Pipe Bender
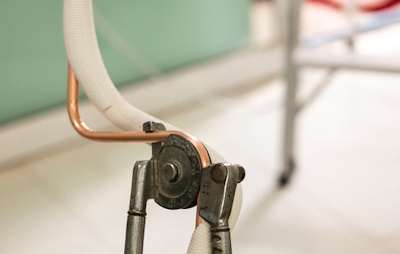
Figure 1: Copper pipe bent by a manual pipe bender
A pipe bender is designed to bend pipes and tubes into different angles and curves without compromising structural integrity. Pipe benders can be manual, electric, or hydraulic. Different pipe bending methods vary based on the machine and the primary mechanism used to achieve the bend. This article focuses on the features of manual and electric pipe benders.
Table of contents
Check out our selection of pipe and tube processing tools!
Manual pipe benders
Manual pipe benders rely on human strength and leverage. They are ideal for tasks that don't require high precision or automation, worksites without access to electrical power, or when mobility is needed. They are best suited for small-scale projects and simple bends.
How to use a manual pipe bender
- Preparation: Cut the pipe to the required length and debur the edges. Mark the points where bends are needed.
- Set up the bender: Secure the pipe in the bending device, ensuring it is level to avoid any angle offset. Select the appropriate die for the pipe size to maintain the correct bending radius and prevent kinks.
- Bending: Use the hand lever to bend the pipe to the desired angle. Slightly over-bend by one or two degrees to compensate for spring-back when the pipe is released.
- Check the bend: Remove the pipe and verify the angle with a second-angle tool. To ensure accuracy, measure the distance from the pipe's end to the bend's middle.
- Adjust for multiple bends: Consider the pipe's thickness when planning additional bends. This is crucial because bends affect the pipe's centerline, not its outer edge.
- Mark the bends: Adjust measurements for half the pipe's thickness. For example, if the pipe is 10 mm thick, add 5 mm to the measurement. So, for a second bend at 135 mm, mark it at 140 mm. Then, bend the pipe as explained in the previous steps.
- Final adjustments: If necessary, make slight adjustments to achieve the perfect angle. Use a hacksaw for any final cuts.
- Assembly check: Once all bends are complete, ensure the pipe fits perfectly into the intended connections.
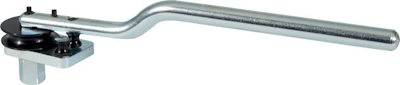
Figure 2: Manual pipe bender suitable for operation with a bench vice press
Applications
-
On-site construction and repairs:
- Ideal for construction sites without access to electrical power
- Used for making simple bends in pipes for plumbing, heating, and cooling systems
-
Small-scale projects:
- Suitable for DIY projects or small workshops where precision is not the primary concern
- Commonly used in automotive repair shops for bending exhaust pipes and other small-diameter tubing
-
Prototyping and custom fabrication:
- Helpful in creating prototypes or custom parts where flexibility and mobility are required
- Allows for quick adjustments and modifications on the spot
- Artistic and decorative metalwork: Employed in crafting metal art pieces, sculptures, and decorative elements that require simple bends
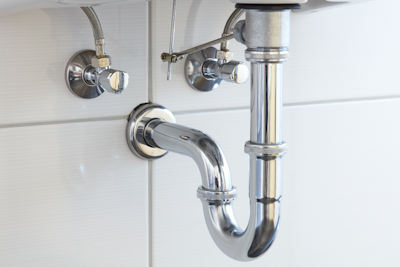
Figure 4: Bent water pipes under a sink
Electric pipe benders
Electric pipe benders use motorized systems to automate bending, ensuring consistent and accurate results with minimal effort. They can be programmed to achieve specific angles and radii and handle larger tube diameters than manual benders. Electric pipe benders are ideal for projects requiring repetitive, complex bends and are perfect for industrial operations where speed, precision, and efficiency are crucial. However, they are heavier than manual pipe benders.
How to use an electric pipe bender kit
- Setup: Place the bending set on a stable surface. Using the provided plug, ensure the device is plugged into the voltage specified by the manufacturer.
- Select components: Choose the appropriate bending segment and sliding shoe for the pipe diameter you intend to bend. Then, according to the manufacturer's instructions, attach these components to the bending set.
- Position the pipe: Insert the pipe into the bending set. Ensure it is correctly aligned with the bending segment and secured by the sliding shoe.
- Set the bending angle: Adjust the settings on the device to select the desired bending angle. The device is capable of bending up to a maximum of 180°.
- Start the bending process: Activate the bending set. The machine will automatically bend the pipe to the preset angle and then shut off once the angle is achieved.
- Remove the pipe: Once the bending process is complete and the machine has shut off, carefully remove the bent pipe from the device.
- Inspect the bend: Check the pipe to ensure the bend is as desired and free from defects or kinks.
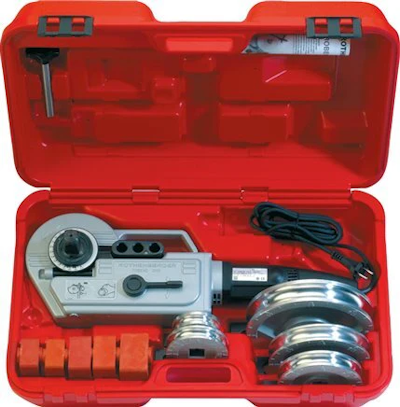
Figure 3: Electric pipe bending kit
Applications
- Industrial manufacturing: Used in manufacturing facilities to create consistent bends in large quantities of pipes
- Complex and repetitive bending tasks: Ideal for projects that require multiple, precise bends, such as in the production of furniture, frames, and structural components
- Large-scale plumbing and HVAC installations: Suitable for bending larger diameter pipes used in commercial plumbing and HVAC systems
- Automotive and aerospace industries: Used for bending fuel lines, brake lines, and other components
Selection criteria
When choosing a pipe bender, consider the following factors:
-
Tool type: Choose the right tool for the project.
- Manual pipe benders are ideal for small-scale projects, simple bends, and lightweight materials.
- Electric pipe benders are better for large-scale projects, complex bends, and heavier pipes.
-
Tool specifications: Ensure the tool specifications match the application requirements.
- Bending radius: The bending radius is the minimum radius at which a pipe can be bent without kinking. Manual pipe benders usually have bending radii of 26 mm, 29 mm, and 51.5 mm.
- Tube diameter: Choose a pipe bender that matches the diameter of the tube. Manual pipe benders are available for tube diameters of 6-8 mm, 10 mm, and 12 mm, while electric pipe benders can handle diameters up to 28 mm.
- Angle limits: Electric pipe benders allow the setting and adjustment of the bending angle within specified limits, with a maximum angle of 180 degrees. This ensures precise and consistent bends.
- Materials: Different pipe materials have different malleability and strength, which affects their bending response. Use a bender compatible with the specific material you are working with, such as steel or copper.
FAQs
What is a pipe bender, and what is it used for?
A pipe bender is a tool to bend pipes and conduits to specific angles and shapes. It's commonly used in plumbing, electrical, and construction work to fit pipes into desired layouts and spaces.
How do you choose the proper pipe conduit bender?
Choose based on the pipe material, size, and desired bend angle. Ensure the bender is compatible with the pipe's diameter and material for accurate and efficient bending.
Can you bend square tubing with a pipe bender?
Yes, you can bend square tubing with a pipe bender, but you'll need different dies and should proceed slowly. If you encounter issues, consider filling the tubing with sand to minimize wrinkling.
Why does my pipe bender machine kink the pipe?
A pipe bender may kink the pipe due to incorrect die size, improper alignment, or using a too-thin-walled pipe for the bend. Ensuring the right die size, proper alignment, and using a suitable pipe can help prevent kinking.
Can you bend a 1/2" or 3/4" pipe with a 1" pipe bend tool?
It's not recommended because the die won't fit snugly, leading to poor support and potential kinking or flattening.
What is the difference between a pipe bender and a tube bending tool?
Pipe and tube benders are similar. However, pipes are classified by wall thickness and inside diameter, and tubes are classified by outside diameter.