Hydraulic Solenoid Valve - How They Work
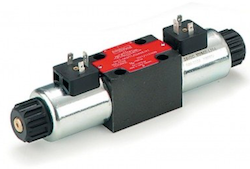
Figure 1: 4/3-way hydraulic solenoid valve
A hydraulic solenoid valve is used for opening, closing, or changing the direction of hydraulics. They control actuators, such as cylinders and motors, across various industries, like manufacturing, aerospace, and construction. This article explores the design, working, and selection criteria for 4/3 and 4/2-way hydraulic solenoid valves.
Table of contents
- Hydraulic solenoid valve construction
- 4/3-way hydraulic valve circuit function
- 4/2-way hydraulic valve design
- Detent mechanism
- Hydraulic solenoid valve selection criteria
- Industrial applications
- FAQs
View our online selection of hydraulic solenoid valves!
Hydraulic solenoid valve construction
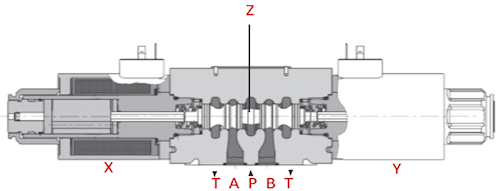
Figure 2: Components of a 4/3-way hydraulic solenoid valve: spool (Z), solenoid on either side (X and Y), and ports (T, A, P, B)
Hydraulic directional control valves are generally represented by the number of ports and switching positions. For example, a 4/3-way hydraulic valve has four ports and three positions (Figure 2). These valves are designed to handle high-pressure applications, with a maximum pressure rating of up to 350 bar (5075 psi), making them suitable for demanding environments.
The different components are:
- Spool (Z): This is a cylindrical component inside the valve that moves to direct the flow of hydraulic fluid. It has lands (sections with larger diameters) and grooves (smaller diameters). The lands block flow, while the grooves allow it.
- Solenoids (X and Y): The solenoids are placed on either side of the valve and move the spool when activated. When solenoid X is activated, the electromagnetic force pulls the spool to the left. Conversely, the spool moves to the right when solenoid Y is activated. This spool movement opens, closes, or changes port connections, altering the flow direction.
-
Ports (T, A, P, B): Hydraulic fluid enters and exits through the ports.
- Pressure port (P): This is where the hydraulic fluid enters the valve under pressure from the pump. It supplies the fluid that will be directed to the working ports.
- Working ports (A and B): These ports connect to the hydraulic actuator, cylinder, or motor). Depending on the spool position, fluid is directed to port A or B to perform work, such as extending or retracting a cylinder.
- Return port (T): This port allows hydraulic fluid to return to the reservoir after passing through the system. It helps maintain the fluid circuit and ensures that excess fluid is safely returned.
Table 1: Single solenoid vs double solenoids for hydraulic valves
Criteria | Single solenoid | Double solenoid |
Functionality | Simple on/off control; returns to default position when de-energized (spring-return) | Controls two positions; remains in the last position when de-energized (bi-stable) |
Application requirements | Suitable for applications needing a default fail-safe position | It is ideal for applications requiring position retention during power loss |
Control system complexity | Simpler wiring and control logic | More complex control logic for managing two coils |
Cost and maintenance | Generally less expensive and easier to maintain | Can be more costly and require more maintenance |
Space and installation | Typically more compact, beneficial for space-constrained installations | May require more space due to additional coil |
4/3-way hydraulic valve circuit function
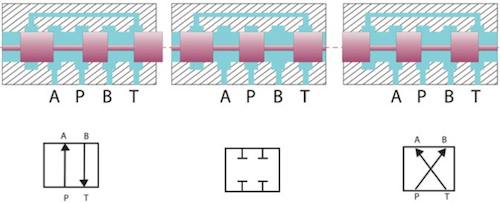
Figure 3: Working principle of 4/3-way solenoid valve
By selecting the appropriate spool position, the 4/3-way valve (Figure 1) efficiently controls the direction and flow of hydraulic fluid, enabling precise operation of hydraulic machinery. The spool inside the valve can shift into three different positions, each altering the flow path of the fluid:
- Position 1 (Figure 3, left): When the spool moves to the right, port P connects to port A, and port B connects to port T. This configuration directs fluid from the pressure port to one working port while the other working port returns fluid to the reservoir.
- Position 2 (Figure 3, middle): In this closed-center position, all ports are blocked. This stops fluid flow, allowing the system to maintain pressure without movement.
- Position 3 (Figure 3, right): When the spool shifts to the left, port P connects to port B, and port A connects to port T. This reverses the flow direction, sending fluid to the opposite working port and returning fluid from the other port to the reservoir.
Working principle
- Circuit function 1 (Figure 3, Left): Activating the spool to the right connects the pressure port (P) to working port A and working port B to the return port (T). This setup moves the actuator in one direction.
- Circuit function 2 (Figure 3, Middle): In the closed-center position, all ports are blocked, halting fluid flow and maintaining system pressure.
- Circuit function 3 (Figure 3, Right): Shifting the spool to the left connects the pressure port (P) to working port B and working port A to the return port (T). This reverses the actuator's movement.
4/2-way hydraulic valve design
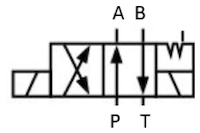
Figure 4: Circuit function of 4/2-way valve
A 4/2-way valve has four ports and two positions. These valves can have a single or double solenoid design (Table 1). They can be configured in a normally open or closed position, with a spring mechanism ensuring they return to their default state.
- In a single solenoid valve, the spool shifts when activated and automatically returns to its original position once the solenoid is de-energized.
- A double solenoid valve allows the spool to shift when one solenoid is energized and return when the other solenoid is activated.
It's crucial to ensure that only one solenoid is energized at any given time to maintain proper function and avoid potential issues.
Working principle
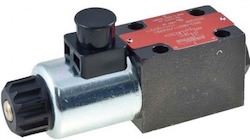
Figure 5: 4/2-way valve with one solenoid
The different components in a 4/2-way hydraulic valve are:
- Four ports: The valve includes a pressure port (P), two working ports (A and B), and a return port (T). These ports manage the flow of hydraulic fluid within the system.
-
Two positions: The spool inside the valve can shift into two different positions, each altering the flow path of the fluid:
- Position 1: In this position, the pressure port (P) connects to working port A, and working port B connects to the return port (T). This configuration directs fluid from the pressure port to one working port, allowing the actuator to move in one direction.
- Position 2: When the spool shifts to the other position, the pressure port (P) connects to working port B, and working port A connects to the return port (T). This reverses the flow direction, sending fluid to the opposite working port and allowing the actuator to move in the opposite direction.
Detent mechanism
The detent mechanism keeps the spool in place when the hydraulic valve is not energized. For example, in a 2-position valve, the detent can hold the spool in either the open or closed position. When the valve is energized, the detent releases the spool, allowing it to return to its neutral position.
Similarly, in a 3-position valve, the detent mechanism can hold the spool in any of its three possible positions. This allows the valve to maintain a specific state without continuous power, which can be helpful for energy efficiency and maintaining system stability.
Hydraulic solenoid valve selection criteria
Valve ports and positions
When choosing between 4/3-way and 4/2-way hydraulic solenoid valves, consider the following:
- 4/3-way valve: 4/3-way valve is typically used for applications requiring a neutral position where the actuator can be held, float, or have pressure relieved. It's ideal for more complex control where intermediate positions are needed.
- 4/2-way valve: A 4/2-way valve is suitable for simpler applications where the actuator must switch directly between two states, such as extending and retracting a cylinder without an intermediate position. It is ideal for straightforward on/off control.
Table 2: Common circuit functions of hydraulic solenoid valves
Circuit function | Application needs | System behavior |
All ports open | Equalize pressure or venting | Allows free fluid circulation |
All ports closed | Stop fluid flow, maintain pressure | The lock system prevents movement |
P open to A, B open to T | Move the actuator in one direction | Extends cylinder or drives motor forward |
P open to R, A and B closed | Relieve system pressure | Depressurizes system |
Detent (No default position) | Maintain position without power | Retains last position, energy efficient |
P closed, A and B open to T | Vent working ports, isolate the pressure | Allows actuator to float or neutralize |
P open to B, A open to T | Move the actuator in the opposite direction | Retracts cylinder or reverses motor |
Material
The material of the hydraulic valve should be compatible with the properties of flowing media.
- Cast iron is typically used for the hydraulic valve body due to its high strength, durability, and excellent wear resistance to hydraulic fluids.
- NBR is used for seals and o-rings in hydraulic systems because it is resistant to oils and fuels and has excellent abrasion resistance.
Read our chemical resistance guide for more information on the compatibility of different materials with various media.
Connection size
Ensure the valve size matches the port dimensions of the existing components. Hydraulic solenoid valves are typically available with connection sizes of NG6 (D03), which indicates a nominal size of 6 millimeters.
Spool action
Spool action is determined by how the application functions. After de-energization, some applications require the spool to stay in its current position, while others need it to return to the center. "Energized flow direction" is the path hydraulic fluid takes when the solenoid valve is activated (energized). For example, for energized flow direction "P open to A, B open to T,":
- P open to A: Fluid flows from the pressure port (P) to working port A, moving an actuator or extending a cylinder.
- B open to T: Fluid returns from working port B to the tank (T), completing the circuit.
Maximum pressure and temperature
The valve must withstand the maximum pressure and the application's minimum and maximum temperature requirements. Temperature is also essential in determining valve capacity, affecting the fluid's viscosity and flow. The hydraulic valve is suitable for a temperature range of -30 to 80 š©C (-22 to 176 š© F) and a maximum pressure of 350 bar (5075 psi).
Flow rate
The application's flow requirement will help determine the valve's size. To maintain efficient operation and avoid bottlenecks, choose a valve with a flow rate capacity that matches or slightly exceeds your system's requirements. Valves with flow rates of 60 - 80 l/m are commonly used.
Special features
- Manual override: Allows manual operation of the valve in case of power failure or for maintenance purposes, providing flexibility and ensuring system functionality when needed.
- Energy efficient (under 9 VA): Designed to consume low power, typically under 9 volt-amperes (VA), which reduces energy costs and minimizes heat generation, enhancing overall system efficiency.
Industrial applications
Hydraulic solenoid valves are used in a wide range of hydraulic system applications. Common solenoid valve applications are:
- Water supply systems: To control water flow and pressure for efficient distribution and leak prevention.
- Turbine systems: To regulate hydraulic fluid, adjusting turbine speed and power output to regulate the hydraulic fluid.
- Fuel/gasoline supply systems: To manage fuel flow to engines, ensuring safe and efficient delivery.
- Wastewater treatment plants: To control fluid movement through treatment stages for proper processing.
- Manufacturing plants: To automate hydraulic fluid regulation for precise machinery operation.
- Automotive industry: To control motors, brakes, and pumps, enhancing vehicle performance and safety.
- Aerospace and marine industries: To operate hydraulic systems like landing gear and steering.
- Construction: To control heavy machinery movement for tasks like lifting and digging.
- Agricultural sectors: To efficiently manage machinery for planting, harvesting, and irrigation.
FAQs
What is a hydraulic solenoid valve?
A hydraulic solenoid valve is a solenoid controlled directional valve used in a hydraulic system to open, close, or change the direction of hydraulic fluid.
What is a spool?
The spool is a cylindrical component within the valve that helps open, close, or change the flow direction in a hydraulic or pneumatic system.
What is the function of a hydraulic control valve?
A hydraulic control valve regulates fluid flow and pressure in a hydraulic system, directing the fluid to different system parts as needed.
How does a solenoid enhance hydraulic pump operation?
It allows for quick and precise control of fluid flow, improving the responsiveness and efficiency of the hydraulic system.