Pressure Drop
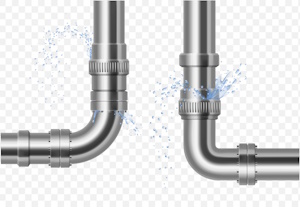
Figure 1: Pipeline leak causing pressure drop
The pressure drop is the difference in pressure between two points in a system. It is often caused by friction or flow resistance from pipe walls, fittings, or obstructions such as valves. This article discusses the pressure drop formula, its significance, and its effect in various situations.
Table of contents
- What is pressure drop?
- Pressure drop significance
- Pressure drop formula
- Pressure drop and flow rate
- Pressure drop in various situations
- FAQs
What is pressure drop?
Pressure drop is the reduction or loss of fluid pressure as it travels through a system. Pressure drop is common in various situations, such as when fluid flows through a pipe, over an orifice, or a valve. This is typically caused by:
- Friction between the fluid and the pipe's interior surface
- Pipeline blockages
- Change in the pipe's direction
Pressure drop significance
Calculating the pressure drop is essential for designing and maintaining the system's integrity. Pressure drop is a diagnostic tool pinpointing problems within a pipeline system. For instance:
- A sudden spike in pressure drop could signal a blockage, a partially shut valve, or a leak in the pipeline.
- In a heating system, a valve controls the flow of hot water to sustain a particular temperature. The pressure drop across the valve affects the volume of hot water circulating through the system, thereby influencing the system's ability to attain and maintain the target temperature.
In general, valve pressure drop calculations play a crucial role in the following:
- Valve size: Pressure drop calculations are necessary to size the valve accurately. A large valve can result in high flow rates, which may expedite valve wear and tear. Conversely, a small valve can lead to an unnecessary pressure drop, leading to energy wastage and reduced system efficiency.
- Predicting system performance: The calculations determine pump power requirement and fluid flow rate.
- System design and integrity: The calculations are a diagnostic tool for identifying pipeline issues.
- Anticipating maintenance: Tracking pressure drops over time helps plan inspections and cleaning.
Read our off-grid elevated water system design article for more information on the layout and working of an off-grid gravity-assisted water system for a cabin.
Pressure drop formula
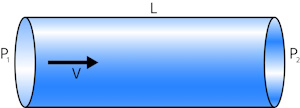
Figure 2: Fluid flow through a pipe: input pressure (P1), output pressure (P2), pipe length (L), and fluid velocity (V)
The pressure drop in a pipe arises from friction between the fluid and the pipe wall, changes in flow direction, blockages, and alterations in pipe diameter. Pressure drop can be calculated using the Darcy-Weisbach formula. In a pipeline system consisting of multiple pipes, valves, and fittings, the total pressure drop is the sum of the pressure drops in each component.
The pressure drop equation (Darcy Weisbach formula) is given by,
- ΔP: Pressure drop
- f: Darcy friction factor
- L: Pipe length
- V: Flow velocity
- D: Pipe diameter
- 𝜌: Fluid density
The Darcy friction factor is primarily determined by the flow type (laminar or turbulent) and the roughness of the pipe's internal surface. It can be obtained using lookup tables, correlations, or software from experimental data.
Example
Determine the pressure drop of water in a 100 m long pipe having a diameter of 0.1 m. Take the friction factor as 0.03 and flow velocity as 30 m/s.
- L = 100 m
- D = 0.1 m
- f = 0.03
- V = 30 m/s
- 𝜌 = 1000 kg/m3
Substituting these values in the above equation, the pressure drop = 13.5 MPa, which is quite significant. This would require strong, high-quality equipment to withstand the pressure and maintain efficient operation. It also means the pump must generate a pressure significantly above 13.5 MPa to maintain the desired water flow rate. This requires high energy consumption and increases operational costs. Therefore, it is essential to consider pressure drop when designing and operating the system.
Pressure drop in fittings
In long pipelines, the pressure drop due to friction in the straight pipe is much larger than the pressure drop caused by the fittings and valves. This is because the frictional losses are proportional to the length of the pipe.
As the pipes get shorter, the proportion of the losses due to the fittings and valves gets larger. However, even in a short pipe, the pressure drop due to friction in the straight pipe is still much larger than the pressure drop due to the fittings and valves. This is why the pressure drop caused by the fittings and valves is still called 'minor losses.' While individual minor losses might seem small, they can add up, especially in complex systems with many fittings and turns.
Pressure drop through fittings is calculated using the equivalent length method. The equivalent length method allows the user to describe the pressure loss through a fitting as the length of the pipe. Consider an elbow fitting with a 0.05m diameter. In many pipe material specifications, there are tables that provide the equivalent length for different types of fittings. For example, a standard elbow fitting might have an equivalent length of 30 pipe diameters.
The equivalent length for a 0.05m diameter elbow would be 30 * 0.05m = 1.5m. Considering a flow velocity of 2 m/s, friction coefficient of 0.025, and using the Darcy Weisbach formula, the pressure drop through the fitting is 1.5kPa.
Pressure drop and flow rate
Flow coefficient Cv or Kv and pressure drop are inversely related. A valve with a high Cv allows for a greater flow, thus causing a smaller pressure drop across the valve for a given flow rate. Conversely, a valve with a low Cv will cause a higher pressure drop for the same flow rate.
It's important to balance these two factors in valve sizing and selection. If a valve is too small for the system, it will have a low Cv and may cause a high pressure drop, leading to poor system performance. On the other hand, a too large valve may not adequately control the flow rate.
Pressure drop in various situations
This section discusses the various instances where pressure drop can be observed.
- Pressure drop across an orifice: As the fluid travels through an orifice, it changes speed and pressure, resulting in a pressure drop. The magnitude of this drop is dependent on the fluid's properties, the orifice's size, and the flow speed.
- Pressure drop across a valve: Valves contribute to pressure drop while controlling a system's fluid flow rate. The extent of this drop is influenced by the valve's design, size, flow rate, and the fluid's properties.
- Water pressure drop per 100 ft: This measure is commonly used in pipeline systems to assess the pressure loss due to friction over a specific pipe length. It depends on the pipe's material, diameter, the water's speed, and temperature.
- Filter pressure drop: Filters contribute to pressure drop while removing unwanted particles from fluids. The pressure drop depends on the filter design, cleanliness, fluid properties, and flow rate.
Read our article on pressure drop in gravity-fed water system for more details on the pressure drop in a gravity-fed system, its causes, and maintenance solutions.
FAQs
Why is calculating pressure drop important?
Calculating pressure drop helps in efficient system design and flow control and ensures the safety and longevity of equipment.
How does pipe size affect pressure drop?
Larger pipe diameters reduce pressure drop by reducing fluid velocity and friction. Smaller pipes increase pressure drop.