Fertilizer Dosing With Electric Actuated Valves
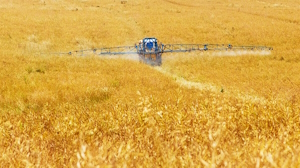
Figure 1: Electric valves provide the automation and precision necessary to optimize crop fertilization.
Electrically actuated valves in fertilizer dosing systems provide precise nutrient delivery to crops, improving growth while reducing waste and environmental impact. Despite their benefits, these systems face challenges due to the corrosive nature of fertilizers and valve wear. Selecting the appropriate valve type and material is crucial to ensure durability, functionality, and cost-effectiveness in agricultural use.
Table of contents
- Fertilizer & corrosion
- Electric valve materials
- Electrically actuated valves used for fertilizer dosing
- Seal materials
View our online selection of valves for fertilizer dosing systems!
Fertilizer & corrosion
Fertilizer equipment frequently faces corrosion challenges due to the fertilizers' properties. These substances often react with metals, leading to the formation of compounds like ammonia or hydrogen sulfide. Solutions containing acid fertilizers with chloride, particularly those with a pH below 3.5, are highly corrosive. Liquid fertilizers based on nitrogen, such as ammonium nitrate and urea, react slowly with steel, with the reaction rate increasing at welded joints, bolts, and holes. Conversely, phosphate-based solutions like ammonium phosphate are less aggressive. They can create a protective phosphate layer that protects the metal from further reaction with nitrogen-based solutions.
Even in dry storage conditions, fertilizers can draw moisture from the air and become corrosive. Corrosion tests indicate that carbon steel is vulnerable to nitrogen-based fertilizers. In contrast, aluminum, chromium, and chromium-nickel stainless steel have resistance. Among these, chromium-nickel stainless steels stand out for their resilience in mixed fertilizer solutions. Galvanizing steel can provide a degree of protection against corrosion.
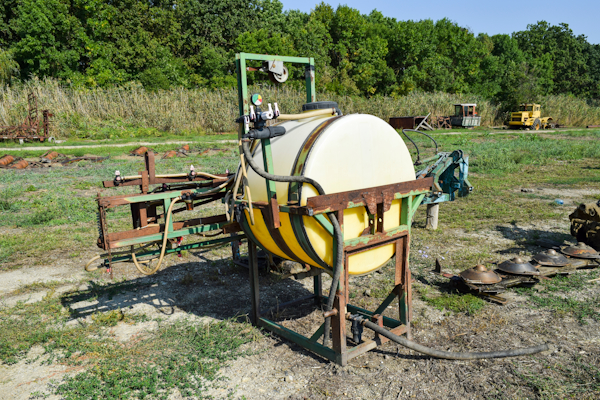
Figure 2: Liquid fertilizer systems (e.g., sprinkler systems) have valves, fittings, and pipes that are vulnerable to corrosion.
Inhibitors such as thiourea, ammonia thiocyanate, and Z-mercapto benzothiazole can be added to fertilizers to protect mild steel exposed to ammonium nitrate or ammonia. Polysulphates like sodium polyphosphate and dibasic ammonium phosphate can be used for aqueous ammonium nitrate, ammonium, and urea solutions.
Electric valve materials
The following materials are best suited for containing and handling fertilizers, ranked in order of preference based on corrosion resistance and overall chemical properties:
- 304 and 316 stainless steels
- Aluminum
- Carbon steel
- PVC
- Brass
Stainless steel
Stainless steels, particularly 304 and 316, are commonly used to handle liquid fertilizers due to their strength, corrosion resistance, ease of cleaning, and abrasion resistance. The nickel content imparts toughness and corrosion resistance, while the chromium forms a thin oxide film that protects the surface from corrosion. However, stainless steel valves are prone to stress corrosion cracking.
Aluminum
Aluminum and its alloys are generally corrosion-resistant as they form a protective oxide layer on the metal surface. However, they offer low resistance to chemicals that can attack this layer. They are susceptible to attack by acids and caustic solutions, especially in the presence of chlorides, where they can exhibit corrosion cracking. They offer the best corrosion resistance in the pH range of 4.5 to 7.0.
Carbon steel
Carbon steel is normally suited for handling anhydrous ammonia but is susceptible to acids and acidic fertilizers. It has limited corrosion resistance to fertilizer solutions despite the availability of many types with different carbon content and properties.
PVC
Plastics such as PVC are corrosion-free and used in low-cost applications, making them suitable for handling corrosive fertilizer solutions. However, they have limited resistance to temperature, pressure, and abrasion.
Brass
Brass offers moderate strength and toughness but has low corrosion resistance to liquid fertilizer solutions consisting of ammonium nitrate and ammonium phosphate.
Other alloys
Other alloys such as Monel, Hastelloy, Inconel, and alloys of tantalum, zirconium, titanium, and nickel offer excellent corrosion resistance but are not widely used in fertilizer handling due to very high costs.
Electrically actuated valves used for fertilizer dosing
-
Needle valves:
- Utilized for precise flow regulation of fertilizers into irrigation systems.
- Often found in drip irrigation setups to finely adjust the rate of nutrient delivery.
- Employed in small-diameter tubing to control the low flow rates required for accurate fertilization.
- Not suitable for large flow rates.
- Learn more in our needle valve overview article.
-
Electric ball valves:
- Suitable for quick and reliable shutoff or activation within the fertilization system, ensuring timely distribution of nutrients.
- Often used in larger-scale systems where the precise control of high-volume fertilizer flow is necessary.
- A dosing ball valve's robust design allows for long-term operation with minimal maintenance, making them a durable choice for harsh fertilization environments.
- For more information on automatically actuated ball valves, read our guide on pneumatic and electric ball valves.
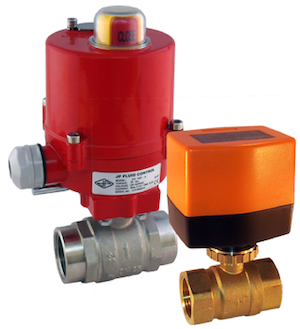
Figure 3: Electric ball valves offer reliable shutoff/activation for larger flow rates.
-
Globe valves:
- Serve as throttling valves to manage the flow and pressure of fertilizers within the system.
- Used in larger fertilization systems where variable flow rates are needed.
- Provide better shut-off capabilities than some other valve types, making them suitable for stopping and starting fertilizer flow.
- Read our globe valve overview article to learn more.
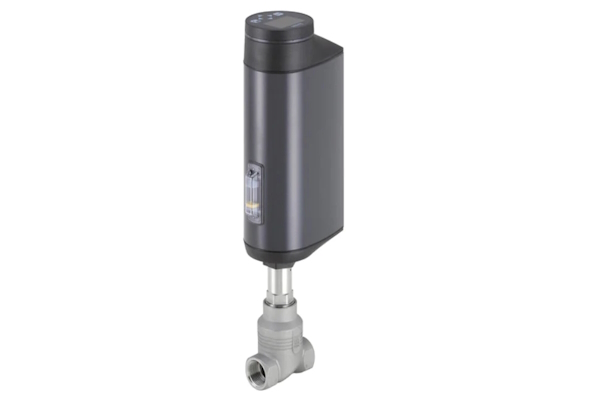
Figure 4: Electric globe valves are used to throttle various flow rates.
-
Angle seat valves:
- Ideal for on/off control of fluid flow at high pressures.
- Their angled design facilitates the flow of viscous fertilizers with minimal pressure drop.
- Commonly used where space is limited due to their compact design and ability to be installed in tight areas.
- To learn more, read our angle seat valve article.
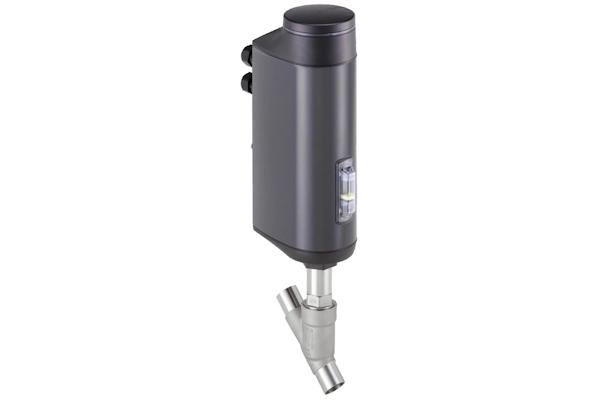
Figure 5: Angle seat valves are optimal for high-pressure systems.
-
Solenoid valves:
- 2-way solenoid valves control the start and stop of fertilizer flow electronically, allowing for automated fertilization cycles.
- 3-way solenoid valves can divert flow between different paths in the system, enabling more complex fertilization schedules and the mixing of different nutrients.
- Integral to automated fertilization systems, responding to timers or sensor inputs to ensure precise nutrient application.
- Find out more in our solenoid valve overview article.
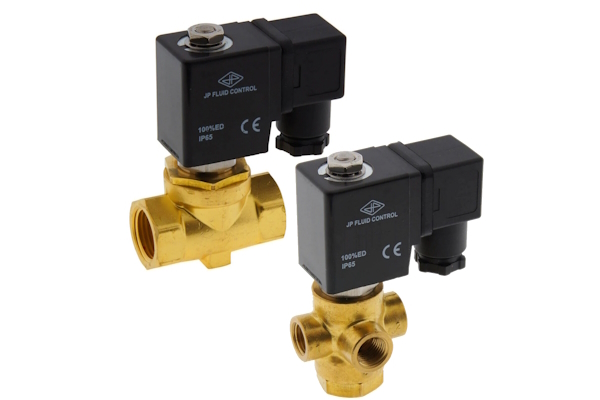
Figure 6: Solenoid valves offer near-instantaneous response times for a variety of application demands.
-
Pressure control valves:
- Regulate the pressure within the fertilization system to optimal levels for efficient nutrient delivery.
- Automatically adjust to maintain a set pressure, ensuring consistent flow rates and preventing system damage due to pressure fluctuations.
- Essential for maintaining the balance between different parts of the fertilization system, especially when varying flow rates and pressures are required for different crops or stages of growth.
- There are various types of pressure control valves, learn more about the types in the following articles:
- Pressure safety valve vs pressure relief valve
- Pressure regulators
Seal materials
Various seals are used in fertilizer dosing valves, such as:
-
PTFE (Polytetrafluoroethylene): Commonly known as Teflon, PTFE seals:
- Are non-reactive
- The most chemically stable compared to all plastics
- Have excellent thermal and electrical insulation properties
-
NBR (BUNA-N): NBR seals:
- Have good resistance to water and hydraulic fluids
- Good tensile and compressive strength
- High abrasion resistance
-
EPDM (Ethyl-Propylene): EPDM seals:
- Offer very good chemical resistance to various acids and weak alkaline solutions
- Good abrasion, tear, and heat resistance
- Can withstand various weather conditions
- Poor resistance to concentrated acids and strong alkaline solutions
-
FKM: Popularly known as Viton, FKM seals:
- Are chemically compatible with various concentration solutions
- Suitable for use across a wide temperature range
- Can be used with various mineral acids and salt solutions
- High heat resistance