Pneumatic Cylinder Cushioning
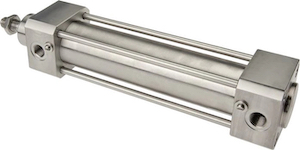
Figure 1: A stainless steel double acting pneumatic cylinder
Pneumatic cylinder cushioning is essential in industrial applications that use pneumatic cylinders. If a pneumatic cylinder comes to a sudden stop, it can damage the system. Cushioning slows the cylinder's motion at the end of the stroke to prevent damage. In addition, using cushioning in pneumatic cylinders improves the overall efficiency and accuracy of the system, and it can help extend the life of the equipment and reduce maintenance costs. This article covers the different types of cushioning for pneumatic cylinders and their advantages and disadvantages.
Table of contents
- Pneumatic cylinder overview
- What is pneumatic cylinder cushioning
- Types of cushioning
- External cushioning
- Mechanical cushioning
- Adjustable pneumatic cushioning
- Self-adjusting cushioning
- Advantages and disadvantages
- FAQs
View our online selection of pneumatic cylinders
Pneumatic cylinder overview
A pneumatic cylinder converts the energy of compressed air into linear motion. The cylinder consists of a cylindrical chamber with a piston and a piston rod, which move back and forth inside the cylinder. The cylinder can be single-acting or double-acting, meaning that the compressed air pushes the piston in one or both directions. Pneumatic cylinders are used in industrial automation systems to control the movement of machines and equipment with high precision and speed. Read our pneumatic cylinder overview and learn more about their design and performance characteristics.
What is pneumatic cylinder cushioning
Cushioning slows down and absorbs the impact of the piston as it reaches the end of its stroke. Without cushioning, the effect of the piston striking the end cap can cause damage to the cylinder and other mechanical components. Also, cushioning improves safety by limiting the piston's noise when it hits the end cap. This protects the hearing of users frequently operating pneumatic cylinders.
Types of cushioning
- External cushioning: External cushioning is a soft material, like rubber or foam, applied to the outside of a pneumatic cylinder to absorb the impact of the piston at the end of its stroke. It is easy to replace when worn out.
- Mechanical cushioning: Mechanical cushioning reduces impact load using a flexible material like an elastomer. It effectively reduces impact noise and absorbs small amounts of energy but is only suitable for applications with slow speeds, small loads, or short stroke lengths.
- Adjustable pneumatic cushioning: Adjustable air cushioning limits the air released at the end of the stroke using a variable orifice and two spuds. Air is trapped in the cylinder end cap and bled off through a small passage controlled by a needle valve. For the cushioning to remain effective, when there are changes in weight, pressure, or velocity, the cushioning must be readjusted.
- Self-adjusting cushioning: Based on the load and speed of the cylinder, the compressed air in the cylinder controls the automatic adjustment of the self-adjusting cushioning.This type of cushioning is often used in applications where the load and speed of the cylinder can vary significantly.
External cushioning
An external shock absorber mounts to the pneumatic cylinder. It reduces the cylinder piston's impact at the end of its stroke. A shock absorber typically has a fluid-filled cylinder (e.g., filled with oil), and a piston that moves inside the cylinder. At the end of its stroke, the pneumatic cylinder's piston pushes against the shock absorber's piston. This compresses the fluid inside the shock absorber. This action slows down and cushions the impact from the pneumatic cylinder's piston.
Shock absorbers are ideal for applications with heavy loads and/or high speeds because they create a lot of force. Without the protection of the shock absorber, the pneumatic cylinder would be at high risk of damage. The shock absorber also dampens vibrations and sounds.
Shock absorbers are classified into three types: fixed cushioning, adjustable cushioning, and self-adjusting cushioning.
- Fixed cushioning: For shock absorbers, fixed cushioning is the most cost-effective choice. It is designed to handle specific loads and speeds.
- Adjustable cushioning: Adjustable cushioning features an adjustment screw that enables the shock absorber to function with various load characteristics.
- Self-adjusting cushioning: Sensors and algorithms work with a self-adjusting shock absorber to automatically adjust the damping force based on the load characteristics.
Mechanical cushioning
Mechanical cushioning in pneumatic cylinders uses flexible elastomers placed inside the cylinder to absorb the impact force. Flexible elastomers are commonly made of rubber or other polymers that deform under stress and return to their original shape once the stress is removed. In pneumatic cylinders, flexible elastomers are placed at the end of the cylinder stroke, where they absorb the piston's kinetic energy and slow it down before it reaches the end of the stroke.
Adjustable pneumatic cushioning
Adjustable air cushioning technology limits the air volume released at the cylinder stroke's end. This cushioning's construction includes a variable orifice and spuds, which are small metal rods mounted on either side of the piston that close off the airflow to the main piston chamber, trapping air in the cylinder's end cap. This trapped air is then bled off through a small passage controlled by a throttle valve.
During each cycle, the cylinder traps a fixed volume of air. However, since air is highly compressible, the load, velocity, and air pressure in the cylinder can all affect the effectiveness of the pneumatic cylinder air cushion performance. For each application, only a narrow range of adjustments will result in optimal cushioning performance. Once the needle valve is set, any weight, pressure, or velocity changes can affect the cushion reaction, requiring the cylinder to be readjusted.
If the cushioning is set too high, the piston will slow down too quickly, which can result in slower overall cylinder speed. On the other hand, if the cushioning is set too low, the piston may not slow down enough, which can result in a bumpy or unstable movement and potential damage to the cylinder or the load being moved.
Self-adjusting cushioning
Instead of using an adjustable cross-section to regulate airflow within the cushioning chamber, self-adjusting cushioning uses slots in the cushioning piston to exhaust the air cushion independently of the cushioning length. The geometry of these air channels provides phased venting of the cushioning air, allowing the pneumatic cylinder cushioning system to adapt automatically to the cylinder's load and speed.
Advantages and disadvantages
Table 1: The advantages and disadvantages of shock absorbers, mechanical, adjustable, and self-adjusting cushioning.
Cushioning type | Advantages | Disadvantages |
Shock absorber |
|
|
Mechanical |
|
|
Adjustable |
|
|
Self-adjusting |
|
|
Read our ISO 15552, ISO 6432, and ISO 21287 pneumatic cylinder articles for the design features of pneumatic cylinders across various standards.
FAQs
What is cushioning in pneumatic cylinders?
Pneumatic cylinder cushioning slows the load that the piston moves. Without it, the piston will hit the end cap, causing shock, vibrations, and loud noises. Ultimately this will damage the system.
How do you adjust the cushioning on a pneumatic cylinder?
For pneumatic cylinder cushion adjustment, turn the adjustment screw at the cylinder's end. This screw controls the airflow through the cushioning valve, which controls the piston's speed at the end of the stroke.