How To Inspect a Valve In a Manufacturing Setting
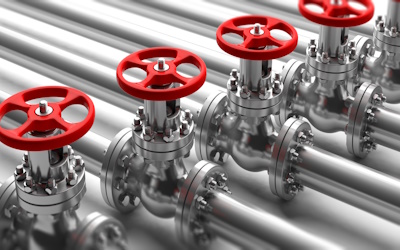
Figure 1: Valves play integral roles throughout various manufacturing processes.
Valves are crucial in controlling liquid and gas flows in a manufacturing setting. Properly functioning valves ensure the smooth operation of a plant's systems and processes. Regular valve inspection is necessary to maintain the plant's operational efficiency and safety. This article discusses the valves used throughout manufacturing processes and when and how to inspect them.
Table of contents
View our online selection of valves!
Valves in manufacturing settings
Many types of valves are used throughout various manufacturing systems and processes. Each type of valve has specific characteristics that make it suitable for certain processes and unsuitable for others.
- Gate valves: Gate valves excel when there is a straight-line flow and flow restriction is not required. These valves are typically fully open or fully closed and unsuitable for tasks requiring frequent valve actuation. They are often used with pipelines in oil and gas production systems.
- Globe valves: Globe valves control and throttle flow in a pipeline. Due to their excellent flow regulation capabilities, they are common in steam systems, such as those found in food and beverage production.
- Check valves: Check valves prevent backflow in a system by permitting flow in one direction only. These valves are common in water cooling systems to ensure water flows past the production machinery once. This ensures that water warmed by the machinery cannot flow past it again, which would greatly reduce the water cooling system's efficiency.
- Butterfly valves: Butterfly valves control large volumes of liquids while occupying a relatively small amount of space. These valves are often found in large-scale food and beverage systems.
- Ball valves: Ball valves offer easy and tight shut-off capabilities, even in high-pressure systems. They are commonly found in natural gas production systems throughout processes necessary to clean the gas of impurities.
- Plug valves: Plug valves provide on-off control and have a robust design, allowing them to work well in high-temperature systems. This makes plug valves ideal in petrochemical production systems that typically handle very high-temperature and corrosive media.
- Pressure relief valves: Pressure relief valves operate to protect equipment from overpressure. These valves are commonly used with boilers that produce steam for various processes throughout manufacturing.
- Diaphragm valves: Diaphragm valves have excellent sealing abilities and can handle viscous fluids. This makes them ideal for processes such as those found in pharmaceutical and food and beverage industries.
- Pinch valves: Pinch valves apply a pinch effect to stop fluid flow. They work well with slurry applications and are often found in mining and waste treatment facilities.
- Needle valves: Needle valves offer very precise flow regulation, making them ideal in chemical and pharmaceutical manufacturing. For example, adding a specific chemical to a reaction vessel requires precise flow control, which a needle valve can accommodate.
When to inspect a valve
Inspecting a valve at the right time can protect a manufacturing process from inefficiencies and damage. There are various times when valve inspection is necessary:
- Scheduled maintenance: Scheduled maintenance is typically set by the manufacturer's recommendations and depends on the application and valve usage.
- Performance issues: When a system or process is not performing as it should, a valve inspection helps identify if a faulty valve is the cause.
- Major system change: After a significant change to the system, such as a change to the process fluid, operating pressure, or temperature, inspect the valves. This helps to ensure the valves are adequate for the new conditions.
- After an incident: If an extreme incident occurs, such as an overpressure event, sudden shutdown, or safety-related incident, all related valves need to be inspected to ensure they were not damaged and are still operating correctly.
- Leak detection: If there is any indication of leaks in the system, all potential sources, including valves, need to be inspected.
- Startup and Shutdown: It is a good practice to inspect valves before system startup and after system shutdown. This helps ensure that the system will operate properly and helps identify any issues that must be addressed before the next startup.
- Unexpected noise or vibration: If the valve is making unusual noises or vibrations, it could be a sign of cavitation, flow turbulence, or a mechanical problem. Valve inspection helps identify and fix the issue.
How to inspect a valve
When it's time to inspect a valve, there are many different methods for going about it. This is because of the large variety of valves. First and foremost, an operator should check the valve manufacturer's guidebook to determine if any special steps need to be taken. In general, follow these steps to inspect a valve:
- Safety first: Always wear personal protective equipment (PPE) such as gloves, Safety glasses, and coveralls when necessary. If there is any need to go beyond a visual inspection, depressurize the system first.
- Visual inspection: Look for any signs of wear and tear, such as corrosion, leaks, or damage to the valve body, stem, or handle. Check around the valve for signs of leakage.
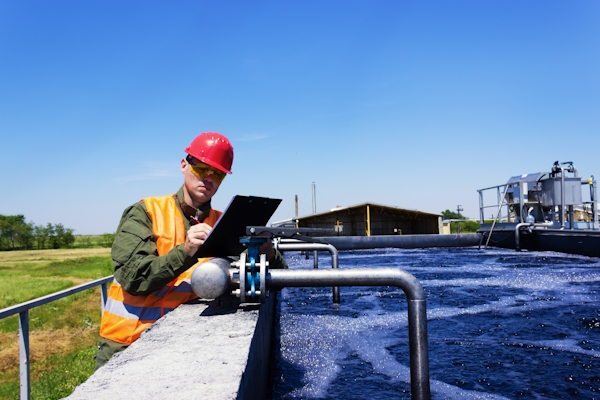
Figure 2: Careful visual inspection is worth the extra time because it can help quickly identify valve issues.
- Valve tag information: Every valve in a manufacturing setting should have a tag indicating its specification. Tag information often includes the valve type, size, material, pressure rating, and manufacturer. This information helps an operator determine whether the valve suits the intended application.
- Manual operation: If the valve has manual actuation and it's safe to do so, operate the valve to assess its functionality. Turn the wheel or handle to check for any signs of resistance. The operation should be smooth without grinding or sticking.
- Inspect internal components: To perform a detailed inspection, disassemble the valve. A qualified technician must do this. Examine the internal components for signs of wear, distortion, or damage.
- Leakage test: Reintroduce pressure to the system to test for leakage. Apply a soapy, non-corrosive leak-detecting solution to the valve and watch for bubbles that indicate a leak.
- Document findings: Document all findings, including irregularities or issues found during the inspection. This information is necessary for maintenance teams to address the identified issues and for future inspection reference.
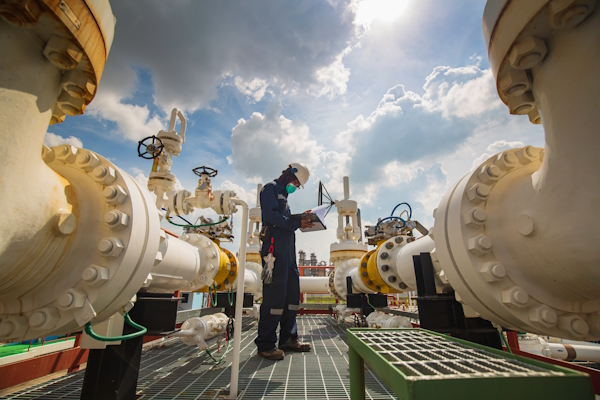
Figure 3: Documenting findings during valve inspection is a big part of the proper inspection procedure.
FAQs
What is the procedure for valve inspection?
Valve inspection procedures can vary. However, the general procedure is to proceed cautiously, visually inspect the valve for irregularities, and possibly disassemble the valve.
How often should valves be inspected?
Valves should be inspected on a regularly scheduled basis determined by the valve's manufacturer. Valves should also be inspected when system irregularities occur.