Ball Check Valve - Working Principle

Figure 1: Stainless steel ball check valve
Ball check valves allow one-way flow by using a ball mechanism to create a reliable seal, ensuring efficient operation in systems handling gasses, liquids, and steam. The ball can either be free floating (uses gravity to close) or with a spring to ensure a proper seal. Ball check valves are reliable, low flow resistance, and require little maintenance, however, they are larger than other check valves. This article discusses the working, function, and installation of a ball check valve.
Table of contents
- Ball check valve design and operation
- Materials
- Ball check valve specifications
- Ball check valve installation
- Advantages of ball check valves
- Disadvantages of ball check valves
- Ball check valve applications
- Troubleshooting ball check valves
- Ball check valve vs swing check valve
- FAQs
View our online selection of check valves!
Table 1: Comparison of Different Check Valves
Feature/Criteria | Lift check valves | Swing check valves | Spring-loaded check valves | Ball check valves | Y-shape check valves | Sanitary check valves |
---|---|---|---|---|---|---|
Operation | Disc lifted by fluid flow, closes by gravity or back pressure | Hinged disc swings open with flow, closes when flow reverses | Spring mechanism compresses to open, expands to close | Ball moves away from seat to allow flow, returns to seat to block reverse flow | Y-shaped body with disc | Designed for hygienic applications, often with a spring-loaded disc |
Advantages | Good sealing for high-pressure applications | Low pressure drop Suitable for fluids with suspended solids | Fast response to flow changes Can be installed in any orientation | Simple design, reliable operation Can handle viscous fluids | Compact design Low pressure drop | Easy to clean Suitable for food and pharmaceutical industries |
Limitations | Lift check valve pressure drop is higher due to disc lifting Limited to horizontal installation Sensitive to debris, which can obstruct disc movement | Generally limited to horizontal installation Slower response, allowing potential backflow before sealing | Higher cost due to spring mechanism Potential for spring wear in high-cycling applications | May not seal well with low back pressure Limited to certain orientations | Not suitable for high-pressure applications Limited to specific flow conditions | Higher cost Requires regular maintenance to ensure hygiene |
Ideal applications | Clean fluid systems with consistent flow | Water and wastewater systems with large volumes and suspended solids | Systems requiring quick response and versatile installation | Pumping systems, wastewater applications | Low-pressure steam and gas systems | Food, beverage, and pharmaceutical processing |
Installation flexibility | Limited (horizontal only) | Limited (primarily horizontal) | High (any orientation) | Moderate (depends on design) | Moderate (depends on design) | High (often designed for easy disassembly) |
Cost | Moderate | Low | Higher | Low to moderate | Moderate | Higher |
Maintenance | Low to moderate, depending on debris exposure | Low | Moderate to high, due to potential spring wear | Low | Low to moderate | Moderate to high, due to hygiene requirements |
Ball check valve design and operation
A ball check valve uses a spring-loaded or free-floating ball that rests on the sealing seat to close the valve orifice (Figure 2). The ball's diameter is slightly larger than the diameter of the seat. The sealing seat is conically tapered to guide the ball into the seat and create a positive seal, thereby stopping reverse flow.
When the fluid pressure in the inlet side exceeds the cracking pressure (the pressure required to overcome spring force), the ball is dislodged from its seat, allowing the fluid to flow (Figure 2 labeled A).
When the inlet pressure does not exceed the cracking pressure or backpressure, the ball closes with the backpressure or via the spring, effectively closing the orifice (Figure 2 labeled B). The ball moves up and down inside the valve based on the flow. It seals against the machined seat when there is no flow or when reverse flow occurs, preventing reverse flow.
A free-floating ball check valve has no spring and requires an inverse flow or gravity to move the ball towards the seat to seal. Read our check valve overview article for more information on the working and various designs of check valves.
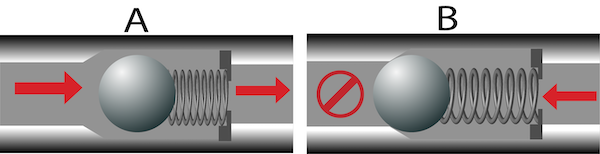
Figure 2: Spring-loaded ball check valve diagram: open position allowing flow (A) and closed position preventing backflow (B).
Materials
Housing
Ball check valves are available in different materials, each suited for specific applications. The choice of material depends on factors like operating environment, lifespan, and the type of media being handled. For example, nickel-plated brass is durable and ideal for high-temperature applications due to its excellent thermal resistance.
Seal
Ball check valves typically use seal materials such as rubber, elastomers (like EPDM or NBR), and PTFE (Teflon). Rubber and elastomers provide flexibility and a good seal for general applications, while PTFE is used for its chemical resistance and ability to withstand higher temperatures. The choice of seal material depends on the specific application requirements, including the type of media, temperature, and pressure conditions. Read our article on the chemical resistance of materials for more information on the compatibility of the valve materials to different media used.
Ball
The standard ball in a ball check valve features a metal core lined with rubber, with the rubber hardness carefully optimized to prevent the ball from becoming stuck in the seat. This design ensures effective sealing and smooth operation.
Ball check valve specifications
Consider the following factors while choosing a ball check valve:
- Connection size: Match the valve size to the existing pipe size for a proper fit and seal. Ball check valves with connection sizes from 1/8 to 3/8 inches are commonly available.
-
Operating temperature and pressure:
- Choose valve materials that can handle the system's temperature and pressure.
- Ensure the valve's pressure rating exceeds the system's maximum pressure for safety.
- Verify the valve's temperature rating matches the system's operating range to prevent material failure.
- Select seals and seats that withstand the specific temperature and pressure conditions.
- Connection types: Ball check valves typically have different threaded connection types like NPT and BSP. Other connection types like flanged, buttweld, soldered, and compression fittings are also commonly used for various applications.
Ball check valve installation
Ball style check valves can typically be installed both horizontally and vertically in a piping system. However, a ball check valve that closes by gravity without a spring must be installed vertically to ensure proper function. The valve should be mounted with the outer thread facing upwards so that gravity can effectively close the valve by moving the ball into the seat. However, a Y-type check valve with a ball closing element can be installed horizontally. The design of the Y-type valve allows the ball to function effectively in both orientations, providing greater flexibility in various piping configurations.
General installation guidelines for ball check valves are:
- Check the inside portion of the valve and remove any foreign particles present.
- To ensure proper ball check valve operation, make sure the ball moves freely by pushing it away from the seating surface.
- Inspect the valve ends and ensure that there are no raised burrs or edges that would not allow the valve to seal during operation.
- Install the valve according to the flow direction. An arrow symbol on the valve represents the direction of fluid flow through the valve.
Read our check valve installation article for more information on the installation position and process for different check valve types.
Note: Ball valve installation requirements can vary across different designs and manufacturers. Always consult the specific manufacturer's guidelines to ensure proper installation and function of the valve in the piping system.
Advantages of ball check valves
- The ball in a ball check valve is typically a hollow steel ball coated with elastic rubber, ensuring a tight seal and minimizing damage to the pipeline system during valve closure.
- The valve allows water to flow almost directly through the valve body, resulting in a low resistance coefficient, energy savings, and stable, minimal water flow resistance, which reduces hydraulic loss from the rubber ball's vibration.
- Ball check valves also offer excellent shock absorption and do not require high water quality. They have a self-cleaning ability due to the movement of the ball, which can dislodge debris as it shifts within the valve chamber during fluid flow. This movement helps maintain a clear passage and reduces the risk of blockages.
- Ball check valves lack rotating parts like shafts and sleeves, eliminating wear on these components. The rubber ball is freely suspended and rotates uniformly, ensuring even wear. The ball's diameter is nearly 1.3 times that of the ball seat, maintaining good sealing and wear resistance even if the rubber layer wears down.
Disadvantages of ball check valves
The main drawback of ball check valves is their relatively large size, which can take up significant space. This can be a limitation, especially when retrofitting check valves in older pump stations where space is restricted. Also, since the ball has a long distance to travel when the pump is turned off, ball check valves are prone to slamming in high head applications.
Ball check valve applications
Ball check valves are widely used in various applications due to their simple and effective design.
- Wastewater applications: Their clear bore design allows for smooth and complete flow, preventing solid deposits from accumulating and reducing the risk of impurities sticking to the rotating ball. This makes them particularly suitable for wastewater applications, where maintaining a clean flow is essential.
- Plumbing: In the plumbing industry, ball check valves are crucial for ensuring unidirectional flow in water supply systems, such as sprinklers, sump pumps, and water heaters. By preventing backflow, they protect the supply line from potential contamination.
- Pumping stations: Ball check valves are also commonly used in pumping stations, where their self-cleaning action helps maintain performance and minimize maintenance needs. This feature is particularly beneficial in stations that are rarely attended, as maintenance is typically only required if issues like noises from insufficient pump capacity or water hammer arise.
- Industrial settings: In industrial settings, such as factories using injection molding processes, ball check valves are essential for preventing backward slip of production fluids. Selecting the appropriate valve material is crucial in these applications to ensure compatibility with non-water fluids.
- Household devices: Ball check valves are found in household devices like liquid pump dispensers, spray devices, and dispensing syringes, where they help control the flow of liquids. Their versatility and reliability make them a popular choice across various industries, including fire protection and irrigation systems.
Read our check valve applications article for more information on the general applications of all check valve types.
Troubleshooting ball check valves
- Insufficient pump capacity: If the pump capacity is inadequate, the ball may not lift properly, restricting flow. In such cases, consider using a lighter ball. A lighter ball requires less force to be displaced from its seat, allowing the valve to open more easily and accommodate the available pump capacity.
- Water hammer issues: Water hammer can occur when the pump stops suddenly, causing a pressure surge. To mitigate this, a heavier ball can be used. A heavier ball increases the closing force, helping to absorb the shock and reduce the impact of the water hammer by closing the valve more gradually.
- Noisy operation: Noise during valve operation can be caused by trapped air in the system piping. Ensure that the system is properly vented to eliminate air pockets. Additionally, if the valve is only partially open, it can create turbulence and noise. In such cases, replacing the ball with a lighter one can help achieve full opening, reducing noise.
- Inadequate flow: If the valve does not provide the desired flow rate, inspect the interior for any obstructions or foreign materials that may be blocking the flow path. Thoroughly clean the valve to ensure that the ball can move freely and the flow is unobstructed.
- Backflow issues: A ball check valve is designed to prevent backflow. If backflow occurs, it indicates a potential issue with the valve seat or the ball. Disassemble the valve and inspect the seat and ball for wear, damage, or debris. Repair or replace any damaged components to restore proper sealing and prevent reverse flow.
Ball check valve vs swing check valve
Table 1 provides an overview of the differences between ball check valves and swing check valves
Table 1: Ball check valve vs swing check valve
Feature | Ball check valve | Swing check valve |
Closure element design | The closure element is a ball that lifts at cracking pressure and returns by spring action or gravity. | The closure element is a disc that swings on a shaft or hinge to restrict or permit flow. |
Flow Orientation | Suitable for both horizontal and vertical flow, but some models like the ones without spring assistance should be installed vertically | Typically used for horizontal flow |
Cost | More expensive due to the ball design | Cheaper because it uses a flapper instead of a ball. Significant cost difference in large projects. |
Water hammer | Water hammer is easily minimized by increasing the ball size. | Swinging action can increase water hammer issues. |
Flow capacity and size | Flow capacity is hindered by the ball along the flow path, but it is more compact and fits tight areas | Delivers larger flow capacity, especially with the top hinge configuration, but requires more space for the closure element to flap open and close |
FAQs
What is the function of a ball check valve?
A ball check valve is used to pass fluid only in one direction and prevents the flow in the reverse direction.
What are the different types of check valves?
Check valves can have different mechanisms like a ball, diaphragm, lift, or swing to prevent backflow.