T-strainer - Design, Features, Applications
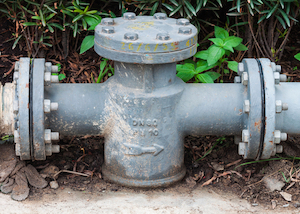
Figure 1: T-strainer
A T-strainer is a common filter in industrial and commercial applications to remove debris and contaminants from liquids and gasses. It consists of a T-shaped body connected to the pipeline. T-strainers are known for their simple design, ease of operation, and versatility in various settings. This article discusses the design, features, applications, and selection criteria of t-type strainers.
Table of contents
- Design and operation
- Benefits
- Selection criteria
- Installation
- Maintenance
- T-strainers vs Y-strainers
- T-type strainer applications
- FAQs
Check out our selection of T-strainers and Y-strainers!
Design and operation
A T-strainer consists of a T-shaped body, a removable strainer basket placed inside the body, and a cover used to access the strainer basket for cleaning or replacement. The T-shape of the device allows it to be easily installed in pipelines and provides a simple and effective way to remove debris and other contaminants from liquids and gasses.
Fluid flowing through the pipeline goes through the strainer. The basket in the strainer is made up of a mesh or other filter material that is designed to trap foreign particles present in the liquid or gas. Trapped in the basket, the particles cannot cause damage to downstream equipment such as pumps, valves, and other components.
Benefits
T-strainers are widely used to protect equipment, improve system efficiency, and reduce maintenance costs. The list below highlights further benefits of using T-strainers in fluid systems.
- Easy maintenance: T-type strainers have a quick-opening cover for convenient access.
- Safety: They are safe in hazardous processes because the cover, when in a horizontal pipeline, can open safely without draining the fluid.
- Low pressure drop: They have a large open area for media to flow through, so the flow is minimally restricted, and the pressure drop stays low.
Selection criteria
There are a few factors to consider when selecting a T-strainer:
- Size of the particles to be trapped: The size of the solid particles that need to be trapped determines the size and type of straining element to use. Smaller particles require a finer straining element, such as a wire mesh, porous media, or a film cloth, as they have smaller openings. Larger particles may need a coarser straining element, such as a large mesh or a perforated plate with larger openings. It is important to ensure the proper mesh and filter size as it also affects media flow.
- Flow rate and fluid pressure: The flow rate and pressure of the fluid will affect the size and design of the strainer housing and straining element. A high flow rate or pressure may require a larger strainer or a straining element with a higher resistance to pressure to prevent leakage, clogging, or failure.
- Corrosion and viscosity: Corrosive liquids require strainer elements that will not react with them. Viscosity determines if the fluid can pass through the strainer openings.
- Size of the pipeline and operation conditions: The size of the pipeline will determine the size of the strainer that is required. Always select a strainer compatible with the pipeline's size to ensure proper fit and function and prevent leakage. Operating conditions include throttling, condensation, pressure drop, flow reversal, and operation frequency.
- Type of the material to be filtered: The type of material being filtered, such as water, oil, or gas, will affect the selection of the strainer and straining element. The straining element should also be compatible with the filtered material to ensure it is effective at trapping solid particles.
Installation
Most strainers are inline T-strainers, meaning they are installed inside the pipeline. They are typically installed at the beginning or end of the pipeline or the storage tank inlet as a final filtration method. T-type strainers should be installed where they are easily accessible for maintenance, cleaning, and effectively filtering out solid particles from the fluid flow. Here are the common installation steps.
- First, determine the correct T-strainer size for the application. This depends on the size of the pipe and the flow rate of the fluid passing through it.
- Next, locate the installation point for the T-strainer. This should be a point in the piping system where the strainer can easily be removed for cleaning or maintenance.
- Cut the pipe at the installation point using a pipe cutter or saw. Be sure to make a clean, square cut to ensure proper alignment of the T-strainer.
- Apply pipe sealant to the threads of the T-strainer, then thread the T-strainer into the pipe. Tighten the T-strainer with a pipe wrench to ensure a secure fit.
- Install the screen or basket into the T-strainer body.
- Install any additional components, such as valves or gauges, if required by the application
- Check for any leaks and make sure the strainer is properly aligned before resuming operation.
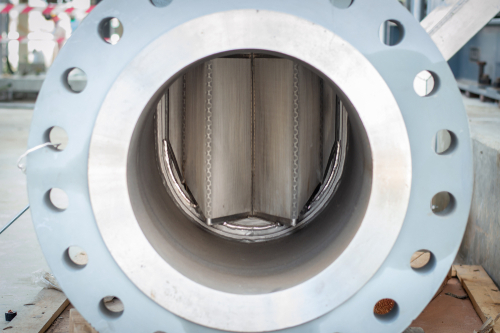
Figure 2: Internal view of a T-strainer filter
Maintenance
It is essential to periodically check and clean or replace the strainer basket to ensure that the T-type strainer operates at peak efficiency. This can be done by removing the cover and inspecting the strainer basket for any buildup of debris or contaminants. If necessary, the strainer basket can be cleaned or replaced to maintain the proper operation of the T-type strainer.
- Shut off fluid flow through the strainer and relieve any pressure in the pipeline.
- Open any valves or covers on the strainer housing to access the straining element.
- Remove the straining element from the housing.
- Clean the straining element, if necessary, or replace it with a new one.
- Reinstall the straining element in the housing, ensuring it is seated and secured correctly.
- Close any valves or covers on the strainer housing.
- Test the strainer to ensure it is functioning correctly.
Note: Follow the manufacturer's instructions for installing and maintaining the T-type strainer to ensure proper function and avoid potential safety hazards.
T-strainers vs Y-strainers
There are several key differences between T-strainers and Y-strainers, making them better suited for different types of applications.
Table 1: T-strainer vs y-strainer
T-strainer | Y-strainer | |
Design | T-shaped body | Y-shaped body |
Strainer basket size | Typically have a smaller strainer basket. | Typically have a larger strainer basket, affecting installation space. |
Cost | More expensive | Less expensive |
Cleaning | A T-strainer has a basket-type strainer typically installed in a vertical position, with the basket placed at a right angle to the pipeline. This design makes it easy to remove the cover for cleaning purposes. | A Y-strainer is typically installed with the strainer leg positioned below the pipeline and pointing downwards. This design allows easy removal of the cover and immediate draining of any particles collected in the strainer basket. |
Installation | T-strainers are primarily designed for horizontal installation because of the orientation of the filter screen. | Y-strainers are more versatile as they can be installed in horizontal and vertical positions, making them suitable for various applications. |
Applications | T-type strainers are often preferred for transferring viscous fluids at high velocities. The basket strainer feature of T-strainers allows for a higher flow capacity, which is essential for quickly draining dangerous fluids. Additionally, the larger filtration system of T-strainers allows for the retention of more particles. | Y-strainers are better suited for non-dangerous fluids in industrial pipelines. These strainers are designed to protect downstream equipment from particles not commonly present in the application, making them ideal for pipelines dealing with a low concentration of particles, as they have a smaller screen size. |
Read our article on how to select a strainer for more details on the parametrs to consider while selecting a filter or strainer.
T-type strainer applications
- Industrial processes: T-Strainers are used in industrial processes to protect pumps, meters, valves, and other equipment from damage caused by debris and other particles. Industrial strainers are installed just before these components to strain the solid particles.
- Chemical processing: T-strainers are used in chemical processing plants to protect pumps and other equipment from damage caused by particulates in the fluid. They also remove any particulates that may be formed during the chemical process. A poly T-line strainer, made of polypropylene, a type of plastic, is commonly used in chemical processes, including food processing, chemical processing, and water treatment due to its corrosion-resistant material.
- Water and wastewater systems: T-strainers are used in water and wastewater systems to filter out debris, such as leaves, twigs, and other large particles before the liquid enters the processing plant.
- Oil and gas systems: T-strainers are installed in oil and gas systems to protect equipment from damage caused by contaminants during the process and ensure that the final product is debris-free.
- Fire protection systems: T-strainers are used in fire protection systems to protect pipelines, pumps, and nozzles from damage caused by debris and other particles and to prevent blockage when they are required to work.
FAQs
What is the difference between T and Y strainers?
The main difference between them is in their design. T-strainers are cylindrical, while Y-strainers have a more "Y" shape. Y-strainers are commonly used for applications with a higher flow rate and more debris.
How often should a T-strainer be cleaned?
The application, frequency of use, and amount of solid particles filtered determine the cleaning frequency. It is generally recommended to check and clean the T-strainer at least monthly and more frequently if debris accumulation is excessive.