When And Why To Use a Sanitary Grade Valve
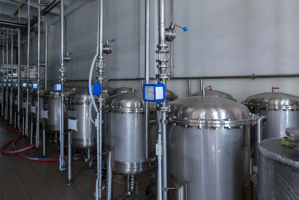
Figure 1: Stainless steel pipes and valves in the food industry
Sanitary grade valves prevent contamination and ensure high hygiene standards in industries prioritizing cleanliness, such as the food, beverage, pharmaceutical, and cosmetic sectors. This article explores the key design features and applications of sanitary grade valves.
Table of contents
View our online selection of valves!
What is a sanitary grade valve?
Sanitary grade valves are built for applications demanding exceptional hygiene and cleanliness standards. Their primary function is safeguarding against cross-contamination, product spoilage, and the associated health risks from unhygienic environments. These valves can be actuated manually, pneumatically, electrically, or hydraulically. They can work with gasses, liquids, and liquids with suspended solids.
Features
- Superior hygiene standards: Sanitary grade valves are built to meet strict hygiene standards. Their smooth surfaces and sanitary seals minimize the risk of product contamination, ensuring the integrity and safety of the fluid being processed.
- Traceability: In some industries, such as pharmaceuticals, it's important to have complete traceability (the ability to track a product's history, origin, materials, and movement throughout its lifecycle) of all components, including valves. Certain manufacturers provide this information for their sanitary grade valves, which users can request while purchasing.
- SIP and CIP compatibility: Sanitary grade valves are designed to be compatible with SIP (Steam-in-Place) and CIP (Clean-in-Place) processes. SIP involves exposing the valve to high-temperature steam to sterilize it. CIP utilizes cleaning solutions and circulation to remove contaminants. The design and materials of sanitary grade valves allow them to withstand these rigorous cleaning and sterilization procedures without compromising their integrity.
-
Easy cleaning and maintenance: Sanitary grade valves are designed for easy cleaning and maintenance.
- Sanitary grade valves can be easily dismantled for cleaning. Some can even be cleaned without disassembly using the CIP technique.
- The smooth surfaces allow for a thorough cleaning, minimizing the risk of bacterial growth.
- Their construction enables quick and efficient maintenance, reducing downtime and ensuring optimal performance.
- Compliance with regulatory standards: Sanitary grade valves should comply with standards such as 3A, FDA , and EHEDG.
- Versatile options: There are various types of sanitary grade valves, including butterfly valve, ball valve, diaphragm valve, check valves or pressure relief valves, each with its own specific uses and advantages.
Design features
Sanitary grade valves are designed to minimize dead spaces (areas where fluids stagnate) leading to bacterial growth or product contamination. These valves often feature streamlined bodies, flush-mounted connections, and the absence of crevices or internal pockets that can trap fluid and contaminants.
-
Material selection: Material selection is important in sanitary grade valves to ensure resistance to corrosion, ease of cleaning using the SIP and CIP techniques, compatibility with substances they contact, and high-temperature resistance. The materials should withstand high temperatures in sterilization methods like autoclaving or steam cleaning.
- Choosing the right materials, such as stainless steel, alloys, or FDA-approved polymers, helps maintain the valves' hygienic properties and prevents contamination risks.
- Surface finish: The internal surfaces of sanitary grade valves are often polished to a high degree of smoothness to prevent the adhesion of particles and bacteria. They have specific surface-finish requirements to ensure optimal hygiene. These standards, such as the Ra (Roughness Average) value, specify the level of smoothness and cleanliness required for the valve's surface. A lower Ra value indicates a smoother surface, easier to clean, and less prone to bacterial adhesion.
- Sealing: Sanitary grade valves utilize high-quality seals to prevent any potential contamination. These seals are usually made from silicone, EPDM, or Viton, which are resistant to high temperatures and corrosion.
- Electropolishing: Electropolishing involves immersing the valve in an electrolyte bath and applying an electric current to remove surface imperfections and enhance corrosion resistance. Electropolished surfaces are smoother, more contamination-resistant, and easier to clean.
- Tri-clamp connections: Sanitary grade valves often use tri-clamp connections, also known as tri-clover or tri-clover fittings. These connections provide a secure and hygienic seal between two components, such as a valve and a pipe or a valve and a tank. Tri-clamp fittings are easy to assemble, disassemble, and clean, making them popular in industries requiring frequent sterilization.
- Welding techniques: Sanitary grade valves often employ specialized welding techniques, such as orbital welding or sanitary TIG (Tungsten Inert Gas) welding. These techniques provide precise and consistent welds without introducing contaminants, ensuring the integrity and hygienic properties of the valve.
Disadvantage
The cost of sanitary grade valves may be higher than standard valves due to their specialized design, materials, and compliance with industry standards. However, the long-term benefits often outweigh the initial investment.
Applications
Sanitary grade valves find applications in various industries, including:
- Water treatment and purification: Sanitary valves are used in water treatment plants to control water flow, ensuring clean and safe drinking water for communities.
- Food and beverage: In food and beverage processing, sanitary valves are essential to maintain hygiene and prevent contamination while producing beverages, dairy products, sauces, and other consumables.
- Pharmaceutical and biotech: Sanitary valves play a crucial role in pharmaceutical and biotech processes, where maintaining the purity and sterility of fluids is vital for drug production and research.
- Cosmetics and personal care products: The cosmetics and personal care industry relies on sanitary valves to precisely control ingredients during the production of lotions, creams, and other personal care products.
- Chemical and petrochemical: Sanitary valves are used in chemical and petrochemical processes, where corrosive or hazardous fluids must be controlled with maximum safety and cleanliness.
FAQs
What is a sanitary valve?
A sanitary grade valve is specialized for hygienic industries (e.g., food, pharmaceuticals) to prevent contamination and ensure easy cleaning.
What are the different types of sanitary valves?
Sanitary valve types include ball, check, butterfly, needle, plug, and pressure relief valves.