Hydraulic Pipe Bender

Figure 1: A hydraulic pipe bender preparing to bend brass pipe.
A hydraulic pipe bender is a device that uses hydraulic pressure to bend various metal pipes to specific angles. Hydraulic pipe benders work the same way as hydraulic car jacks and can perform multiple bends on the same pipe. Although they aren't as effective as electric pipe benders, making bends using hydraulic pipe benders takes less time and effort than manual benders. This article discusses more about what hydraulic pipe benders are, their design and operation, and compares them with other pipe benders.
Table of contents
- What is a hydraulic pipe bender?
- The basics of hydraulics
- Hydraulic pipe bender design
- Hydraulic pipe bender operation
- Hydraulic pipe bender applications
- FAQs
Check out our selection of pipe and tube processing tools!
What is a hydraulic pipe bender?
A hydraulic pipe bender requires less effort to bend pipe than manual pipe benders. It uses hydraulic pressure to bend pipes of different sizes and material types (e.g., copper and stainless steel). Hydraulic pipe benders use the ram bending method to bend pipes to specific angles. This method uses a bending die (Figure 2 labeled A), which controls the inside radius of the bend. The die presses the pipe against two stationary rollers (Figure 2 labeled B) to achieve the bend.
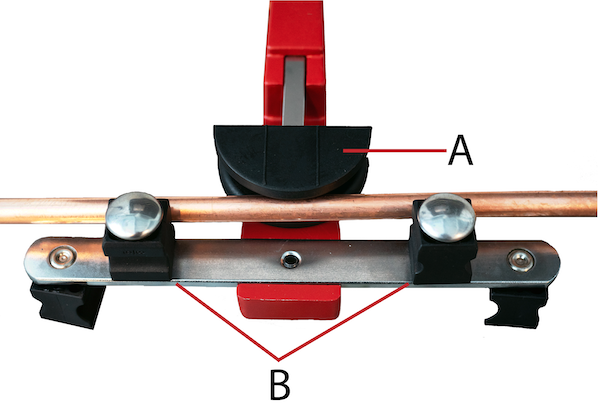
Figure 2: A black bending die (A) about to press a brass pipe into two stationary rollers (B).
The basics of hydraulics
Hydraulic machines take advantage of Pascal’s principle, which states that an increase of pressure at one point in a confined space filled with incompressible fluid will lead to an equal increase at all other points. Hydraulic machines typically use water or oil as the incompressible fluid. An example of hydraulics is if two cylinders containing pistons are filled with oil and connected to one another with a pipe, any force that one piston applies to the oil will act upon the other piston.
Multiplication factor in hydraulics
In hydraulic systems, it's possible to multiply the force on the second piston or cylinder in the above example based on Pascal's principle and the pressure definition. Pressure is the force acting per unit area. Thus, with a constant pressure value, an increase of the second piston’s surface area results in an increase of force acting upon that piston. Most hydraulic systems have valves connecting cylinders and pistons to a high-pressure oil pump. Therefore, by applying a small force on the hydraulic pipe bender's pump, a larger force is created to make bends in pipes of various sizes and materials.
Hydraulic pipe bender design
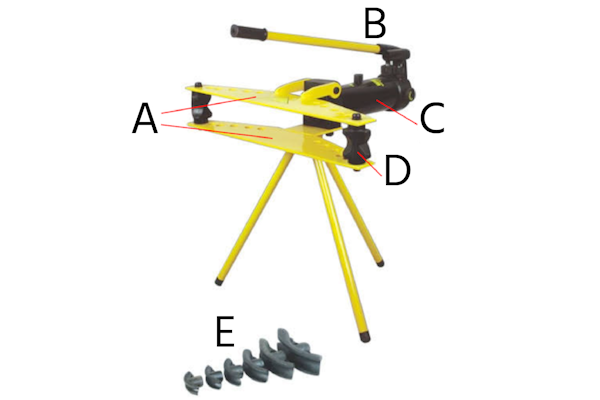
Figure 3: A hydraulic pipe bender mounted on a tripod with the following components: frame plates (A), hand pump (B), cylinder (C), pivot assembly (D), and dies (E).
Below are the components of a hydraulic pipe bender:
- Hand Pump: The pump (Figure 3 labeled B) supplies high-pressure oil to the entire cylinder through the release knob valve and the hydraulic hose. It has a handle that facilitates the opening and closing of the valve to release the oil as required. The pump has an oil filler screw for refilling or replacing the oil.
- Cylinder: Pressure, force created in the hand pump, is transmitted to the cylinder (Figure 3 labeled C) via the hydraulic hose. Given that the cylinder has a higher surface area than the pump, the force is multiplied there, making it possible to bend pipes of various sizes and materials to the required degrees.
- Plunger bracket: Not visible in Figure 3, the plunger bracket holds the bending die and moves forward as the hand pump operates.
- Frame Plates: The lower and upper frame plates (Figure 3 labeled A) have different hole sizes to hold the rollers and plunger bracket in position.
- Pivot Assembly: This is an assembly of rollers (Figure 3 labeled D) placed between the upper and lower frame plates and secured in applicable holes with pins and snap pins. The pivot assembly allows the pipe to roll through as the bending occurs, making it possible to achieve the required bending degree.
- Dies: The dies (Figure 3 labeled E) press into pipes to bend them and control the inside radius of bends.
Read our manual pipe bender article for more details on the manual pipe bender type.
Hydraulic pipe bender operation
Below is the pipe bending process using a hydraulic pipe bender:
- Make sure the bender and the work area are properly set up and free from distractions.
- Make sure the ON/OFF switch is in the OFF position.
- Select the correct die size for the pipe and measure the minimum length of pipe required on each end of the die to achieve the bend.
- Attach the die to the plunger bracket.
- Position the pivot assembly within the frame plates. As a precaution, ensure that the pivot pins go through both frames and secure them with snap pins.
- Mark the desired bend location and direction on the pipe.
- Place the pipe into the bender and align the mark with the center of the bending die.
- Support the pipe to prevent the machine from tipping over during use.
- Connect the hand pump, switch it on, and attach the cylinder with the hydraulic hose.
- Operate the pump slowly, monitoring the bend until achieving the desired bend angle.
- Don't force the pipe to bend. If it doesn't bend, stop, release the hydraulic pressure and remove it from the bender.
- When finished, turn the hydraulic pipe bender off and retract the cylinder by slowly turning the release valve knob counterclockwise. Release the left side pivot pin and the pivot assembly.
- Remove the pipe from the bender after fully retracting the cylinder plunger.
Hydraulic pipe bender precautions
There are some necessary precautions to take before and during operation of a hydraulic pipe bender:
Inspection
- Clean any dirt or grease from handles and controls for better and more stable control.
- Inspect for leaks and check the oil level.
- Check for any broken, missing, or damaged parts that could compromise the machine's safety.
- Ensure the machine and pipe are stable.
Safety guidelines
- Stand next to the cylinder on the same side as the release knob. Don't lean over the bending machine during use.
- Correctly fix the corner brackets and fully insert the pins into the frame.
- Don't insert fingers or hands in any compromising position that could cause an accident.
- Ensure the pipe's ends extend beyond the corner brackets to prevent it from slipping or falling off once it bends.
- Any groove in the cylinder means that the ram is expanding. Stop the cylinder to prevent hydraulic leakage and cylinder damage.
Hydraulic pipe bender applications
Hydraulic pipe benders are useful for various uses, such as wall returns, handrails, roll cages, car chassis, rail elbows, furniture frames, and pipeline construction and repair. They are suitable for more robust pipes like those made of iron and steel. These machines are also ideal for producing tubes and pipes that require precision.
Hydraulic pipe bender comparison
Hydraulic pipe benders are a good compromise between manual and electric pipe benders for the following reasons.
- Cost: Hydraulic pipe benders cost more than manual pipe benders but significantly less than electric pipe benders.
- Readiness: Hydraulic pipe benders need a little more time to set up than manual pipe benders. Electric pipe benders vary in set up time depending on the type.
- Material: Hydraulic pipe benders can bend steel and cast iron pipes more easily than manual pipe benders.
- Precision: Hydraulic pipe benders are more precise than manual pipe benders and less precise than electric pipe benders.
FAQs
What is a hydraulic pipe bender?
A hydraulic pipe bender is a device that uses hydraulic pressure to bend various metal pipes and conduit to specific angles.
How to choose between a hydraulic and electric pipe bender?
The choice of a pipe bending machine depends on budget, use, and requirements. A hydraulic pipe bender is ideal for small-scale uses, where high precision and quality don't matter much.