Air Check Valve
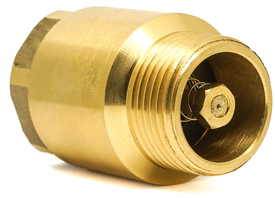
Figure 1: Air check valve
An air check valve allows air to flow in one direction and prevents any flow in the reverse direction. They are widely used in air compressors, and pneumatic and vacuum systems. Choosing the right check valve for the air compressor is crucial as any problem with the valve can directly affect the compressor’s performance. They are also commonly referred to as pneumatic check valves. This article discusses the working of an air compressor, the role of an air check valve, and the various ways to maintain the valve and the compressor.
View our online selection of check valves!
Check valve for compressed air
An air check valve allows airflow in the forward direction and prevents any backflow. The most common application of an air backflow valve is in an air compressor.
A check valve allows compressed air to flow from the compressor pump into the air storage tank while preventing the compressed air from flowing back into the pump. These valves can be located on a piston compressor (inlet and outlet), air receiver, or discharge pipes. The main roles of a check valve in an air compressor are:
- Preventing backflow: The check valve protects the compressor pump from potential damage caused by backflow. If compressed air were allowed to return to the pump, it could cause mechanical stress or damage, as the pump is designed to operate with airflow in one direction only.
- Air tank pressure: By preventing the backflow of air, the check valve helps maintain the pressure within the air tank. This is essential for the efficient operation of the compressor, as it ensures that the stored air remains at the desired pressure level. Without a check valve, the compressed air could flow back into the pump when it stops, leading to pressure loss in the tank.
- Energy efficiency: By maintaining pressure in the tank and preventing backflow, the check valve contributes to the energy efficiency of the air compressor. It ensures that the compressor does not have to work harder to compensate for lost pressure, thereby saving energy and reducing operational costs.
- Unloader valve interaction: In many air compressor systems, the check valve works in conjunction with an unloader valve. The unloader valve releases pressure from the compressor head and the line leading to the check valve when the compressor stops. This action prevents the compressor from having to start against high pressure, which would require more energy and could strain the motor. The check valve ensures that releasing this pressure does not affect the air stored in the tank.
- Moisture and debris: The check valve protects the system from moisture and debris. By ensuring one-way flow, it prevents moisture from the air tank and debris from traveling back into the compressor pump, which could lead to corrosion, wear, or operational issues.
Selection criteria
Selecting the right check valve for an air compressor involves considering several crucial factors to ensure efficiency, reliability, and safety.
- Compatibility with compressor size and type: Ensure the check valve is compatible with the specific size and type of the air compressor. The valve should be able to handle the maximum pressure and flow rate of the system without causing any restrictions or inefficiencies.
- Material and construction: Choose a check valve made from materials that can withstand the operating conditions, including pressure, temperature, and any potential chemical exposure from oils or moisture in the air. Common materials include brass, stainless steel, and plastic. The choice of material for check valves goes beyond just durability and corrosion resistance. For example, in systems where cleanliness of the air is paramount (like in medical or food processing applications), check valves made from materials that do not contaminate the air, such as certain grades of stainless steel or specific plastics, are crucial. Refer to our chemical resistance chart for more information on the compatibility of different materials with various media.
- Cracking pressure: The cracking pressure is the minimum upstream pressure required to open the valve. It's important to select a check valve with a cracking pressure suitable for the system's operating conditions to ensure that the valve opens at the appropriate time, allowing air to flow into the tank without significant resistance.
- Connection type and size: The check valve must fit securely and seamlessly into the air compressor system. This means selecting the correct connection type (e.g., threaded, flanged) and size to match the inlet and outlet ports of the compressor and piping. An improper fit can lead to leaks and reduced system efficiency.
- Integrated unloader features: In some air compressor systems, check valves have integrated unloader valves. The unloader valve is crucial for relieving pressure from the compressor head and supply line when the compressor stops, making it easier for the compressor to start up again. Integrating this feature into the check valve simplifies the system design and reduces the number of potential failure points.
Air check valve issues and solutions
Table 1: Air compressor check valve issues, effects, and solutions
Issue | Cause | Effect | Solutions/Preventive measures |
Sticking or seizing | Dirt, debris, rust | Valve fails to prevent backflow or obstructs airflow, leading to pressure loss or safety issues |
|
Leakage | Wear and tear, damage to valve seat/seal, presence of debris | Continuous pressure drop, increased energy consumption, accelerated wear on compressor components |
|
Corrosion | Exposure to moisture | Compromised valve integrity, potential for leaks or failure, parts may break off and damage system |
|
Improper installation | Incorrect orientation, inadequate sealing | Valve may not function correctly, allowing backflow, causing pressure issues or system failure |
|
Component wear | Normal wear and tear, frequent opening and closing cycles | Valve may not seal properly, leading to leaks or failure to open/close, affecting efficiency |
|
Cleaning air compressor check valves
Cleaning the check valve in an air compressor regularly helps prevent clogging and ensures expands the valve's lifespan.
- Safety first: Disconnect the air compressor from its power source to prevent accidental startup.
- Access the check valve: Locate the check valve, which is typically found at the connection point between the compressor pump and the air tank. Use a wrench to carefully remove it. Some systems might have a cover that needs to be unscrewed first.
- Disassemble: If the check valve can be disassembled, carefully take it apart. Keep track of all the components (springs, seals, etc.) to ensure correct reassembly.
- Clean: Soak the disassembled parts in a cleaning solvent designed for the type of material your check valve is made of. Use a soft brush or cloth to gently remove any debris, corrosion, or buildup. For hard-to-reach areas, compressed air can be effective. For this, blow air through the check valve in the opposite direction of normal flow.
- Inspect: After cleaning, inspect all parts for wear or damage, such as cracks or degraded seals. Replace any damaged components.
- Reassemble and reinstall: Once the parts are clean and dry, reassemble the check valve, ensuring all components are correctly positioned. Reinstall the valve, making sure it's securely fastened and sealed to prevent leaks.
Read our article on check valve installation for more information on how to install a check valve.
Air injection check valve
Air injection systems are designed to reduce emissions by combustion engines. The air injection system works by injecting air into exhaust systems. The injected air oxidizes the exhaust gasses, thus reducing carbon monoxide and hydrocarbon emissions. The injection system works together with a catalytic converter. The air injection system comprises a pump, a controller, a set of injectors, and check valves. The pump supplies air to the injectors, and the controller controls air pressure. The injectors are responsible for injecting air into the exhaust system.
The air injection check valves are used to prevent the backflow of exhaust gasses from the combustion engine into the injection system. Whenever the exhaust pressure exceeds the injection pressure, the check valve closes to stop the reverse flow of exhaust emissions.
The air injector check valve is a critical component in this system. It serves as a one-way gate, allowing air to flow into the exhaust system while preventing exhaust gasses from back flowing into the air injection system. This safeguard ensures the air injection process operates efficiently without contamination from exhaust gasses.
Typically, the check valve is located close to the air injection point in the exhaust system, often between the air pump (which supplies the fresh air) and the exhaust manifold or catalytic converter.
FAQs
What is the purpose of an air tank check valve?
The air tank check valve prevents backflow, maintaining pressure and protecting the compressor.
What are some symptoms of a bad air pump check valve?
Symptoms of a bad check valve include air leaks, pressure loss, and frequent cycling of the compressor.