Plug Valves: How They Work and How to Select One
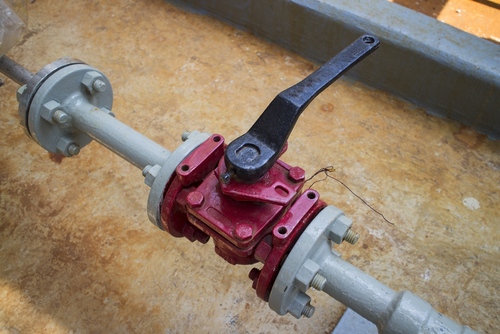
Figure 1: A plug valve in an industrial system
Plug valves are recognized for their ease of regulating flow by providing bidirectional, throttling, and on/off capabilities. These valves have many functions in industrial applications, ranging from gas processing and petroleum to chemical industries. They can handle diverse fluid types, including corrosive and flammable fluids. This article closely examines plug valves, how they work, their typical applications, and how to select them.
Table of contents
Plug valve design
The typical plug valve design has several key parts that work together to create a robust and reliable valve suitable for various industrial applications. Depending on the specific application, the plug valve may have additional features, such as seals and gaskets, to improve leak resistance.
- Body: A plug valve's body is usually cylindrical or globular and made of durable material such as cast iron, stainless steel, or alloy steel.
- Plug: The plug opens or closes the flow path. It is typically cylindrical or tapered and features a hole, or port, through its center.
- Stem: The stem connects the plug to the actuator.
- Bonnet: The bonnet covers the valve body and provides a leak-proof closure at the top. It is usually attached to the body with bolts, but it can also be screwed or welded into place.
- Actuator: The actuator rotates the stem, which rotates the plug. Plug valve actuators can be manual (handle), electric, pneumatic, or hydraulic.
2-port vs 3-port plug valve
Plug valves can be 2-port (2-way) or 3-port (3-way) in design. A 2-port plug valve is the typical design that has one inlet and one outlet. The plug either allows flow, blocks flow, or throttles flow. A 3-port plug valve, however, can have different designs:
- L-port plug valve: An L-port plug valve allows flow from one port to two outlets or vice versa. However, it does not allow flow to pass through all ports simultaneously.
- T-port plug valve: A T-port plug valve permits flow between any two ports or all three simultaneously. This allows for more complex flow-switching or diverting applications.
Non-lubricated vs lubricated plug valve
Plug valves can be non-lubricated or lubricated:
- Non-lubricated: Non-lubricated plug valves have an elastomeric sleeve that fits over the plug and reduces friction between moving parts. This type of plug valve requires less maintenance because it does not need to be relubricated. However, the sleeve may eventually wear out over time and use.
- Lubricated: Lubricated plug valves use a lubricant to reduce friction inside the valve and provide a better seal. This type of plug valve can handle higher pressures, temperatures, and abrasive materials. However, as mentioned above, the lubricant wears down and must be replaced periodically.
Plug valve working principle
Plug valve have a straightforward working principle that is based on the rotational movement of the plug to control the flow of fluid:
- Open position: When the stem is rotated to open the valve, the plug's hollow part aligns with the fluid flow. Fluid can flow through the valve unobstructed.
- The transition between open and closed positions: When the plug is rotated from open to closed or vice versa, part of the plug's hollow section is obstructed, restricting and throttling the flow.
- Closed position: In the closed position, the solid part of the plug blocks the flow path, preventing fluid from passing through the valve.
L-port and T-port plug valve working principles
L-port and T-port plug valves have unique working principles related to the plugs' port configurations:
- L-port plug valve: The flow path through an L-port plug valve is L-shaped. When the plug rotates 90°, the flow path is changed from one port to another. This allows for simple flow diversion applications.
- T-port plug valve: The flow path through a T-port plug valve is T-shaped. When the plug is rotated to different positions, it can either connect all three ports, connect two ports and block the third, or block all ports. T-port plug valves are suitable for diverting, mixing, or even shutting off flow.
Advantages and disadvantages
Plug valves have the following advantages:
- Simple design and operation
- Durability
- Fast operation
- Tight sealing
- Versatility
- Flow control
Plug valves have the following disadvantages
- Lubricated plug valves require regular maintenance.
- Non-lubricated plug valves are more likely to leak when the elastomer sleeve wears down.
- Plug valves offer throttling capabilities but only to a limited extent.
Plug valve applications
Plug valves are used in various industrial applications because they regulate flow rates, stop and start flow, and provide both-directional and throttling capabilities. Typical plug valve applications are:
- Gas processing industries: Plug valves are used in gas processing plants because they can handle high-pressure and temperature conditions. They also provide a tight seal, which is necessary for handling gasses.
- Petroleum and chemical industries: Plug valves can manage various fluid properties, including corrosive, flammable, toxic, and thick fluids. This makes them ideal for the petroleum and chemical industries.
- On/off control: Plug valves provide quick and reliable on/off control over media.
- Liquid handling: Plug valves can handle high flow rates and minimally resist flow, making them suitable for liquid handling applications.
- Throttling control: Plug valves can regulate flow rates.
- High-viscosity fluids: Plug valves do well handling high-viscosity fluids due to the valves' straight flow path.
- High-temperature applications: Plug valves hold up well in high temperatures.
- Vacuum control: Plug valves provide a reliable enough seal for vacuum applications.
Unsuitable applications
As seen above, plug valves are suitable for a wide range of application types. However, there are some system factors that may make plug valves less than ideal:
- Extremely high-pressure applications: Plug valves typically have lower pressure ratings than ball valves and gate valves. Therefore, plug valves may not be suitable for very high-pressure applications.
- Very precise flow control: While capable of throttling flow, plug valves are not as precise as other valve types, such as globe valves.
- Sanitary applications: Plug valves are not the best choice for applications that require high-sanitary standards. Diaphragm valves are well-suited for these types of applications.
To learn more about how plug valves compare with other valve types, read our articles on plug valve vs ball valve and plug valve vs gate valve.
Selection criteria
Consider the following factors when selecting a plug valve:
- Fluid type: Lubricated plug valves are better suited for corrosive, high-temperature and pressure, and abrasive fluid.
- Flow control needs: A 2-port plug valve will suffice for simple on/off control. A 3-port plug valve can provide diversion and mixing operations.
- Maintenance capabilities: If regular lubrication is not suitable, a non-lubricated plug valve is the better option.
- Material compatibility: Ensure the valve's material is compatible with the media. For example, a plastic or specially coated plug may be necessary for corrosive media.
- Size and end connections: The valve's size must match the pipe's size. The end connections (e.g., threaded, welded, flanged) should be compatible with the existing pipeline for easy installation.
FAQs
What is a plug valve used for?
A plug valve is a quarter-turn control valve that is primarily used to provide on/off flow control. It also has low level throttling capabilities.
Is a plug valve a shutoff valve?
Yes, a plug valve can be used as a shutoff valve.
What's the difference between a plug valve and a gate valve?
Plug valves are easier and faster to operate than gate valves.