Pressure Switch Explained
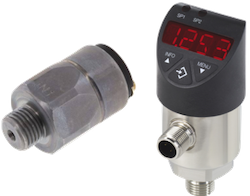
Figure 1: Mechanical (left) and electronic (right) pressure switches
A pressure switch controls an electrical circuit based on the fluid pressure within a system by activating or deactivating the circuit when a preset pressure level is reached. Pressure switches work in various industrial and residential applications like HVAC systems, well pumps, and furnaces. They are essential for maintaining system safety and efficiency by preventing overpressure conditions. There are mechanical and electric pressure switches, each suited to different applications and offering unique advantages. This article explores the working mechanisms of pressure switch types, their typical selection criteria, and their applications.
Table of contents
- Mechanical pressure switch
- Electronic pressure switch
- How to adjust pressure switch
- How to select a pressure switch
- Common applications
- Troubleshooting pressure switches
- FAQs
View our online selection of pressure switches!
Mechanical pressure switch
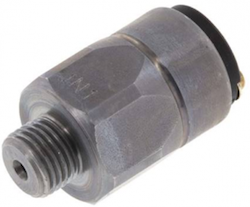
Figure 2: Mechanical pressure switch
A mechanical pressure switch (Figure 2) operates based on the physical movement of its internal components, primarily a spring and either a diaphragm or piston, to activate an electrical micro-switch at predetermined pressure levels. These pressure switches usually have three different types of contact: normally open (NO), normally closed (NC), and changeover (SPDT) contacts.
How a mechanical pressure switch works
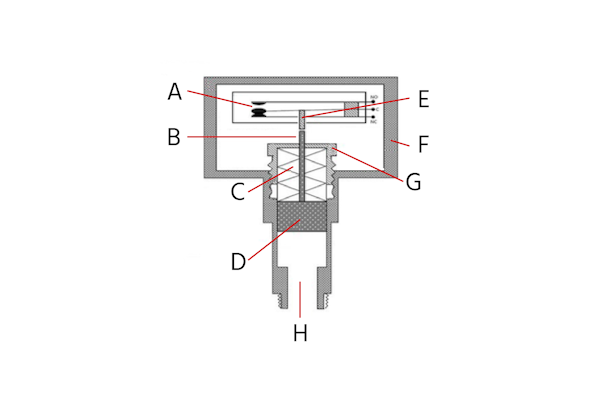
Figure 3: The components of a pressure switch include: micro-switch (A), operating pin (B), range spring (C), operating piston (D), insulated trip button (E), switch case (F), trip setting nut (G), and inlet pressure (H)
The structure of a mechanical pressure switch is designed to monitor and respond to the pressure levels in various systems.
- Micro-switch (A): The microswitch opens and closes the electrical circuit. It activates when the pressure switch senses that the fluid pressure has reached the predetermined level.
- Operating pin (B): The operating pin connects the mechanical movement of the pressure switch's internal components (like the operating piston) to the micro-switch. When the pressure moves the piston, the operating pin translates this motion into the action of the micro-switch.
- Range spring (C): The range spring is adjustable and determines the pressure range that the switch operates within.
- Operating piston (D): The piston is a movable component that reacts to changes in pressure. When the pressure within the system reaches a certain level, it pushes the piston. This movement is then translated into an electrical signal by the microswitch.
- Insulated trip button (E): This feature allows for manual testing or resetting of the pressure switch. It is insulated to ensure safety during operation.
- Switch case (F): The switch case houses all the internal components, protecting them from external elements and ensuring the durability of the switch.
- Trip setting nut (G): The trip setting nut is used to adjust the range spring, allowing users to set the desired pressure level at which the switch will activate.
- Inlet pressure (H): The fluid pressure enters the pressure switch through the inlet. The switch monitors the pressure level at this point.
In short, the inlet pressure exerts pressure upon the operating piston, generating a force opposing the range spring. Once the inlet pistons force is higher than the opposing spring force, it pushes the operating pin into the insulated trip button. This button then moves the micro-switch from closed to open. If the pressure decreases below the spring force, the button, pin, and piston move away from the micro-switch, breaking the connection. The connection then goes from the open to closed. Read our article on pressure switch installation for more information on how to install a pressure switch in a system.
Electronic pressure switch
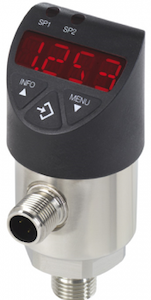
Figure 4: Electronic pressure switch
An electronic pressure switch (Figure 4) monitors the pressure of a fluid and activates an electrical signal or output when the pressure reaches a specified level. It combines the functions of pressure sensing and electrical switching into a single unit, offering a more sophisticated and versatile approach to pressure control compared to mechanical pressure switches. Electronic pressure switches offer advantages over mechanical pressure switches:
- Greater accuracy
- The ability to handle a wide range of pressures
- Programmability
- Digital outputs for integration with modern industrial control systems
Electronic pressure switches are suitable for automated and controlled equipment systems that require programmable function, digital display, flexibility, accuracy, ingress protection, and stability.
How an electronic pressure switch works
The working principle of an electronic pressure switch involves several key components and steps:
- Pressure sensor: The pressure sensor is the core component that detects pressure changes, converting the physical pressure into an electrical signal. Common types of sensors include piezoelectric, strain gauge, and capacitive sensors.
- Signal processing circuitry: This includes amplifiers and analog-to-digital converters that condition the sensor signal, making it suitable for analysis by the control unit.
- Control unit: Often a microcontroller or digital circuit that interprets the sensor signal based on programmed thresholds (setpoints). It decides when to activate or deactivate the output switch.
- Output switch: This can be a relay or a solid-state component that opens or closes an electrical circuit in response to the control unit's commands, thereby controlling external devices like pumps, valves, or alarms.
- User interface: Many electronic pressure switches feature a user interface, which can range from simple dials for setting pressure thresholds to digital displays and keypads for programming and monitoring.
Read our digital switches article for more information on the various sensing mechanisms used in an electronic pressure switch.
How to adjust a pressure switch
Adjusting a pressure switch involves setting the desired pressure levels at which the switch will activate and deactivate. For a mechanical pressure switch, the pressure can be adjusted using a hex key or turning knob. The electronic pressure switches have a digital display to set up the switching function. The following parameters can typically be adjusted by the user according to the requirements:
- Switch point
- Output signals
- Hysteresis (discussed later)
- Delay time
How to select a pressure switch
Choosing the right pressure switch for an application involves considering the following parameters:
- Mechanical vs electrical pressure switch: When choosing between mechanical and electrical pressure switches, consider the application's specific needs, like accuracy, response time, and integration capabilities (Table 1). For example, an electronic pressure switch is more expensive but comes with more control over the settings, like pressure switch set point and hysteresis, compared to a mechanical pressure switch.
-
Type of media: The type of media should be compatible with the housing and seal material. Nitrile butadiene rubber (NBR) is suitable for use with air and hydraulic/machine oil. Ethylene propylene diene monomer rubber (EPDM) is preferred for drinking water systems because it does not affect the taste of the water. Common media used with pressure switches are:
- Hydraulic oil
- Heating oil
- Turpentine
- Petrol/gasoline
- Air
- Water
- Pressure: The pressure switch must be able to withstand the maximum working pressure. Low pressure switches typically use a diaphragm as the sensing element, while high-pressure switches use a piston design.
- Temperature: The pressure switch's temperature range must include the application's minimum and maximum temperatures. High temperature pressure switches should use materials that can withstand elevated temperatures without degrading.
- Accuracy and repeatability: Accuracy refers to how close the switch's activation point is to the true pressure value, while repeatability is the switch's ability to consistently activate at the same pressure point over multiple cycles. The range of accuracy required determines the selection of the pressure switch for the application. Diaphragm designs generally provide more accuracy than the piston design.
- Hysteresis: Hysteresis is the difference between the switch point and the reset point. The switch stays active for a long time if the reset point is too large. If the reset point is too short, the switch will flip between on/off states frequently. Hysteresis is configurable in an electric pressure switch but preset by the manufacturer in a mechanical pressure switch.
- Process connection: The size and type of the process connection should match the system's piping or equipment. Common types include NPT, BSP, and flange connections.
- Approvals: Choose pressure switches with ATEX certifications for use in a potentially explosive atmosphere.
Table 1: Mechanical vs electronic pressure switch
Criteria | Mechanical pressure switch | Electronic pressure switch |
Cost | More affordable | Higher cost |
Application complexity | Best for simple, basic control | Ideal for complex, precise control |
Accuracy | Basic accuracy | High accuracy |
Durability | Robust in harsh conditions. | Sensitive to extreme environments |
Power requirements | No external power needed | Requires power source |
Environmental suitability | Handles harsh conditions well | Needs protection from elements |
Maintenance | Low maintenance | May need more maintenance |
Features | Basic on/off functionality | Advanced features like displays and programmability |
Response time | Slower response | Faster response |
Example applications | HVAC, well pumps, air compressors | Industrial automation, process control, advanced HVAC systems |
Common applications
A pressure switch is used in a wide range of domestic and commercial applications as listed below:
- HVAC, gas cylinders, air pumps, etc. use air compressor pressure switches to monitor and control the systems air pressure. Read our air compressor pressure switch adjustment article to learn more about how to adjust them.
- Oil pressure switches are used by engines as an actuator or sensor to determine when the engine's oil pressure has dropped below the preset level.
- Furnace pressure switches act as safety devices for industrial as well as residential purposes. They detect the negative pressure during the furnace start-up and shut down the furnace if there is low air pressure.
- Well pump pressure switches are used in residential and commercial buildings to bring water from the well and ensure that there is enough water pressure in the system to provide water without being over-pressurized.
- Water pump pressure switches in residential, commercial, and agricultural applications auto-regulate water flow.
- Vacuum pressure switches measure vacuum or negative pressure in the system. They are in residential boilers, electric heaters, air compressors, and transmission systems.
Read our pressure switch symbol article for more details on pressure switch symbols and diagrams.
Troubleshooting pressure switches
There are several signs that a pressure switch may be malfunctioning. Common indicators include:
- The pressure switch does not activate or deactivate the connected system as expected
- Erratic or inconsistent operation
- Unusual noises coming from the switch
Follow these steps to troubleshoot a bad pressure switch:
- Ensure all connections are secure and free of corrosion.
- Use a multimeter to test the continuity of the switch.
- If the switch does not show continuity when it should be closed, it may be faulty.
- Check the diaphragm or piston for any signs of wear or damage.
- For mechanical pressure switches, ensure the range spring and adjustment screw are properly set and not worn out.
- For electronic pressure switches inspect the sensor and signal processing circuitry for any faults.
- Ensure that the settings are correct and have not been altered.
If these steps don't resolve the issue, replacing the pressure switch entirely may be necessary.
FAQs
What features should an outdoor pressure switch have to withstand harsh environments?
An outdoor pressure switch should have a robust housing with a high IP rating, such as IP65 or higher, to protect against dust and water ingress.
Can a pressure switch be repaired?
Yes, a pressure switch can often be repaired if the issue is minor, such as replacing a faulty diaphragm or cleaning electrical contacts, but severe damage may require replacement.
What pressure switch is suitable for a well pump?
A mechanical pressure switch is suitable for a well pump, as it provides reliable on/off control for maintaining water pressure.
What is a pressure switch on a furnace?
A pressure switch in a furnace ensures safe ignition by verifying proper venting of combustion gasses through the draft pressure (the airflow created by the inducer motor to expel gasses) from the inducer motor.