What Causes a Solenoid Coil To Burn Out
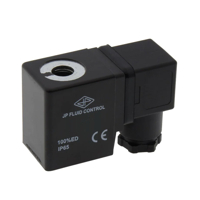
Figure 1: 24V DC solenoid valve coil
Solenoid coil burnout is an issue that can lead to system failures and costly repairs, significantly affecting the life expectancy of solenoid valves. Solenoid valves are essential for controlling fluid flow in various applications, but their coils are susceptible to damage. Identifying the factors that contribute to coil burnout is crucial for effective maintenance and prevention. This article explores the primary reasons behind solenoid valve coil burnout and offers solutions for reducing these risks.
View our online selection of solenoid valves!
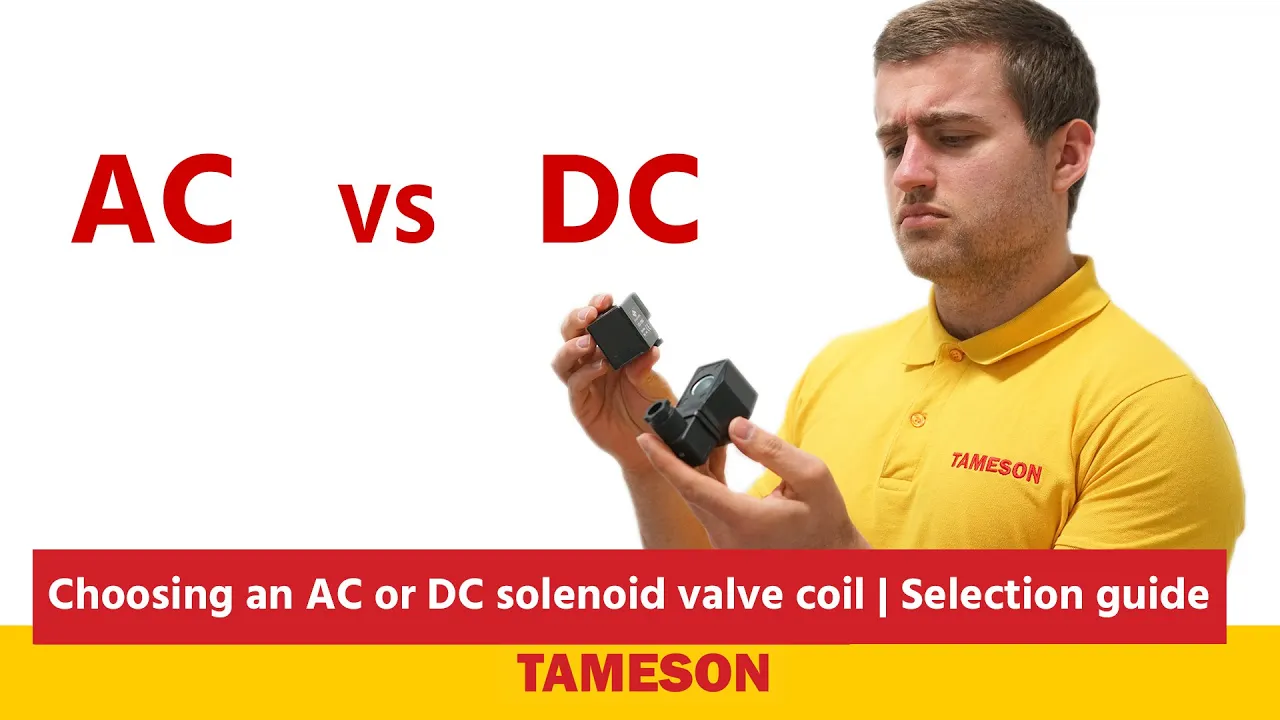
Key causes of solenoid coil burnout
Burnout occurs more frequently in solenoid valves with AC coils because they experience a high inrush current, which can be up to five times higher than the normal operating current. This high current continues until the solenoid armature closes the air gap. The inrush current in DC solenoid valves is similar to the holding current, making them less likely to burn out.
Voltage issues
One of the most common causes of solenoid coil burnout is improper voltage supply. Both overvoltage and undervoltage conditions can be harmful to the coil.
- Over voltage: Supplying a voltage higher than the coil's rated voltage can cause excessive current flow, leading to overheating and eventual burnout.
- Under voltage: Conversely, supplying a voltage lower than the rated voltage can prevent the solenoid from fully engaging, causing it to draw inrush current continuously, which can also lead to overheating.
To check for low voltage, use a multimeter to measure the voltage directly on the coil wires while the solenoid is powered and its armature is held open. Briefly energize the solenoid to take this reading. Then, take another reading with the solenoid disconnected from the power source. If the difference between these two readings exceeds 5%, it indicates excessive resistance in the wiring or an undersized control transformer. Read our solenoid valve voltage article for more information on how the application of different voltages affect the operation of a solenoid valve coil.
High inrush current
AC solenoid valves are particularly susceptible to burnout due to high inrush current, which can be up to five times higher than the normal operating current. This high current persists until the solenoid armature closes the air gap. In contrast, DC solenoids have inrush currents similar to their holding currents, making them less prone to this issue.
Rapid cycling
Frequent cycling of solenoid valves can lead to overheating, especially in AC coils. High cycling rates generate excessive heat that cannot dissipate quickly enough, damaging the coil insulation. For applications requiring frequent cycling, consider using oil-immersed solenoid structures. The oil helps dissipate heat more effectively, maintaining a lower operating temperature.
Electrical transients
If the current for the solenoid valves is drawn directly from a power line that also supplies large inductive devices like electric motors, switching these motors can generate high voltage transients that may damage the insulation of the solenoid valve coils. To protect against this, install a thyrector (Figure 2 labeled A) across each coil to effectively short-circuit these transients.
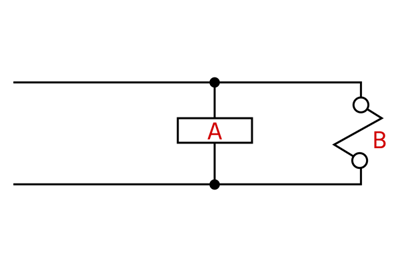
Figure 2: Connecting a thyrector (A) directly across the coil (B) of a solenoid valve
Contaminants and environmental factors
Dirt, oil, and other contaminants can cause mechanical issues that lead to coil burnout. For example, particles can lodge under the solenoid armature, preventing it from fully seating and causing the coil to draw excessive current. Ensure that solenoid dust covers are securely in place to protect against airborne contaminants. Regularly clean and maintain the system to prevent the buildup of dirt and varnish in the oil.
Environmental conditions such as extreme temperatures and high humidity can also affect solenoid performance.
- High temperature: Excessive heat can damage coil insulation. Use heat shields or high-temperature-rated solenoids to mitigate this risk.
- Low temperature: Cold environments can increase oil viscosity, potentially overloading the solenoid. Use oil suitable for low temperatures or opt for oil-immersed solenoids.
- Humidity: High humidity can cause corrosion and electrical shorts. Use molded coils or oil-immersed solenoids and ensure protective covers are tightly sealed.
Additional considerations for DC solenoids
While AC solenoids are more common, DC solenoids offer specific advantages in certain applications.
- Consistent inrush current: DC solenoids have inrush currents similar to their holding currents, reducing the risk of burnout.
- High cycling capability: DC solenoids can generally handle higher cycling rates without overheating.
- Repeatability: The shifting time of DC solenoids is consistent, providing reliable performance in applications requiring precise control.
- Switch contact wear: DC solenoids can cause faster wear on switch contacts compared to AC solenoids. When the coil is disconnected, the energy stored in the coil's inductance needs to be released, which can create an arc across the switch contacts. Wiring a diode (Figure 3 labeled D) across the coil is one way to safely dissipate this energy. Ensure the positive side of the diode is connected to the positive side of the coil voltage. The diode should be rated for at least twice or thrice the DC supply voltage. Another method is to wire a capacitor (Figure 3 labeled C) across the switch contacts (Figure 3 labeled S) to absorb the dissipated energy. The optimal capacitance value can be determined through trial and error. This can be done by observing the arc intensity or by measuring the voltage spike by testing capacitors of different magnitudes.

Figure 3: Wiring a capacitor (C) across the switch contacts (S) or a diode (D) across the valve coil can help dissipate the energy stored in a solenoid valve coil (A). Either a diode or a capacitor-switch combination can be used.
Read our solenoid valve overview article for more information about the design, working, and types of solenoid valves.