Single Ferrule vs Double Ferrule Fittings
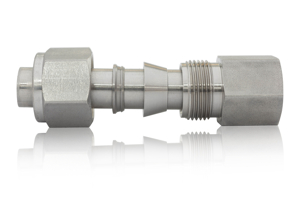
Figure 1: Arrangement of tube and double ferrule fitting
Ferrule fittings connect and seal tubes in a hydraulic or pneumatic system. They provide a strong and leak-proof connection and are crucial in applications with high pressures, vibration, and temperature changes. For a quick comparison, single ferrule fittings are typically used for low-pressure applications, less demanding environments, and they are cheaper than double ferrule fittings. Double ferrule fittings are typically used for high-pressure applications and when superior sealing performance and reusability are required. This article explores the differences between single and double ferrule fittings.
Table of contents
What are single and double ferrule fittings?
Compression fittings have three core components: a compression nut, one or two ferrules, and a body.
Single ferrule fittings
Single ferrule fittings have one ferrule (Figure 2 labeled B), which provides the sealing pressure against the fitting body (Figure 2 labeled C) and the tube. As the compression nut (Figure 2 labeled A) is tightened, the shoulder inside engages with the ferrule's back end. This results in the angled front end of the ferrule compressing into the body and securely gripping the tube.
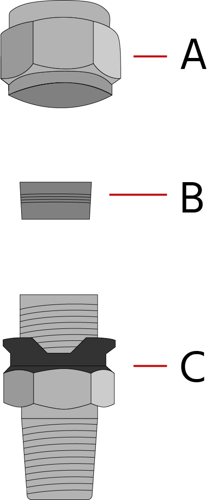
Figure 2: Single ferrule tube fitting anatomy: compression nut (A), single ferrule (B), and fitting body (C)
Double ferrule fittings
A double ferrule fitting has two ferrules.
- The front ferrule (Figure 3 labeled C) is the larger piece that sits deep in the body. The back ferrule (Figure 3 labeled B) is small and engages with the compression nut (Figure 3 labeled A).
- The softer, metal front ferrule securely seals the connection by compressing between the tube and the fitting body (Figure 3 labeled D). On the other hand, the back ferrule is equipped with a chemically-hardened lead edge, allowing it to grip the softer metal of the tubing firmly. This gripping action effectively prevents the tubing from slipping under high pressure, ensuring a safe and reliable fluid control system.
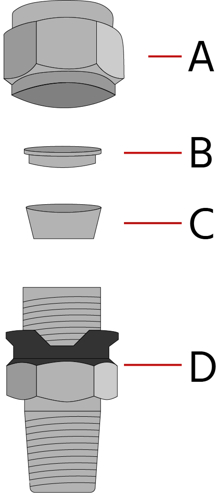
Figure 3: Double ferrule fitting anatomy: compression nut (A), back ferrule (B), front ferrule (C), and fitting body (D)
Single ferrule vs double ferrule fittings
-
Design and working: As already discussed, single ferrule fittings have one ferrule, while double ferrule fittings consist of two ferrules. This difference in design influences their applications and performance.
- In a single ferrule fitting, the ferrule is forced into the tubing material as the nut is tightened, creating a seal and a grip on the tube. However, this design may cause some deformation to the tube.
- In a double ferrule fitting, the front ferrule creates the seal, and the back ferrule provides the grip. As the nut is tightened, the front ferrule is pushed into the fitting body, forming a strong seal. Simultaneously, the back ferrule is forced against the tubing, creating a firm grip. This two-ferrule system distributes the mechanical load and reduces the chance of deformation.
-
Operating pressure:
- Single ferrule fittings are typically used for low-pressure applications up to 344 bar (5000 psi).
- With their two-ferrule system, the double ferrule fittings distribute the pressure evenly, ensuring a better seal and grip, making them suitable for high-pressure applications (up to 689 bar or 10,000 psi). However, the pressure resistance may vary based on the material and design.
-
Vibration resistance:
- The single ferrule has a compressed, lightweight back-end grip, which effectively isolates the seal point on the front end of the ferrule. This helps dampen vibration, allowing any vibration to flow from the back of the ferrule through the nut/body of the assembly. Due to this, single ferrule fittings excel in applications where vibration is a concern.
- Vibration can impact the double ferrule fitting seals. The non-isolated grip of the back ferrule can experience concentrated stress. Therefore, double ferrule fittings may not be suitable in vibration and pulsation applications.
- Reusability: Single ferrule fittings may not be as reusable as double ferrule fittings. The double ferrule design allows for the reusability of its parts, which extends the life of the fitting.
- Sealing performance: Single ferrule fittings can provide an efficient seal but might not perform as effectively under fluctuating temperatures or pressures. With their two-ferrule design, double ferrule fittings provide a dynamic seal that can maintain its integrity under a wider range of conditions.
- Cost: Single ferrule fittings are generally less expensive than double ferrule fittings. However, one must also consider the potential costs associated with leakage, maintenance, and replacement, which might be higher for single ferrule fittings, especially in high-pressure or high-vibration applications.
-
Applications:
- Single ferrule fitting: Suitable for water treatment, pneumatic applications, instrumentation, and control systems, and plumbing and heating systems.
- Double ferrule fittings: Ideal for high-pressure environments, used in the oil and gas industry, chemical processing, laboratory and research applications, semiconductor manufacturing, and aerospace and aviation.
Table 1 compares single and double ferrule fittings to help the user make an informed decision for an application.
Table 1: Single ferrule vs double ferrule fittings
Feature | Single ferrule fitting | Double ferrule fitting |
Design | One ferrule | Two ferrules |
Working | The ferrule is forced into the tubing as the nut is tightened. | The front ferrule creates the seal, back ferrule creates the grip |
Operating pressure | Suitable for low-pressure applications (up to 344 bar) | Suitable for high-pressure applications (689 bar) |
Vibration resistance | Good | Slight disadvantages in applications involving pulsation and vibration. |
Reusability | May not be reusable | Parts are reusable, extending the fitting's life |
Sealing performance | Effective seal, but may not perform as effectively under fluctuating conditions | Dynamic seal maintains integrity under a wider range of conditions |
Cost | Less expensive | Higher initial cost but potential savings in maintenance, leakage, and replacement |
Applications | Water treatment, pneumatic applications, Instrumentation and control systems, plumbing and heating systems | Ideal for high-pressure environments, used in the oil and gas industry, chemical processing, laboratory and research applications, semiconductor manufacturing, and aerospace and aviation. |
Conclusion
While single ferrule fittings might be suitable for low-pressure applications, less demanding environments, and situations where cost is a significant factor, double ferrule fittings might be more appropriate for high-pressure applications or where superior sealing performance and reusability are required. The decision should be made considering the specific requirements of the application.
FAQs
What is the purpose of ferrule?
The purpose of a ferrule is to create a strong, leak-proof seal between the fitting and the tubing or pipe in various applications like plumbing and instrumentation.
What is the difference between single ferrule and double ferrule fittings?
Single ferrule fittings have one ferrule (compression ring), while double ferrule fittings have two ferrules (front and back) for better seal and leak-tight connection.