How to prevent solenoid valve noises
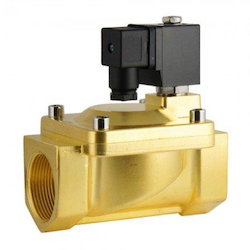
Figure 1: 2/2-way solenoid valve
Solenoid valves that produce unusual noises can indicate underlying issues that need attention to avoid potential malfunctions. While some valves naturally emit sounds during normal operation, it is important to distinguishing between typical operational noise and problematic sounds. This distinction helps identify whether the issue lies within the solenoid valve itself, the control circuitry, or the plumbing system. Below are some of the most common noises associated with solenoid valves, which can serve as indicators of their operational status.
Couldnt fix the noise issue and want a new one? View our online selection!
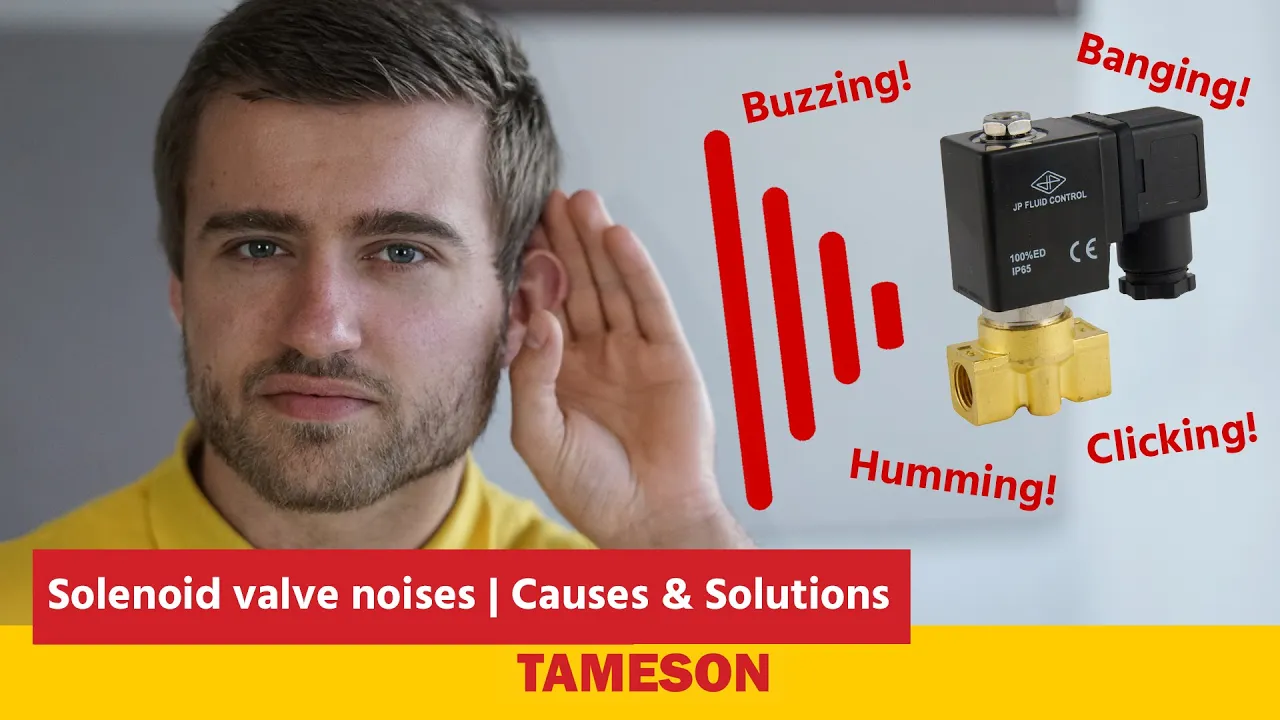
Humming or buzzing noise
AC noise
Solenoid valves operating on alternating current may produce a noise accompanied by vibrations. Soft buzzing and slight vibrations are normal in some types of AC solenoid valves. They are the result of alternating current producing a varying magnetic field which acts on the armature of the valve. Most solenoid valves include a shading ring, usually made from copper, which is used to buffer the magnetic energy created by the current flowing through the solenoid. They smoothen out the varying strength of the magnetic field by storing magnetic energy while the current is at its peak, and releasing it when the AC current is near to zero.
Undervoltage
However, if the noise or vibrations are excessive, this may point to one or more issues. One potential cause is undervoltage, caused by improper control signal, faulty control system, bad wiring or control relay malfunction. Undervoltage may cause the solenoid to never fully open, oscillating between the open and closed states, a state which produces abnormal vibrations and an audible hum. This fault can be diagnosed by energizing the solenoid and measuring the voltage across it, making sure that it is within the manufacturer-provided specifications.
Loose or missing parts
Another cause can be loose or missing parts in the assembly. This case might be characterized by a chattering noise. It should be verified that all parts are installed according to the manual and that all components are properly tightened. This problem can occur if improper maintenance is performed on the valve. If some components are missing, you may find a suitable spare in your distributor’s catalogue.
Excessive pressure or flow rate
An excessive pressure differential across a solenoid valve, or a too high flow rate, can cause humming noises in some valve types. Solenoid valves should be chosen having in mind the pressure and flow requirements. Inlet and exhaust tubing should be of sufficient diameter to allow for lower flow rates. Some solenoids require speed-control devices for proper operation.
Internal damage can also produce noisy operation. Worn armature or damaged springs are often to blame in such cases, and if wear-related issues are suspected, the valve should be examined and serviced by a professional.
Indirect operated valves with too low differential pressure
Some valve designs require a minimum pressure differential for the valve to open from the closed position, and to stay in the open state. This is called indirect operated, pilot operated or servo operated. If the minimum pressure differential requirement is not met, the valve may not fully open, or may rapidly resonate between the open and closed position, producing audible noise. In order to avoid this issue, pay attention to the minimum operating pressure differential specification in the solenoid valve datasheet, or use a valve design that does not have minimum pressure differential requirements. An example is a direct operated solenoid valve or a (motor driven) ball valve.
Foreign matter
Finally, foreign matter such as dirt can affect the operation of the valve. Limescale can be another cause, especially in systems used with hard water. Solenoid valves run at temperatures that can be considerably higher than the temperature of the surrounding air. In a process similar to the one occurring in water heaters, calcium deposits can build up on the armature, causing it to stick and possibly fail. Noises are sometimes an early indication of this problem. Valves can be more or less immune to this problem, depending on their design.
Water hammer
When a valve is open, the medium flows through the valve at a certain speed. If the flow is abruptly stopped by rapidly shutting off the valve, pressure builds up due to the momentum of the moving medium and this causes a short pressure surge. The pressure surge causes a noise which sounds like the pipes were struck by a hammer. This phenomenon is more pronounced in liquid than in gaseous media due to the fact that gasses are compressible and can absorb part of the kinetic energy at the instant the valve is closed.
There are several approaches to solving the water hammer problem. One is to reduce the flow rate by uprating the diameter of the tubing. This reduces the momentum of the medium and as a result reduces the maximum amplitude of the pressure surge.
Another solution is to ensure that the valve closes gradually instead of instantly. This is not always an option when using solenoid valves, as some of them have fast state switches. The speed of opening and closing is indicated by the response time of a solenoid valve. An electric or pneumatic actuated ball valve switches state considerably slower than solenoid valves.
A third solution is to use a water hammer arrestor, sometimes called a shock arrestor, which is a device that dissipates the energy carried by the pressure surge in a more controlled manner. These devices are consisted of an air pocket sometimes contained behind a sealed piston inside a cylinder which is closed on one side. The pressure surge causes the piston to move, compressing the air pocket and dissipating the kinetic energy as heat. In some high-flow applications, it is very important to prevent the water hammer effect because it might be powerful enough to cause ruptures or leaks at the weakest point in the system.
Clicking noises
When solenoid valves open and close, they may produce a clicking noise. The noise may come from the valve itself, or it may come from supporting circuitry, usually a relay that supplies current to the valve. In most cases, these clicks are considered normal operating noise and may be difficult to prevent.
However, if the solenoid clicks rapidly, for example every second or every few seconds, then this usually indicates a problem. It is most often caused by a faulty controller or bad wiring. The best approach is to measure the voltage across the solenoid valve when it is energized, and ensure that it is within specs and not fluctuating by more than a few volts. A small voltage fluctuation may be normal when the solenoid is first energized, but it should quickly settle to a specified value. To eliminate wiring problems as the cause, the solenoid can be connected directly to the controller using short leads. If this solves the problem, then it is a good idea to look for a short or a bad connection somewhere in the wiring harness.
If the wiring is correct, then the controller might be broken, or the problem might come from one of the controller inputs, for example a bad sensor or bad input wiring that keeps cycling the solenoid valve. In any case, the root cause of the problem should be found and corrected, because a rapidly cycling solenoid is prone to increased wear and premature failure.
Pneumatic valve exhaust
Some pneumatic devices used in industrial applications have valves that vent system pressure directly to the surrounding atmosphere. Depending on the pressure and flow, the noise can be quite loud, and in some cases require ear protection for workers in order to avoid problems such as hearing loss, tinnitus and overall stress. Continuous or repeated exposure to sound pressure levels in excess of 90 dB can cause hearing loss over time. In order to avoid or reduce these effects, pneumatic mufflers or silencers can be installed in exhaust ports.
The noise generated by pneumatic valve exhaust ports comes from turbulent air leaving the exhaust port. The turbulence is caused by a sudden surge in the flow through the orifice. Mufflers operate by dissipating the energy released during this process, and diffusing the air through a larger surface area, thereby reducing the sound pressure spike and reducing overall noise. Their secondary purpose is to protect the exhaust port from water and dirt ingress.
There are several different types of pneumatic silencers available on the market. They come in various flow ratings, back pressures, noise reduction ratings and fittings. Most have filters that prevent various contaminants such as oil mist from being released into the atmosphere. Depending on the design, some pneumatic mufflers may need periodic maintenance to prevent the filter from clogging.