Ball Valve Connection Types
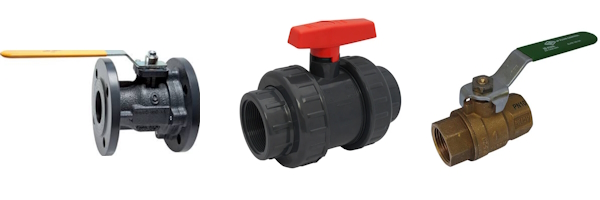
Figure 1: Main types of ball valve end connections: flanged (left), true union (middle), and threaded (right).
Selecting the correct type of ball valve connection is crucial in fluid control systems, as it significantly impacts installation and valve performance. Understanding the various connection options, such as threaded, flanged, and welded, is essential for selecting the appropriate valve for specific applications. This article examines the end connection types for different ball valve types, highlighting their advantages, limitations, and typical use cases.
Table of contents
- Threaded connection
- Flanged connections
- Cutting ring connection
- True union connection
- Glued sleeve connection
- Hose pillar connection
- Selection criteria
- FAQs
Check out Tameson's selection of ball valves with different connection types!
Threaded connection
Threaded connection ends provide a convenient method for attaching small ball valves to pipes. Threaded ball valves are commonly used in applications involving ball valves with diameters less than 1010 mm (4 inches), as larger diameters can be challenging to seal and may be prone to leakage through the threads. These connections are cost-effective and straightforward to install, maintain, and replace. Typically, the valve features female-threaded ends that connect to a male-threaded component. However, some valves may have male threaded ends or a combination of one male and one female threaded end.
The threads are manufactured in strict accordance with thread standards, which define the specific parameters of the thread to ensure compatibility and reliability. The common thread standards for ball valves are BSP, NPT, and Metric (M). Threaded connections are available in two types: straight and tapered.
- Straight connections (for example, BSPP or British Standard Pipe Parallel) typically require an o-ring, which compresses to create a secure seal between the valve and the pipe.
- Tapered threads (for example, BSPT or British Standard Pipe Tapered) achieve a tight seal without needing an o-ring.
Both types of threads can benefit from applying pipe tape or sealant between the male and female threads. This acts as a lubricant, enhances sealing, and prevents metal-to-metal contact, which can lead to wear.
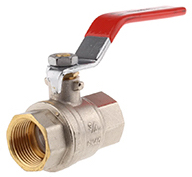
Figure 2: Ball valve with a threaded connection.
Flanged connections
Flanges are solid metal plates with holes for bolts and nuts, which secure the valve to the pipe. Flanged ball valves are used in applications requiring robust connections and easy maintenance. They are easy to install and can be removed for cleaning and maintenance without disturbing other parts of the piping system, making them popular in industrial settings. They are often used for valves larger than 101 mm (4 inches). These connections follow strict standards that specify details like the design of the plates, hole size, thread type, and hole placement.
The connection sizes, such as D15 and D20, indicate the nominal diameter of the flange in millimeters, with D15 corresponding to 15 mm (0.59 inches) and D20 to 20 mm (0.79 inches).
The ISO 5211 flange type, such as F04 and F05, refers to standardized mounting flanges for actuators, with specific bolt patterns and sizes ensuring compatibility with actuators. The numbers correspond to specific dimensions, such as the distance between bolt holes and the diameter of the bolt circle.
The primary standards for flanged connections are:
- DIN 1092-1, which is the European standard under ISO 7005
- ANSI/ASME B16.5, set by the American National Standards Institute and the American Society of Mechanical Engineers
- SAE J518, from the Society of Automotive Engineers
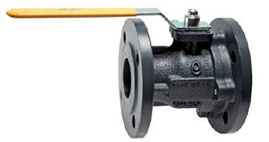
Figure 3: A manual ball valve with a flanged connection
Cutting ring connection
Cutting ring connections are commonly used in high-pressure hydraulic systems. A metal ring cuts into the tube when the nut is tightened, creating a robust and leak-proof seal. This type of connection is suitable for applications requiring high reliability and resistance to vibration, such as industrial machinery and automotive systems.
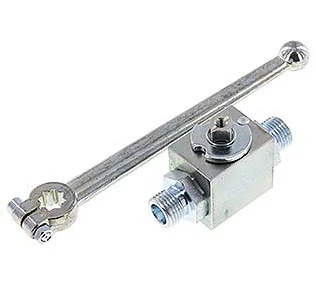
Figure 4: 2-way hydraulic ball valve with cutting ring
True union connection
A true union ball valve design allows the centerpiece of the valve (ball valve assembly) to be removed from the entire unit while the valve is installed. True union ball valves can be easily disassembled and rebuilt. The seals and other internal components can be easily replaced, extending the valve's lifespan. They are typically used for PVC ball valves. True union ball valves can be configured with different connection types to suit various plumbing needs:
- True union ball valve with solvent socket: These valves have solvent socket connections, allowing them to be glued directly into PVC piping systems. This type is ideal for systems that require a permanent, leak-proof connection.
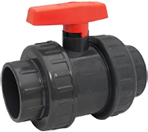
Figure 5: True union ball valve with solvent socket
- ISO Top ball valve with solvent socket: This valve is similar to the true union ball valve with solvent sockets. However, it has an ISO top, allowing for easy actuator mounting for automated control.
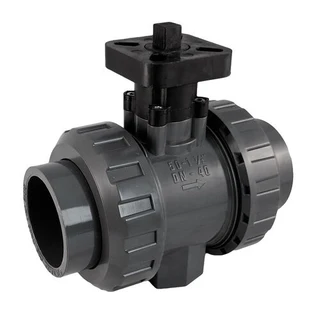
Figure 6: PVC ISO-top ball valve with solvent socket
- True union ball valve with threads: These valves have threaded connections, making them suitable for systems where disassembly and reassembly are needed without cutting the pipe. They are ideal for applications requiring frequent maintenance or changes.
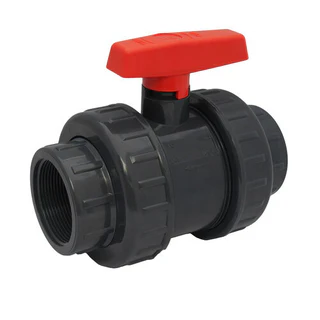
Figure 7: PVC true union ball valve with threads
- Single union ball valve with threads or solvent sockets: These have a union connection on one side and a threaded or solvent socket connection on the other. They offer some of the flexibility of true union valves but are more compact and typically used in limited-space applications.
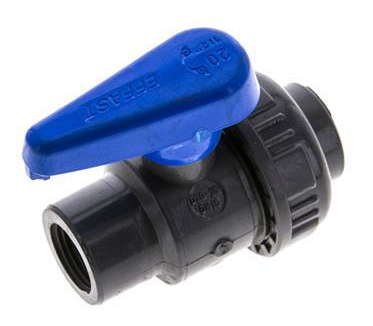
Figure 8: PVC single union ball valve with threads
Glued sleeve connection
Glued sleeve connections utilize adhesive for a secure, permanent bond. This type of connection is commonly used in plastic piping systems. The adhesive creates a chemical bond between the valve and the pipe, ensuring a leak-proof seal. Glued sleeve connections are ideal for applications where a permanent installation is desired, such as in residential plumbing and irrigation systems.
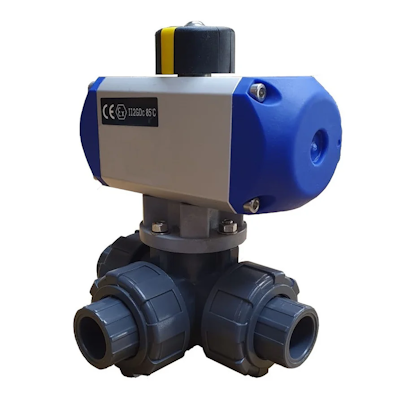
Figure 9: Glued sleeve ball valve with a pneumatic actuator
Hose pillar connection
Hose pillar connections are designed for flexible hoses, typically in low-pressure applications. They feature a barbed end that fits inside the hose, creating a secure fit that prevents leaks. The hose is usually secured with a clamp to ensure a tight seal.
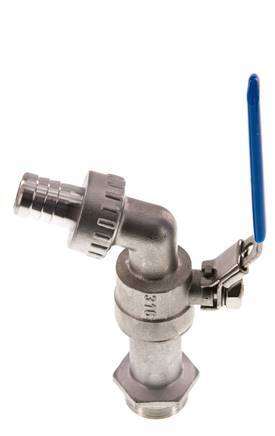
Figure 11: Stainless steel 2-way faucet ball valve with a threaded inlet and hose barb outlet port
Selection criteria
When selecting the appropriate connection type for a ball valve, several key factors should be considered to ensure compatibility, performance, and cost-effectiveness. Here is a guide to selecting the right ball valve connection type for an application:
- Compatibility with existing valves: If there are existing valves in the same network, choosing a connection type that matches them is advisable. This ensures consistency and simplifies installation and maintenance.
- Process pressure rating: The connection type must withstand the maximum pressure expected in the system. Welded connections are suitable for high-pressure applications, flanged and cutting ring connections are suitable for high-pressure, and threaded connections are appropriate for low-pressure applications.
- Cost considerations: Welded connections are generally the least expensive but offer no flexibility and require professional installation. The cost of threaded and flanged connections varies with valve size, with larger sizes typically being more expensive.
- Leakage prevention: Welded connections are ideal for applications with critical zero leakage. Flanged connections effectively minimize leaks in larger pipe sizes, while threaded connections are suitable for smaller pipe sizes.
- Ease of installation, replacement, and maintenance: Flanged connections are the easiest to maintain, allowing for straightforward installation and removal. Threaded connections are more challenging, and welded connections do not allow maintenance once installed.
- Pipe size: Flanged or welded connections are typically used for large pipe sizes above 4 inches. Smaller pipe sizes can use threaded connections, and welded connections are recommended if the process fluid is hazardous.
- Connection standards: Ensure that the connection standards for threaded and flanged connections match the pipe specifications. For welded connections, verify that the materials of the valve and pipe are compatible.
FAQs
How to install a threaded ball valve?
Clean the threads, apply thread sealant or Teflon tape, and screw the valve onto the pipe, tightening it with a wrench.
What is a flanged ball valve?
A flanged ball valve has flanges for bolting to a piping system, providing a secure connection for high-pressure applications.
What is the difference between flanged and threaded ball valves?
Flanged ball valves use bolted flanges for secure, high-pressure connections, while threaded ball valves screw onto pipes for easier installation, typically in lower-pressure settings.