Installing, Replacing, and Measuring O-rings
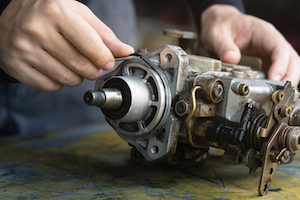
Figure 1: Removing o-ring from a diesel injection pump
O-rings are sealing components used in mechanical systems to prevent fluid leakage. Correct installation is important to ensure proper sealing. If an o-ring needs to be replaced, the replacement needs to be sized properly to ensure optimal performance once it is installed. This article explores the best practices for o-ring installation and removal, helping to ensure the system runs smoothly and efficiently.
Table of contents
- Installing an o-ring
- O-ring replacement
- Removing an o-ring
- Measuring o-rings
- Determining o-ring material
- Hardness of the o-ring material
- Lubrication
- FAQs
View our online selection of O-rings!
Installing an o-ring
Proper o-ring installation ensures proper sealing of mechanical systems, preventing fluids and gasses from leaking out or entering unwanted areas. Installing an o-ring involves several crucial steps that must be performed carefully to avoid damaging the o-ring or compromising its performance. Here's a general overview of the installation process:
- Choose the right o-ring size and material: Selecting the right o-ring size and material is crucial. The o-ring should be compatible with the contact fluid, and the size should fit snugly into the groove (discussed in depth later in the article).
- Clean the o-ring and groove: The groove where the o-ring is installed must be clean and free from any dirt, debris, or previous sealant residue. Also, ensure the o-ring is clean and free from debris or damage. Use a clean, lint-free cloth to wipe the groove clean.
- Lubricate the o-ring: Lubricating the o-ring and the groove with a compatible lubricant is critical to ensure it slides into the groove smoothly without any twisting or damage (discussed in depth later in the article).
- Install the o-ring: Carefully place the o-ring into the groove, ensuring it fits snugly and is not twisted or pinched. Use a suitable tool, such as an o-ring pick (Figure 4), to ensure the o-ring is correctly seated. Ensure the o-ring is stretched evenly on all sides for a strong seal.
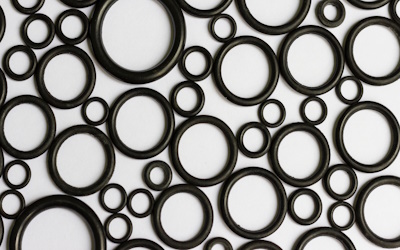
Figure 2: O-rings of various sizes
O-ring replacement
Over time, o-rings can become worn, cracked, or damaged, causing leaks and reducing the effectiveness of the seal. Before replacing an o-ring, determine if it needs to be replaced and why it malfunctions. Replace the o-ring if it develops splits or rough edges on its flattened surface and shows visible signs like cracks, voids, or discoloration. Read our article on preventing o-ring damage for more details on the common reasons for o-ring damage. After deciding that the o-ring requires replacement, remove it from the groove. Next, determine the appropriate size and material for the replacement ring to ensure a suitable fit.
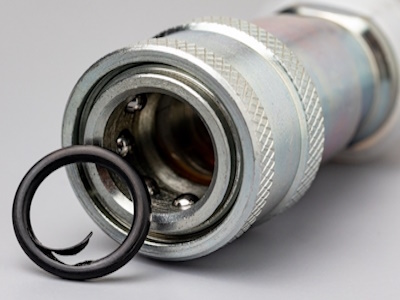
Figure 3: Damaged o-ring
Removing an o-ring
Use an o-ring removal tool like an o-ring pick (Figure 4) to remove the old rings and fit a new one, reducing the likelihood of installation damage. O-ring picks come in various shapes and sizes but typically consist of a long, slender shaft with a pointed or hooked end that can be used to grab and remove o-rings.

Figure 4: O-ring picks
Measuring o-rings
An incorrectly-sized o-ring can lead to leakage. O-rings are typically measured in millimeters. Measure the inner diameter (Figure 5 labeled A), outer diameter (Figure 5 labeled B), and cross-section (Figure 5 labeled C) using a ruler or caliper. Read our article on o-ring sizes for more information on measuring o-rings and the various ISO standards used for their measurements.
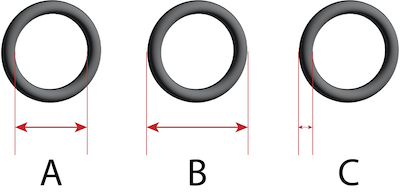
Figure 5: O-ring measurement: Inner diameter (A), outer diameter (B), and cross-section (C)
Determining o-ring material
Choosing the correct o-ring material for a replacement requires consideration of various factors, including the application's operating conditions and the material compatibility with the fluid being used. Several methods are available to identify the material if it has not been initially discovered.
Use a rubber indicator test
This testing device comprises of a tube containing a specific magnitude weight (Figure 6 labeled A). The weight descends a predetermined distance for each material, as shown on Figure 6.
- Keep the o-ring on a stable and flat surface (Figure 6 labeled B).
- Position the testing device over the o-ring and lift the weight to the topmost point of the tube. Then allow it to drop onto the o-ring.
- Upon impact, the o-ring will rebound, and the height of the first bounce will fall into one of four calibrated ranges.
- The highest range corresponds to Ethylene Propylene (Figure 6 labeled E), followed by Nitrile (Figure 6 labeled N), Kalrez (Figure 6 labeled K), and the lowest range indicates Viton (Figure 6 labeled V).
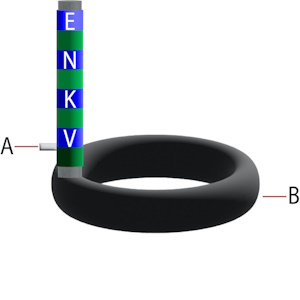
Figure 6: Rubber indicator test: Weight (A) and o-ring (B), Ethylene Propylene (E), Nitrile (N), Kalrez (K), and Viton (V)
Use a seal material guide
Using a seal material guide will indicate the material the previous seal was made of or which material to choose while replacing the seal. Various sealing materials include NBR, FKM, and EPDM. Read our article on o-rings for more information on the advantages, disadvantages, and compatibility of each material with different media.
Hardness of the o-ring material
An o-ring is typically represented by its material, size, and hardness. For example,
NBR O-ring 5.7 X 1.9MM (OD 9.5MM) 70 Shore A
The specification yields the following information:
- The o-ring is made of NBR; it has an inner diameter, cross-section, and outer diameter of 5.7, 1.9, and 9.5 mm, respectively.
- The o-ring has a durometer of 70 Shore A. Shore A is a commonly used durometer scale to measure the hardness of rubber materials. The Shore A scale measures the indentation hardness of the material, which is the material's resistance to permanent indentation or deformation caused by a sharp object pressing against it. The higher the number on the Shore A scale, the harder and less flexible the material. A durometer of 70 Shore A means that the material has a medium hardness, with some resistance to deformation under pressure but still capable of some degree of flexibility.
Note: As a rule of thumb, the smallest dimension in the specification will be the o-ring cross-section, the largest dimension will be its outer diameter, and the intermediate value is its inner diameter.
Lubrication
Proper lubrication of the seal before installation is a crucial step in the installation process that ensures the o-ring remains in excellent working condition for an extended period.
- Lubrication facilitates seating in the groove by reducing or eliminating surface friction.
- Lubrication reduces radial seal installation force and ensures smooth transitions in male and female seals.
The application parameters should be considered when choosing the appropriate lubricant. The lubricant chosen must be:
- compatible with the material being used
- suitable for the temperature range of the application
- suitable for system fluids
- capable of producing a high surface tension film
- should not clog system filters
Lubricant types
- General-purpose grease lubricants: General-purpose grease lubricant is excellent for o-ring and elastomer seal varieties used in hydrocarbon service. General-purpose grease lubricant has a recommended service temperature of -29 𐩑C - 82 𐩑C (-20 𐩑F - 180 𐩑F).
- High-viscosity silicone oil: High viscosity silicone oil is an ideal all-purpose o-ring lubricant. It is an incredibly efficient seal lubricant and can be utilized in temperatures between -54 𐩑C - 204 𐩑C (-65 𐩑F - 400 𐩑F).
FAQs
How are o-rings measured?
O-rings are measured by their inside, outside, and cross-sectional diameter. O-ring measuring tools like rulers or calipers can be used for these measurements.
What is an o-ring installation tool?
An o-ring installation tool is designed to assist with installing o-rings into their intended groove or housing. O-ring pliers and pick tools are examples of installation tools.