Angle Seat Valve Working Principle
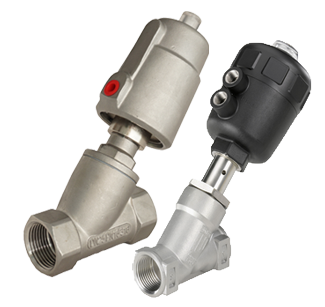
Figure 1: Common angle seat valves
An angle seat valve regulates the flow of various media types, minimizing flow impedance and pressure loss due to its angled seat design. Known for durability and high cycle life, these valves excel in harsh environments and handle high temperatures and viscosities, making them superior to ball and solenoid valves. They can be actuated manually, pneumatically, or electrically.
Table of contents
- Construction and design
- Advantages and disadvantages of angle seat valves
- Applications
- Angle seat valve selection
- FAQs
View our online selection of angle seat valves!
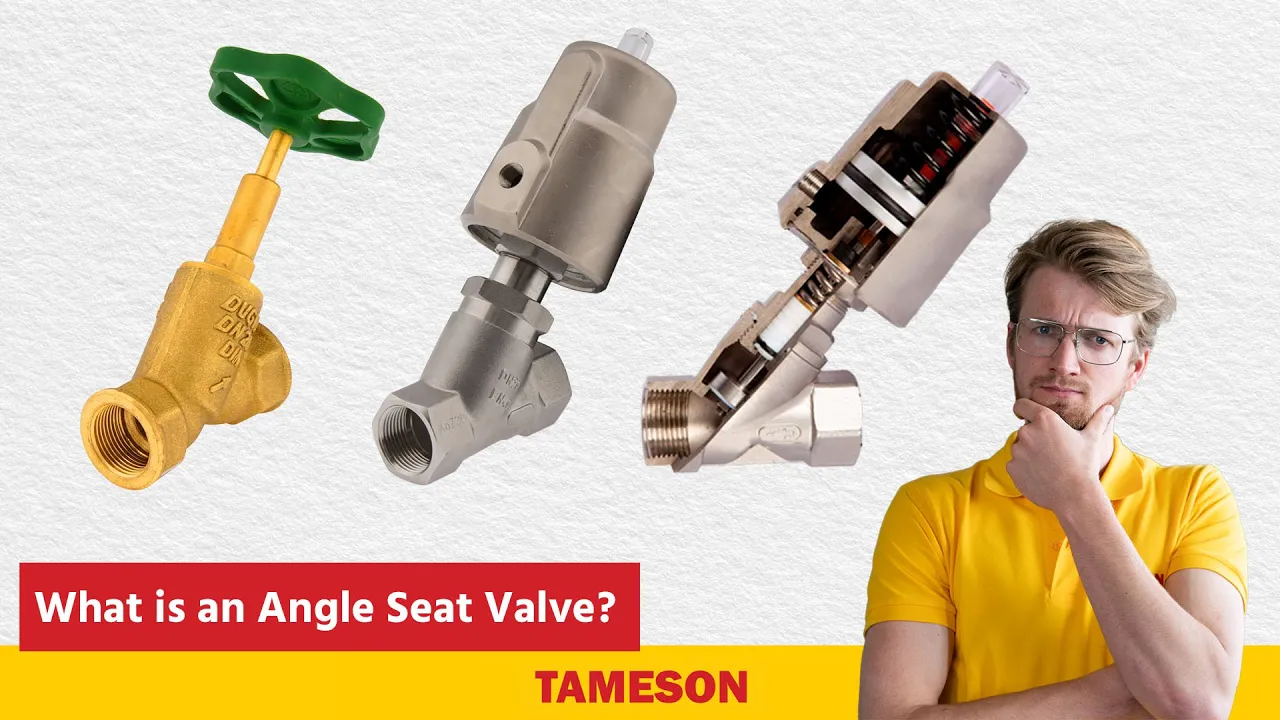
Construction and design
This section offers a detailed overview of manual and pneumatic angle seat valves in order to describe angle seat valve function for manual and automatic valves. It breaks down the key components and their roles, ensuring a solid understanding of angle seat valve operation and structural features for effective application.
Manual angle seat valve
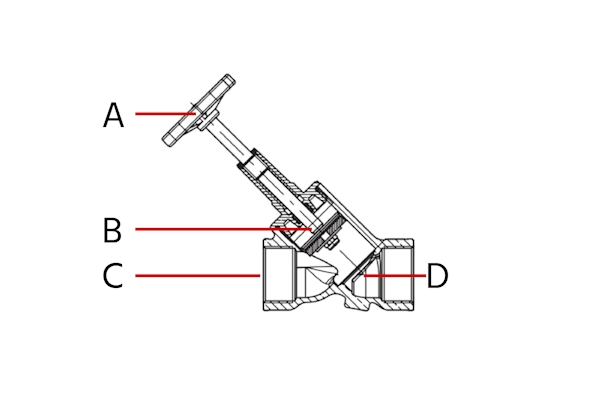
Figure 2: Diagram of a manual angle seat valve with components: handwheel (A), plug/disc (B), connecting port (C), angled valve seat (D).
Key components (Figure 2) of an angle seat valve explained:
- Handwheel (A): Enables manual operation of the valve, allowing the user to open or close it by turning the wheel.
- Plug/disc (B): Acts as the closure element within the valve, sealing off flow when the valve is closed.
- Connection port (C): Serves as the interface for attaching the valve to piping systems, facilitating the flow of media through the valve.
- Angled valve seat (D): Designed to ensure a tight seal when the valve is closed and to regulate flow efficiently when open, its angled position enhances flow dynamics.
Automatic angle seat valve
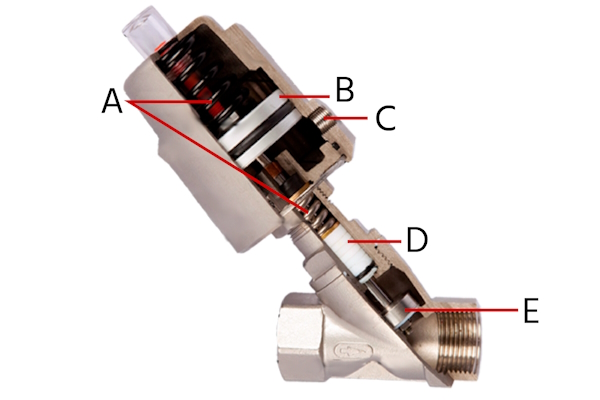
Figure 3: Section view of a pneumatic angle seat valve: spring return (A), piston (B), air port (C), packing (D), and plug/disc (E).
Key components of a pneumatic angle seat valve (Figure 3):
- Spring return (A): The spring return ensures the valve returns to its original position (either open or closed) when air pressure is no longer applied.
- Piston (B): The piston in a pneumatic angle seat valve acts as the actuator's driving force. When pressurized air enters the valve, it moves the piston. This linear motion is then transferred to the valve plug, lifting it off its seat to open the valve or allowing it to return to its seat to close the valve.
- Air port (C): The air port is the entry point for pressurized air into the valve's actuator chamber. Its size and design are critical for controlling the flow rate of air that moves the piston.
- Packing (D): Packing provides a seal between the moving and stationary parts of the valve, particularly around the piston rod that connects the piston to the valve plug. This seal prevents the media being controlled from leaking out of the valve body and also keeps the pressurized air from escaping.
- Plug (E): The plug, or disc, is the component that directly interacts with the valve seat to control the angle seat valve flow direction through the valve. When the piston lifts the plug from the seat, the valve is open, allowing flow. When the plug is pressed against the seat, the valve is closed, stopping the flow.
Often, the actuator head can be rotated 360° to allow the optimum position of air and electric lines in tight locations. The valve body is generally made of brass or stainless steel. Connection types include threaded, clamped, or welded. Typically, a visual indicator on the top of the piston shows whether the valve is open or closed.
Electric angle seat valves
The electric actuator in angle seat valves is equipped with a motor that converts electrical energy into mechanical torque, facilitating precise control over the valve's opening and closing actions. This motor is often paired with a gearbox to enhance torque output and control, allowing for the fine adjustment of the valve position. Additionally, integrated sensors and control circuits within the actuator provide feedback on the valve's status and position, enabling real-time adjustments and automation. This setup ensures that the electric actuator can accurately respond to control signals, adjusting the flow of media through the valve with high precision.
Advantages and disadvantages of angle seat valves
Angle seat valves offer an option for many industrial applications due to their efficiency, durability, and versatility. However, considerations around control complexity, installation, maintenance, and cost should be carefully weighed against the specific requirements of the application.
Advantages
- High flow rate with minimal pressure loss: Angle seat valves have a direct flow path when the valve is open, significantly reducing flow impedance and pressure loss.
- Durability and high cycle life: Angle seat valves are known for their robust construction and ability to withstand harsh environments. Also, they can handle high temperatures and viscosities. They are suitable for demanding applications with an expected life of over 10 million cycles.
- Versatility: These valves can regulate liquids, gasses, steam, and aggressive fluids.
- Suitability for high-temperature applications: Angle seat valves can handle temperatures up to 200 °C (392 °F) with PTFE sealing.
Disadvantages
- Larger actuator requirement for strong return springs: A stronger return spring may be necessary to balance the reduced working pressure due to water hammer. A larger actuator is necessary to overcome the increased spring strength.
- Installation and maintenance considerations: Manufacturer specifications require proper installation and regular maintenance. This prevents leaks and ensures efficient operation. This extra work may be seen as a disadvantage.
- Cost: Due to their robust design and material options, angle seat valves can be more expensive upfront compared to simpler valve types like ball or solenoid valves. However, their durability and long service life can offset the initial investment over time.
Applications
Angle seat valves are highly versatile and find applications across a broad spectrum of industries due to their efficiency, durability, and ability to handle a wide range of media types and operating conditions.
-
Food and beverage industry
- Sterilization processes: Utilized in steam sterilization equipment to ensure the sterility of food and beverage products, as well as the equipment used in their production.
- Filling systems: Employed in the precise control of filling operations for bottles and cans, where the fast response time and accurate flow control of angle seat valves are essential.
- Process control: Used in the control of various media, such as water, steam, and other fluids involved in food and beverage processing.
- Learn more in our sanitary angle seat valves article.
-
Chemical industry
- Dosing systems: Angle seat valves are used for the accurate dosing of chemicals in processes where precise amounts of chemicals need to be added to a reaction or process stream.
- Flow control in aggressive media: Their robust construction makes them suitable for handling aggressive and corrosive chemicals, providing reliable flow control in harsh chemical environments.
-
Oil and gas industry
- Steam applications: Ideal for steam control applications, including steam injection for enhanced oil recovery, where their ability to handle high temperatures and pressures is crucial.
- Process isolation and control: Used for isolating and controlling the flow of gasses and liquids in various stages of processing and refinement.
-
Water and wastewater treatment
- Sludge control: The angle seat valve's design minimizes clogging, making it suitable for controlling the flow of slurry and sludge in wastewater treatment plants.
- Water treatment processes: Employed in various water treatment processes, including filtration, chemical dosing, and disinfection, where their reliability and precise control improve process efficiency.
-
Pharmaceutical industry
- Clean steam systems: Utilized in clean steam applications for sterilization of equipment and pharmaceutical products, where their ability to handle high temperatures and ensure sterile conditions is valued.
- Process control: Angle seat valves are used in the precise control of fluids and gasses in the manufacturing of pharmaceuticals, ensuring the integrity and quality of the products.
-
Manufacturing and automation
- Automated production lines: In automated manufacturing processes, angle seat valves are used for controlling the flow of air, water, and other media, contributing to the efficiency and automation of production lines.
- Cooling systems: Employed in the control of cooling media in machinery and equipment, ensuring optimal operating temperatures and preventing overheating.
-
Heating, ventilation, and air conditioning (HVAC)
- Steam heating systems: Used in the control of steam for heating purposes, where their ability to handle high temperatures and pressures is essential for efficient heating operations.
Angle seat valve selection
End connections and line size
Angle seat valves come in various sizes and end connections, ranging from 1/2 to 3 BSP or NPT threads, with some manufacturers offering flange options. The nominal diameter (DN) of the valve seat and the Kv-value, which indicates the flow rate of water at a pressure drop of 1 bar, are essential for selecting the right size. Use our valve sizing calculator to determine the minimum required Kv-value for your application, ensuring high and efficient flow with minimal wear and leakage.
Operating temperature, pressure, and material properties
The maximum working pressure typically ranges from 5 to 20 bar. Consider both the media pressure and the compressed air circuit pressure range. Angle seat valves can handle temperatures up to 200 °C (392 °F) with PTFE (Teflon) sealing, while other materials like NBR, FKM, and EPDM have lower temperature ratings. The choice of housing material, such as bronze, stainless steel, brass, plastic, or gunmetal, affects the temperature and pressure rating, with stainless steel providing excellent corrosion resistance and material strength. For high-pressure or high-temperature applications, opt for a stainless-steel angle seat valve with PTFE seals. Learn more about the various materials in our chemical resistance guide.
Valve installation and maintenance
Proper angle valve installation is critical for performance and safety. Ensure that the valve is installed according to the manufacturer's specifications. Regular maintenance checks are necessary to prevent leaks and ensure the valve operates efficiently.
FAQs
What is an angle seat valve?
An angle seat valve is a pneumatic valve designed for regulating flow with minimal pressure loss, ideal for high-temperature and viscosity applications.
How does a pneumatic angle seat valve operate?
A pneumatic angle seat valve operates by using air pressure to move a piston, which in turn opens or closes the valve for flow control.
What are the advantages of using an angle seat valve?
Angle seat valves offer high durability, superior flow rates, and are suitable for harsh environments, making them more efficient than ball or solenoid valves.