Well Foot Valve
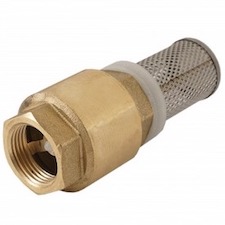
Figure 1: Brass foot valve
A well foot valve is a key component in any well pumping system because it helps prevent damage to the pump and keeps it primed. A non-primed pump can quickly overheat and break. Installed on the intake of the suction line, the foot valve stops water from flowing back into the well, thus keeping the pump primed. This article discusses the operating principle, design, and installation of well foot valves
Table of contents
- Well foot valve operating principle
- Well foot valve design
- Well foot valve flow systems
- Materials
- Well foot valve installation
- Well foot valve issues
- Well foot valve maintenance
- Well foot valve applications
- Well foot valve advantages
- FAQs
View our online selection of check valves!
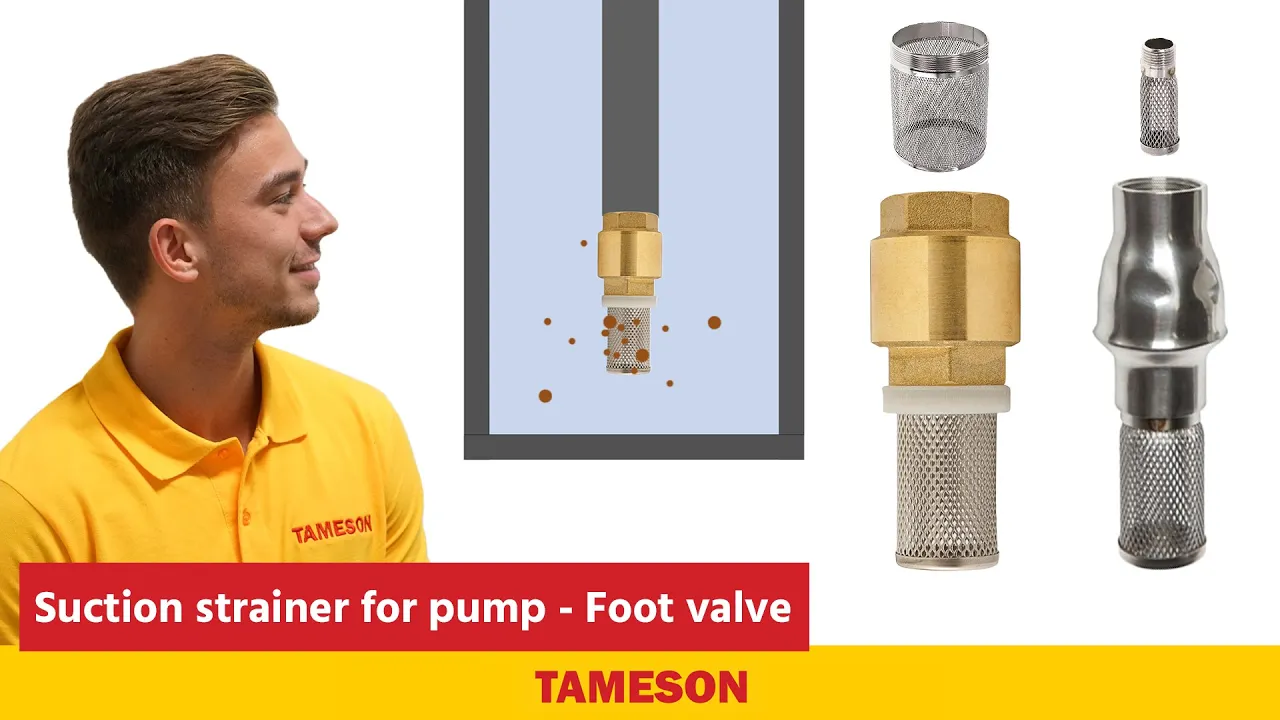
Well foot valve operating principle
A foot valve operates similarly to a check valve: it allows media to flow in a single direction by closing if backflow occurs. When the well pump turns on, water in the suction line moves towards the pump, creating a vacuum at the outlet of the foot valve. The vacuum creates a suction, pulling water from the well, through the valve, and towards the pump. When the pump turns off, the water in the suction line reverses direction and begins falling back towards the foot valve. The pressure from the backflow closes the foot valve and stops the column of water from reentering the well.
A well foot valve’s key feature is the strainer installed on its inlet port. This strainer prevents large debris from entering the valve and sticking it open or damaging it.
Figure 2 illustrates a generalized well pump system. Note that the check valves (Figure 2 labeled B) are unnecessary for systems shallower than 8 meters. Deeper well systems use check valves to relieve pressure on the foot valve when the pump is not running.
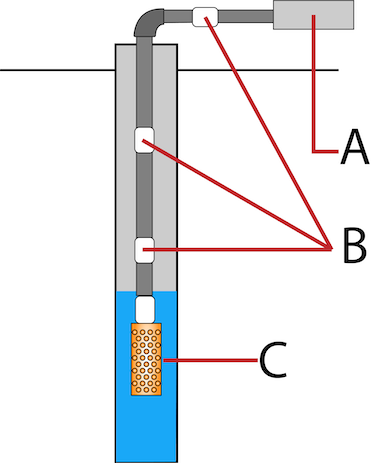
Figure 2: A generalized well pump system: pump (A), check valve (B), well casing (C), and foot valve (D).
Well foot valve design
There are five types of foot valves: ball type (with or without a spring), flapper type, membrane type, and spring type.
- Ball type with spring: A spherical ball is held on the valve seat by a spring when the valve is closed. This type of foot valve is optimal for viscous and sewage media.
- Ball type without spring: As seen in Figure 2, a ball rests on an o-ring seat (Figure 2 labeled A). Flow through the valve (Figure 2 labeled B) pushes the ball off the seat and into a side chamber (Figure 2 labeled C). When flow reduces, the ball falls back towards the seat. This valve is suitable for low-pressure applications.
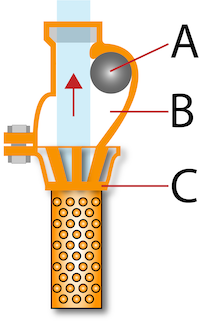
Figure 3: Ball foot valve: inclined chamber (A), o-ring seat (B), and ball (C).
- Flapper type: A flat, hinged disc rests on the valve seat. When the pump turns on, and pressure in the suction line reduces, flow through the valve pushes the disc open. When the pump turns off, backflow shuts the valve. The correct operation of this valve is gravity-dependent, so installation is not possible in any orientation.
- Membrane type: As seen in figure 3, a rubber membrane sits inside the valve’s strainer, blocking water from entering. When the pump operates and suction occurs, the membrane is displaced, allowing the liquid to flow through the valve. When suction stops, the membrane regains its original position, closing the valve.
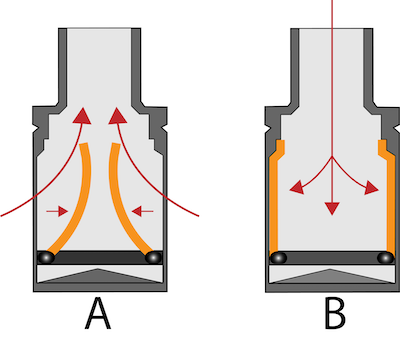
Figure 4: Membrane foot valve. The membrane displaces to let water in (A) and closes during reverse flow (B).
- Spring type: This type of foot valve has a spring and poppet. When the valve is closed, the spring holds the poppet against the valve seat. Installation is possible in any orientation.
Strainer
A foot valve has a strainer, also called a filter or screen, installed on its inlet side. The strainer stops large debris in the well from entering the valve and sticking it open. Depending on the potential debris within the well, the strainer material and opening size can be specified per the application to ensure proper filtering.
Connection types
There are two common connection types used with foot valves: threaded and flanged.
- Threaded: A significant difference between foot valves and check valves is that foot valves have threading only on the outlet side. The inlet side has a screen. There are three thread types. Learn more about each type by reading our thread design article.
- Female: Threaded on the inside to connect with piping that has threading on the outside.
- Male: Threaded on the outside to connect with piping that has threading on the inside.
- Dual: Threading on the inside and outside to connect with any piping threading type.
- Flanged: Flanged connections are more suitable for industrial, high-pressure applications. Two common classes for foot valves are ANSI 125 and 150.
- ANSI 125: Cast iron flanges rated for 125 psi at 353 °F (8.6 bar at 178 °C).
- ANSI 150: Ductile iron, steel, or stainless steel flanges rated for approximately 150 psi at 600 °F (10.3 bar at 315 °C).
Well foot valve flow systems
Foot valves have three flow systems, each with its own applicability to specific application requirements.
Microflow system foot valves
Microflow system foot valves are used in micro-wells involving direct push technology (a subsurface soil investigation procedure). These valves are mostly made of stainless steel and consist of either FEP (Florotherm) or HDPE (High-density polyethylene) tubing.
High flow system foot valves
High flow system foot valves are designed to withstand high pumping rates and deep wells. These valves are generally used on 2-inch diameter wells or larger.
Low flow system foot valves
Low flow system foot valves are used in small diameter piezometers that lift up to 100 feet of water.
Materials
A foot valve remains submerged in water for the duration of its lifetime. Therefore, the material chosen needs to be rust and corrosion-resistant. Common materials for foot valves are heavy-duty cast iron, stainless steel, bronze, and PVC.
Metal materials are more suitable for high-pressure applications. PVC, however, has internal pressure ratings up to 84 bar (1218 psi). PVC is also non-corrosive, so if an application’s system pressure is within the PVC foot valve’s pressure rating, PVC is preferable. Read our chemical resistance guide for more information.
Well foot valve installation
Foot valves are appropriate for shallow and deep wells, whether using a one- or two-line jet pump (Figure 2). Also, submersible pumps use check valves.
Before installing a well foot valve:
- Ensure that the foot valve is the correct size for flow conditions, not pipe size. Typically, foot valves work best at flow rates lower than 1.5 meters per second. Greater velocities can lead to cavitation of the foot valve and early failure.
- Take the entire system’s pressure into consideration, not just the pump’s pressure setting.
- Clean out built-up sediment. Shoot high-pressure water into the bottom of the well to push sediment up and out of the well. Wait for the water coming out of the well to be clear.
- Ensure the inside portion of the foot valve is clear of foreign objects such as metal chips, welding slag, and pipe scale. These can prohibit disc movement and damage the disc or seating.
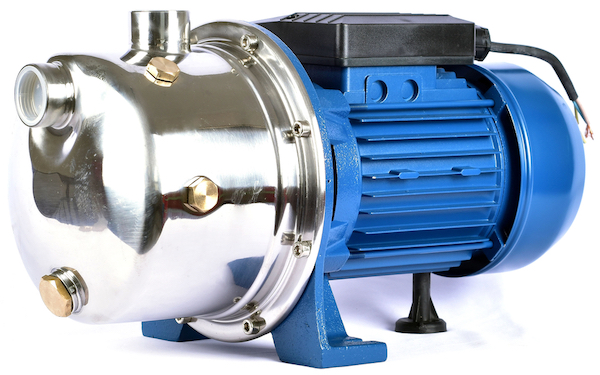
Figure 5: A jet pump.
During the installation of the well foot valve:
- Ensure the arrow on the valve faces towards water flow (up).
- Install the foot valve in a vertical position.
- For shallow wells, the foot valve should be at most 25 vertical feet (7.6 meters) below the pump’s inlet.
- For deep wells that use a submersible pump, ensure to install check valves to alleviate stress on the foot valve. The first check valve should be approximately 6 meters from the pump. After that, install a check valve every 60 meters of piping.
- Ensure the screen is not at the bottom of the well but instead is 3 to 6 meters below the minimum pumping level (the level the water drops to while the pump is operating).
Well foot valve issues
Loss of water pressure from a pump does not necessarily mean an issue with the foot valve. It’s also possible that there is damage to the piping between the valve and the pump that is also letting air into the suction. However, since all components are underground, dealing with these issues will require pulling up the piping and foot valve.
Foot valves have three common issues: wire drawing, disc flutter, and sediment buildup in the screen. The first two issues require foot valve repair, but the third is fixable without pulling up the piping. Therefore, trying to solve the issue of sediment buildup may be the best first step to take.
Wire drawing
Wire drawing occurs when high-velocity water or sediment flows past a rubber valve seat. Over time, a groove carves into the seat. When the valve closes, the groove remains, and small flows escape the valve, causing pressure creep (increase in outlet pressure). Alleviate pressure creep by running a faucet connected to the well. However, more significant issues can occur in systems that do not often run. To avoid wire drawing:
- Use a stainless steel seat.
- Choose the smallest foot valve possible to handle the media flow through the system. Smaller valves open more widely, keeping the sediment away from the seat and reducing flow velocity through the valve.
Disc flutter
Disc flutter occurs when a foot valve is used at a small portion of its full capacity which causes excessive wear over time. This issue can also be mitigated by carefully selecting the smallest valve possible to handle the media flow.
Sediment buildup on screen
Surging the well is a standard method to prevent excessive sediment buildup in the foot valve screen. Using a surge block or a bailer are two preemptive measures to take.
- Surge block: A surge block fits like a sleeve over the foot valve and is shaped somewhat like a donut. The surge block reduces the distance between the valve and the well casing. Then, the well piping can be moved up and down like a plunger several times. Downward strokes are easier to accomplish because some of the water is going into the piping. Over time, this action may shake loose some or all of the sediment on the screen.
- Bailer: A bailer is a check valve that is plunged into a well to collect water and sediment, then brought back up to empty. This process takes a long time to develop the well but ultimately will remove a lot of sediment from the location where the foot valve will be.
- Compressed air: A third method is possible when the foot valve is already in the well. Compressed air is pumped into the well to raise the water level. When the water level reaches the top of the well casing, the air is turned off to allow the water level to drop quickly. This action may shake loose some sediment from the foot valve but is not as reliable as using a surge block.
Well foot valve maintenance
After lifting a foot valve out of a well, take the opportunity to disassemble it and determine if anything inside of the valve is repairable. However, before disassembling the valve, determine whether or not the manufacturer will void the valve’s warranty if it is taken apart.
Disassembling a foot valve is a simple process. First, remove the screen and seat, and then remove the disc. Once the disc is removed:
- Examine the inside of the valve for cleanliness.
- Remove scale buildup on the stem and stem guide using white vinegar.
- Ensure there is no elliptical wear on the stem or guides. If there is, replace either or both.
- Ensure the flow passage is free and clear.
Well foot valve applications
Beyond water wells, foot valves are suitable for lakes, rivers, ponds, and other bodies of water. However, in non-well applications, construct a valve stand so that the foot valve doesn’t rest on the bottom. Industrial sump pumps, river and lake intake pumps, and pneumatic brake lines of commercial trucks also use foot valves.
Well foot valve advantages
Some argue that a foot valve is unnecessary for shallow wells (shallower than 4 meters). Non-primed pumps may be able to create a suction and pull up approximately 2-4 meters of water from the well. This can get water into the pump before 45 seconds, which is the amount of time most pumps can run dry without causing damage.
Foot valves cannot completely protect a pump from damage because they are not the only component of the system that can fail. However, well foot valves are simple to install and add an extra layer of protection against air entering the piping, which can cause cavitation.
FAQs
Do you need a foot valve for a well?
Wells deeper than 4 meters require a foot valve to keep the pump primed. Running a dry pump can quickly damage it. Foot valves are also recommended for shallow wells.
How do you check if a foot valve is working?
It’s difficult to tell if a foot valve works because it cannot be seen without pulling it out. However, if the well pump is not staying primed, there is likely an issue with the piping or the foot valve and both should be seen to.
What’s the difference between a foot valve and a check valve?
A check valve is threaded on both sides and a foot valve is threaded on one side, with a screen on the other.