Pneumatic Lubricator
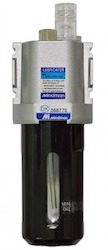
Figure 1: A pneumatic lubricator
An air lubricator provides needed lubrication to moving components in a pneumatic tool. Without lubrication, most air tools will quickly stop working and likely take damage. However, most modern pneumatic systems are self-lubricating, meaning they don't require an individual lubricating unit. Therefore, it is important to know the system and component requirements to see if an individual lubricating unit is needed. A pneumatic system can use just a compressed air lubricator or a lubricator that is part of a filter, regulator, lubricator (FRL) unit. This article discusses the design and function of pneumatic lubricators, the different types, their applications, and how to install them in a pneumatic system. Read our pneumatic tool oil article for more details on the importance of oiling pneumatic tools
Table of contents
- Pneumatic lubricator design and operation
- Types of pneumatic lubricators
- How to install an air lubricator in a pneumatic system
- What kind of oil is in a pneumatic lubricator?
- Are pneumatic lubricators necessary?
- FAQs
View our online selection of filters, regulators & lubricators!
Pneumatic lubricator design and operation
A pneumatic lubricator’s design allows it to fit in a pneumatic system directly upstream of an air tool. This way, the compressed air is immediately lubricated before it enters the tool. A pneumatic lubricator has the following components:
- Oil adjusting valve: The oil adjusting valve controls how much oil drops into the compressed air moving through the regulator.
- Sight feed: The sight feed allows users to see how much oil drops into the compressed air. This is necessary for the user to ensure the air remains lubricated. Without lubrication, the air tool will quickly fail.
- Bleeder assembly: Excess air from the inlet flows out of the bleeder assembly.
- Lubricator cap: The lubricator cap allows access to the oil reservoir to refill it. This can happen during operation.
- Capacity valve: Air flows through the capacity valve. This valve opens proportionally to the air flow. If the air flow increases, the valve also controls an increase in oil dripping into the valve.
- Body: Air lubricators’ bodies are typically aluminum, die-cast zinc, PA 66 (Nylon 66), or stainless steel. See our chemical resistance of materials guide to learn more about in which environments these various materials are suitable.
- Siphon tube: The siphon tube siphons oil from the reservoir to the sight feed.
Operation
A pneumatic lubricator adds small drops of oil to an airstream. When air moves through the lubricator, a portion diverts to apply pressure on the oil in the reservoir. The air also opens the capacity valve, which creates a differential pressure to siphon the oil from the siphon tube. The capacity valve also atomizes the air and oil to create the lubricated mist that flows into the air tool.
Types of pneumatic lubricators
Three general types of pneumatic lubricators are sight-feed, wick-feed, and single-point.
Sight-feed lubricators
The previous section discusses a sight-feed regulator. The primary benefit of this type of lubricator is that a user can refill it during operation.
Wick-feed lubricators
Wick-feed lubricators have a porous bronze wick in the oil reservoir. Oil moves up the wick via capillary action. The air flow takes oil off the top of the wick to maintain a consistent oil-to-air ratio. The system needs to be shut off before refilling a wick-feed lubricator.
Single-point lubricators
Single-point lubricators apply oil to a pneumatic system at the exact place that needs oil. The lubricator applies a consistent amount of oil. A single-point lubricator may be the best option if oil mist lubricators are not properly lubricating the air tool.
Read our article on how to oil pneumatic tools for more details on how and when to oil pneumatic tools.
How to install an air lubricator in a pneumatic system
An air lubricator in a pneumatic system goes right before the pneumatic tool and after the air filter and regulator if either is in the system. If multiple air tools in the system use the same type of lubricant, then the lubricator goes right before the line splits for each tool. Use the following guidelines to properly install a pneumatic lubricator:
- Shut off compressed air to the in-line pneumatic system.
- Inspect the air lines to ensure they are free of corrosion, damage, or other flaws.
- Use the manufacturer’s installation directions to attach the air lubricator to the line. When attaching, use fittings the manufacturer recommends to avoid injury to operators and machinery.
- Determine how other components in the system will react to the oil. For example, steel and copper react differently than rubber or plastic. When choosing o-rings and gaskets, consider their resistance to lubricant.
- After installation, test the system for leaks to eliminate air pressure or oil loss.
- If using a sight-feed or single-point pneumatic lubricator, and if necessary, adjust the drip rate for optimal performance.
What kind of oil is in a pneumatic lubricator?
The downstream equipment that a lubricator must supply oil to determines which type of oil to use. Check with the manufacturer of a pneumatic lubricator to determine which type of oil(s) is suitable for that specific lubricator. The oil will likely be one of the following:
- Air tool lubricating oil
- SAE 30 or lower machine oil
- 3-in-one oil (SAE 20)
- Mineral oil
- Food-grade air tool lubricant
- Automatic transmission fluid
- Hydraulic fluid
Are pneumatic lubricators necessary?
Most modern pneumatic systems are self-lubricating, so lubricator units are not always required. Use a pneumatic lubricator only if you intend to use a pneumatic product that needs internal lubrication, otherwise, it can wash away the existing self-lubrication, cause poor system performance, and increase costs. It is also important to only use the lubricator for specific components that require it and not the entire pneumatic system. Always refer to the manufacturer’s manual to verify whether the product needs external lubrication.
FAQs
What is the function of a pneumatic lubricator?
Pneumatic lubricators provide oil to air tools to ease friction, reduce heat and noise, and improve performance.
Is an air compressor oiler necessary?
How often a pneumatic tool is used determines whether or not a pneumatic lubricator is necessary. For example, a nail gun may not need a lubricator, whereas a pneumatic rivet tool may.