Pneumatic Cylinder Lubrication
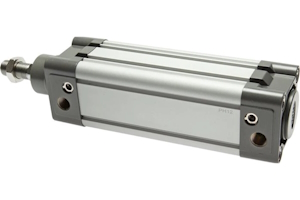
Figure 1: Pneumatic cylinder lubrication ensures a long lasting pneumatic cylinder
Proper pneumatic cylinder lubrication ensures the efficient and reliable operation of pneumatic systems. It minimizes friction between moving parts, reduces wear, and can prevent corrosion, extending the lifespan of the cylinders and maintaining optimal performance. This comprehensive guide delves into determining if a pneumatic cylinder requires lubrication, the steps to assess lubrication needs, the issues arising from over-lubrication, and detailed instructions on lubrication techniques. Additionally, it explores the various types of lubricants suitable for pneumatic cylinders and introduces the concept of lubrication-free pneumatic cylinders, highlighting their operational benefits and the technology that enables their maintenance-free operation.
Table of contents
- How to know if a pneumatic cylinder requires lubrication
- How to manually lubricate a pneumatic cylinder
- Lubricate a pneumatic cylinder with an FRL
- Types of lubricants for pneumatic cylinders
- Lubrication-free pneumatic cylinders
- FAQs
View our online selection of pneumatic products!
How to know if a pneumatic cylinder requires lubrication
To determine if a pneumatic cylinder needs lubrication, determine whether the manufacturer has pre-lubricated the cylinder. Pre-lubricated cylinders are designed to operate without the need for additional lubrication. These cylinders will not require lubrication in most instances. However, further lubrication may be required in the following situations:
- Increased friction: If the cylinder's movement becomes less smooth or more force is required to achieve the same motion, it may indicate increased friction due to insufficient lubrication.
- Unusual noises: Squeaking or grinding sounds during operation can signal metal-on-metal contact, suggesting inadequate lubrication levels.
- Visible wear: Inspection of the cylinder may reveal signs of wear, such as scoring on the piston rod or inside the cylinder barrel, indicating the need for lubrication.
- Operational environment: Harsh environments with high levels of dust, debris, or corrosive substances can compromise the cylinder's internal lubrication, necessitating additional lubrication.
Steps to determine lubrication needs
- Consult the manufacturer's guidelines: Always start by reviewing the manufacturer's recommendations regarding lubrication. This information can guide on whether and how often lubrication is needed.
- Assess operational conditions: Consider the environment in which the cylinder operates. Extreme temperatures, contaminants, and high cycle rates can all increase the need for lubrication.
- Monitor performance: Regularly monitor the cylinder for any signs of increased friction or wear. Performance metrics can serve as an early indicator of lubrication needs.
- Perform regular inspections: Visual inspections of the cylinder can reveal signs of wear or damage that lubrication could mitigate. Pay special attention to the piston rod and seals.
- Check for lubrication ports: Some pneumatic cylinders are equipped with lubrication ports, indicating that external lubrication is intended and necessary.
Issues from over-lubrication of pneumatic cylinders
-
Accumulation of excess oil:
- Contaminates air supply.
- Attracts dust and debris, forming sludge.
- Increases risk of component failure.
-
Impaired performance:
- Decreased efficiency due to fluid resistance.
- Erratic operation, including slow or incomplete movements.
-
Seal degradation:
- Seals may swell or soften, reducing effectiveness.
- Accelerated wear on seals and components.
-
Safety hazards:
- Slip hazards from leaked lubricant.
- Increased fire risk in flammable environments.
-
Maintenance and operational costs:
- Requires more frequent maintenance.
- Wastes lubricant, increasing purchase and disposal costs.
How to manually lubricate a pneumatic cylinder
Manually lubricating a pneumatic cylinder is a crucial maintenance task, ensuring smooth operation and longevity. Proper lubrication reduces friction between moving parts, minimizes wear, and can prevent corrosion.
Note: There is no universal guideline on how often a pneumatic cylinder requires lubrication. The ideal is to maintain a thin film of lubricant between mating surfaces and moving parts.
Before starting, ensure that all safety protocols are followed. Disconnect the pneumatic cylinder from its power source to prevent accidental activation. Wear appropriate personal protective equipment (PPE), such as gloves and safety glasses.
- Preparation
- Identify the lubrication points: Consult the manufacturer’s manual to locate the lubrication points. Common lubrication points include the piston rod, seals, and bearings.
- Choose the right lubricant: Use the lubricant recommended by the cylinder manufacturer. Pneumatic cylinders typically require a specific type of lubricant that won’t degrade the seals or cause other issues.
- Cleaning
- Clean the external surfaces: Wipe down the cylinder's external surfaces with a clean, lint-free cloth to remove any dirt or debris. This prevents contaminants from entering the cylinder during lubrication.
- Clean the lubrication points: Ensure that the areas around the lubrication points are clean. Use a mild solvent if necessary, but make sure it is compatible with the cylinder materials.
- Lubrication
- Apply lubricant to the piston rod: Lightly coat the piston rod with lubricant. Avoid applying too much lubricant, as excess can attract dirt or lead to hydraulic lock.
- Lubricate other points: Depending on the cylinder design, there may be additional points that require lubrication, such as bearings or internal surfaces accessible through grease fittings. Apply lubricant as directed by the manufacturer’s guidelines.
- Reassembly and testing
- Reassemble any parts: If any parts were removed or disassembled, carefully reassemble them according to the manufacturer’s instructions.
- Test the cylinder: Reconnect the power source and activate the cylinder several times to distribute the lubricant evenly. Observe the operation to ensure there are no leaks or unusual noises, which could indicate improper lubrication or assembly.
Lubricate a pneumatic cylinder with an FRL
An FRL unit is a combination of a Filter, Regulator, and Lubricator, used in pneumatic systems to prepare compressed air for use in pneumatic cylinders. Here's a simplified explanation of its role, with a focus on lubrication.
- The filter component cleans the compressed air by removing impurities such as dust and moisture. This step prevents potential damage to the system.
- The regulator adjusts the air pressure to ensure it's at an optimal level for the system's needs. Proper regulation prevents damage from excessive pressure and ensures the system operates efficiently.
- The lubricator introduces a small amount of oil into the cleaned and regulated air. This oil mist lubricates the internal components of a pneumatic cylinder as the air passes through it. The lubrication reduces friction and wear, helping to maintain smooth operation and extend the life of the cylinders.
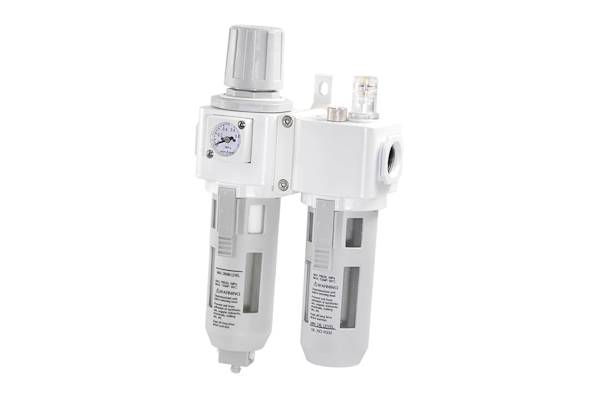
Figure 2: An FRL unit not only lubricates a pneumatic cylinder but also improves the compressed air quality, extending the cylinder's lifespan.
Types of lubricants for pneumatic cylinders
This section provides guidance on typical lubricants used with pneumatic cylinders. It explains the different lubricant types and the materials (i.e., seal materials) that these lubricants can and cannot be used with. For more information on lubricants, read our lubricant types, uses, and functions article.
Mineral oil-based lubricants
Mineral oil-based lubricants are derived from petroleum and are among the most commonly used lubricants for pneumatic cylinders. They offer good lubricity, protection against wear, and are compatible with many seal materials. However, their use is limited in applications involving high temperatures or exposure to oxygen, as they can form deposits or degrade under these conditions.
- Composition: Primarily composed of alkanes, cycloalkanes, and aromatic hydrocarbons.
- Interactions: Generally safe for use with nitrile rubber (NBR), polyurethane, and Viton seals. However, they may cause swelling in some synthetic rubber materials.
Synthetic lubricants
Synthetic lubricants are engineered to provide superior performance in extreme conditions, including high and low temperatures, high pressures, and exposure to chemicals. They can be tailored to meet specific requirements of pneumatic systems.
- Composition: Can include polyalphaolefins (PAO), esters, polyglycols, silicones, and fluorosilicones.
- Interactions: Compatibility varies widely depending on the synthetic base and additives. For example, ester-based lubricants may not be suitable for use with certain types of rubber seals, such as nitrile, due to swelling or degradation risks. Silicone and fluorosilicone lubricants are generally compatible with a wide range of seal materials but may not be suitable for all plastic components.
Greases
Greases are used in pneumatic cylinders where liquid lubricants are not practical or where additional sealing properties are needed. They consist of a base oil thickened with a soap or other thickener and may include additives to enhance performance.
- Composition: Base oil (which can be mineral or synthetic), thickener (commonly lithium, calcium, or polyurea), and additives for oxidation resistance, corrosion inhibition, and wear protection.
- Interactions: The compatibility of grease with pneumatic cylinder materials depends on the base oil and thickener. For instance, lithium-based greases are generally compatible with a wide range of materials, but greases with a synthetic base oil may need to be selected carefully to ensure compatibility with specific seal materials.
Food-grade lubricants
In applications involving food processing or packaging, food-grade lubricants are required. These lubricants are formulated to be safe in the event of incidental contact with food products.
- Composition: Typically based on white mineral oil or synthetic fluids that meet food safety standards, such as NSF H1 certification.
- Interactions: Food-grade lubricants are designed to be compatible with common seal and gasket materials used in pneumatic cylinders, including nitrile, silicone, and fluoropolymer seals. However, it's important to verify compatibility with specific materials used in a given application.
Lubrication-free pneumatic cylinders
The following selection criteria determine whether or not a pneumatic cylinder can be lubricant-free or not:
- Material selection: Components such as seals and bearings are typically made from polymers or composite materials with inherent low-friction properties. For instance, polytetrafluoroethylene (PTFE), known for its minimal friction coefficient, is commonly used in seals, reducing the need for additional lubrication.
- Internal coating: The internal surfaces of the cylinder barrel often receive a special coating designed to reduce friction and wear. This coating, which can include materials such as nickel or ceramic, provides a smooth surface that interacts efficiently with the piston and seals, further reducing the need for lubrication.
- Piston design: The piston in a lubrication-free pneumatic cylinder is designed to work with minimal lubrication. This involves not only the use of low-friction materials but also precision engineering to ensure a tight fit within the cylinder, minimizing air leakage and reducing the wear on the piston and cylinder walls.
- Seal technology: Advanced seal technology is a hallmark of lubrication-free pneumatic cylinders. These seals are engineered to provide a tight seal while operating with low friction. The materials used for the seals are selected for their durability and resistance to wear, even in the absence of lubrication.
- Self-lubricating components: Some lubrication-free cylinders incorporate self-lubricating components, such as bearings or guide rings, that release small amounts of lubricant when movement occurs. This internal lubrication mechanism ensures smooth operation over the cylinder's lifespan without the need for external lubrication sources.
Operational benefits
- Reduced maintenance: The primary advantage of lubrication-free pneumatic cylinders is the significant reduction in maintenance requirements. Without the need for regular lubrication, these cylinders can operate efficiently for longer periods, reducing downtime and maintenance costs.
- Clean operation: In industries where cleanliness is paramount, such as food processing or pharmaceuticals, lubrication-free cylinders offer the advantage of clean operation, eliminating the risk of oil contamination.
- Environmental impact: By eliminating the need for external lubricants, these cylinders contribute to a more environmentally friendly operation, reducing the potential for oil leaks and disposal issues associated with used lubricants.
- Versatility: The design of lubrication-free pneumatic cylinders allows them to be used in a wide range of environments, including those with extreme temperatures or where traditional lubricants could fail.
FAQs
What is pneumatic cylinder lubrication?
Pneumatic cylinder lubrication is the process of applying a lubricant to reduce friction and wear between the cylinder's moving parts, enhancing performance and longevity.
How often should pneumatic cylinders be lubricated?
The lubrication frequency for pneumatic cylinders depends on their usage intensity and environment, but regular assessments are recommended to maintain optimal performance.
Can over-lubrication of pneumatic cylinders cause issues?
Yes, over-lubrication can lead to the accumulation of excess oil, attracting dirt and debris, which may impair the cylinder's function and lifespan.
Are there lubrication-free pneumatic cylinders?
Yes, lubrication-free pneumatic cylinders are designed with materials that eliminate the need for external lubrication, offering maintenance-free operation.