Selecting Digital Pressure Switches and Sensors Instead Of Mechanical
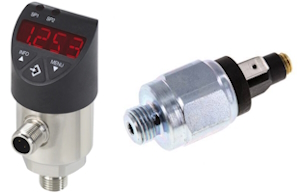
Figure 1: A digital pressure switch (left) and mechanical pressure switch (right)
Digital pressure sensors and switches represent a significant advancement over their mechanical counterparts, offering enhanced accuracy, reliability, and integration capabilities. As industries increasingly prioritize precision and efficiency, shifting towards digital solutions becomes imperative. These devices provide real-time monitoring and control and enable seamless connectivity with modern control systems, facilitating smarter decision-making.
View our online selection of pressure switches!
Pressure switches and sensors
Pressure switches and sensors are fundamental to monitoring and controlling systems across various industries. These devices play a crucial role in ensuring various processes' safety, efficiency, and reliability by measuring and regulating the pressure within systems. Understanding their functions and applications is key to selecting the appropriate device for specific needs.
Function
Pressure switches and sensors are designed to measure the pressure level of gasses or liquids within a system. Their primary function is to convert the physical pressure value into an electrical signal, which can then be used for monitoring or control. While pressure switches typically act to either open or close an electrical circuit when a preset pressure level is reached, pressure sensors provide a continuous pressure reading, offering more detailed monitoring. Read more about how pressure switches operate.
General applications
- Industrial automation: In manufacturing plants, these devices monitor and control pneumatic and hydraulic systems, ensuring that machinery operates within safe pressure ranges.
- HVAC systems: They regulate pressures in heating, ventilation, and air conditioning systems, contributing to energy efficiency and system longevity.
- Automotive industry: Pressure sensors are integral in monitoring engine performance, tire pressure, and oil pressure, enhancing vehicle safety and efficiency.
- Medical equipment: In healthcare, they are used in devices such as ventilators and infusion pumps, where precise pressure monitoring is critical.
- Water management: These devices are employed in water treatment plants and distribution systems to control pump operations and manage water pressure.
Digital vs mechanical pressure switches & sensors
Understanding the distinct advantages of digital devices is crucial when deciding between digital and mechanical pressure sensors and switches. This comparison demonstrates why digital options might be preferred based on reliability, ease of use, cost-effectiveness, and versatility.
Table 1: Aspects - Digital vs mechanical pressure sensors and switches
Aspect | Digital | Mechanical |
Reliability | High precision, stable over time, self-diagnostic, meaning they can identify errors in their normal operation. | Durable, less accurate over time, no advanced diagnostics. |
Ease of use | User-friendly interfaces, remote monitoring and adjustments. | Simple plug-and-operate, less convenient for remote access. |
Cost-effectiveness | Higher initial cost, lower operational costs due to remote diagnostics. | Lower initial cost, higher long-term operational costs. |
Versatility | Highly adaptable, integrates well with modern systems. | Limited application scope, less adaptable. |
Power requirement | Higher power consumption because they need an external power source to operate electronic circuitry, display, and sensors. Common power requirements are 12VDC and 24VDC, but this can vary | These switches do not require an external power source. However, power may be indirectly necessary for their operation if they are part of a bigger system that includes electronic signaling. |
Operating environment | Limited due to the electronic components but can still operate within most environments with normal conditions (e.g., non-extreme temperature and humidity conditions) | Can operate in harsher environments because they do not have electric components that need protection |
Selection guide
There are simple reasons to choose either a digital or mechanical pressure switch or sensor. If the system requires multiple switch/sensor points, select electric devices because they are simpler and less expensive to connect to control systems. However, for a single switch/sensor point that will not operate often, select a mechanical device primarily for its cost-effectiveness.