Pneumatic Solenoid Valve For a Single-Acting Cylinder
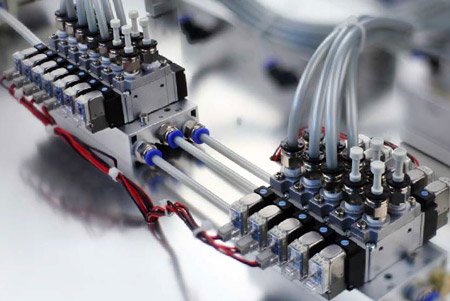
Figure 1: Pneumatic directional control valves mounted to a manifold.
A pneumatic solenoid valve controls compressed airflow to a pneumatic cylinder, allowing it to perform a working stroke in or out. Typically, a 3/2-way valve is used, featuring three ports and two positions: one connects to the air source, another serves as the exhaust, and the third links to the cylinder. The valve alternates between filling the cylinder with air to extend the piston and venting air to retract it using a spring mechanism. Understanding how to operate and select the right 3/2-way solenoid valve is crucial for efficient and reliable pneumatic system performance.
Table of contents
- Basic principle of pneumatic solenoid valves
- Types of pneumatic solenoid valves
- Valve sizing
- Basic principle of single acting-cylinders
View our online selection of pneumatic products!
Basic principle of pneumatic solenoid valves
Pneumatic solenoid valves control the flow direction of compressed air using a moving part called a spool or piston, which blocks or opens the valve ports. The spool's movement can be controlled directly or indirectly.
- Direct operation: The solenoid directly actuates the spool, making these valves suitable for low pressures or vacuum.
- Indirect operation: The spool is actuated by system pressure via an additional pilot valve. This method allows a smaller solenoid to switch the valve but requires inlet pressure to operate.
Controlling a single-acting cylinder
A 3/2-way directional control valve's ports are IN (1 or P), OUT (2 or A), and EXHAUST (3 or R). The valve has two positions: one to pressurize the cylinder and the other to vent air from the cylinder to the exhaust. Various fittings can connect to the IN and OUT ports, and a muffler can be installed in the exhaust port to reduce noise. A pneumatic muffler throttle valve can regulate the speed of the exhaust and in turn regulate the speed of the cylinder's motion. See Figure 2 for single acting cylinder symbols connected to air cylinder control valves.
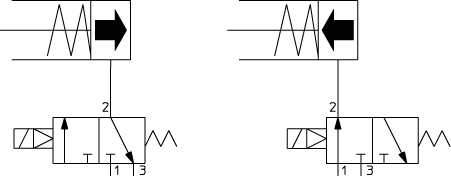
Figure 2: Symbolic representation of a spring return cylinder controlled by a mono-stable NC 3/2-way solenoid valve.
Basic principle of single-acting cylinders
A single-acting air cylinder is a linear actuator that works with compressed air. Single-acting cylinders have a spring inside that returns the piston to its base position. They are specified by key parameters such as stroke length, bore size, rod diameter, spring force, and system pressure.
Single-acting cylinders are advantageous because they require less tubing, compressed air, and wiring. However, the spring limits the working stroke and reduces the pneumatic force.
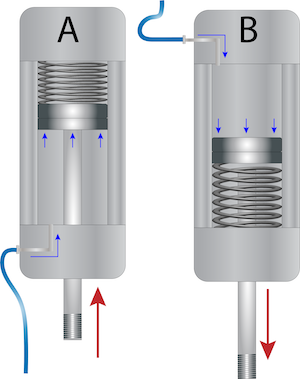
Figure 3: A spring extend (A) and spring return (B) single-acting pneumatic cylinder.
Types of pneumatic solenoid valves
Several types of pneumatic solenoid valves are available, but the 3/2-way valve is most relevant for single-acting cylinders. These can be:
- Normally open (NO): Air flows from port 1 to port 2 when the solenoid is not actuated. When the solenoid is energized, air is vented from port 2 to port 3. Upon deactivation, a spring returns the valve to the open position.
- Normally closed (NC): When not actuated, air is vented from port 2 to port 3. When the solenoid is energized, airflows from port 1 to port 2. Upon deactivation, a spring returns the valve to the closed position.
- Bi-stable: A bi-stable valve changes its position when activated and maintains it when deactivated, so it does not need constant energy to maintain its position.

Figure 4: Symbols for 3/2-way solenoid valves: normally open & mono-stable (left), normally closed & mono-stable (center) and normally closed & bi-stable (right).
Valve sizing
To specify the appropriate size for a solenoid valve for a pneumatic cylinder, the pneumatic system's air consumption and required airflow must be calculated. Boyle-Charles's law (pV=nRT) can be used for this calculation. In the case of a single-acting cylinder, the volume, tubing length, operation frequency, and system loss are relevant for the calculation.
where:
- A: pressure receiving area [mm2 ]
- a: pipe inner section area [mm2 ]
- p: supply pressure [MPa] (1MPa = 10bar)
- N: operation frequency [cycle/min]
- L: cylinder stroke [mm]
- l: piping length [mm]
- t: total stroke time [s]
- T: temperature [K] (K = °C + 273.15)
The above formulas are valid for A.N.R. conditions. A.N.R. is a French abbreviation for “conditions de l’atmosphère normale de rèfèrence”, which means “standard reference atmospheric conditions” (20 °C, 1013 mbar, humidity (relative) 65%).
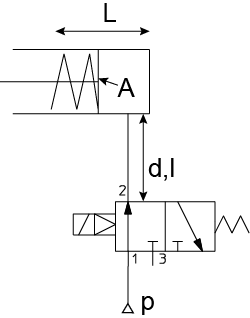
Figure 5: Pneumatic circuit with a single-acting spring return cylinder and a NC 3/2-way valve.
Example
In this example, a pneumatic system contains a single-acting spring return cylinder with the following parameters:
- System pressure = 0.5 MPa (5 bar)
- Temperature = 293K (20 °C)
- Cylinder stroke (L) = 50 mm
- Bore size/Piston diameter = 40 mm
To connect the cylinder with the 3/2 valve, the following tube is used:
- Piping length (l) = 2 m
- Pipe inner diameter (d) = 4 mm
The required operation frequency (N) is 50 cycles/min.
The pressure receiving area can be calculated from the bore size:
The pipe's inner area is:
The air consumption at the time of extrusion (Q) can be calculated now. In this case, this is also the air consumption for one cycle:
The air consumption/minute is:
The total stroke time (t) is 0.6 s.
The required airflow:
The valve can be selected when the air consumption and the required airflow are calculated. The valve data sheets must be checked to find the appropriate valves. All data sheets contain information about the valves' flow rates (see the picture below). The flow rate of the selected valve needs to be higher than the system's required air flow.
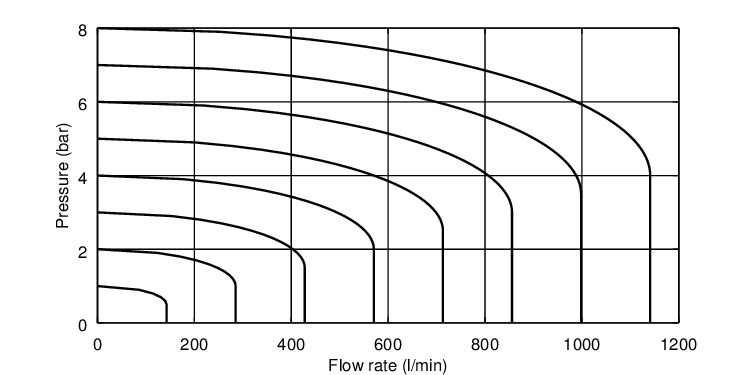
Figure 6: Example of a flow rate diagram with nominal flow rate (L/min) against inlet pressure and pressure loss.
FAQs
What is a solenoid valve for a pneumatic cylinder?
A solenoid valve for a pneumatic cylinder regulates compressed airflow to control the cylinder's movement, typically using a 3/2-way valve.
How does a single acting pneumatic cylinder work?
A single acting pneumatic cylinder uses compressed air to extend the piston and a spring to retract it, controlled by a solenoid valve.
How do you control an air cylinder with a solenoid valve?
To control an air cylinder with a solenoid valve, connect the valve to the air source, exhaust, and cylinder. The valve alternates air supply and venting to move the piston.