What Is an O-ring And Its Purpose
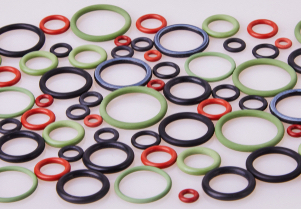
Figure 1: NBR o-rings
An o-ring is a circular mechanical gasket used to create a leak-free seal between two components. The o-ring sits in a groove and gets compressed during assembly between two or more parts, creating a reliable seal at the interface. O-rings are commonly used in mechanical designs as they are easy to make, inexpensive, and have simple mounting requirements. This article explores what an o-ring is, how it works, and its types.
Table of contents
- What is an o-ring
- Working principle
- Advantages
- Static and dynamic o-rings
- O-ring materials
- Selecting an o-ring
- Applications
- FAQs
View our online selection of O-rings!
What is an o-ring
O-rings are circular elastic loops that serve as seals for both stationary and moving applications. Their primary function is to provide a sealing mechanism between structures, such as pipes, tubes, pistons, and cylinders. Depending on the intended use, o-rings are manufactured using different materials and are highly flexible.
O-rings are used in various applications, from hydraulic and pneumatic systems to automotive engines and aerospace components. Their resilience allows them to maintain their shape and sealing properties over time, even after repeated compressions and decompressions.
Working principle
An o-ring seal consists of the o-ring and a gland, which is the location where the o-ring goes. The gland is typically a groove or channel cut into a metal or plastic component, such as a cylinder or a valve body, where the o-ring is placed and compressed between two mating surfaces. The gland ensures that the o-ring is properly positioned and sealed to prevent leakage of fluids or gasses.
- When compressed between the two mating surfaces, the o-ring material deforms and fills any gaps or imperfections. This creates a barrier that resists fluid leakage even under extremely high or low pressures.
- The materials that o-rings are made from (elastomers) are naturally spring-like and return to their original shape. Therefore, when the pressure ceases, they spring back to their original position, maintaining a seal and being ready for the next cycle.
Advantages
O-rings offer several advantages over other sealing methods, including their ability to create a reliable and leak-free seal in various applications. Some of the advantages include:
- O-rings seal over a wide range of pressure, tolerance, and temperature
- Easy to use
- Doesn't cause structural damage to the equipment while or after mounting
- Mostly reusable
- Light-weight and compact
- The o-ring failure takes time and can be easily identified
- Cost-effective
In an industrial setting, the wear and tear of an o-ring can have a significant impact on productivity. Therefore, it is recommended to ensure a sufficient supply of replacement o-rings in appropriate sizes; this enables the immediate replacement of a worn-out o-ring. O-rings are generally categorized by their function and the materials used to produce them.
Static and dynamic o-rings
Static o-ring
A static o-ring creates a dependable, leakproof seal between two stationary parts, such as a pipe and a fitting. To achieve this, a groove is cut on the flat surface, and an o-ring of the appropriate dimension and size is inserted into the groove. Subsequently, the o-ring is compressed in place by a second flat surface (the surface that exerts pressure on the o-ring). Once the connection is established, the application remains static, and the o-ring remains stationary and does not move.
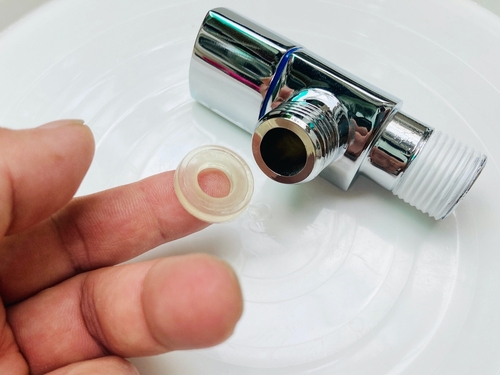
Figure 2: An o-ring for a faucet (static o-ring)
Dynamic o-ring
A dynamic o-ring creates a seal between two surfaces in relative motion or moving against each other. These o-rings are typically utilized in applications with movement or rotation, such as in engines, hydraulic and pneumatic systems, and other mechanical devices. Unlike static applications, dynamic applications cause o-rings to wear faster in constant motion. Therefore, it is essential to lubricate dynamic o-rings regularly to ensure their longevity and effectiveness. Compared to static o-rings, the materials for dynamic o-rings should be:
- Stronger
- Tougher
- More resistant to friction and abrasion
Dynamic o-rings are commonly used to create reciprocating or rotary seals.
- Reciprocating seal: A reciprocating seal is used in applications with back-and-forth or reciprocating motion, such as piston or cylinder. Reciprocating seals are designed to maintain a seal between two surfaces moving in opposite directions while also withstanding the friction and wear resulting from this motion.
- Rotary seal: A rotary seal maintains a seal between two surfaces that are rotating against each other, such as in a shaft or bearing. Rotary seals are designed to prevent fluid leakage while withstanding the friction and wear resulting from rotation.
O-ring materials
O-rings are frequently utilized in high-pressure applications where the pressure deforms the o-ring within the groove, resulting in uniform mechanical stress on the surface. Maintaining a pressure gradient that remains below the o-ring's stress rating is crucial to prevent any leaks or seepage. However, mechanical failures in some instances can cause extrusion and destruction of the o-ring. To prevent this, selecting the appropriate material for the particular application is necessary. These materials include a range of rubber, silicone, and polymer compounds. The selection of materials for o-ring manufacturing is based on their ability to exhibit specific traits such as elasticity and strength, which are crucial due to the critical and demanding environments in which o-rings are typically utilized.
FKM (Viton)
- Good chemical resistance, mechanical properties, and resistance to compression set
- Designed to operate between -10 °C and 120 °C (-14 - 248 °F)
- Good resistance to oils and solvents such as aliphatic, aromatic and halocarbons, acids, animal and vegetable oils; not resistant to methanol
- Poor resistance to hot water and steam as FKM swells at high temperatures
- Unsuitable for polar solvents, certain esters and ethers, and glycol-based brake fluid
EPDM (Ethylene Propylene Diene Monomer)
- Suitable for water, steam, ketones, alcohols, brake fluids, acids/alkalis in low concentrations
- Very good resistance to weather influences and ozone
- Poor resistance to oil, grease, and solvents and unsuitable for aromatic hydrocarbons
NBR (Nitrile Butadiene Rubber)
- Also known as acrylonitrile butadiene or Buna-N
- Good resistance to compression, tearing, and wear
- Compatible with oil products, solvents, and alcohol
- Sensitive to weather influences, moderate temperature resistance, unsuitable for brake fluid and polar solvents
PTFE (Polytetrafluoroethylene)
- Exceptional chemical resistance
- Designed to operate between -20 °C and 180 °C (-4 - 356 °F)
- PTFE rings are naturally white and can withstand a wide range of substances, including chemicals, acids, oils, and steam.
- PTFE possesses high toughness and abrasion resistance; however, they cannot be compressed easily, which may result in less effective sealing.
Silicone
- Resistant to the harmful effects of oils, chemicals, heat, ozone, and solvents
- Flexible even at low temperatures
- Functions within a temperature range of -60 °C to 225 °C (-76 - 437 °F), while specifically engineered types can endure temperatures spanning from -100 °C to 300 °C (-148 - 572 °F)
Selecting an o-ring
Here's a step-by-step guideline on how to select an o-ring for a particular application.
- Determine the o-ring material: Determine the o-ring material based on the application requirements like temperature, pressure, and media. Getting an o-ring replacement can be difficult if the material of the existing o-ring is not known. Use a rubber indicator test to determine the material.
- Measure the o-ring size: O-rings are usually specified by their inner diameter, outer diameter, and cross-sectional width. At times, o-rings of standard sizes may not be suitable for specific requirements in existing systems; use custom-made o-rings in this case. Read our article on o-ring sizes for more information.
- Determine the hardness: The hardness of the o-ring determines its ability to resist extrusion and deformation. Hardness is measured in a durometer and can range from 30-90. For example, an o-ring with a durometer reading of 60 is softer than 70, while 90 is stiff compared to a reading of 70.
- International standards: O-rings are manufactured to conform to various international standards such as ISO, DIN, and JIS. These standards ensure that o-rings have uniform dimensions, tolerances, and material properties, making them interchangeable and compatible with different applications. A few examples of these standards specific to o-rings are ISO 3601, DIN 3771, and JIS-B2401.
- Special cases: There are various o-ring types designed for specific connections or applications. For example, SAE (Society of Automotive Engineers) flange o-rings are designed to fit into SAE flange connections commonly used in hydraulic systems.
Applications
The versatility and reliability of o-rings make them an essential component in many industries and applications. Here are a few examples:
- Aerospace and aviation: aircraft engines, hydraulic systems, and other critical components
- Medical devices: medical equipment such as syringes, pumps, and valves
- Plumbing: pipes, faucets, valves, and other plumbing components to prevent leaks
- Hydraulics and pneumatics: create a seal between moving parts such as cylinders, actuators, and pistons
- Food and beverage processing: processing equipment to prevent contamination and ensure hygiene
- Electronics: electronic components such as connectors and switches to prevent moisture and dust from entering
- Common household applications: Doors, windows, and containers to prevent leaks and maintain airtight or watertight seals
FAQs
How to identify an o-ring material?
Use a rubber indicator test to determine the material of the existing o-ring; this helps get a suitable o-ring replacement.
What are the various types of o-ring materials?
FKM, EPDM, NBR, PTFE, and silicone are the most common materials used for making o-rings.