V-belt Tensioning
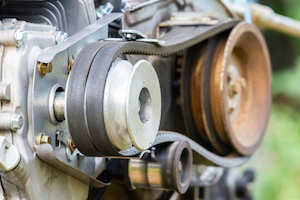
Figure 1: V-belt and pulley system
Proper v-belt tension is the key to long, efficient, and trouble-free belt operation. Tensioning the belts to the manufacturer’s recommendations is essential once the pulleys are aligned to the belt. Incorrect v-belt tension adversely affects belt drive reliability and efficiency. This article discusses the importance of v-belt tensioning and how to determine the tension of a v-belt. For more information, read our v-belt overview article.
Table of contents
View our online selection of V-belts
Why is v-belt tensioning important?
A v-belt is a transmission belt with a trapezoidal cross-section. It is made of rubber polymer. V-belts allows for higher torque transmission in applications that have multiple groove pulleys. Proper v-belt tension is the lowest force at which the belt does not slip under the maximum load. V-belts require very little maintenance; however, having improper belt tension can cause issues in belt drive systems. There are two cases of improper belt tensioning:
- V-belt too tight: When a v-belt is too tight in a system, it may add stress to the bearings. The added stress results in excessive current consumption from a motor and, eventually, motor failure.
- V-belt too loose: A loose v-belt in a pulley system may slip during motion, causing extra friction. The additional friction results in heat buildup on the belt and the pulley, causing premature damage to belts.
Symptoms of improper tensioning include:
- Squealing during startup
- Pulleys wearing out prematurely
- Belt cracking
- Hardened appearance
- Over amperage of the motor
Always test the tension of a v-belt while installing a new one or if any of the symptoms mentioned above occurs.
Minimum pulley diameters
The diameter of the pulleys determines the operation of a v-belt drive. The ARPM (Association for Rubber Product Manufacturers) lists the minimum recommended pulley diameter for each v-belt profile. Using pulleys smaller than the recommended diameters results in a substantial increase in belt tension and decreases the overall belt life.
How to test v-belt tension
Different materials and tension cables are involved in v-belt manufacturing; hence, not all v-belts feel the same when adequately tensioned. Physically touching the belt to determine its tension may not yield correct results. While installing a new v-belt, use a tension gauge to establish the correct tension. Then, recheck belt tension periodically or when any of the symptoms of improper tensioning become evident; this helps maintain v-belt performance.
Force-deflection method
V-belt tension is a function of two parameters: belt deflection and its force. Use the following method to determine the v-belt tension.
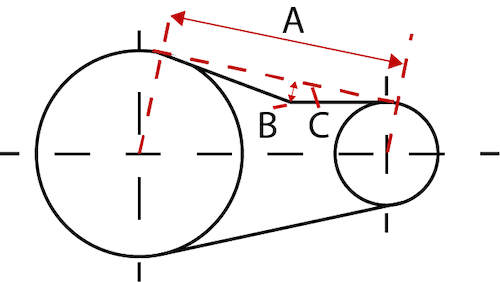
Figure 2: Force-deflection method for v-belt tensioning; span length (A), deflection length (B), and force or tension caused by the deflection (C)
- Measure the v-belt span length (Figure 2 labeled A) using tape.
- Calculate the deflection distance (Figure 2 labeled B). The deflection distance is approximately 1/64 inch (0.4 mm) of the span length.
- Set the upper small o-ring (Figure 3 labeled A) on the plunger (Figure 3 labeled D) at zero against the body of the tension gauge.
- Slide the lower o-ring (Figure 3 labeled C) against the deflection scale (Figure 3 labeled B) to set it at the deflection distance calculated in Step 2.
- Keep the tension gauge perpendicular to the v-belt span. Press down on the belt so that it deflects until the bottom of the large o-ring aligns with the top of the adjacent belt. This sets the gauge at the calculated deflection distance.
- Release the pressure. The upper small o-ring moves on the scale to point at the force (tension) created by the deflection. Hence, the lower o-ring sets the deflection distance, while the upper o-ring calculates the necessary tension (in pounds) caused by the deflection.
- Refer to the manufacturer’s manual for the recommended v-belt tension metric chart for the belt type used. The deflection force value should lie within the minimum and maximum values given in the manufacturer’s sheet.
- A deflection force value less than the minimum recommended value in the range suggests an under-tensioned drive. A deflection force higher than the maximum recommended value indicates an over-tensioned drive. Adjust the v-belt tension until the force required to achieve the desired deflection is within the recommended level range.
Note
- Turn the equipment off before tensioning or doing maintenance on the v-belt; this ensures proper safety for the user.
- New belts require higher tension levels (approximately 1.3 times the nominal value) than used belts as they have not been run in.
- For banded belts, multiply the belt deflection force by the number of ribs in the grip band. Place a steel bar across the banded v-belt and apply the belt deflection force to the bar such that an equal amount of deflection appears across all the individual ribs.
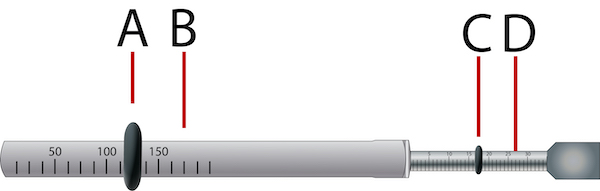
Figure 3: Tension gauge used to determine v-belt tension; A: Large o-ring, B: Body with deflection force scale, C: Small o-ring, and D: Plunger with deflection distance scale.
Example
Consider a v-belt with a span of 48 inches.
- The deflection for the belt is 48/64 inches (19 mm).
- Use a tension gauge to calculate the force required to deflect the belt to the value in step 1.
- Refer to the manufacturer’s sheet and check whether the force value lies within the nominal range of the v-belt.
- Re-tension the belt if necessary
- If the tension value is less than the minimum recommended range, the v-belt is under tensioned.
- If the tension value exceeds the maximum recommended range, the v-belt is over-tensioned.
Red our articles on how to measure a v-belt and v-belt replacement for more information.
FAQs
What happens when a v-belt is too tight?
A tight v-belt can add stress to the bearings resulting in over-amperage of the motor and potential motor failure.
What causes v-belts to burn?
Worn pulleys and incorrect tensioning in the v-belts cause squeals (spin burns).
What causes a v-belt to slip?
Improper v-belt tension generates heat causing the belt to slip.