prevents contamination. Common materials include stainless steel and specialized polymers like Polypropylene (PP) that meet sanitary standards. An electropolished finish (if present), eliminates microscopic imperfections for a hygienic design. Additionally, full material traceability, when available, allows tracking and documenting the origin, composition, and processing history of all materials used in the valve's construction.
- Connection type: Hose barb connections are commonly available for sanitary check valves. The connection ensures a secure fit with flexible tubing, making it easy to install and ideal for low-pressure systems.
- Industry standards: Ensure the valve complies with relevant industry standards and regulations. Common standards for sanitary applications are:
- FDA: The FDA ensures food safety and proper labeling in the U.S. For example, FDA 21 CFR 177.1520 specifies the regulations for olefin polymers, such as polyethylene and polypropylene, used in food contact applications.
- 3-A: 3-A sets sanitary design standards for food processing equipment.
- Operational temperature and pressure: Verify that the valve can withstand the operational temperature range and the system pressure to prevent material degradation and ensure reliable performance and prevent leaks or failures.
Applications
Sanitary check valves are commonly used in:
- Food and beverage processing: Food and beverage check valves prevent backflow and contamination by stopping fluids like coolants and cleaning agents from re-entering the production line. This ensures a smooth transition between processing stages and maintains high hygiene standards, safeguarding products.
- Pharmaceutical manufacturing: They ensure that fluids, such as cleaning agents and process solutions, do not re-enter the production line, maintaining sterile conditions.
- Chemical processing: In chemical processing, sanitary check valves are used to prevent backflow and contamination by ensuring that chemicals and process fluids do not re-enter upstream equipment or pipelines. This is critical for maintaining the purity of chemical reactions, preventing cross-contamination between different chemical batches, and protecting sensitive equipment from damage or corrosion caused by unintended fluid exposure.
Within these industries, sanitary check valves are commonly employed in:
- Condensate lines: To prevent backflow of condensate, ensuring efficient removal and preventing contamination of the steam system.
- Evaporators: To control the flow of fluids and prevent reverse flow, which could compromise the efficiency and safety of the evaporation process.
- Gas purges: To allow for the controlled release of gasses while preventing backflow, ensuring the integrity of the system and the safety of operations.
FAQ
Why are check valves on sanitary piping crucial in pharmaceutical manufacturing?
They maintain sterile conditions by preventing cleaning agents and process fluids from flowing back into the system.