Pressure regulators
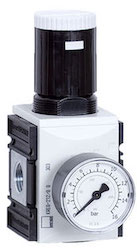
Figure 1: A pressure regulator
A pressure regulator controls the pressure of liquids or gases by reducing high input pressure to a lower, constant output pressure, even with inlet pressure fluctuations. They are used in various domestic and industrial applications, such as regulating propane in gas grills, oxygen in healthcare equipment, compressed air in industrial settings, and fuel in automotive and aerospace engines. The key function across these uses is pressure control. This article explores the types of pressure regulators, their applications, and factors to consider when selecting one.
Table of contents
- Components
- Types of pressure regulators
- Applications
- Selection criteria
- Installing a pressure regulator
- Pressure regulator vs other pressure control devices
- FAQs
View our online selection of pressure regulators!
Components
A typical pressure regulator consists of the following elements:
- A sensing element such as a diaphragm, piston, or membrane (Figure 2 labeled A).
- A loading element that applies necessary force to the reducing element, such as a spring, piston actuator, or diaphragm actuator (Figure 2 labeled C).
- An inlet (Figure 2 labeled B) and an outlet (Figure 2 labeled D).
- A pressure-reducing element such as a poppet valve (Figure 2 labeled E).
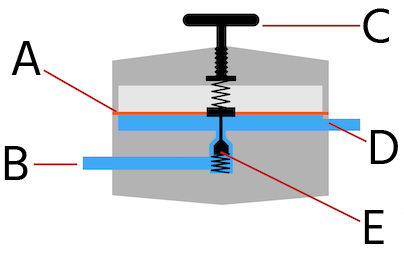
Figure 2: Schematic representation of a typical single-stage pressure regulator with a membrane (A), inlet (B), handle for manual pressure adjustment (C), outlet (D), and poppet valve (E).
Pressure reducing element
A spring-loaded poppet valve is a standard pressure-reducing element in a pressure regulator. Poppet valves have elastomeric sealing for regular applications and thermoplastic sealing for high-pressure applications. The sealing seals the valve against any gas or fluid leakage. Spring force controls the poppet valve by opening it to let media flow from the inlet to the outlet. As outlet pressure rises, the poppet valve closes due to the force of the sensing element, which overcomes the spring force on the poppet.
Loading element
The loading element controls the sensing element which opens the valve. The amount of spring force is adjustable, which determines the amount of outlet pressure obtained.
The sensing element
Pistons are suitable for high pressures, rugged applications, and applications for which wider tolerances on the outlet pressure are acceptable. Pistons tend to be sluggish due to friction between the pinion sealing and regulator body.
For higher accuracy, a diaphragm type of sensing element is suitable. Diaphragms tend to have lower friction than piston-type designs. They also provide a higher sensing area for a given regulator size. They are made of elastomer or a thin disc type of material sensitive to changes in pressure.
Types of pressure regulators
Pressure regulators have the following categories:
- Direct-operated or self-operated
- Pilot-operated
Direct-operated regulators
Direct-operated regulators (Figure 2) are the simplest form of pressure regulators. They usually operate at lower set pressures, below 0.07 bar (1 psi), and can have greater accuracy. At higher pressures, up to 35 bar (500 psi), they can have 10-20% accuracy levels.
Direct-operated regulators are self-contained: they do not require an external sensing line at the output to operate effectively. They consist of a spring-actuated valve that a diaphragm assembly directly controls. Energy or pressure from the flowing media works to activate the diaphragm. The increasing downstream pressure acts on the diaphragm, which closes the valve plug by compressing the spring. As downstream pressure falls, the spring force becomes greater than the force of the medium, acting on the diaphragm and opening the valve.
Pilot-operated regulators
Pilot-operated regulators provide precise pressure control for conditions associated with gas from cylinders or small storage tanks, such as:
- significant variation in flow rates
- fluctuations in inlet pressure
- decreasing inlet pressure conditions
This type of regulator is generally a one- or two-stage device. A single-stage regulator is ideal for a relatively small reduction in pressure. It is not suitable for systems with large fluctuations in inlet pressure or flow rates.
A double-stage regulator (Figure 3) is the most common pilot-operated regulator. The first stage consists of a spring-actuated pilot that controls the pressure on the diaphragm of the main regulating valve. As the pressure increases, the spring compresses, and the pilot valve opens, creating a pressure differential between the inlet side of the main regulating valve and the output valve. This pressure differential actuates the main operating valve, and flow occurs at a reduced pressure through the outlet valve. As long as the pressure of the medium on the spring-actuated pilot is low, there is no flow downstream.
Double-stage pilot-operated regulators accurately regulate a wide range of pressures and capacities. These regulators are applicable with only clean fluids or gasses, as small passages and ports can clog. This arrangement results in a stable and sustained outlet pressure from the second stage despite pressure drops in the first stage.
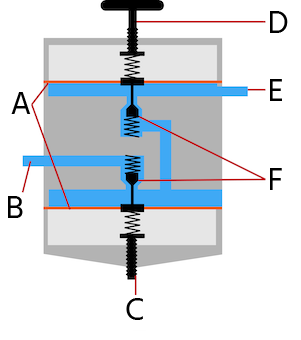
Figure 3: Schematic representation of a double-stage pressure regulator with membranes (A), inlet (B), a factory-set pressure valve (C), a handle for manual pressure adjustment (D), outlet (E), and poppet valves (F).
Applications
Other than reducing input pressure, there are additional functions that a pressure regulator can perform:
Backpressure regulators and pressure relief valves
A pressure relief valve limits system pressure to a prescribed maximum. It diverts some or all quantity of liquid or gas from the pump to the tank when the pressure reaches the set pressure. A backpressure regulator maintains a desired input pressure by means of varying the flow of liquid or gas in response to a change in input pressure.
Pressure switching valves
Pressure switching valves are for pneumatic logic systems. These valves are either 2/2-way or 3/2-way switching.
Air regulator
Air regulators, or air compressor regulators, connect to an air compressor to regulate the pressure setting. The air regulator cannot increase the pressure from the air tank; it can only lower the pressure or return it to the tank’s pressure setting. Therefore, an air regulator allows an air compressor to support various air tools with different pressure requirements. The only necessity is that the air tank’s pressure output can support the air tool with the largest pressure requirement.
Low-pressure air regulator
Low-pressure air regulators are suitable for low-pressure systems. These air regulators use relatively large diaphragms. The large diaphragm increases the surface area on which input air contacts, allowing low-pressure media to open the diaphragm. Also, the large diaphragm supports systems that require high flow rates.
Vacuum regulator
Vacuum regulators control a vacuum. It maintains a constant vacuum at the regulator’s inlet with a higher vacuum at the outlet.
Other applications
Pressure regulators also have the following applications:
- Household/Domestic: Gas grills, gas ovens, pressure cookers, pressure vessels, and home heating furnaces
- Compressed air: Industrial and commercial workshops for cleaning, powering air-actuated tools, and inflating tires
- Aerospace: Propulsion pressurant control engines and fuel lines
- Welding and cutting: Supply gas at necessary pressures from storage cylinders for oxy-acetylene welding. Read our welding regulator article to learn more.
- Gas-powered vehicles: Deliver pressurized gas to the engine
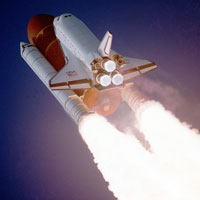
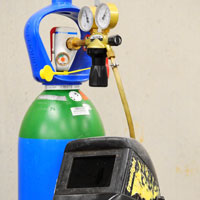
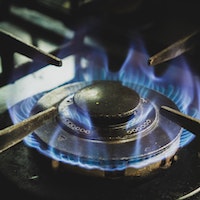
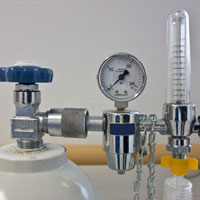
Figure 4: Examples of pressure regulator applications: aerospace, welding, household gas burner and oxygen regulation for medical purposes.
Selection criteria
Pressure regulators are available in various sizes and constructions. Below is a list of considerations when choosing the correct pressure regulator for an application:
- Operating pressure range
- Capacity or flow required
- Nature of the medium (fluid or gas) transmitted
- Operating temperature range
- Material requirements
- Accuracy required
1) Operating pressure range
An application’s requirement for input and output pressures determines the type of regulator to use:
- The supply range of input pressure that a regulator can handle safely.
- The required values of output pressure.
- The required accuracy of output pressure.
2) Capacity or flow requirements
Evaluate the following criteria:
- The maximum flow rate necessary.
- The expected variation in flow rate.
- Correct selection of pipe size.
3) Nature of medium (liquid or gas)
Care should be taken about the type of medium in the regulator:
- Liquid/Gas
- Chemical composition
- Flammability/Explosive nature
- Hazardous/Toxic nature
- Corrosive properties
4) Operating temperature range
The materials for pressure regulators should be such that they need to be able to perform their function effectively at a certain operating temperature range without losing their material properties. The elastomers for regulator sealing are below:
- Nitrile (NBR) or Neoprene (-40 °C to 82 °C)
- Ethylene Propylene (EPDM) or Perfluoroelastomer (FKM) for higher temperatures
5) Material requirements
Depending on the medium and operating conditions, various regulator component materials are available such as:
- Brass: Common and economical
- Plastic: Cost-effective and disposable
- Aluminum: Weight considerations
- Stainless steel: Corrosive environments, high cleanliness requirements, and high operating temperatures.
The seal in the pressure regulator should be compatible with the operating temperature and medium. The size and weight of the pressure regulator are important considerations. The material, required port size, adjustment requirements, and type of mounting should be taken into account to select the appropriate type.
6) Accuracy required
A pressure regulator’s 'droop' value indicates the accuracy of a pressure regulator. Droop is the reduction of output pressure with an increase in fluid flow. For lower accuracy requirements, a relatively higher amount of droop can be acceptable. Pressure regulators with higher droop tend to be more cost-effective. For higher accuracy, the type of construction, optimized valve size, and multi-staged design can reduce the amount of droop.
Installing a pressure regulator
Installing a pressure regulator, whether for water or air systems, is a straightforward process that significantly enhances system efficiency and safety. The installation begins with turning off the system's main supply to prevent any flow during the setup. The regulator is then positioned in the appropriate section of the system, ensuring it aligns correctly with the flow direction, which is crucial for its operation. After securing the regulator in place, the system can be gradually brought back online, and the regulator adjusted to the desired pressure level to ensure optimal performance. For more in-depth information on installing pressure regulators, read our article on pressure regulator installation.
Pressure regulator vs other pressure control devices
Pressure regulators, pressure limiting valves, and pressure relief valves are all integral components in managing system pressures, yet they serve distinct functions.
- Pressure regulators: A pressure regulator's primary role is to maintain a constant output pressure regardless of variations in the input pressure, making it ideal for applications requiring consistent pressure for optimal operation.
- Pressure limiting valve: Pressure limiting valves are designed to prevent the pressure from exceeding a predetermined level, acting as a safeguard against pressure spikes that could damage the system. They repeatedly release pressure to keep it at safe levels.
- Pressure relief valves: Pressure relief valves are safety devices that release excess pressure from a system when it reaches a critical threshold, thus preventing potential failures or accidents.
Learn more about how pressure regulators compare with similar devices in our article that compares pressure controlling devices.
FAQs
What is a pressure regulator?
A pressure regulator is a valve that automatically cuts off the flow of a liquid or gas at a certain pressure to maintain a desired pressure level.
What does a pressure regulator do?
A pressure regulator accepts an input pressure and reduces it to a constant output pressure. It is adjustable for a wide range of pressures that are higher than or equal to the output pressure.
How does a pressure regulator work?
A pressure regulator maintains a constant output pressure by adjusting its valve opening in response to changes in input pressure and downstream demand.
Can pressure regulators fail?
Yes. A pressure regulator can fail over time due to moving parts failing or wearing down from long-term exposure to abrasive media. However, pressure regulators are designed to last a long time.
When is a pressure regulator necessary?
A pressure regulator is necessary whenever the pressure of the source is higher than maximum required pressure. For example, pressure coming from an air compressor going to a paint gun.
Where is a pressure regulator located?
Regulators are upstream of sensitive equipment. A water pressure regulator is where a water main comes into a home’s plumbing. An air regulator is located before the compressor’s discharge.