Valves For High Viscosity Fluid
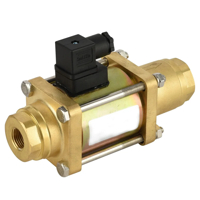
Figure 1: Coaxial solenoid valve suitable for highly viscous fluids
In industrial processes involving high viscosity media, like thick liquids or pastes, valves encounter several challenges affecting their reliability and effectiveness. Therefore, it is important to carefully select a valve for its performance to achieve efficient and precise flow control. This article explores the issues that arise when using valves with viscous media and how to select valves for these media.
Table of contents
- Viscous media for valves
- Selecting the right valve for viscous fluid service
- Valves for high viscosity fluids
View our online selection of valves suitable for high viscosity fluids!
Viscous media for valves
Valves handling viscous media face several challenges due to the thick and sticky nature of the fluid.
- Viscous media's increased friction and resistance make it harder for the valve to open and close smoothly. This can lead to slower response times and reduced accuracy in flow control.
- Viscous media may cause clogging, leading to valve malfunctions and maintenance problems.
- The high pressure drops (caused by the resistance encountered by the thick fluid as it flows through the narrow passages and restrictions within the valve) across the valve can cause energy losses and decreased system efficiency.
Proper valve design, material selection, and regular maintenance are crucial to reduce these issues and ensure reliable performance in applications dealing with viscous fluids.
Selecting the right valve for viscous fluid service
The Cv, Kv, and viscosity correction factors (Fv) help choose the right valve size and type for high viscosity media.
- A valve's flow coefficient (Cv or Kv) measures its efficiency in allowing fluid flow, which depends on the valve's size and type.
- Fluid viscosity is crucial in pressure drops for semi-turbulent or laminar fluid flow. Fluid viscosity affects the pressure drop differently in laminar and turbulent flow regimes.
- In laminar flow, higher viscosity leads to increased pressure drop, while in turbulent flow, the impact of viscosity is less significant.
- In turbulent flow, the irregular mixing reduces the impact of viscosity, making pressure drop less dependent on viscosity and more influenced by other factors like the Reynolds number.
- Viscosity correction factors (a way of adjusting the Cv to account for the thickness of the fluid) are used to size the valve accurately.
Increasing the orifice size is one way to address the flow coefficient for viscous fluids. But, it can cause drawbacks like higher costs, increased particle retention (the bigger orifice might trap particles present in the fluid), and velocity losses. The ideal approach is to choose the correct valve type and size to ensure sufficient flow and minimize other effects like pressure drops.
Valves for high-viscosity fluids
It's crucial to consider several parameters while selecting a valve for highly viscous media.
Level of contaminants
It is crucial to first evaluate the level of contaminants in the fluid before selecting a valve type. A choke valve is suitable for contaminated viscous fluids. The hierarchy for the suitability of valves according to the level of contaminants in the media is as follows:
- High: A choke valve is highly suitable for contaminated viscous fluids. Choke valves are designed to handle highly contaminated fluids and can effectively manage the erosion caused by such fluids. They control the flow rate of fluids in pipelines, especially in the oil and gas industry, and are robust enough to handle high pressures and temperatures.
- Medium: Diaphragm valves are suitable for fluids with a medium level of contaminants. These valves are used for throttling purposes and to control the fluid flow. They provide better shut-off than gate valves and are often used in applications where flow needs to be regulated, and leakage needs to be minimized.
-
Low:
- Ball valves: Ball valves are preferred for controlling viscous fluids in industrial and oil and gas operations due to their excellent flow coefficients and minimal pressure drops. They have smooth flow paths and reliable sealing characteristics throughout their service life, with pressure drops occurring between the ball and the seat.
- Diaphragm valves: Diaphragm valves have good flow coefficients but rank lower than ball valves. These valves limit contamination and particle accumulation around the valve body, making them common in high-purity fluid applications. They offer rapid shut-off, precise actuation, and cleanliness.
- Butterfly valve: Butterfly valves are suitable for low-contaminant fluids and are commonly used in large pipe diameters. They regulate fluid flowing through a section of the pipeline and have a simple structure, which makes them cost-effective.
Pressure recovery factor and flashing
High-viscosity fluids have higher flow resistance and therefore experience a significant pressure drop when passing through a valve. When a fluid passes through a valve, its pressure decreases at the vena contracta (the point of maximum constriction) and then recovers downstream (Figure 2). The pressure recovery factor measures the potential for pressure recovery after the fluid passes through a valve (Figure 3).
A high pressure recovery factor indicates that the pressure recovers significantly, which could lead to cavitation and flashing if the pressure drops below the fluid's vapor pressure.
- The design and style of the valve can affect its pressure recovery factor. For example, globe and angle valves generally have higher recovery factors than gate or ball valves. This is because these valves have a greater pressure drop and more turbulent flow paths in globe and angle valves.
- Globe valves perform better than butterfly valves in distributing pressure losses. Globe valves have multiple constriction points that evenly distribute a system's pressure drops. On the other hand, butterfly valves experience pressure drops at limited constriction points between the valve body and disc, resulting in lower pressure recovery and making them unsuitable for conveying viscous fluids with lower vapor pressure limits.
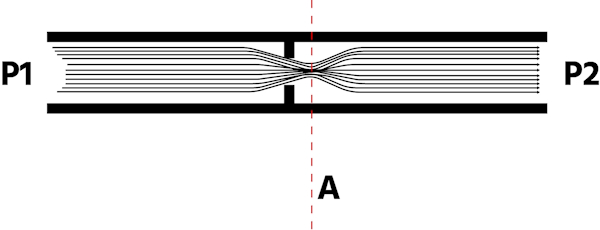
Figure 2: Fluid pressure variation through a valve showing vena contracta (A). Inlet pressure is P1, and outlet pressure is P2.
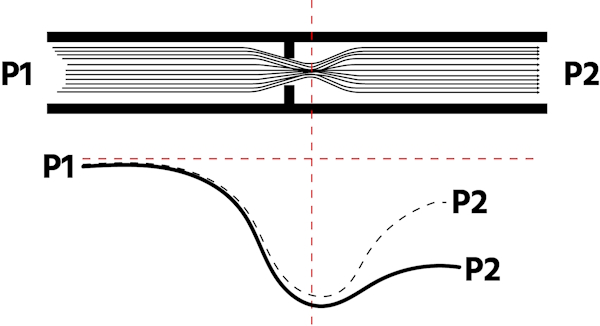
Figure 3: Fluid pressure recovery through a valve. A fluid's pressure recovery along the dashed line is better than that of a fluid along the solid line.
Precision
Precision in valve flow means adjusting the flow rate, pressure, or direction of the fluid very precisely, down to very small increments, to meet specific requirements or standards. High-precision flow processes necessitate automated valves that respond effectively to flow conditions. Solenoid valves work well for fluid flow processes requiring the highest levels of precision. Coaxial solenoid valves (Figure 1) are engineered to handle viscous and contaminated media, even under high pressures or temperatures. The inlet and outlet ports are opposite, creating an almost linear flow path. Read our article on fluid viscosity for more details.