How to Select a Pneumatic Cylinder
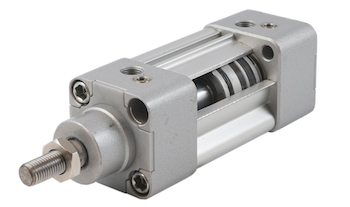
Figure 1: Pneumatic cylinder
Pneumatic cylinders are critical to many industrial systems, providing linear motion and force for various applications. Choosing the right pneumatic cylinder for a specific application is essential to ensure optimal performance and reliability. This article discusses the key factors to consider when selecting a pneumatic cylinder.
Table of contents
- Common mistakes to avoid when selecting a pneumatic cylinder
- How to choose a pneumatic cylinder
- Example
- FAQs
View our online selection of pneumatic cylinders!
Common mistakes to avoid when selecting a pneumatic cylinder
Table 1: Common mistakes while selecting a pneumatic cylinder and how to avoid them
Description | How to avoid | Consequences |
---|---|---|
Not considering factors like load mass, stroke length, and operating environment | Carefully assess all application specifics before selection | Poor performance, premature failure, or inability to complete the task |
Choosing a cylinder with insufficient force output | Ensure the cylinder's force output is at least twice the required load | Cylinder may stall or move too slowly, leading to process inefficiencies |
Not calculating the required actuation speed | Determine necessary speed and check cylinder specifications | Slow cycle times, reduced productivity, or inability to meet process requirements |
Failing to account for air supply and consumption | Calculate air consumption and ensure adequate supply | System pressure drops, inconsistent operation, or complete failure during peak demand |
Selecting cylinders too large or small for the application | Match cylinder size to application requirements and space constraints | Wasted energy, increased costs, or physical interference with other equipment |
Choosing cylinders with incompatible mounting configurations | Consider how the cylinder will attach to adjacent equipment | Difficult installation, misalignment, or inability to properly secure the cylinder |
Not accounting for temperature, corrosion, or cleanliness requirements | Select appropriate materials and seals for the operating environment that can tolerate the operating temperature without failure | Accelerated wear, contamination, or premature failure in harsh conditions |
Failing to consider end-of-stroke impact | Evaluate if cushioning is needed to prevent mechanical damage | Loud operation, excessive vibration, or damage to cylinder end caps and adjacent equipment |
Choosing non-repairable cylinders for heavy-duty applications | Select repairable cylinders for applications requiring frequent maintenance | Higher long-term costs, increased downtime for replacements, or reduced equipment lifespan |
Not considering position sensing needs | Choose magnetic cylinders if position feedback is required | Lack of precision control, inability to automate processes, or safety issues in critical applications |
How to choose a pneumatic cylinder
Choosing a pneumatic cylinder requires clearly defining the system's performance specifications, such as load capacity, stroke length, operating speed, and maximum operating pressure and temperature. The most crucial factors to consider during the selection process are discussed below.
- Form factor and ISO standards
- Pneumatic cylinder type
- Force and bore size
- Stroke length
- Cushioning
- Mounting options
- Speed
Read our pneumatic cylinder overview article for more information on the construction, working, and types of pneumatic cylinders. Our pneumatics glossary provides a reference for terms related to pneumatic systems.
1. Form factor and ISO standards
The form factor of a pneumatic cylinder refers to its physical size, shape, and dimensions. It includes factors such as:
- Cylinder type
- Bore size
- Stroke length
- Mounting style
- Overall shape
The form factor of a pneumatic cylinder determines whether the cylinder can fit into the available space in the application and whether it can move the load effectively. If the cylinder is too small or too large, it may not provide the necessary force or speed to move the load or may not fit into the available space respectively. Getting a pneumatic cylinder that adheres to a standard allows it to be easily interchangeable between brands if needed. These standards define pneumatic cylinders' dimensions, performance, and testing requirements. Common cylinders include round bodies, compact, and guided cylinders.
- Pneumatic ISO 15552 cylinders (32 - 320 mm): These pneumatic cylinders follow ISO 15552 for profile cylinders with diameters of 32 - 320 mm. Options include single-acting and double-acting cylinders, with various configurations for rod diameter, stroke length, force, pressure, magnetic piston, and adjustable damping.
- Pneumatic round cylinders (32 - 63 mm): Round body cylinders have a cylindrical shape and are one of the most common pneumatic cylinders. They are available in various bore sizes and stroke lengths and can provide high force and speed. These cylinders are suitable for various applications and come in different configurations for rod diameter, stroke length, force, and pressure.
- Pneumatic ISO 21287 compact cylinders (20-100 mm): ISO 21287 pneumatic compact cylinders have diameters ranging from 20-100 mm. They are smaller than round body cylinders and ideal for applications where space is limited. They have a shorter stroke length and a smaller bore size than round-body cylinders. Compact cylinders can be either single-acting or double-acting and are commonly used in automation and robotics applications.
- Pneumatic rodless cylinders: Rodless cylinders provide linear motion with the load moving alongside the piston. This gives the main advantage of having the same stroke length in significantly less space. Rodless cylinders are commonly used in material handling, loading, lifting, web cutting, and other applications.
- Pneumatic ISO 6432 mini cylinders (8 - 25 mm): Pneumatic cylinders following ISO 6432 for round cylinders (mini cylinders) have diameters in the range of 8 - 25 mm.
- Guided cylinders: Guided cylinders have additional guidance mechanisms that help prevent the piston rod from bending or twisting during operation. They are suitable for applications with a risk of the piston rod being subjected to lateral forces. Guided cylinders can be either round body or compact and are commonly used in pick-and-place operations and material handling.
2. Pneumatic cylinder type
There are several types of pneumatic cylinders, each with its own advantages and disadvantages. The three most common types are single-acting, double-acting, and rodless cylinders.
- Single-acting cylinders use compressed air to extend or retract the piston rod and a spring or other external force to return the piston rod to its original position.
- Double-acting cylinders use compressed air to extend and retract the piston rod.
Read our article on single-acting vs double-acting pneumatic cylinders for more information on the features of each type.
3. Force and bore size
A pneumatic cylinder must produce enough force to move the load. Use the formula F = m × a to calculate the force required to move an object of mass 'm' with an acceleration of 'a.' It is crucial to perform this calculation for both the inward and outward strokes and choose a pneumatic cylinder with a force rating slightly above the calculated force.
Choosing the right bore size is critical to ensure the cylinder can provide enough force for the application. Selecting an oversized cylinder may result in increased costs due to its larger size, while having an undersized cylinder can make it incapable of moving the intended load. A general rule of thumb is to choose a bore size 1.5 to 2 times the diameter of the load being moved. Read our pneumatic cylinder force calculator article for more information on the force calculations in single-acting and double-acting pneumatic cylinders.
4. Stroke length
Stroke length is the distance the piston travels linearly when actuated by compressed air. To lift a load 1 meter high, the stroke length of the cylinder should be at least 1 meter so that it can move the load from the starting point to the end. Estimating the stroke length correctly is crucial, as the cylinder can get expensive as the stroke length increases. A cylinder with a stroke length that is too short will be unable to move the load to the intended position. On the other hand, a stroke length that is too long can exceed the target position, and a heavy load placed at the end of a fully extended piston can cause piston stress and bending.
5. Cushioning
Cushioning slows the cylinder's motion at the end of the stroke to prevent damage. There are various types of cushioning, like shock absorbers, mechanical, and adjusting cushions, among others.
- Shock absorbers: Shock absorbers are external devices that absorb kinetic energy and reduce impact forces. They are suitable for applications with heavy loads and high-impact forces but require extra space and mounting provisions.
- Mechanical cushioning: Mechanical cushioning is a built-in elastomer within the cylinder and provides consistent cushioning. It is a simple and reliable option suitable for applications with moderate impact forces and limited space.
- Adjustable cushioning: Adjustable cushioning allows precise control over deceleration and impact forces. It offers customization and flexibility but can be more complex than mechanical cushioning or shock absorbers.
Read our pneumatic cylinder cushioning article for a more in-depth analysis of each cushioning type.
6. Mounting options
The pneumatic cylinder mounting style depends on the application's specific requirements, such as the available space and the direction of the load. Pneumatic cylinders can be mounted in various ways, like clevis, trunnion, flange, and foot mounts.
- Clevis mounts: A clevis mount attaches to the cylinder's clevis (a U-shaped bracket on the end of the cylinder) to the machine or system. Clevis mounts are suitable for applications where the load is in tension or compression, and the cylinder needs to move in a straight line.
- Trunnion mounts: Trunnion mounts use a trunnion bracket to attach the cylinder to the machine or system. Trunnion mounts are suitable for applications where the load is off-center, or the cylinder needs to pivot.
- Flange mounts: Flange mounts use a flange bracket to attach the cylinder to the machine or system. Flange mounts are commonly used in applications where the cylinder must be fixed.
- Foot mount: A foot mount attaches to the bottom of the cylinder using bolts or screws and secures the cylinder to a flat surface on the machine or system. Foot mounts are typically used when the load is vertical, and the cylinder needs to be placed without any lateral movement.
7. Speed
The speed of a pneumatic cylinder is its stroke length divided by the time it takes to move the load to the end position. Consider the application requirements while selecting the speed; for example, slower speed for assembly tasks and higher speed for packaging processes. The pneumatic cylinder speed can be controlled by adjusting the air supply pressure, installing a flow control valve, and using electronic controls or a pressure regulator. Read our article on pneumatic cylinder response time and speed for more details on pneumatic cylinder speed and the various factors that control them.
Example
Consider an application in which a pneumatic cylinder is used to lift a load that weighs 1000 kg and needs to be lifted to a height of 2 meters in 2 seconds. The cylinder will be mounted vertically, and the load will be attached to the piston rod. The cylinder is operated using compressed air at a pressure of 7 bar.
Choosing a suitable pneumatic cylinder
- Cylinder type and ISO standard: A single-acting cylinder is suitable for this application as it only needs to extend in one direction to lift the load. A double-acting cylinder can also be used, but it would be more complex and expensive. To ensure compatibility and interchangeability, choosing a cylinder that conforms to the ISO 6431 or ISO 15552 standards is recommended.
- Stroke length: The stroke length required is the distance the load needs to be lifted, which is 2 meters.
- Force:
Force = ma
The acceleration is the derivative of full-stroke velocity (v/t) or ((L/t)/t)
a = 0.5 m/s2
Force = 1000 ✕ 0.5 = 500 N
The cylinder should be able to produce a minimum of 500 N to move the load.
- Mounting options: Since the cylinder will be mounted vertically, a suitable mounting option would be a clevis or a trunnion mount.
- Cushioning: Choose any shock absorber cushion, as the application involves a significant load and relatively fast movement.
- Speed:
Speed = Stroke length / Lifting time = 2/2 =1 m/s.
The cylinder should be able to lift the load at a minimum speed of 1 m/s.
Based on the above calculations, a suitable pneumatic cylinder for this application would be a single-acting ISO 6431 or ISO 15552 standard cylinder with a rated minimum force of 500 N, a minimum stroke length of 2 m, and a rated speed of 1 m/s. The cylinder can be mounted using a clevis or trunnion mount.
FAQs
What factors should I consider when choosing a pneumatic cylinder?
Consider the cylinder's bore size, stroke length, operating pressure, and mounting style. Additionally, the type of application and the load requirements should also be taken into consideration.
How do I determine the bore size of a pneumatic cylinder for my application?
Select the pneumatic cylinder bore size based on the force required to move the load, the available air pressure, and the required speed of operation.
What factors influence linear actuator sizes for different applications?
Linear actuator sizes are influenced by factors such as load capacity, stroke length, speed requirements, and the specific environmental conditions of the application.
How to size linear actuators?
To size a linear actuator, determine the load requirements, stroke length, speed, power source, and actuator type, then consult manufacturer specifications to ensure it meets the application's needs.