Spring Loaded Check Valves Overview
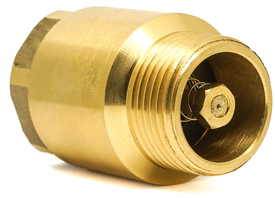
Figure 1: Spring check valve
Spring-loaded check valves prevent backflow, are relatively silent, minimize water hammer, and can be installed horizontally or vertically. This type of check valve has a relatively large disc that is closed by spring force. Spring-loaded check valves are chosen over other valve types because they have versatile installation (vertical and horizontal), minimize water hammer, and have exceptional sealing due to the spring force.
Advantages
- Versatility: With correct spring settings, spring check valves can be installed in any orientation. Spring check valves perform well in vertical piping locations. These valves depend on the spring’s potential energy to close the valve. Therefore, the valve closes independently without waiting for the fluid to force its way back into the piping.
- Ease of installation: Because of their versatility, spring-loaded check valves are more likely to fit in the system without rearranging pipe configurations.
- Noise control: If water hammer does occur, spring check valves are more able to diminish any disruptive noises. They are considered silent check valves.
- Sealing: With the spring’s support, check valves can fully seal without backflow.
Disadvantages
Spring-loaded check valves have a lower flow capacity than swing check valves due to the control disc blocking flow. Swing check valves have a wide open flow path. Learn more in our article swing check valves vs spring check valves.
Table of contents
- Spring loaded check valve components
- How does a spring check valve work?
- Installation guidelines
- Materials
- Selection criteria
- Advantages and disadvantages
- FAQs
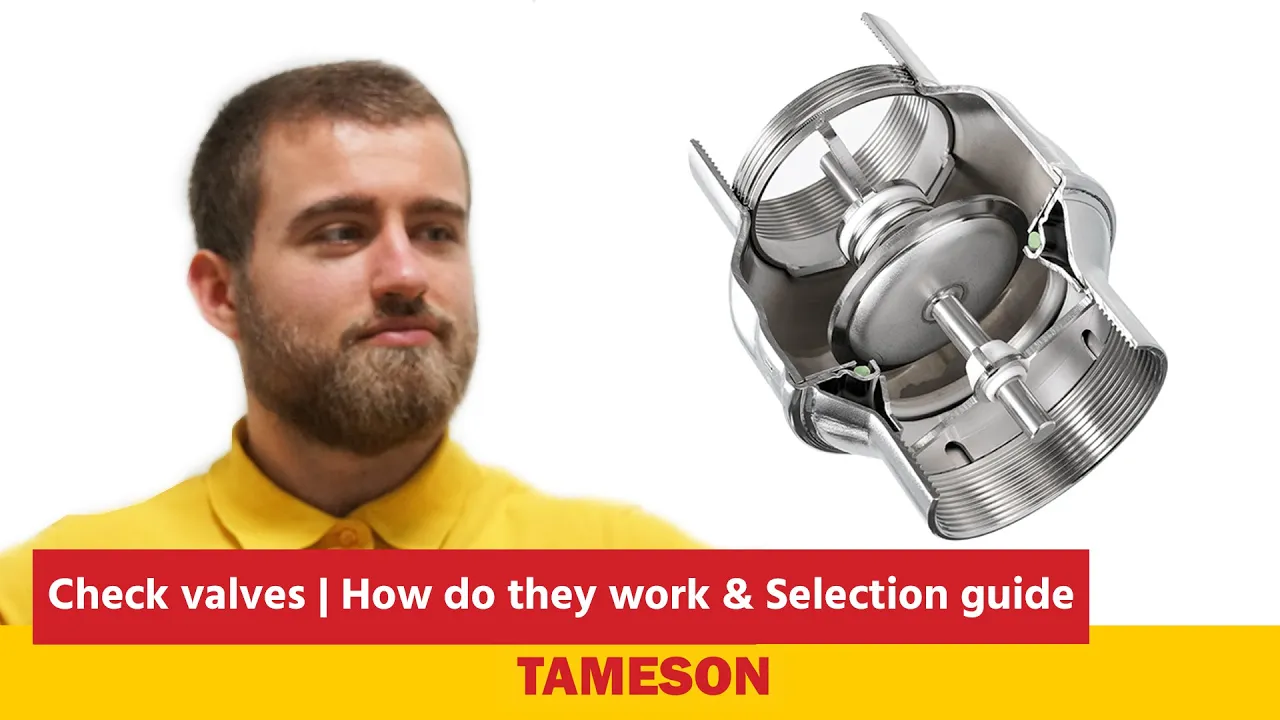
Spring loaded check valve components
How does a spring check valve work?
A spring-loaded check valve's function is straightforward. Under normal flow conditions, the fluid pushes against a disc (Figure 2 labeled D) or poppet inside the valve. When this force overcomes the spring's tension (Figure 2 labeled B), the valve opens, allowing the fluid to pass through. The spring is calibrated to provide just enough force to close the valve against the seal (Figure 3 labeled C) when the flow slows or stops, but not so much that it prevents the valve from opening under normal flow conditions. The check valve's body (Figure 2 labeled A) ensures all of the components described above are protected from the environment.
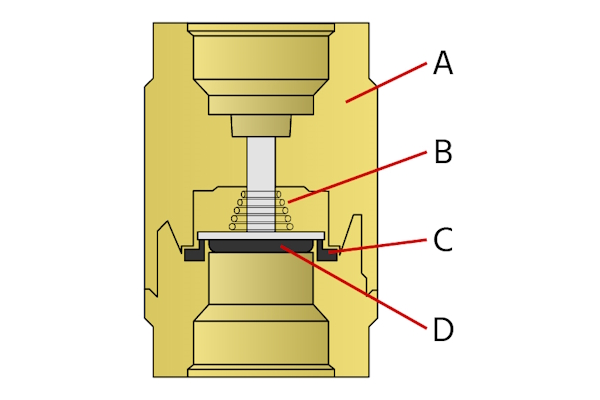
Figure 2: Spring check valve components: body (A), spring (B), seal (C), and disc (D).
Cracking pressure
Cracking pressure is the minimum pressure difference required to overcome the spring force and slightly open the check valve. There is a technical balance between cracking pressure and the effectiveness of a spring check valve's sealing. The higher the spring force, the higher the cracking pressure and the better the seal. It is not always ideal to have a high cracking pressure, as some systems have relatively low flow rates.
Pressure drop
A spring-loaded check valve's pressure drop is the pressure reduction as fluid passes through it. The fluid must go around the disc and this change in direction causes the pressure drop. A lower pressure drop means less flow resistance, making the system more efficient. In a spring-loaded check valve, a larger valve size reduces pressure drop by providing a bigger passage for fluid, which decreases flow resistance. A lower flow rate reduces pressure drop by decreasing fluid velocity and resistance. Conversely, higher spring tension increases the pressure drop by requiring more pressure to open the valve.
Spring check valve symbol
As shown in Figure 3, the symbol for the spring-loaded check valve features a horizontal Y that opens in the direction of the flow. Opposite the horizontal Y is a horizontal line with a zigzag line passing through it. This zigzag line represents the spring, and the circle represents that the check valve is spring-assisted.
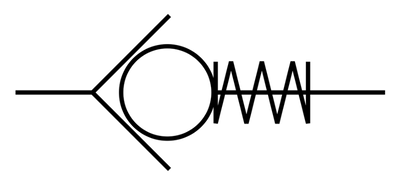
Figure 3: Spring check valve P&ID symbol
Installation guidelines
- Valve orientation and flow direction: Ensure the valve is oriented correctly to allow media to flow through it. Typically, an arrow is stamped on the valve body to indicate the flow direction. If you install the valve in the wrong direction, proper flow will be stopped.
- End connections: Ensure the valve's end connections are properly fitted to the piping. Common pipe threads are NPT (in North America), BSP, and metric. Check valves also come with a compression ring, cutting ring, push-in, and more. See Table 1 for more information.
- Installation orientation: Spring-assisted check valves can be installed in any orientation. However, for vertical installation, gravity will impact the cracking pressure. The fluid column above the check valve will impact the cracking pressure for upward flow installation.
Read our article on check valve installation for more in-depth information.
Selection criteria
There are several variables to consider when choosing the most suitable spring-loaded check valve for an application:
Body material
- Stainless steel: Handles high temperatures up to 200 °C (392 °F) and pressures up to 400 bar (5800 psi). Ideal for demanding industrial applications.
- Brass: Suitable for moderate conditions, withstanding temperatures up to 180 °C (356 °F) and pressures up to 25 bar (600 psi). Common in plumbing and HVAC systems.
- Brass, nickel-plated: Offers temperature resistance up to 130 °C (266 °F) and can handle pressures up to 20 bar (290 psi).
- Red brass: Manages temperatures up to 100 °C (212 °F) and pressures up to 20 bar (290 psi). Used in water supply systems for its corrosion resistance.
- Steel: Withstands temperatures up to 200 °C (392 °F) and pressures up to 400 bar (5800 psi). Used in industrial settings.
-
Plastic: Plastic spring check valves come in a variety of different materials:
- Polypropylene: Best for temperatures up to 80 °C (176 °F) and pressures up to 6 bar (87 psi). Ideal for chemical and water treatment applications.
- PVC (polyvinyl chloride): PVC spring check valves are suitable for temperatures up to 60 °C (140 °F) and pressures around 16 bar (232 psi). Commonly used in residential and commercial plumbing due to its cost-effectiveness and chemical resistance.
- PA (polyamide/nylon): Can handle temperatures up to 90 °C (194 °F) and pressures around 6 bar (87 psi). Known for its strength and abrasion resistance, making it suitable for industrial applications.
Seal material
- EPDM (ethylene propylene diene monomer): Excellent resistance to heat, ozone, and weather. Good resistance to polar substances and steam. Poor resistance to petroleum-based fluids.
- NBR (nitrile butadiene rubber): Good resistance to oils, fuels, and other chemicals. Moderate temperature resistance. Poor resistance to ozone and weathering.
- FKM (fluoroelastomer, commonly known by the brand name Viton): Excellent heat and chemical resistance. Good resistance to oils, fuels, and a wide range of chemicals. High temperature stability.
- PTFE (Teflon, polytetrafluoroethylene): Exceptional chemical resistance, low friction, and high-temperature stability. Non-reactive and non-stick properties.
- FEP (fluorinated ethylene propylene): Similar to PTFE but with improved flexibility. Excellent chemical resistance and high-temperature performance. Transparent and can be welded.
Recommended media
The following describes various media and their compatible housing and seal materials.
- Dilute acids and bases: Stainless steel with FKM seal
- Strong acids and bases: Stainless steel with FKM seal
- Solvents: Brass, nickel-plated with FKM seal
- Alcohols: Brass with NBR seal, Stainless steel with EPDM or NBR seal
- Combustible gasses: Stainless steel with NBR or FKM seal
- Sea water: Stainless steel with any seal type
- Demineralized water: Stainless steel with EPDM or FEP seal
- Air: Brass with NBR or FKM seal, stainless steel with any seal type except EPDM
- Carbon dioxide: Stainless steel with any seal type except NBR
- Oil: Brass with NBR or FKM, stainless steel with NBR, FKM, or Teflon
- Fuel: Brass with FKM seal, Stainless steel with FKM, Teflon, or FEP
- Lubricant: Brass with NBR or FKM, Stainless steel with NBR, FKM, Teflon, or FEP
- Water: Brass, PP, PVC, PA, or Stainless steel with any seal type
- Steam: Stainless steel with EPDM, Teflon or FEP, or Red-brass with Teflon
Max pressure
It's necessary to choose a check valve with a pressure rating high enough to handle the system's normal operating pressure. If the system's pressure exceeds the valve's operating pressure, it may lead to valve failure, leakage, or other issues. Spring-loaded check valves are available with maximum operating pressures ranging from 4 to 40 bar (58 to 580 psi).
Temperature
Check valves have a minimum and maximum temperature range. Keeping the valve within this range is necessary to prevent damage to the valve. Spring-loaded check valves range between -25 to 200 °C (-13 to 392 °F).
Approval
Check valve approvals indicate which applications a valve meets the requirements for. Spring-loaded check valves have the following approvals:
- Drinking water: This approval indicates the check valve is suitable for drinking water applications.
- NSF ANSI 61:NSF ANSI 61 is another drinking water approval used in the United States.
- WRAS:WRAS sets requirements for water applications in the UK.
Kv value
The Kv value, or flow coefficient, is a measure of a valve's capacity to allow fluid flow; it represents the flow rate in cubic meters per hour (m³/h) of water at a pressure drop of 1 bar across the valve. Choosing the correct Kv value is essential because an oversized valve with a high Kv value can lead to poor control and instability, while an undersized valve with a low Kv value can restrict flow, causing pressure drops and inefficiencies in the system. Learn more in our Kv calculator, which uses metric units, or our Cv calculator, which uses imperial units.
Features
- Reinforced pin: A reinforced pin is designed to enhance the durability and reliability of the valve by providing additional strength to the moving parts, reducing the risk of mechanical failure.
- Backflow preventer type EA: This is a type EA backflow preventer according to EN 1717, which means it is suited for drinking water and hot water installations such as coffee and vending machines, ice machines and steam ovens.
- Heavy duty: This indicates that the valve is constructed to withstand demanding conditions, such as high pressure or temperature, making it suitable for industrial applications.
- Air feeder connection: An air feeder connection allows the valve to be integrated into systems where air is used as a medium, facilitating the controlled flow of air through the valve.
- High pressure: This feature signifies that the valve is capable of operating under high-pressure conditions, ensuring reliable performance in systems with elevated pressure levels.
- Flow to the thread: Fluid enters the valve from the side opposite the threaded connection.
- Flow from the thread: Fluid enters the valve from the side with the threaded connection.
- Vacuum: This feature means the valve is designed to operate effectively in systems where vacuum conditions are present, preventing backflow in low-pressure environments.
- Auto shut-off: An auto shut-off feature allows the valve to automatically close when flow stops or reverses, providing an additional layer of safety and preventing unwanted flow.
Minimum pressure difference
The minimum pressure difference is the valve's cracking pressure. See the Cracking pressure section above to learn more.
FAQs
What is a spring-loaded check valve?
A spring-loaded check valve has a spring that applies pressure and seals the valve’s disc. It allows media flow in one direction and prevents backflow.
What is the difference between a swing check valve and a spring-loaded check valve?
A spring check valve uses a spring to force the valve to close. A swing check valve has a flapper that allows flow passage but returns to its original position when it stops.
Is a swing or spring check valve better?
Spring check valves are more versatile than swing check valves and have better sealing properties.
Can a spring check valve be installed horizontally?
Yes, a spring check valve can be installed horizontally and vertically. With the proper spring properties, the valve's flow direction can face in any direction.