Solenoid valves for vacuum applications
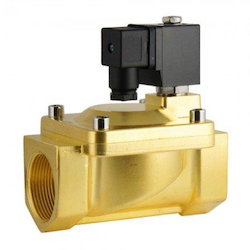
Figure 1: A 2/2-way solenoid valve
A solenoid valve for vacuum systems regulates airflow to generate or release a vacuum, playing a vital role in maintaining the required pressure levels. Selecting the appropriate vacuum solenoid valve is essential for achieving optimal performance in diverse applications, including vacuum pumps, robotics, and medical devices. This article will walk you through the important factors to consider when choosing a vacuum solenoid valve.
View our online selection of solenoid valves!
What is a vacuum?
A vacuum is an area of pressure lower than the surrounding pressure. Generally, this is a pressure below atmospheric pressure at sea level, which is 1 bar (14.7 psi) (Figure 2). However, vacuums do not necessarily need to be in relation to atmospheric pressure. For example, vacuum generators use low-pressure zones to create vacuums for suction applications. Learn more by reading our atmospheric, absolute, gauge, and differential pressure guide.
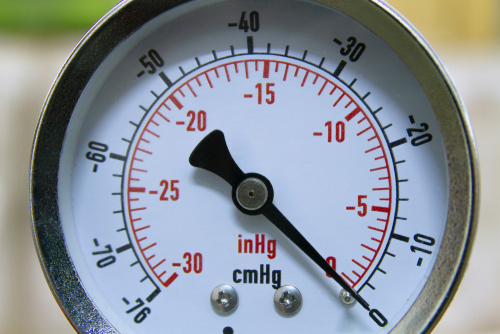
Figure 2: Vacuum pressure is an area of pressure lower than the surrounding pressure.
Can a solenoid valve be used in a vacuum application?
Yes, solenoid valves can be used to control air flow in a system to control the amount of air entering or exiting a vacuum chamber.
- Entering a vacuum chamber: A solenoid valve can be put on the vacuum chamber input to block air going into the chamber so that the vacuum pump can remove air from the chamber, thus creating a vacuum. Then solenoid valves open to return airflow into the chamber and dissipate the vacuum.
- Exiting a vacuum chamber: Alternatively, solenoid valves connect to the vacuum system between the vacuum chamber and the suction end of the application. For example, solenoid valves control a suction gripper by connecting one port to the gripper, one to the vacuum line, and one to the atmospheric pressure.
Vacuum solenoid valve selection
When choosing the right valve for a vacuum application, several factors should be considered, such as:
-
Circuit function (2/2-way, 3/2-way):
- 2/2-way solenoid valves have two ports (inlet and outlet) and two positions (open and closed). These valves can be normally open or normally closed. Typically used to control the airflow going into a vacuum chamber.
- 3/2-way solenoid valves have three ports. The third port connects to the atmosphere, which allows the solenoid valve to more precisely control the vacuum level in the application (see suction gripper example above).
- Design principle (direct, semi-direct): Direct and semi-direct solenoid valves are ideal for vacuum applications. They do not require significant pressure differentials between the inlet and outlet ports to operate properly. Some vacuum applications, though, do have a high enough pressure differential for indirect solenoid valves to function, but still, this design is not ideal.
- Flow rate (Kv-value): Different applications require different flow rates. For example, pick and place machines in the electronics industry do not require large flow rates.
- O-ring material: Common materials used for o-rings in vacuum applications are Nitrile, FFKM, FKM, EDPM, silicone rubbers, and Fluorocarbon.
- Response time: Direct-acting solenoid valves have a faster response time than semi-direct solenoid valves.
- Leakage rate: Vacuum applications that require an ultra-high vacuum have very strict leakage requirements. High vacuum solenoid valves are available, and ensuring the solenoid valve is clean helps prevent leakage.