Why Pneumatic Tool Oil Is Important
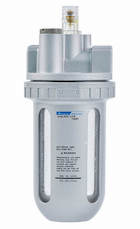
Figure 1: Air lubricator
Pneumatic tool oil lubricates and maintains pneumatic equipment. The oil reduces the friction between moving components and prevents rust buildup, o-ring breakdown, and moisture buildup within the tool. Tools driven by compressed air, such as a paint sprayer, nail gun, air hammer, or impact wrench, use pneumatic tool oil to lubricate their parts.
Table of contents
- Oil for pneumatic tools
- When to add pneumatic tool oil?
- Other equipment needed with pneumatic tool oil
- Micro fog vs oil fog lubricator
- Do all pneumatic tools need oil?
- Pneumatic tool oil selection criteria
- Common applications
- FAQs
View our online selections of lubricating oils and FRL systems!
Oil for pneumatic tools
There are different kinds of oil. Petroleum-based hydraulic fluid transfers energy from one component to another. Pneumatic tool oils, which are mineral-based or synthetic, differ from other oils. It has a low viscosity; the oil is easily atomized and transported throughout the tool by compressed air. As the oil is either synthetic or mineral-based, it does not leave behind the sticky buildup found with petroleum-based oils.
While mineral-based and synthetic oils are suitable for lubricating pneumatic systems, it may be worth using one over the other, depending on the application. For example, mineral-based oils are commonly used in small residential applications, whereas synthetic oils are used in industries. Read our lubrication guide for more details on the types and functions of lubricants.
Mineral-based pneumatic tool oil
Mineral-based oil is the most common and standard oil type. However, it is more volatile, meaning it will evaporate more quickly; this increases the total amount of oil necessary. Mineral-based pneumatic tool oil is also more reactive and tends to react with other materials and clump up, thus shortening the tool's life span.
Synthetic-based pneumatic tool oil
Synthetic-based oil is more expensive than standard oil. It has a higher performance, allowing the air tool to last up to 50% longer by reducing friction. In addition, it will not gum up inside the tools like mineral-based oil.
When to add pneumatic tool oil?
Adding pneumatic tool oil to air tools is essential in maintaining the equipment. The best way to determine the quantity of the oil is to read the pneumatic tools manufacturer's recommendations.
- Add oil to the tools at regular intervals, for example, daily or weekly.
- Another factor determining the frequency of oiling is how often the tool is used. A tool that has frequent use will require more oil. A helpful tip is to add oil throughout the day, as waiting till the end of the day may risk the tool running low on oil and eventually damaging it. Read our article on pneumatic tool oiling for more information on how and when to oil pneumatic tools.
Other equipment needed with pneumatic tool oil
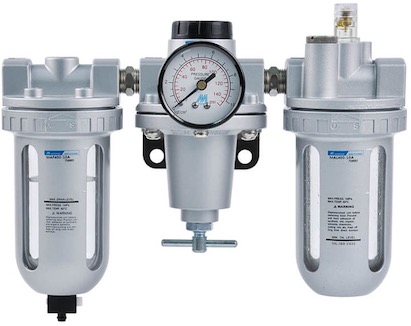
Figure 2: A filter, regulator, and lubricator unit.
The equipment necessary to add oil to the pneumatic tools can vary between tools, so refer to the user manual to confirm the oil type and quantity. Most of these products release the oil slowly. This can be helpful as having too much oil or too little oil could damage the tools.
- Toolless option: Add a few drops of oil to the tool’s air inlet, allowing the compressed air to distribute the oil.
- Oil reservoir: Certain air tools contain an oil reservoir that may need a screwdriver or hex wrenches to access.
-
Air tool oiler: An air tool oiler attaches to the air line right before the tool's air inlet. It contains air tool lubricant, distributed as air passes through the oiler. Figure 1 shows an air tool oiler.
- Note: This device is at the tool end of the air system and not at the compressor side of the system. An air system may run off of only one compressor, and different tools or components may have different oil requirements.
- Lubricator: A lubricator fits in the air line before the equipment downstream, which requires lubrication. As with the air tool oiler, it is necessary to ensure that all downstream equipment requires the same type and amount of oil. Lubricators release a controlled mist of oil into the compressed air. The drip rate (oil-fog or micro-fog) depends on the amount of oil needed for the tool.
- FRL: An FRL (Filter, Regulator, Lubricator) unit (Figure 2) lubricates the air tool like the oiler or lubricator. An FRL also contains an air filter to prevent dirt and dust from entering the tool and uses a regulator to maintain the required pressure for the tool.
Micro fog vs oil fog lubricator
A lubricator is a device in the air line that provides oil to the tool. There are two types of lubricators, an oil fog lubricator and the micro fog lubricator.
Oil fog lubricator
An oil fog lubricator is the most common type of air line lubricator. The oil fog lubricator adds oil droplets directly to the airflow. This allows relatively large droplets to pass downstream. This lubricator type is beneficial when the equipment requires more oil, such as equipment that moves slower, requires the oil to move a relatively short distance, or has a large bore.
Micro fog lubricator
In a micro fogger, the oil droplets in the reservoir atomize and sit above the oil droplets. This mist of oil moves into the airflow and heads downstream. This type of lubricator is ideal for more complex equipment, such as equipment with valves, manifolds, or air that travels a further distance due to the smaller and lighter size particles.
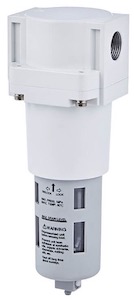
Figure 3: A micro fog lubricator
Do all pneumatic tools need oil?
Whether or not a tool needs pneumatic tool oil depends on the tool and its driving mechanism. A tool not driven by air does not need pneumatic tool oil. However, there is an exception; some pneumatic tools, such as oil-free nail guns used in wood finishing work, are manufactured to be oilless. The best way to determine if the tool needs oil is to refer to the owner's manual and check to see if your tool is oilless or not.
Pneumatic tool oil selection criteria
Selecting a pneumatic tool lubricant requires considering several factors.
- Temperature: The air tool oil should rate for use at the temperature of operation.
- Condensation: Condensation is due to the outside temperature or compressed air being heated and cooled rapidly. It is crucial to choose an oil that can handle condensation. Read our article about condensate drain valves to learn more about condensation in a pneumatic system.
-
Additives: Additives assist with improving the performance of the oil and thus protecting the equipment better. Some common additives are:
- Anti-oxidants (such as zinc dithiophosphates) that combat sludge build-up and rust prevention
- Anti-foaming agents (such as silicone polymers) that weaken the oil bubble wall causing the bubble to burst
- Mineral or synthetic: Depending on the tool’s usage frequency, it may be worth looking into these two options. If the tool is rarely used, it may be better to use mineral-based oil as it is cheaper. For tools working daily, it may be worth looking into the additional performance of synthetic base oils.
Common applications
All air-driven tools that do not operate oil-free require pneumatic tool oil for maintenance. Air tool oil is applicable in devices such as axial grinders, impact wrenches, pneumatic screwdrivers, air nail guns, pneumatic blowers, air cylinders, angle grinders, pneumatic sanders, and pneumatic rivet guns.
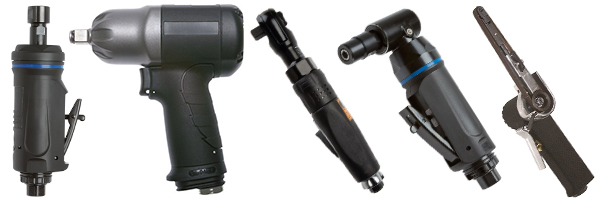
Figure 4: Pneumatic tools from left to right: axial grinder, impact wrench, pneumatic screwdriver, angle grinder, pneumatic sander
FAQs
What oil do you use to lubricate air (pneumatic) tools?
Mineral oil that contains anti-foaming and anti-gumming additives work best in air tools.
What’s the best oil for air tools?
Mineral and synthetic-based oils are considered the best oil for air tools.
Can I use WD40 as an alternative to air tool oil?
No, WD40 is not an air tool oil substitute. Pneumatic tools require oil specifically designed for these types of tools.
What is air tool oil?
An air tool oil lubricates the parts of air-powered tools and maintains them properly.