Swing Check Valve - Types and Features
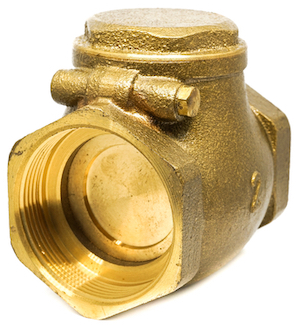
Figure 1: A brass swing check valve
A swing check valve uses a hinged disc that swings open with forward flow and closes against reverse flow, preventing backflow. These valves operate automatically without power, are cost-effective, are made of a wide range of materials, and have different designs for specific functionality. This article discusses a swing check valve's operation, applications, advantages, and disadvantages.
Table of contents
- Check valve comparison table
- What is a swing check valve
- Materials
- Installation
- Advantages and disadvantages
- Swing check valve applications
- Swing check valve symbol
- Comparison with other check valve types
- FAQs
View our online selection of check valves!
Check valve comparison table
Table 1: Lift check valve vs swing check valve vs spring-loaded check valve
Feature/Criteria | Lift check valves | Swing check valves | Spring-loaded check valves |
---|---|---|---|
Operation | Disc lifted by fluid flow, closes by gravity or back pressure | Hinged disc swings open with flow, closes when flow reverses | Spring mechanism compresses to open, expands to close |
Advantages | Good sealing for high-pressure applications | Low pressure drop Suitable for fluids with suspended solids |
Fast response to flow changes Can be installed in any orientation |
Limitations | Lift check valve pressure drop is higher due to disc lifting Limited to horizontal installation Sensitive to debris, which can obstruct disc movement |
Generally limited to horizontal installation Slower response, allowing potential backflow before sealing |
Higher cost due to spring mechanism Potential for spring wear in high-cycling applications |
Ideal applications | Clean fluid systems with consistent flow | Water and wastewater systems with large volumes and suspended solids | Systems requiring quick response and versatile installation |
Installation flexibility | Limited (horizontal only) | Limited (primarily horizontal) | High (any orientation) |
Cost | Moderate | Low | Higher |
Maintenance | Low to moderate, depending on debris exposure | Low | Moderate to high, due to potential spring wear |
What is a swing check valve?
An inline swing check valve has a disc (Figure 2 labeled B) that can swing on a hinge (Figure 2 labeled A). When closed, the disc rests on the valve seal (Figure 2 labeled C) on the inlet side of the valve. When the pressure of the media flowing into the valve is higher than the valve's cracking pressure, the disc rises, the valve opens, and media is allowed to flow through the valve. When the inlet pressure drops, the valve swings shut to block any downstream backflow that may occur. Read our guide on check valves for a comprehensive understanding.
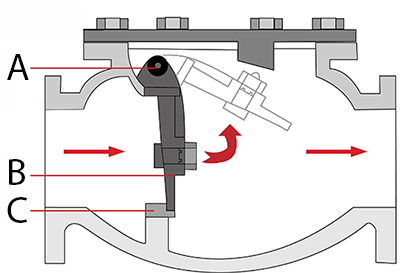
Figure 2: Swing check valve diagram showing its components: hinge (A), disc (B), and seal (C).
Materials
Valve body
-
Stainless steel
- Stainless steel swing check valves are durable and resistant to corrosion and rust, making them suitable for many applications. However, they may not be cost effective for systems with low pressures or temperatures.
- While generally resistant to corrosion, not all stainless steel grades are suitable for saltwater applications. 316 stainless steel is recommended for such environments due to its enhanced resistance to chloride-induced corrosion.
- These valves typically operate effectively within a temperature range of -20 to 200 𐩑C (-4 to 392 𐩑F).
-
Brass
- Brass swing check valves are suitable for high-temperature and high-pressure applications and are more cost-effective than stainless steel valves.
- They operate effectively within a temperature range of approximately 0 to 90 𐩑C (32 to 194 𐩑F).
Valve seat
-
NBR
- NBR seats are resistant to oil and have high abrasion resistance.
- These seals' working temperatures range from -35 𐩑C to 120 𐩑C (-31 𐩑F to 248 𐩑F).
-
Metal
- While offering high-temperature and pressure resistance, metallic seats are more prone to leakage than rubber seats and may need corrosion protection in specific environments.
- The exact temperature range depends on the specific metal used.
Read our chemical resistance guide to learn more about the chemical properties of different materials.
Installation
A swing check valve is typically installed horizontally. If installed on a vertical pipe where the flow is upwards against gravity, the disk may slam against the seat when the flow stops, potentially leading to water hammer. If the flow is downwards, as in the case of boiler supply lines and mining applications with limited spacing, the swing check valve will always be open and not perform its function.
The general installation steps are:
- Ensure that there is no foreign material inside the valve, for example, packing material.
- Push the disc away from the seat to make sure it functions properly.
- Align the valve correctly by facing the arrow in the flow direction.
- Install the swing check valve.
- For threaded end connections, start by screwing the valve into both ends of the piping until it is hand tight. Then, use a wrench to tighten the valve by one half turn further. Further tightening can damage the valve.
- Pay close attention to the threading when starting to screw in the valve. If the valve threading and the pipe threading do not align correctly, cross threading can occur and damage the threads.
- After installing the valve, run media through it to ensure it flows in the right direction. Also, ensure there is no leaking.
Advantages and disadvantages
Advantages
- The hinge and disc assembly are shielded from the flow, reducing the chances of viscous or slurry media adhering to it and obstructing the valve's closure.
- Swing check valves are available in large sizes. Typically, the connection sizes are available from 1/2 to 4 inches (12.7 to 101.6 mm).
Disadvantages
- Swing check valves are unsuitable for frequent flow reversal and pulsating flow. Spring check valves are preferred in these systems because they are quieter.
- Swing check valves are generally prone to water hammer issues.
- Design the piping system to minimize abrupt changes in direction and flow velocity, which can contribute to water hammer.
- Another potential solution is to install a pressure relief valve upstream of the swing check valve so it can respond to pressure buildup in the system before it reaches the check valve.
- Swing check valve closure is typically slower than other check valves (e.g., lift and spring check valves).
- Less suitable for vertical flow. Spring check valves can be installed vertically.
Swing check valve applications
- Petroleum and chemical industries: These valves are commonly installed in pipelines for petroleum and chemical processes. They effectively manage clean process media, ensuring smooth and reliable flow in these critical applications.
- Water supply and wastewater treatment: Swing check valves are the most common choice in water supply systems and wastewater pumping. They are effective in preventing backflow and are less prone to clogging, although they may require occasional cleaning if solids build up over time.
- Slurry transport systems: While swing check valves are generally not recommended for media with solid particles or high viscosity, they are still used in slurry transport systems where clogging is less of a concern. Their design allows for easy maintenance and cleaning without removing the valve from the system.
Swing check valve symbol
The swing check valve symbol includes a line, arc, or semicircle to depict the swinging motion of the valve disc, which allows flow in one direction and prevents backflow. It often features an arrow to indicate the direction of permissible flow.
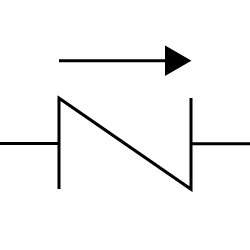
Figure 3: Swing check valve symbol
Comparison with other check valve types
Ball check valve vs swing check valve
Ball check valves and swing check valves are both cost-effective and commonly used in water and wastewater applications. They are both suitable for viscous media. Ball check valves use a spherical ball to block reverse flow, are typically more compact, and are suitable for low-flow applications. Swing check valves are better suited for higher flow rates and larger pipe sizes. Read our ball check valve article for a thorough comparison between ball and swing check valve types.
Spring check valve vs swing check valve
The spring in a spring check valve controls the valve's cracking pressure and closure. As inlet pressure drops, the spring begins to close the valve until the pressure drops below the valve's cracking pressure, and the valve fully closes. Apart from the construction, the main differences between both valve types are listed below:
- A spring check valve is ideal for reducing loud noises that occur when a swing check valve closes rapidly. Spring check valves, also called ‘silent’ check valves, are potentially resistant to water hammer. Swing check valves are prone to water hammer issues. As the spring controls closure, a spring check valve can be installed in any orientation (vertical or horizontal) so long as the arrow on the valve body is facing the flow direction. Swing check valves are preferred only in horizontal pipe runs.
- Spring check valves typically cost more than swing check valves.
- Spring check valves have a lower flow capacity than swing check valves.
Learn more in our article Swing check valves vs spring check valves.
FAQs
What is the purpose of a swing check valve?
A swing check valve allows the media to flow in one direction. When the media’s pressure drops, the valve closes and prevents backflow.
Is a swing or spring check valve better?
Swing check valves are more cost-effective than spring check valves. However, installation of spring check valves is possible in more orientations.
Where should a swing check valve be installed?
A swing check valve should be installed wherever backflow can contaminate media or damage system parts.