Plug Valve vs Gate Valve
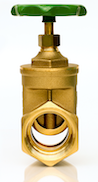
Figure 1: Gate valve
Plug and gate valves are both stop-valves suitable for a wide array of applications and media types. For example, they can both be used for clean media and media containing solids or stringy material. Therefore, it may be difficult to determine which is more suitable for a specific application. This article looks closer at the similarities and differences between gate valves and plug valves to help ensure the correct valve is chosen and used for varying applications.
Before deciding between the two valves, it is important to consider the following:
- The number of ports needed
- How fast the valve needs to operate
- The pressure and temperature of the planned system
- Installation space available
View our online selection of gate valves!
Plug vs gate valve comparison
Plug and gate valves are named after the method that each uses to allow or block flow. A plug valve uses a plug with an opening running through it. When a gate valve is closed, its disc sits perpendicular to and blocks the flow, operating much like a gate.
Operating principles
Plug valves are quarter-turn valves, meaning the valve stem needs to turn only 90° for the valve to fully open or close. With mechanical lever actuation (pneumatic and electrical actuation are also possible), the valve’s lever is turned 90° to accomplish this. When turned on, the opening in the plug is in line with the ports, and media can flow through the valve. Closing the valve rotates the plug, so the opening is no longer aligned with the ports, and the plug’s body blocks the flow.
Gate valves are multi-turn valves, meaning the valve stem needs to turn more than 360° for the valve to fully open or close. Therefore, a gate valve closes significantly slower than a plug valve. Turning the valve’s handwheel (mechanical actuation) can raise or lower the disc within the valve’s body. Fully raising the disc allows media to flow unobstructed, and fully lowering the disc blocks the media. Discover more by reading our gate valve and plug valve articles!
Plug valve design
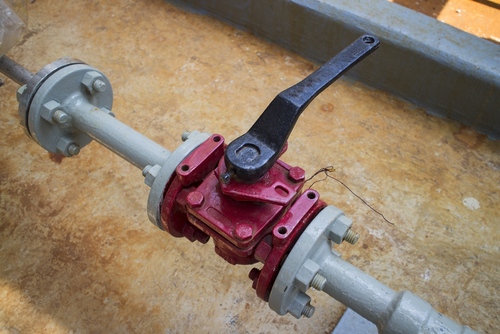
Figure 2: Plug valve
The four distinguishing design characteristics of a plug valve are the plug shape, plug opening, whether the valve is lubricated or non-lubricated, and the number of ports.
Plug shape
- Cylindrical: This shape allows for a larger opening but has a shorter life span.
- Tapered: This shape has a restricted opening but typically lasts longer.
Plug opening
- Rectangular: This opening is the most common; the size of the opening is at least 70% of the connecting pipe’s inner diameter.
- Round: This opening can be full-bore or reduced-bore design.
- Diamond: This opening has a venturi restricted flow type and is designed for throttling flow.
Lubricated vs non-lubricated
-
Lubricated: The valve’s parts are entirely metal. Lubrication reduces friction between the plug and valve body, acts as a seal, and prevents corrosion.
- Before lubricating a plug valve, consult the plug valve’s manufacturer to determine the correct lubricant to use.
- Non-lubricated: A Teflon or plastic sleeve fits around a tapered plug, which presses the sleeve against the valve body for better sealing. Non-lubricated plug valves require minimal maintenance and are unsuitable for high-temperature applications.
Ports
- Double-port: A standard, bidirectional design used as a full-bore or reduced-bore valve.
- Multiport: 3-way plug valves are common, but 4-way and 5-way are also possible. Multiport plug valves are used in transfer lines and diverting services. A single multiport plug valve can take the place of multiple gate valves.
Gate valve design
Beyond how to actuate a gate valve (mechanically, pneumatically, or electrically), the primary distinguishing design characteristics are the valve’s disc, how the bonnet connects to the valve body, and whether the stem is rising or non-rising.
Disc types
- Wedge: This type has a high wedging force which assists with sealing due to its wedge shape that sits on two inclined seats.
- Knife: This type can cut through thick fluids and dry solids that build up using its beveled edge.
- Double-disc: This type uses two discs that expand from one another to give a tight seal.
- Slab: This type is one piece with a hole bored through it. The hole aligns with the ports, allowing flow, when the gate is fully open and the disc body blocks flow through the ports when the gate is fully closed.
Bonnet types
- Welded: This type is less likely to leak because it is threaded into the valve body and the body-bonnet joint is welded.
- Bolted: This type is suitable for high-pressure and large valve size applications.
- Screwed: Normally used in small size valves, this is the simplest type of bonnet construction.
- Pressure sealed: As pressure within the valve increases, the body-bonnet joint seal increases. This type is used typically for high-pressure applications above 100 bar.
Rising vs non-rising stem
- Rising stem: The stem moves up or down as the valve opens or closes.
- Non-rising stem: The stem remains within the valve as the valve opens or closes.
Advantages vs disadvantages chart
There are many materials available for plug and gate valves, so finding the right material for an application is possible. Learn more by reading our chemical resistance guide!
Tbale 1: Plug valve vs gate valve
Plug valve | Gate valve | |
Installation space | Requires less space but has a long handle relative to valve size that must be considered | Requires more space, particularly space above for rising stem valves |
Response time | Quarter-turn valve, faster | Multi-turn valve, slower |
Operation frequency | Designed for more cycles | Designed for infrequent cycles |
Leakage | Can provide a bubble-tight shutoff | Strong sealing capabilities except for low-pressure systems |
Corrosion/Wear | Less corrosion and wear on the stem because it doesn’t sit in the flow path. May cause water hammer if incorrectly operated. | The stem sits in the flow path and will experience more corrosion and wear |
Pressure | Excellent design for low-pressure systems | More suitable for high-pressure systems and may leak if used in low-pressure systems |
Temperature | Lubricated plug valves are more suitable for high-temperature applications than non-lubricated plug valves | Suitable for higher temperature systems but check with the manufacturer as too high of temperatures may warp the valve body, which will cause the disc and seats to become unaligned |
Flow control | Provides on/off functionality and diamond opening plug valves can throttle flow | Can only provide on/off functionality. Throttling flow will damage the valve. |
Flow restriction/Pressure drop | Plug valves with restricted openings cause some pressure drop, full-bore plug valves are available | Full-bore valve, pressure drop is insignificant |
Flow capacity | Lower | Higher |
Flow direction | Bidirectional and multiport | Bidirectional |
Power requirement | Higher under high pressure | Lower under high pressure |
Torque | High, especially under high pressure | Low |
FAQs
Is a plug valve full bore?
A plug valve’s plug opening can be full bore but is also available in reduced flow for applications where pressure drop is not a large concern.
What is the difference between a gate valve and a plug valve?
A big difference between a gate and plug valve is that a gate valve is multiturn, and a plug valve is quarter-turn. So a plug valve can be opened or closed faster than a gate valve.