Stainless Steel, Brass, Aluminum, & Plastic Camlock Couplings

Figure 1: Stainless steel (top left), brass (top right), aluminum (bottom left), and plastic (bottom right) camlock couplings
Common camlock fitting materials are stainless steel, aluminum, brass, and plastics like polypropylene. Each material offers distinct properties that suit specific applications and industry requirements.
- Stainless steel is ideal for long-term use in demanding high-pressure applications.
- Brass is durable, has good corrosion resistance, and is less costly than stainless steel.
- Aluminum is lightweight, budget-friendly, and strong.
- Plastic is lightweight, cost-effective, and chemically resistant, ideal for low-pressure applications involving corrosive substances.
This article explores the main features and limitations of camlock coupling materials like stainless steel, brass, aluminum, and plastic. Read our camlock fitting overview article for more information on the working, types, and selection criteria for camlock fittings.
Table of contents
- Stainless steel camlock fittings
- Brass camlock couplings
- Aluminum camlock couplings
- Plastic camlock couplings
- Temperature tolerance
- Pressure rating
- FAQs
View our online selection of camlock couplings!
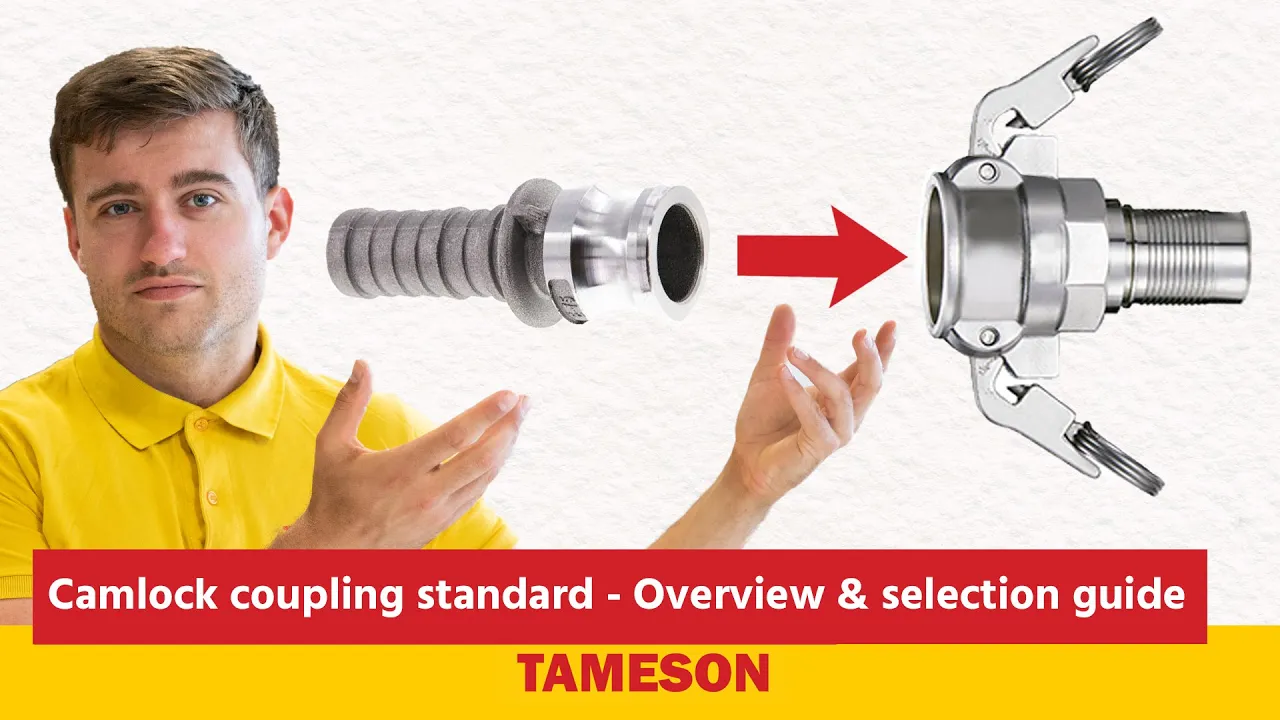
Stainless steel camlock fittings
Key features
- Strength: Stainless steel camlock fittings are ideal for high-pressure applications with significant stress.
- Corrosion resistance: Stainless steel has excellent corrosion resistance to water, moisture, acids, chlorides, and organic chemicals.
- Applications: Commonly used in the food, marine, chemical, and pharmaceutical industries due to their durability and resistance to corrosive substances.
Considerations
- Cost: Stainless steel fittings are generally more expensive due to higher material and production costs, but they offer long-term value through durability and performance.
- Malleability: Less malleable than aluminum, making it harder to customize.
Brass camlock couplings
Key features
- Corrosion resistance: Brass is highly resistant to corrosion, particularly against salt water, hydraulic oil, and coolants.
- Non-sparking: Brass is non-sparking and suitable for environments where sparks pose a hazard.
- Cost: Brass is less expensive than stainless steel and balances cost and performance.
- Applications: Agriculture, firefighting, oil and gas, and chemical processing.
Considerations
- Durability: While corrosion-resistant, brass is less durable than stainless steel in highly abrasive or high-pressure environments.
- Weight: Brass is heavier than aluminum, which could be a factor in applications where minimizing weight is essential.
Aluminum camlock couplings
Key features
- Lightweight: Aluminum is lightweight, making these fittings easy to handle and install.
- Cost: More cost-effective than stainless steel, making them suitable for budget-conscious, short-term applications.
- Applications: General industrial applications and use cases with fresh water mixtures.
Considerations
- Strength: While strong, aluminum is less robust than stainless steel, making it less suitable for high-pressure applications with vibrations.
- Corrosion resistance: Aluminum is corrosion-resistant due to a natural oxide layer that protects it from rust, making it a reliable choice for many applications. However, this layer only protects against certain types of corrosion, so it's essential to ensure aluminum camlock fittings are compatible with the specific environmental conditions they will encounter.
Plastic camlock couplings
Key features
- Material: Made from polypropylene, offering excellent chemical resistance.
- Ease of use: Lightweight, quick, and secure connections with cam lever arms.
- Versatility: Compatible with various hoses and pipes, including rubber and PVC.
- Applications: Ideal for agriculture, chemical processing, and water management.
Considerations
- Pressure and temperature limits: Suitable for low-pressure applications, always adhere to the manufacturer's specified pressure and temperature ratings.
- Durability: Plastic is not as durable as metal. Consider resistance to UV exposure and abrasion for long-term use.
Temperature tolerance
The seal typically determines a camlock coupling's temperature rating. Plastic camlock fittings may be an exception, as they may not be suitable for high temperatures. The coupling's metal components are generally more heat-resistant and can withstand higher temperatures than the gaskets. NBR and EPDM are the common seal materials for camlock couplings, and they can operate up to 80 𐩑C (176 𐩑F).
Pressure rating
The working pressure of a camlock coupling is primarily influenced by the coupling material and the operating temperature. Aluminum may not be suitable for extremely high pressure applications, while stainless steel can withstand high pressures.
Temperature and pressure derating
Camlock couplings are rated for working pressure at ambient temperature (20 𐩑C/68 𐩑F), but their maximum safe working pressure decreases as temperature increases. This is due to changes in material properties at elevated temperatures, affecting the coupling's strength and integrity.
Each material has a specific temperature derating factor for accurate pressure ratings at higher temperatures. For example, stainless steel retains a higher percentage of its rated pressure at elevated temperatures than aluminum or polypropylene. Before installing camlock couplings, evaluate the working environment, including temperature and fluid type, to ensure optimal material choice and safety.
FAQs
What material is a camlock?
Camlock fittings can be made from various materials, including stainless steel, aluminum, brass, and plastics like polypropylene. Each material is chosen for its specific properties suited to different applications.
What is the pressure rating of an aluminum camlock?
The pressure rating of aluminum camlock fittings typically ranges from 5 to 18 bar (72 to 261 psi) at standard temperature, depending on their size and specific design.