How Bourdon Tube Pressure Gauges Work
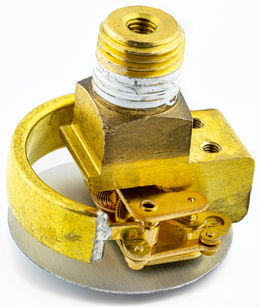
Figure 1: Bourdon tube pressure gauge mechanism
A bourdon pressure gauge is the most common type of pressure gauge and it uses a curved tube that straightens under pressure and shows the reading on a dial. Key features of them are: high accuracy, high precision, resistance to vibration, and easy maintenance. This article discusses a bourdon tube’s operating principle, selection criteria, and applications.
Table of contents
- Bourdon tube operating principle
- Dry and wet bourdon tube gauge
- Features
- Selection criteria
- Applications
- FAQs
View our online selection of pressure gauges!
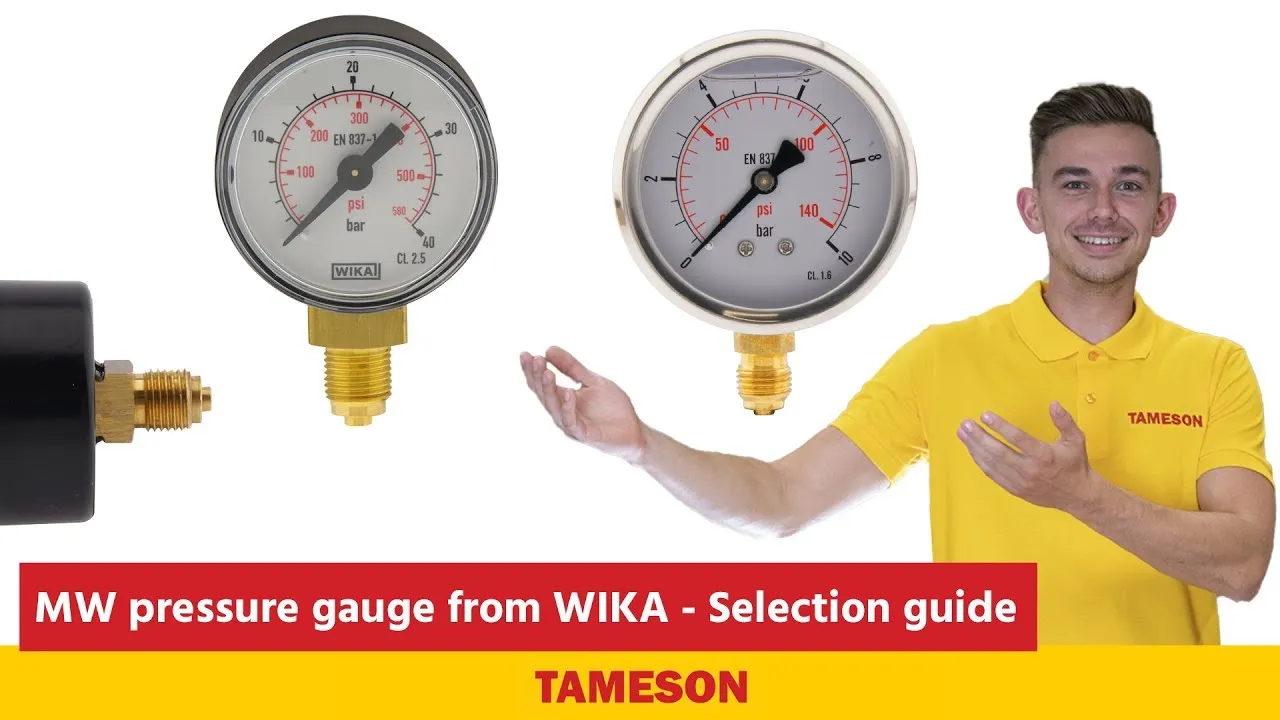
Bourdon tube operating principle
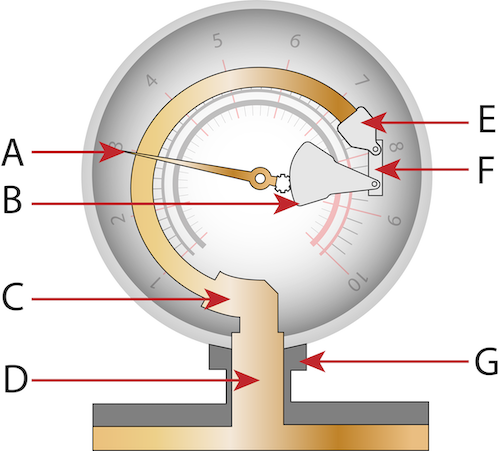
Figure 2: Bourdon tube components: indicator needle (A), sector gear (B), bourdon tube’s stationary end (C), inlet pipe (D), bourdon tube moving end (E), pivot and pivot pin (F), and socket block (G).
Figure 2 illustrates the components of a bourdon tube pressure gauge. The following list describes the operating principle.
- A bourdon tube pressure gauge is attached to the pipeline at the inlet pipe (D). The socket block (G) holds the inlet pipe in place, which also holds the device to the process line.
- Fluid flows into the stationary end of the bourdon tube (C).
- The fluid pressure distributes throughout the C-shaped bourdon tube (E). As a result of this pressure, the C-shape straightens.
- A pivot and pivot pin (F) connect the straightening movement with the sector gear (B) at the moving end of the bourdon tube.
- The movement at the moving end is amplified by the gearing system so that a very slight pressure change results in a considerable motion of the indicator needle (A). Generally, the indicator moves from left to right in a circular path over a calibrated scale. A complete decrease in pressure will result in the bourdon tube returning to its original position.
Dry and wet bourdon tube gauge
Dry bourdon tube gauge
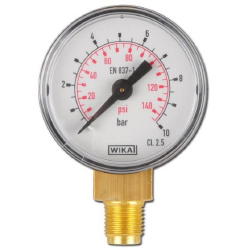
Figure 3: Bourdon tube pressure gauge
A dry bourdon tube pressure gauge is not filled with any type of fluid. It is sealed and contains only air. These types of gauges are less expensive to produce and are generally less complex than oil-filled gauges. However, dry gauges are not as accurate as oil-filled gauges and may require more frequent calibration.
Wet bourdon tube gauge
An oil-filled bourdon tube pressure gauge is filled with oil or glycerine. The fluid serves to lubricate the movement of the bourdon tube and the pointer, improving the gauge's overall accuracy and lifespan. Additionally, oil-filled gauges are more resistant to vibration and temperature changes than dry ones, making them more accurate and stable for high-pressure hydraulic measurements. However, oil-filled gauges are more expensive and may require more maintenance.
Features
- High-pressure range: Bourdon gauges can withstand high pressures, with typical pressure ranges of up to 1034 bar (15,000 psi).
- High accuracy: The bourdon tube pressure gauge exhibits high sensitivity to pressure changes, ensuring high accuracy and precision in the reading, typically within 2% of full scale. This makes them ideal for use in applications with critical pressure measurements, such as in process control and real-time monitoring systems.
- Vibration and corrosion resistance: The vibration and corrosion resistance offered by the pressure gauge makes it the preferred choice of many industries for their pressure measurement applications.
- Ease of use: They are simple to install and require minimal maintenance. They are also equipped with clear, easy-to-read dials and pointer indicators.
- Low cost: Bourdon tubes are relatively inexpensive, making them a cost-effective option for many industrial and commercial applications.
Selection criteria
There are several factors to consider when selecting a bourdon pressure gauge for a particular application.
- Gauge material: The gauge material should have chemical compatibility with the fluid media to avoid corrosion. The most common housing material for the bourdon tube pressure gauge is stainless steel, aluminum, or copper alloys. Stainless steel is the preferred choice when working with corrosive media. See our chemical compatibility chart for more detail on material compatibility; also, check our article on housing selection guide.
- Gauge diameter: The dial size for the bourdon tube pressure gauge is available in a wide range of diameter options depending upon the space limit and readability requirement. The dial diameter ranges from 25 mm to 406 mm (1 in to 16 in).
- Pressure range: It is important to consider the maximum and minimum pressure ranges of the application to ensure there is no excess stress exerted on the bourdon tube. The maximum operating pressure should not exceed 75% of the full-scale range and 65% for pulsating pressure.
-
Temperature range: The normal temperature ranges for the bourdon tube pressure gauge are:
- Dry or silicon-filled gauge: -40 𐩑C to +60 𐩑C (-40 𐩑F to +140 𐩑F)
- Glycerine or oil-filled gauge: -20 𐩑C to +60 𐩑C (-4 𐩑F to +140 𐩑F)
Glycerine is a standard fill suitable for warmer temperatures. The glycerine-filled pressure gauge is also suitable for applications with pulsating pressure.
- Vibration resistivity: Use a dry bourdon tube gauge if the gauge is exposed to minimal vibration. However, in the case of excess vibration, the dry gauge will shake the pointer making it hard to read the measurement. In this case, use a wet gauge; the liquid in the gauge absorbs the shake and pulsation, allowing easy reading of accurate pressure. Use a pressure gauge snubber in case of pressure spikes or pulsation.
- Corrosion resistance: The stainless steel liquid-filled gauge is recommended to keep the gauge from high corrosion. The liquid (oil or glycerine) filled gauge lubricates and protects against corrosion for the pointer.
- Mounting options: The bourdon tube pressure gauges are available with horizontal or vertical threaded connections or panel mounting options.
- Pressure unit: The pressure measure unit for the bourdon tube pressure gauge is bar or psi. The pressure usually ranges from 0.6 to 700 bar (8 to 10000 psi).
Read our pressure gauge selection guide to learn more.
Applications
The bourdon tube gauges are the most common pressure gauge used for medium to high-pressure measurement due to their durability, accuracy, and ease of use. The most common industries that utilize the bourdon tube pressure gauge are:
- Pneumatics and hydraulics: They are used in pneumatic and hydraulic systems to measure the pressure of air and liquids in cylinders, pumps, and other components.
- Water treatment: They are used to measure the water pressure in water treatment plants, ensuring that the water is being pumped and treated at the correct pressure.
- Oil and gas production: Bourdon tube pressure gauges are often used in the oil and gas industry to measure the pressure of well fluids, pipelines, boilers, and other equipment.
- Power generation: They are used in power plants to measure the pressure of steam, water, and other fluids to generate electricity.
- HVAC systems: They measure air pressure and other gasses in heating, ventilation, and air conditioning systems. Read our article on air compressor gauges for more details.
- Automotive and transportation: They are used in automotive and transportation applications to measure the pressure of fluids in engines and vehicle braking systems.
- Agriculture: Bourdon tubes are commonly used to measure the pressure of fluids in sprayers, irrigation systems, and other agricultural equipment.
- Medical: They are used to measure the pressure of gasses and fluids in medical equipment, such as in oxygen tanks and blood pressure monitors.
There are various designs available for pressure gauges besides the bourdon tube, like the bellows pressure gauge and the diaphragm pressure gauge. Read our pressure gauges overview article for more information on how they work.
FAQs
What is a bourdon tube pressure gauge?
A bourdon tube gauge measures pressure by using a curved tube that straightens under pressure and shows the reading on a dial.
What is the use of a sprayer pressure gauge?
Bourdon tube pressure gauges in sprayers measure fluid pressure for consistent spray patterns and optimal results.