V-belt Sizes, Types, and Characteristics Overview
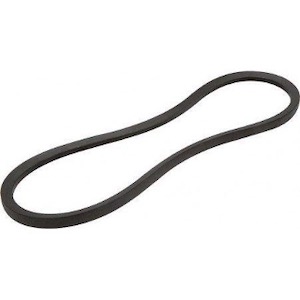
Figure 1: A v-belt
V-belts transmit mechanical power efficiently between different parts of a machine. They are commonly on automobile engines to drive accessories, such as the air conditioning compressor, power steering pump, alternator, and fan. A v-belt has a trapezoidal cross-section and comes in various types depending on their dimensions. This article discusses the constructional features, types, and main applications of v-belts.
Table of contents
- What is a v-belt
- Constructional features of a v-belt
- V-belt types based on dimensions
- Wedge v-belts
- V-belt types based on construction
- V-belt sizing
- Advantages of a v-belt drive
- Disadvantages of a v-belt pulley system
- V-belt applications
- FAQs
View our online selection of V-belts
What is a v-belt
A v-belt is flexible and transmits power from one shaft to another. As seen in Figure 2, a v-belt has a trapezoidal cross-section. The wedge-shaped belt fits perfectly into the wedged groove of a pulley. Due to this good fit, v-belts transmit more force than flat belts. Also, pulley systems that use v-belts typically have pulleys near one another. Therefore, the system is compact.
Constructional features of a v-belt
A v-belt consists of the following parts:
- Steel wires: Steel wires (Figure 2 labeled A) have no joints between them and are of the endless type. These wires provide the necessary strength and reinforcement to the v-belt for torque transmission.
- Base rubber compound: A rubber compound (Figure 2 labeled B) acts as the core surrounding the steel wire providing shape to the v-belt. The rubber compound (an elastomer) also acts as a medium of compression to absorb shocks during the transmission of power.
- Protective cover: The protective cover (Figure 2 labeled C) is a layer of plastic that provides sufficient tolerance for the rubber against the high temperature that is generated during the v-belt movement.
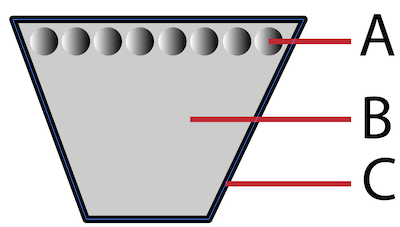
Figure 2: Structure of a v-belt: steel wires (A), base rubber compound (B), and protective cover (C).
V-belt types based on dimensions
There are several industry standards for the types and sizes of v-belts. Each type features the basic trapezoidal shape but has different dimensions.
Standard v-belt
Standard v-belts are common in power transmission applications. These v-belts come in various types, as shown in Table 1. Each type varies from one another with respect to its dimensions. Standard v-belts are designated as A, B, C, D, E, and Z. Read our article on how to find a v-belt replacement for more details on how to measure and name a v-belt. All sizes have a top width to height ratio of approximately 1.6:1.
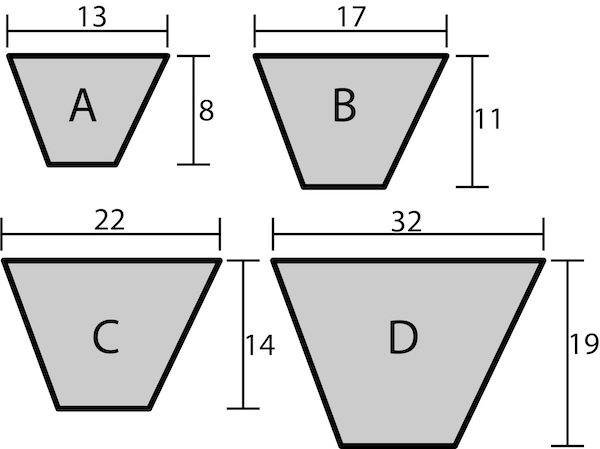
Figure 3: Standard v-belts (dimensions are in mm)
Table 1: Standard v-belt dimensions
Designation (ISO, BS, IS, JIS) | Designation (DIN) | Top width (mm) | Height (mm) | Recommended minimum pulley pitch diameter (mm) |
Z | 10 | 10 | 6 | 50 |
A | 13 | 13 | 8 | 71 |
B | 17 | 17 | 11 | 125 |
C | 22 | 22 | 14 | 200 |
D | 32 | 32 | 9 | 355 |
E | 38 | 38 | 23 | 500 |
Wedge v-belts
Wedge-type v-belts are for limited space applications. Fewer belts are needed to transmit the load due to a higher power rating. These belts operate at 1.5 - 2 times the load of standard v-belts with the same top width. Wedge v-belts have an included angle of 40 degrees (see Figure 2) and a top to width ratio of approximately 1.2:1. They have better steel cord placement and construction, thereby providing the highest strength while in motion. The common designations for Wedge v-belts are SPZ, SPA, SPC, and SPB, as seen in Table 2.
Table 2: Wedge v-belt dimensions
Designation | Top width (mm) | Height (mm) | Recommended minimum pulley pitch diameter (mm) |
SPZ | 9.7 | 8 | 63 |
SPA | 12.7 | 10 | 90 |
SPB | 17 | 13 | 140 |
SPC | 22 | 18 | 224 |
Narrow v-belts
Narrow v-belts are ideal for transmitting large loads. The common designations for these belts are 3V, 5V, and 8V. These belts are standardized and commonly used in North America. A narrow v-belt has an included angle of 40 degrees and partially matches up to the profile of a wedged v-belt:
- 5V: SPB
- 3V: SPZ
Therefore, it is a safe practice to use 5V and 3V for SPB and SPZ pulleys, respectively. However, it is not recommended to use SPB and SPZ pulleys on American standard pulleys.
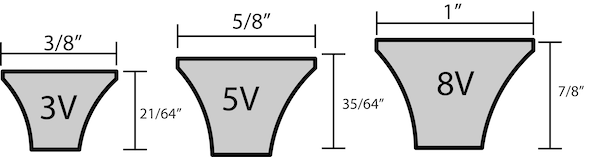
Figure 3: Narrow v-belt sections
Table 3: Narrow v-belt dimensions
Designation | Top width (mm) | Height (mm) | Recommended minimum pulley pitch diameter (mm) |
3V | 9.7 | 8 | 63 |
5V | 15.8 | 14 | 140 |
8V | 25.4 | 23 | 335 |
Double or hexagonal v-belt
Hexagonal v-belts, or double v-belts, are versatile. The steel wires in these belts run through the center of the cross-section, as seen in Figure 4. Therefore, these belts can bend in either direction and are suitable for systems that have pulleys moving in opposite directions. The typical designations for hexagonal v-belts are AA, BB, and CC.

Figure 4: Hexagonal v-belt
Table 4: hexagonal v-belt dimensions
Designation | Top width (mm) | Height (mm) | Recommended minimum pulley pitch diameter (mm) |
AA | 13 | 10 | 80 |
BB | 17 | 14 | 125 |
CC | 22 | 17 | 224 |
Banded v-belt
As seen in Figure 5, a cover on the top side of a banded v-belt joins together multiple v-belts. Each of the individual v-belts can have standard, wedge, or narrow dimensions. Banded v-belts are ideal for high power applications, such as clutching and vertical shaft drives. The designation of a banded v-belt begins with an H, followed by the designation for the individual v-belts. Examples are HA, HB, HSPA, HSPB, H3V, and H5V.
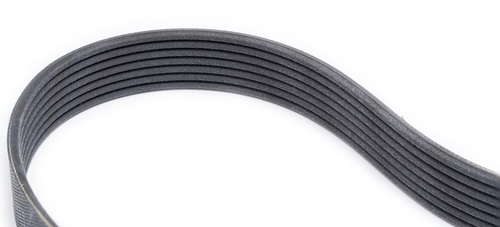
Figure 5: Banded v-belt
Fractional horsepower v-belts
Fractional horsepower v-belts are suitable for light-duty applications. For example, equipment in a machine shop or common household appliances for which the power requirement is one horsepower or less. The common designations for fractional horsepower v-belts are 2L, 3L, 4L, and 5L. The number before the L denotes the top width of the belt multiplied by 1/8 of an inch (3.2 mm).
Table 5: Fractional horsepower v-belt designations
Designation | Top width (mm) | Height (mm) |
2L | 6.4 | 3.2 |
3L | 9.5 | 5.6 |
4L | 12.7 | 7.9 |
5L | 16.7 | 9.5 |
Cogged v-belts
Cogged v-belts have notches at the bottom, allowing them to have smaller bend radii. Cogged belts can have cross-section dimensions of standard, narrow, wedge, banded, and fractional horsepower v-belts. Except for wedge belts, the common designation for cogged belts has an X after the v-belt section number. Example designations are AX, 5VX, 3VX, HAX, H3VX, etc. The designations for cogged wedge belts are XPA and XPB.
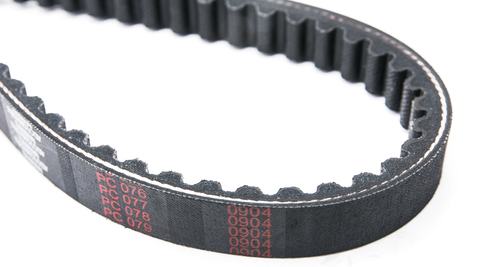
Figure 6: Cogged v-belt
Double cogged v-belts
A double cogged v-belt combines a cogged and hexagonal v-belt. These belts are suitable for applications that require high belt flexibility and a small bend radius. The cogged construction on the top of the belt allows it to bend in a zigzag-like path. This feature is beneficial for driving multiple pulleys. The dimensions of double cogged v-belts depend on manufacturer standards.
Cogged v-belt vs standard v-belt
Cogged belts have notches at the bottom that are perpendicular to the belt’s length (see Figure 5). This feature allows the belt to bend at smaller radiuses. Cogged belts are suitable in applications with the same pulley system as equally rated v-belts. But, cogged belts are more durable, produce less heat, and have higher efficiency than standard v-belts.
Poly v-belts
A poly v-belt is similar to a banded v-belt. However, unlike banded v-belts, poly v-belts do not have the section dimensions of standard, wedge, and narrow v-belts. Instead, poly v-belts have a more compact construction. Also, they are thinner, giving them improved flexibility and making them suitable for driving multiple pulley systems. Poly v-belts can take a zig-zag path with the help of idlers. Common designations for poly v-belts are PJ, PH, PK, PL, and PM.
V-belt types based on construction
Based on construction, v-belts divide into:
- Wrapped v-belts: Plastic or fabric completely covers the surface of a wrapped v-belt.
- Raw edge v-belts: Raw edge v-belts do not have an external cover.
Wrapped v-belts are the most common. They have high resistance against external factors and operate quietly. However, these belts have a very low coefficient of friction, meaning they are more likely to slip, which results in power loss. Wrapped v-belts are suitable for applications in which some amount of slippage without damaging the belt is permissible.
The bare material of raw edge v-belts physically connects to a pulley’s surface. Therefore, the belt’s coefficient friction is higher, which reduces the amount of slippage. This v-belt’s rubber core has a higher tolerance to abrasions compared to that of wrapped v-belts. Raw edge v-belts are again classified into:
- Raw edge plain (REP): Several layers of plastic or fabric cover the top side of a raw edge plain v-belt. The bottom side may or may not have a cover, depending on the design.
- Raw edge laminated (REL): Raw edge laminated types of v-belts are similar to REP but have additional layers of laminate fabric at their core. The addition of these laminated fabrics helps to reduce noise.
- Raw edge cogged (REC): Raw edge cogged v-belts come with notches (cogs) on the bottom side of the belt; hence, these belts are also called raw edge notched v-belts. These cogs improve the belt's flexibility, so they are suitable for pulleys with small diameters. Also, there is better heat dissipation because of the large surface area at the bottom. Therefore, these v-belts are suitable for applications involving high temperatures.
V-belt sizing
Length, depth, and top width specify the dimensions of a v-belt. V-belt designations use these parameters. Read our v-belt size calculator article for more details on a v-belt pulley system and how to calculate the belt length.
Advantages of a v-belt drive
- The slip between the v-belt and pulley is negligible.
- A pulley system operated by a v-belt has a quiet operation.
- Compact structure due to the small distance between the centers of pulleys.
- A v-belt pulley system dampens vibration.
- V-grooves provide excellent grip; hence, the transmission of high power is possible.
Disadvantages of a v-belt pulley system
- Construction of v-belt pulleys is complicated compared to flat-belt pulley systems.
- Centrifugal tension prevents the use of v-belts at speeds below 5 m/s and above 50 m/s.
- V-belt drives have a relatively high weight per unit of length; hence, they cannot be used over long distances.
V-belt applications
Some of the most popular applications of v-belts are:
- Drills
- Power tools
- Agricultural machines
- Light-duty milling machines
FAQs
What is a V-belt used for?
V-belts are used to transmit mechanical power efficiently between different parts of a machine. They are commonly used on automobile engines to drive accessories, such as the air conditioning compressor, power steering pump, alternator, and fan.
What does V stand for in V-belt?
A v-belt has a trapezoidal cross-section that resembles a ‘V.’