How Does a Bellows Pressure Gauge Work?
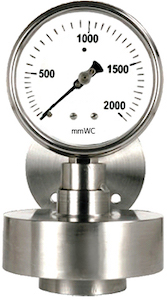
Figure 1: Bellows pressure gauge
A bellows pressure gauge consists of a flexible metal bellows that expands or contracts in response to changes in pressure. The expansion and contraction converts into a readable measurement by a connected mechanical or digital display. It is capable of measuring absolute, differential, or positive and negative (vacuum) gauge pressure. These gauges have high accuracy and durability, making them a popular choice in many industrial and laboratory settings. They are commonly used in applications with low to intermediate system pressures such as process control, fluid power systems, and gas analysis. This article provides a technical overview of bellows pressure gauges, including their design and functioning, as well as their advantages and limitations.
Table of contents
View our online selection of pressure gauges!
Working principle
To learn about other pressure gauge types, read our articles on diaphragm pressure gauges, liquid filled pressure gauges, and bourdon tube pressure gauges.
There are two types of bellows pressure gauges: single bellows and dual bellows pressure gauges. A single bellows pressure gauge measures a system’s gauge or vacuum pressure whereas a two bellows pressure gauge measures absolute and differential pressure. Read our guide on pressure types to learn more.
Single bellows pressure gauge
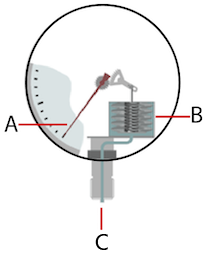
Figure 2: A bellows pressure gauge with components: pointer (A), bellows (B), and inlet (C).
A single bellows pressure gauge measures pressure relative to atmospheric pressure, in other words, gauge and vacuum pressure. System media flows into the pressure gauge through the gauge’s pressure inlet (Figure 2 labeled C). For low pressure applications, media flows directly into the bellows (Figure 2 labeled B) and for high pressure applications, the media flows around the bellows. The difference in pressure inside and outside of the bellows causes it to expand or contract. The bellows is mechanically linked to the pointer (Figure 2 labeled A). Bellows expansion and contraction proportionally moves the pointer to indicate the media’s pressure. Bellows are typically spring-loaded, preventing their full expansion, which minimizes the potential for damage to the bellows.
Dual bellows pressure gauge
Dual bellows pressure gauges are typically used to measure absolute pressure. One bellows is evacuated and sealed, making it a perfect vacuum. The other bellows is connected to the system process pressure. The two bellows are joined by a motion balance mechanism on a fixed pivot. Increase in system pressure causes the measuring bellow to expand, which tilts the motion balance mechanism and moves the needle that indicates absolute pressure.
Dual bellows pressure gauges are also suitable for measuring differential pressure. One bellows connects to the low pressure side of the system and the other bellows connects to the high pressure side. Each bellows influences the movement of the pointer mechanism to show the difference in pressure impacting the bellows.
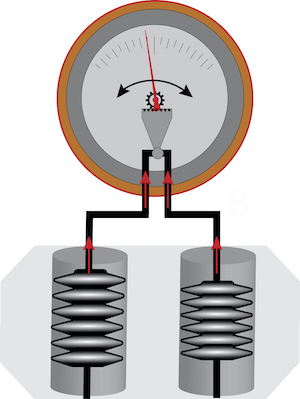
Figure 3: A dual bellows pressure gauge that can be used to measure absolute or differential pressure.
Selection criteria
- Gauge material: The gauge material must be chemically compatible with the system’s media. A bellows pressure gauge is generally made of stainless steel, Inconel, brass, beryllium copper, or phosphor bronze. Stainless steel is a preferred choice for its corrosion-resistant properties. For more detail, see our chemical compatibility chart.
- Gauge diameter: Bellows pressure gauge diameters are available in a wide range of sizes. Generally, the dial is 6 - 10 cm (2.5 - 4 in) in diameter.
- Pressure range: To ensure safe and stress-free operation, it is important to consider the maximum and minimum pressure ranges of the application. The maximum operating pressure should not exceed 75% of the gauge’s full-scale range or 65% for pulsating pressure. A bellows pressure gauge is recommended for control pressure ranges between 0.2 to 1 kg/cm2 (2.8 to 14.5 psi).
- Hysteresis: Hysteresis means the pressure sensing element (bellows) does not return to its original position once the pressure causes its mechanical deformation. Generally, metal bellows exhibit negligible hysteresis as long as the deflection is kept beneath the springs’ elastic limit. Beyond the elastic limit, the bellows can be permanently deformed. Want to learn more about hysteresis? Then read our article on the hysteresis of pressure switches.
- Bellows fabrication: Bellows are usually made from a thin-walled seamless tube with wall thickness typically ranging from 0.008 to 0.3 mm. Phosphor bronze bellows provide good hysteresis properties. Stainless steel provides good corrosion resistive properties but can be less elastic. Read our article on choosing the right housing material to learn more.
For more information about selection criteria, read our pressure gauge selection tips article.
Applications
Compared to other gauges, the bellows pressure gauge provides the advantage of low cost. It also provides excellent pressure measurement for low to moderate pressure ranges. However, it may not be suitable for high-pressure applications. These gauges also show adaptability to absolute or differential pressure. These advantages make bellows pressure gauges suitable to use in applications including:
- HVAC: Bellows pressure gauges measure the pressure of the refrigerant or air in the system.
- Power transmission system: Bellows pressure gauges are typically installed on the discharge side of a pump to measure the pressure of fluid (oil) in the system.
- Aerospace systems: There are several subsystems in aerospace systems that bellows pressure gauges are applicable for. For example, fuel systems, pneumatic and hydraulic systems, and engine systems.
- Electrical interrupters: An electrical interrupter uses an insulated gas to separate electrical contacts to open or close an electrical circuit. A bellows pressure gauge reads the pressure of the gas.