Selecting an Angle Seat Valve
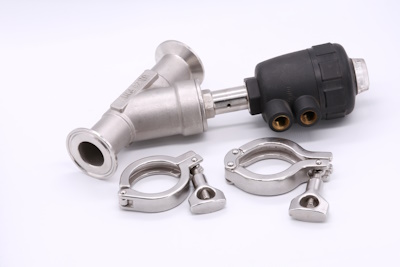
Figure 1: Angle seat valve with clamps
Selecting the right angle seat valve is crucial for efficient fluid control in various industrial applications. Known for their Y-shaped design, these valves excel in flow rate and minimize clogging, making them suitable for handling viscous fluids. They stand out for their ability to withstand high pressures and offer fast actuation, which is essential for both on/off and control tasks. This article explores the key selection parameters while choosing an angle seat valve for an application.
Table of contents
- Actuation type
- Operation type
- Connection type
- Connection size
- Material
- Maximum pressure difference
- Temperature
- Flow rate (Kv value)
- Approvals
View our angle seat valve selection here!
Actuation type
Pneumatic actuation
Pneumatic actuation uses compressed air to move the piston to shift the seal towards or away from the valve seat. Some considerations are:
- Availability of compressed air: Ideal for environments where compressed air is readily available.
- Speed of operation: Pneumatic actuators offer rapid response times, making them suitable for applications requiring quick actuation.
- Safety and explosion risk: Preferred in hazardous environments since they do not generate sparks.
- Force and torque requirements: Capable of generating significant force, making them suitable for larger valves or higher pressure applications.
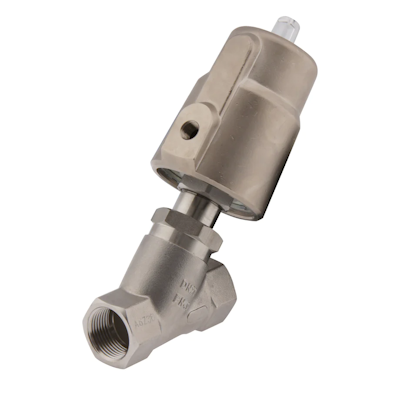
Figure 2: Stainless steel pneumatic angle seat valve
Manual actuation
Manual actuation involves the use of a handwheel, lever, or gear to manually open or close the valve. Some considerations are:
- Simplicity and cost: Ideal for simple, low-cost applications where automated control is not necessary.
- Accessibility: Suitable for installations where the valve can be easily accessed by an operator.
- No need for power supply: Does not require electricity or compressed air, making it suitable for remote or off-grid applications.
- Limited by human effort: Not suitable for large valves or high-pressure applications that would require excessive manual force. Choose a valve with ergonomic knob options for ease of operation.
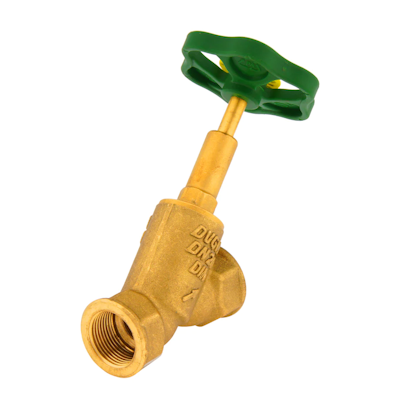
Figure 3: Manual brass angle seat valve
Electric actuation
Electric actuation uses an electric motor to drive the actuator, opening or closing the valve. Electric actuators can be controlled remotely and integrated into automated control systems. Some considerations are:
- Precision and control: Offers precise control over valve position, suitable for applications requiring accurate flow regulation.
- Remote operation: Ideal for situations where remote or automated control is needed.
- Power availability: Requires access to an electrical power source, which may be a limitation in some environments.
- Cost and maintenance: Generally higher initial cost and maintenance requirements compared to manual actuators, but offers significant advantages in terms of automation and control capabilities.
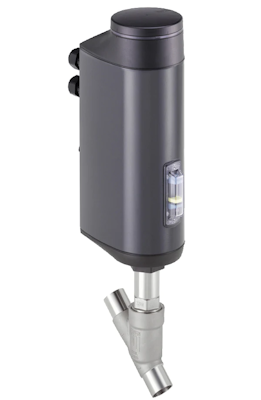
Figure 4: Electric stainless steel angle seat valve
Read our angle seat valve overview article for more details on the working and various types of angle seat valves.
Operation type
Selecting the right type of angle seat valve - normally closed (NC), normally open (NO), or double acting - depends on the specific requirements of the application. Enhanced by spring mechanisms, these valves can offer additional reliability in maintaining their default states.
Normally closed (NC) and normally open (NO)
An NC valve opens when actuated, and remains closed in the default state. This category often includes spring closing (NC) valves, which utilize a spring mechanism to ensure the valve automatically returns to a closed position when not actuated, adding an extra layer of safety and reliability.
An NO valve is open in its default state, allowing flow; It closes when actuated. This category may also include spring opening (NO) valves, which feature a spring mechanism to ensure the valve automatically returns to an open position when not actuated, ensuring continuous flow.
Read our normally open vs normally closed valve article for more details on the working and typical applications of both valve types.
Double acting
- A double acting angle seat valve requires two signals to change states; one to open and another to close. There is no default state; the valve remains in its last position until actuated. This type of valve is independent of spring mechanisms and relies on precise control signals for operation.
- Ideal for applications where the valve must stay in its last position during a power or pressure loss and for scenarios demanding high control accuracy. For example, these valves are used in regulating the flow in a fermentation process in the biotech industry, where precise control over the introduction and release of gasses is critical for maintaining optimal conditions for microbial growth.
Connection type
The connection type of an angle seat valve determines how it will be attached to the piping system. Common types include:
- Threaded:
- Flanged: Best for larger pipe diameters and high-pressure applications. Flanges provide a robust seal and are suitable for systems where the valve is not frequently removed. They facilitate easier alignment and assembly in pipelines.
-
Welded:
- Offers the most durable and leak-proof connection.
- Suitable for high-pressure, high-temperature applications, and where the valve is a permanent part of the system.
- Common in critical or hazardous fluid applications.
- Clamp: Clamp connections with a hose tail/barb ensure a secure, leak-proof connection that is easily disassembled for cleaning, enhancing both hygiene and operational efficiency in sanitary applications, , such as food, beverage, and pharmaceutical processes.
Connection size
The connection size must match the size of the piping in the system to ensure proper flow and prevent leaks or pressure drops. It's typically measured in inches or millimeters, depending on the standard used:
- Determine the pipe size: Know the nominal diameter of the pipes in the system. This is crucial for selecting the correct valve size.
- Consider flow requirements: The valve size impacts the flow rate through the system. Ensure the valve's size is appropriate for the required flow rate to avoid restrictions or excessive velocity.
- System compatibility: Ensure the connection size and type are compatible with existing piping and fittings. Adapters can be used in some cases, but direct compatibility is preferable for optimal performance.
Material
Selecting the appropriate materials for the body and seals of an angle seat valve is crucial for ensuring compatibility with the media being controlled, as well as the longevity and reliability of the valve in specific operating conditions. Read our chemical resistance chart for more details on the compatibility of various materials with different media.
Valve body materials
- Brass: Suitable for water, air, and some mild chemicals. Brass valves offer good corrosion resistance and are a cost-effective choice for non-aggressive applications.
- Stainless steel: Ideal for aggressive media and high-temperature applications. Stainless steel provides excellent corrosion resistance and durability, making it suitable for a wide range of industrial applications, including food and beverage, pharmaceuticals, and petrochemical processes.
Seal materials
- PTFE (Polytetrafluoroethylene): Offers excellent chemical resistance and can handle a wide temperature range. PTFE is suitable for aggressive media and is commonly used in applications requiring high purity.
- NBR (Nitrile Butadiene Rubber): Good for general use with oils, water, and some hydraulic fluids. NBR seals are not suitable for strong oxidizers or solvents.
- EPDM (Ethylene Propylene Diene Monomer): Excellent resistance to hot water, steam, and various mild chemicals. EPDM is commonly used in heating, cooling, and some mild chemical applications.
Maximum pressure difference
Pressure difference is the highest difference of pressure across the valve that it can withstand during operation without failing or experiencing performance degradation. Various factors affect the maximum pressure difference:
- Valve design: The construction and materials of the valve determine its strength and ability to withstand pressure differences. For example, valves designed with robust materials and thicker walls may handle higher pressures.
- Actuation method: Pneumatic, electric, and manual actuation methods can influence the valve's capability to manage pressure differences. Pneumatic actuators, for instance, might be limited by the air supply pressure, affecting the valve's ability to open against high differential pressures.
- Application requirements: Consider the operating conditions, including the maximum system pressure, the nature of the media (liquid, gas, steam), and temperature. High-temperature applications may reduce the valve's pressure handling capability due to material strength changes at elevated temperatures.
Review the angle seat valve manufacturer's datasheet or manufacturer specifications for the maximum rated pressure difference. Ensure it meets or slightly exceeds the maximum pressure difference expected in the application.
Temperature
Select an angle seat valve valve with temperature ratings that provide a safety margin beyond the expected maximum and minimum temperatures in the application to ensure reliable operation under all conditions.
- Material considerations: The body material (e.g., brass, stainless steel) and seal material (e.g., PTFE, EPDM) largely dictate the temperature range a valve can handle. Stainless steel and PTFE, for example, are suitable for higher temperature applications.
- Application specifics: Consider the specific requirements of the application, including any temperature fluctuations and the presence of aggressive media, which can affect material performance at various temperatures.
Flow rate (Kv value)
The Kv value helps in calculating whether a valve can handle the required flow rate in the system without causing excessive pressure drop. Selecting a valve with an appropriate Kv value ensures the system operates efficiently, with minimal energy loss due to friction and pressure drop. Operating conditions such as temperature, viscosity, and specific gravity of the media can affect the actual flow rate through the valve. Adjust the Kv value calculation accordingly.
Approvals
When selecting angle seat valves for specific applications, especially those involving stringent safety, health, or environmental standards, it's crucial to consider various approvals and certifications.
Food grade/drinking water approvals NSF/ANSI 61:
- NSF: Certification for products that come into contact with drinking water, ensuring they do not contribute contaminants that could cause health effects.
- FDA compliance: For food and beverage applications, valves must comply with FDA (Food and Drug Administration) regulations regarding materials that come into contact with food.
- ATEX: Essential for equipment intended for use in potentially explosive atmospheres within the EU.
- IECEx: An international certification that ensures equipment can be safely used in explosive atmospheres.