Selecting Seal Material For High-Temperature Applications
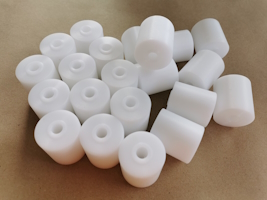
Figure 1: PTFE (Teflon) seals are suitable for some high-temperature applications.
Selecting the right material for a high-temperature seal is critical to ensure the seal does not fail during operation. The choice of high temperature sealing solutions between metal-to-metal and elastomeric (rubber-like properties of a polymer) high-temperature (can vary, typically above 350 °C) sealing solutions depends on temperature extremes, pressure levels, chemical interactions, and flexibility needs. This article overviews the common materials used to create different high temperature gaskets and seals and how to select them for varying applications.
Table of contents
- Selecting a high-temperature seal
- Metal-to-metal high-temperature seals
- Elastomeric high-temperature seals
- Applications
Selecting a high-temperature seal
When determining whether a metal-to-metal or elastomeric seal is appropriate for a specific high-temperature application, consider the following factors:
- Temperature range: Metal-to-metal seals are preferred for applications involving sustained high temperatures that exceed the limits of elastomeric materials.
- Pressure: Metal-to-metal seals offer the strength and durability needed for high-pressure applications, while elastomeric seals are suitable for lower-pressure environments.
- Chemical compatibility: If the application involves exposure to aggressive chemicals, metal-to-metal seals may be necessary. Elastomeric seals can be used with less aggressive media and where compliance with food-grade standards is required.
- Flexibility and resilience: Elastomeric seals are chosen for applications where flexibility and recovery are needed, such as in dynamic systems with movement or temperature cycling.
Metal-to-metal high-temperature seals
Metal-to-metal seals are used in extreme high-temperature applications where elastomeric seals such as rubber or plastic would decompose or lose their sealing capabilities. These seals must also withstand high pressures, aggressive media, and corrosive environments. The design and material selection of metal seals are critical to their performance.
Design considerations
-
Shape and geometry: Metal seals have various shapes, such as C-rings, E-rings, and O-rings.
- C-ring metal seals: Metal C-rings have an elastic core from a high-strength alloy shaped into a "C" profile. The softer outer layer is typically silver electroplating or a PTFE coat.
- E-ring metal seals: Metal E-rings are for low-load, high-recoil performance. The core is made of an alloy and shaped like a bellows. E-rings have a relatively higher leak rate than metal seals due to their low-loading force.
- O-ring metal seals: MetalO-rings are for high-pressure and -temperature environments. They are constructed from sturdy metal tubing, coiled, cut, and welded to the desired size.
Figure 2: Profiles for metal-to-metal seals: E-ring (left), C-ring (middle), and O-ring (right).
- Contact surfaces: The sealing surfaces must be machined to a high degree of flatness and finish to ensure proper sealing. Surface imperfections can lead to leak paths in metal-to-metal sealing.
- Seal deformation: Metal seals go through controlled deformation during installation. This deformation is how the metal-to-metal contact is created. The deformation amount must be calculated, as over-deformation can cause damage, and under-deformation can result in leaks.
- Load and stress distribution: The design must ensure uniform stress distribution to maintain sealing integrity. Uneven loading can cause parts of the seal to lift away from the mating surface, leading to failure.
Metal-to-metal material selection
The common materials used to create metal-to-metal seals are:
- Stainless steel: Stainless steel has a good balance of strength and corrosion resistance. Various grades, such as stainless steel 304 and 316, are available to suit different temperature and environmental conditions.
- Nickel alloys: Materials such as Inconel are often used to maintain strength at high temperatures and resist oxidation and corrosion.
- Copper alloys: Copper and its alloys, like beryllium copper, have good thermal conductivity and are used in applications where heat transfer is important.
- Cobalt alloys: Alloys like Stellite are known for their wear resistance and ability to retain hardness at elevated temperatures.
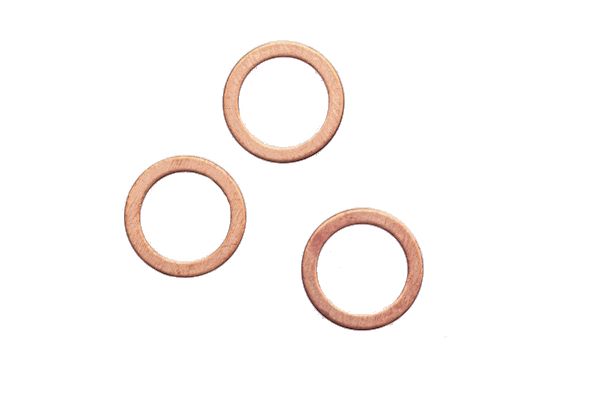
Figure 3: Copper o-rings
The following criteria are considered when choosing between the different materials for metal-to-metal seals:
Table 1: Materials and selection criteria for metal-to-metal seals
Criteria | Stainless steel | Nickel alloys | Copper alloys | Cobalt alloys |
Thermal expansion | Moderate thermal expansion coefficients. Approximately 16-18 x 10^-6 /°C | Low thermal expansion coefficients. 13-15 x 10^-6 /°C Suitable for applications with dimensional stability at elevated temperatures. | Higher thermal expansion coefficients than stainless steel and nickel alloys. 17-18 x 10^-6 /°C | Low thermal expansions. Similar to nickel alloys. 12-15 x 10^-6 /°C |
Strength at high temperatures | Strength at high temperatures, but as temperature rises, strength can reduce faster than nickel and cobalt alloys. Grade 310 retains strength up to 1150 °C | Maintain strength, mechanical properties, and oxidation resistance at high temperatures. Inconel 718 maintains strength up to 650 °C | Lower strength at high temperatures. Often limited to below 300 °C | High strength at high temperatures. Haynes 188 maintains strength up to 1090 °C |
Corrosion resistance | High corrosion resistance in extreme environments. | Similar to stainless steel, high corrosion resistance in extreme environments. | Good corrosion resistance. However, in marine environments it can undergo stress corrosion cracking or dezincification. | Corrosion resistance but not as resistant as nickel alloys and stainless steel in aggressive environments. |
Elasticity and hardness | Elasticity varies significantly between grades. Typically around 193-200 GPa for austenitic steels like 304 and 316. 304 SS has a hardness around 150-200 HB whereas hardened grades can exceed 600 HB. |
Elasticity ranges from 200-220 GPa. Hardness varies. Inconel 625 might have 20 HRC in annealed condition. | Elasticity ranges from 110-130 GPa for brasses and bronzes, pure copper lower around 110. Pure copper is soft around 40-60 HB, certain heat-treated bronzes can exceed 200 HB. | Elasticity ranges between 210-240 GPa. Some cobalt alloys can reach 40 HRC or higher. |
Elastomeric high-temperature seals
High-temperature elastomer seals are typically made of the following materials:
-
Silicone rubber
- Withstands temperatures up to 230 °C (446 °F). Some compounds can withstand temperatures up to 305 °C (581 °F) for a short period of time.
- Resistant to UV, ozone, and oxygen
- Often used in aerospace and automotive applications
- Relatively low tear resistance
-
PTFE (Polytetrafluoroethylene)
- Maintains integrity in temperatures above 260 °C (500 °F)
- Resistant to strong industrial chemicals
- Very low friction, excellent electrical insulator
- Used in a wide range of industries, from plumbing to pharmaceuticals
-
FKM (Viton)
- Can resist temperatures above 225 °C (437 °F)
- Good chemical resistance to oils, fuels, lubricants, and most mineral acids
- Not recommended for use with certain chemicals, such as brake fluids or strong acids
-
EPDM (Ethylene Propylene Diene Monomer)
- Performs well up to 150 °C (302 °F)
- Resistant to UV exposure, ozone, aging, weathering, and many chemicals
- Versatile for various applications, including in the automotive and HVAC industries
-
HNBR (Hydrogenated Nitrile Butadiene Rubber)
- Can withstand temperatures up to 150 °C (302 °F)
- Good abrasion resistance and strength
- Suitable for oil and gas industry applications and resistant to many oils and chemicals
- Not recommended for use with chlorinated hydrocarbons, polar solvents, or strong acids
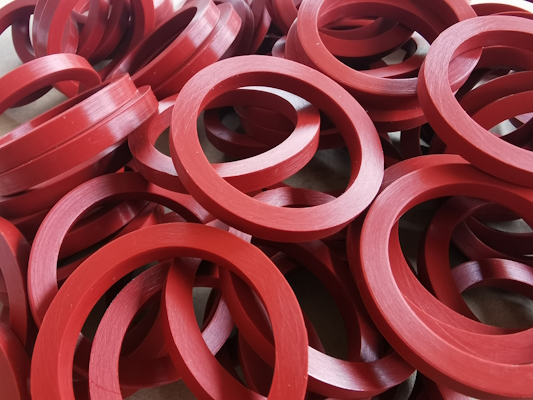
Figure 4: Silicone rubber gasket rings
Applications
Metal-to-metal seal applications
- Aerospace and aviation: Metal-to-metal seals are used in the aerospace industry for their ability to withstand extreme temperatures and pressures found in jet engines and space vehicles. They are essential for fuel systems, hydraulic lines, and exhaust manifolds where failure is not an option.
- Automotive industry: In high-performance engines, especially in exhaust systems and turbochargers, metal-to-metal seals are chosen for their durability and capacity to maintain a seal at high temperatures that would degrade elastomeric options.
- Oil and gas: For applications that involve high pressure and temperatures, such as downhole tools and wellhead equipment, metal-to-metal seals provide the necessary strength and corrosion resistance to ensure safe and efficient operations.
- Power generation: Seals in power plants, including nuclear reactors and gas turbines, must withstand aggressive media and high temperatures. Metal-to-metal seals are often the first choice due to their robustness and long service life under such demanding conditions.
- Chemical processing: Metal-to-metal seals are suitable for sealing applications involving corrosive chemicals and solvents that would compromise the integrity of elastomeric seals. They are able to withstand a broad range of chemicals without significant degradation.
Elastomeric seal applications
- Automotive cooling systems: Elastomeric seals are commonly used in automotive applications where they provide flexibility and sealing capabilities at moderate temperatures, such as in water pumps and radiator hoses.
- HVAC systems: For residential and commercial heating and cooling systems, elastomeric seals offer the necessary flexibility and chemical resistance to accommodate temperature fluctuations and prevent refrigerant leaks.
- Food and beverage processing: In industries where hygiene and cleanliness are critical, elastomeric seals are preferred due to their compliance with food-grade standards and ability to withstand the cleaning and sterilization processes without losing their sealing properties.
- Pharmaceutical manufacturing: The pharmaceutical industry requires seals that can maintain their integrity during rigorous sterilization cycles. Elastomeric seals are used in applications where a high degree of cleanliness and non-reactivity is essential.
- General industrial applications: Elastomeric seals are versatile and can be used in a variety of less extreme applications, including pneumatic and hydraulic systems, where they provide an effective seal at lower temperatures and pressures.