Diaphragm Valve Detailed Overview and Selection Guide
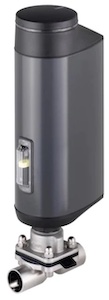
Figure 1: An electrically actuated diaphragm valve
Diaphragm valves, utilize an elastomeric diaphragm that interacts with a seat to regulate or completely stop the fluid flow. The diaphragm's flexibility allows it to move up or down, adjusting the fluid flow rate accordingly, and ensures a tight seal when closed against its seat. Diaphragm valves are linear motion valves, ideal for controlling fluid movement with high precision.
Diaphragm valves, also called membrane valves, can handle various types of media, including liquids, gasses, and semi-solids like slurries, even with solid particles. This is especially useful for industries working with thick or harsh materials. Their simple design lowers the chance of sediment and biofilm build-up, important for clean industries like food and pharmaceuticals. They are also great for managing wastewater, proving their worth in environmental care, such as water and sewage treatment. Diaphragm valves are also used in industries like electronics manufacturing and pulp and paper production.
View our online selection of diaphragm valves!
Diaphragm valve parts and design
As seen in Figure 2, a diaphragm valve has the following primary components:
- Actuator (A): A manual diaphragm valve has a handwheel for actuation. Pneumatic and electric actuators can also be used in place of the handwheel for automation and remote operation.
- Stem (B): The stem connects the actuator to the compressor. The actuator moves the stem up and down, which moves the compressor up and down.
- Compressor (C): The compressor is disc-shaped. It connects the stem to the diaphragm and distributes the stem's force to improve throttling and control.
- Diaphragm (D): The diaphragm is a rubber disc that rises to allow flow and lowers to the valve seat to block flow.
- Bonnet (E): The bonnet bolts onto the valve body. It protects the valve stem and packing from the environment. Bonnets in properly functioning diaphragm valves do not interact with the media.
- Valve body (F): Media flowing through the diaphragm valve goes through the valve body. The volume of the valve body determines the valve's flow rate when it is fully open.
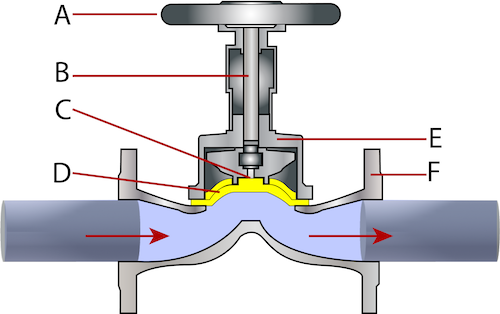
Figure 2: The components of a diaphragm valve: handwheel/manual actuator (A), stem (B), compressor (C), diaphragm (D), bonnet (E), and valve body (F).
Diaphragm valve operation
A diaphragm control valve uses an elastomeric or plastic diaphragm to control flow through the valve. Diaphragm valves are multi-turn valves, meaning the stem must rotate greater than 360° for the valve to open or close fully. When actuated, the diaphragm moves towards or away from the valve seat. The amount the diaphragm is lifted away from the seat controls the flow rate. When the diaphragm closes, its edges press against the valve seat's edges, and the rest of the diaphragm deforms. The diaphragm's shape, when it deforms, fits perfectly with the bottom of the valve seat and creates a tight seal.
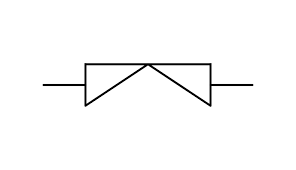
Figure 3: Diaphragm valve P&ID symbol
Types of diaphragm valves
Diaphragm valves come in two main types: weir diaphragm valves and straight/full port diaphragm valves.
Weir diaphragm valves
Weir diaphragm valves have a distinctive raised ridge or weir in the center of the valve body, against which the diaphragm seals to regulate or stop flow.
- Weir design minimizes the diaphragm's travel distance to achieve a full seal, reducing stress and material wear, making it particularly effective for managing both low and high flow rates.
- The weir-type design, being the most popular, is especially suited for throttling applications and fluid flow control at low flow rates.
- It employs a two-piece compressor system for precise flow regulation, with the inner compressor lifting a central portion of the diaphragm in the initial stem travel phases. This design not only extends the diaphragm's life by requiring less material but also makes the diaphragm valve suitable for vacuum and high-pressure applications.
- Weir diaphragm valves are recommended for handling gasses, clean and homogeneous liquids, and even corrosive, hazardous, and abrasive media. However, they may experience increased pressure drops across the valve and are prone to sediment build-up and gumming from viscous liquids on either side of the saddle.
- Bonnet assemblies in these valves ensure safety by preventing fluid release if the diaphragm fails, and their self-draining feature makes them ideal for food processing applications.
Full port diaphragm valves
Full port or straight-through diaphragm valves have a flat-bottomed valve seat, allowing fluid to flow in a straight path with minimal obstruction.
- Straight-through design is characterized by a lower pressure drop compared to weir valves, making it better suited for high-flow rate applications.
- The diaphragm in these valves must be highly flexible to seal against the flat bottom, which subjects it to more wear and tear, necessitating more frequent replacements.
- Straight-through valves excel in handling semi-solid media like slurries, sludges, and viscous fluids, thanks to their unobstructed flow path.
- They are also advantageous for bi-directional flow applications, as there are no saddles to impede flow reversal.
Materials for diaphragm valves
Diaphragm valves come in various materials, making them suitable for multiple applications.
- Typical materials for the diaphragm valve body are PVC, stainless steel, brass, bronze, and cast iron. The material should withstand the environment and media flowing through the valve. For example, stainless steel is commonly chosen for applications requiring sterile conditions (e.g., food and beverage).
- The diaphragm's material is flexible so that the valve can operate correctly. Commonly used materials are EPDM, PTFE, butyl rubber, and nitrile rubber.
Read our diaphragm valve materials article for more details on the temperature ratings and flexibility details of various diaphragm valve materials.
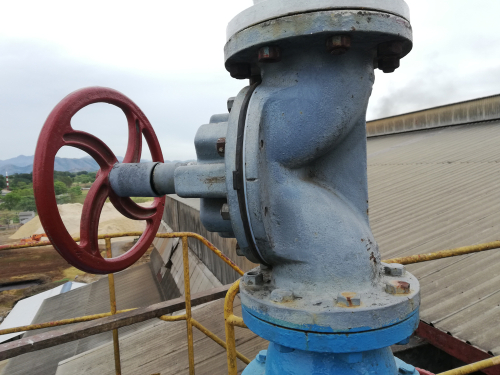
Figure 4: A diaphragm valve used in a hot water pumping system
Selection criteria
- Valve flow coefficient: The diaphragm valve flow coefficient Cv is essential for determining the appropriate size of a diaphragm valve needed to achieve a specific flow rate of fluid. The flow coefficient of a valve increases as the valve opens wider and the stem travels further. An undersized valve (low Cv) will restrict flow, harming performance. Conversely, an oversized valve (high Cv) wastes energy due to excessive pressure drop.
- Pressure drop: Pressure drop is the reduction in pressure from the valve's inlet to its outlet side. When the ratio of this pressure drop across the valve to the total system's pressure drop is low, the flow rate changes minimally until the valve is completely closed. Therefore, a diaphragm valve that opens quickly or acts rapidly is preferred.
- Rangeability: Rangeability refers to a valve's capability to control flow from its maximum to its minimum rate. This characteristic depends on the actuator's size and precision, as well as the design of the valve body, diaphragm, and compressor. A higher rangeability means the diaphragm valve can manage a broader spectrum of flow rates.
- Media: Understand the media's corrosiveness to determine which material to choose for the valve body and diaphragm.
- Temperature: Ensure the diaphragm's material can withstand the application's minimum and maximum temperatures.
-
Flow rate: Select a valve size and style that can provide the flow rate desired for the application.
- Full bore: Low pressure drop and can handle slurries and viscous fluids better.
- Weir: More precise flow control.
- Manual: Cost-effective and direct control of the diaphragm's position.
- Pneumatic: Requires compressed air and provides fast response time.
- Electric: Requires electricity and provides very high precision.
Diaphragm valve advantages
- Leak-free operation: The diaphragm provides an effective seal between the valve body and the stem, significantly reducing the risk of leaks. This is particularly beneficial in applications where leakage could be hazardous or costly.
- Contamination control: Since the media only contacts the valve body and diaphragm, there is a reduced risk of contamination. The design minimizes areas where sediments or biofilms could accumulate, making these valves extremely clean and suitable for applications requiring high hygiene levels.
- Excellent flow control: Diaphragm valves offer precise flow control across a wide range of flow rates, making them suitable for throttling applications.
- Suitability for aggressive media: These valves are particularly effective for corrosive, viscous, and abrasive media, including slurries, due to their robust design and material selection.
- Simple maintenance: The diaphragm is easily replaceable without needing to remove the valve from the pipeline, facilitating straightforward maintenance and reducing downtime.
Read our article on diaphragm valve applications for more details on the various applications of diaphragm valves.
Diaphragm valve disadvantages
- Pressure and temperature limitations: Diaphragm materials can limit the valve's ability to operate under high temperatures and pressures, making them unsuitable for certain applications.
- Diaphragm wear and tear: The diaphragm is susceptible to wear, requiring more frequent maintenance or replacement compared to some other valve types. Also, extensive use in severe throttling applications can lead to diaphragm erosion, impacting valve performance and longevity.
- Slower actuation: Diaphragm valves typically have slower response times due to their multi-turn operation, which may not be ideal for applications requiring rapid actuation.
- Moderate pipeline temperatures and pressures: These valves are best suited for moderate conditions, as extreme temperatures and pressures can exceed the diaphragm's capabilities.
- Limitations with high hydrostatic pressures: The diaphragm's design can restrict its use in systems with high hydrostatic pressures, potentially limiting its application scope.
- Drainage issues: The valve's weir may prevent full drainage of the piping system, which could be a significant drawback in certain applications requiring complete system drainage.
FAQs
What are the primary applications of 3 way diaphragm valves?
3-way diaphragm valves are used in fluid control applications, mixing or diverting flow paths in pharmaceutical, food, and biotech industries.
What material is commonly used for diaphragm valve seats, and why?
PTFE or EPDM are common for diaphragm valve seats due to their chemical resistance and suitability for sanitary applications.