Understanding and Preventing Swing Check Valve Failure

Figure 1: Swing check valves require regular maintenance to ensure they are working properly
Swing check valve failure can cause major problems in fluid systems, as these valves are key to allowing flow in one direction and stopping backflow. Failures often happen due to worn-out parts, debris buildup, incorrect installation, or material fatigue. Regular maintenance and inspections can help prevent these issues and improve system reliability. By understanding these common failure causes and taking preventive steps, you can keep the system running smoothly for longer.
View our online selection of check valves!
Common causes of swing check valve failure
Common causes of swing check valve failure are:
- Wear and tear: Regular use can cause the internal parts of a swing check valve to wear out, leading to leaks and reduced efficiency, so they should be checked and replaced as needed.
- Incorrect installation: Incorrect installation of swing check valves, such as improper direction or loose connections, can lead to misalignment, early failure, or poor performance.
- Debris and corrosion:Debris and rust can damage swing check valves by blocking movement and weakening the valve, so using filters and corrosion-resistant materials can help prevent these issues.
-
Pressure and flow issues
- Pressure surge: Sudden pressure changes, such as water hammer, can damage swing check valves by causing rapid opening and closing, but using surge protection devices and proper system design can mitigate these risks.
- Low flow velocity: If the flow velocity is below the minimum required, the valve disc may not stay fully open, leading to chattering and excessive vibration.
- Flow disturbances: Non-uniform or turbulent flow caused by improper upstream or downstream piping can lead to chattering and noise.
-
Material and design selection
- Wrong selection of disc material: Using materials with low impact strength, such as martensitic stainless steel (CA15), can lead to fatigue failure in dynamic loading conditions.
- Disc slamming: Incorrect valve type or size can cause pressure pulsations and rapid disc closure, leading to slamming.
- Disc tapping: Oversized valves with low flow velocity can cause the disc to tap against the seat, especially in gas applications with fluctuating flow.
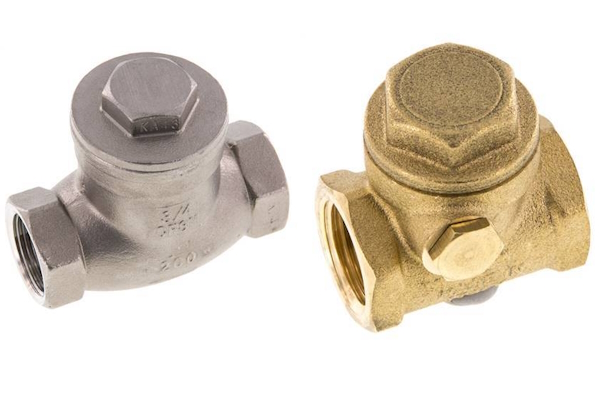
Figure 2: Determine if the system needs a robust material like stainless steel (left) or a more cost-effective material like brass (right).
How to reduce swing check valve failures
Selection and sizing
- Selecting swing check valve sizes: Ensure the valve is appropriately sized to match the flow requirements. A valve that is too small can restrict flow, while one that is too large may not close properly. Choose materials that are compatible with the fluid and operating conditions to enhance durability and performance.
- Choosing the right valve type and size: Select a valve type with a shorter travel distance, like a tilting disc check valve, to prevent slamming. Ensure the valve is correctly sized to avoid disc tapping.
- Selecting appropriate disc material: Use materials with high fatigue resistance and ductility, such as carbon steel, for applications with dynamic loading.
Installation
- Proper installation guidelines: Follow the manufacturer's instructions carefully to avoid misalignment and loose connections. Ensure the valve is installed in the correct orientation and all connections are secure. Read our check valve installation article for more details.
- Maintaining proper piping layout: Ensure a minimum straight pipe length of 5D upstream and 10D downstream to promote uniform flow and reduce turbulence.
Operation and performance
- Ensuring adequate flow velocity: Size the valve to maintain a flow velocity above the minimum required (VMin) to keep the disc fully open. For systems with variable flow, ensure the disc opening angle is greater than 25% at minimum flow.
- Addressing swing check valve chattering: Investigate and resolve causes of chattering, such as pressure fluctuations or incorrect valve sizing. Consider installing dampeners or adjusting system settings to mitigate chattering.
Maintenance
- Routine maintenance and inspection: Conduct regular maintenance and inspections to identify and address issues early. Check for signs of wear, rust, and debris build-up to maintain optimal valve performance.
- Importance of cleaning and lubrication: Keep the valve clean to prevent blockages and ensure smooth operation. Regularly lubricate the valve to reduce friction and extend its lifespan.
- Regular monitoring and maintenance: Regularly inspect and maintain valves, especially in critical services, to detect wear and prevent mechanical failure.
FAQs
What causes swing check valve chattering?
Chattering is often caused by pressure fluctuations, improper sizing, or debris in the valve. Addressing these issues can help eliminate chattering.
How can I prevent swing check valve failure?
Regular maintenance, proper installation, and selecting the right size and material are key to preventing failure.
What are the benefits of using a full flow swing type check valve?
Full flow swing type check valves offer reduced pressure drop, increased efficiency, and are suitable for high flow applications.