Air Compressor Automatic Drain Valve
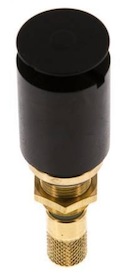
Figure 1: Float-activated automatic drain valve
An air compressor automatic drain valve is designed to periodically remove accumulated condensate, oil, or rust from the compressed air system. These valves function without manual intervention, opening, and closing based on specific parameters, such as pressure, level of condensation, or via a timer. This article explores the operation and installation of air compressor automatic drain valves.
Table of contents
- Automatic drain valve for air compressors
- Operation
- Choosing the right automatic drain valve
- Air loss
- Installation
- Determining when to drain the condensate
- FAQ
View our online selection of drain valves!
Automatic drain valve for air compressors
Compressed air contains water and moisture in condensed form. The accumulated condensate should be emptied regularly; otherwise, it can lead to the failure of downstream components.
Automatic drain valves open and close periodically, allowing the accumulated liquid and debris to be expelled from the system. These valves eliminate the need for regular manual intervention, reducing maintenance efforts and enhancing system efficiency. Certain models have a manual flush button to drain excess condensation if required. Automatic drain valves are more suitable for air compressors where:
- The filter location is difficult to access for servicing.
- The equipment is continuously used, and stopping it for manual draining is not feasible.
- Applications where large quantities of water can accumulate over short periods.
Operation
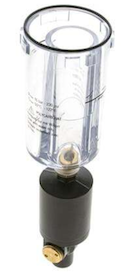
Figure 2: Plastic bowl (reservoir) for an externally fitted automatic drain valve
Automatic drain valves can be operated on a timer control or be triggered by a sensor or float that detects the liquid level in the system.
- Condensate flow: The condensate, collected in the compressed air system, flows into the valve's condensation reservoir or bowl. This bowl can be an integrated part of the drain valve or a separate component (Figure 2).
-
Control mechanism: Common control mechanisms include:
- Timer-based valves: Timer-based automatic drain valves discharge condensate by opening at regular intervals set by an adjustable timer. They can be adjusted to allow the desired draining frequency. However, these valves are not ideal for applications with variable condensate accumulation as the drain intervals are fixed, regardless of actual condensate levels.
- Float-based valves: Level-sensing automatic drain valves open when the liquid level reaches a certain threshold and close when it drops below that level. They offer more responsive and accurate drainage as they react to actual condensate levels. Level-sensing valves are well-suited for applications with varying condensate generation. However, they are more complex and expensive than timer-based valves. Also, they require proper calibration to ensure accurate level detection and additional maintenance due to float mechanisms.
- Electronic-controlled drain valves: Electronic-controlled automatic drain valves use sensors to detect condensate levels and control the opening and closing of the valve electronically. They can be programmed for specific drainage cycles or conditions and provide precise and customized control based on real-time condensate levels. Electronic-controlled valves are suitable for applications with varying condensate accumulation. However, they are more expensive than timer-based or level-sensing valves. Also, they require an electrical power supply and potential integration with control systems.
- Pneumatic piston and valve opening: The outlet design for letting the condensate out varies depending on the automatic drain valve model. For example, in a float-based automatic drain valve, as the condensate rises in the reservoir, the float (Figure 3 labeled A) is pushed upwards, allowing air to reach the top of the piston (Figure 3 labeled E) and causing the piston to move downwards. This opens the aperture at the o-ring (Figure 3 labeled D) for draining the condensate.
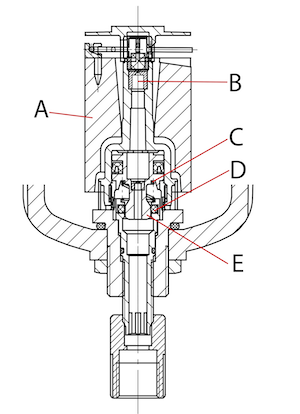
Figure 3: Main parts of a float-operated drain valve: Float (A), nozzle (B), pressure spring (C), o-ring (D), and piston (E)
Choosing the right automatic drain valve
Consider the following factors when selecting an automatic drain valve for the air compressor:
-
Drain valve type: Selecting the suitable model for the automatic drain valve depends on equipment compatibility and operating requirements.
- Choose a float-operated drain valve if the compressor is not located near a power source.
- Choose timer-based or float-based valves if the condensate accumulation is relatively constant.
- If the application needs precise control over the draining process or wants additional features like alarms or fault detection, choose a sensor-based valve.
- If the condensate contains debris or contaminants that can interfere with float mechanisms, choose a sensor-based valve that relies on conductivity or capacitive sensors.
- Operating pressure and temperature: Choose a drain valve that can handle the operating pressure and temperature of the system.
- Connection size and type: Choose a drain valve with the appropriate connection size and style (threaded or flanged) for easy and secure installation in the system.
- Cost: Timer-based and float-based valves are generally more affordable than sensor-based valves.
Comparing different automatic drain valves
- Timer-based: Timer-based drain valves have a simple installation, are cost-effective, and are suitable for applications with relatively consistent condensate generation. However, they may not respond to varying condensate levels, potentially leading to insufficient drainage or unnecessary discharges.
- Float-based: Float-based automatic drain valves automatically drain when condensate reaches a certain level, conserving energy and reducing unnecessary draining. However, the mechanical components in a float-based drain valve may require maintenance and can be susceptible to debris or corrosion, affecting reliability.
- Sensor-based: Sensor-based valves are precise and efficient and respond to actual condensate levels or system conditions, reducing the risk of insufficient drainage or wasteful discharges. But, they have a high initial cost due to the complexity of the sensing technology but provide better control and optimization.
Air loss
Air loss in an automatic drain valve is the unintended release of compressed air during drainage. Air loss results in energy wastage and increased operating costs, as it consumes compressed air that could otherwise be utilized for productive purposes.
The type of automatic drain valve used can significantly impact the amount of air loss in the system.
- Float-type drain valves usually have minimal air loss, as they only open when the condensation level reaches a certain point.
- Timer-based drain valves can cause more significant air loss as they open at preset intervals, regardless of the condensation level.
- Electronic sensing drain valves can minimize air loss by only opening when the sensor detects moisture, ensuring the valve remains closed when not needed.
Zero-loss drain valve
Zero-loss drain valves prevent air loss in compressed air systems. Unlike regular electronic sensing drain valves that directly open the valve to discharge condensate, zero-loss auto drain valves incorporate a multi-step process to achieve zero air loss.
- A reservoir collects liquid (condensate) from a compressed air system that triggers a switch when the liquid level in the reservoir reaches a certain point.
- The switch sends a small amount of pilot air to an air cylinder.
- The air cylinder, in turn, opens a valve to let the liquid drain out.
- The switch detects the dropping liquid level and stops sending pilot air.
- When the pilot air stops, the valve closes, preventing any more liquid from draining. This process repeats as needed to remove condensation without wasting any compressed air.
Installation
Automatic drain valves are typically installed at critical points within the compressed air system where condensate is likely to accumulate, like the air receivers or storage tanks, filters, separators, air compressor outlets, or the downstream equipment. The exact location and number of automatic drain valves installed depend on the specific configuration and needs of the compressed air system. Here's a general guideline for the installation steps:
- Choose the right drain valve: Determine the appropriate automatic drain valve for the air compressor drain valve based on operating pressure, temperature, and voltage. Also, fix the type of drain valve depending on the application.
- Shut off the compressor: Before installing the valve, turn off the air compressor and disconnect it from the power source to ensure safety.
- Release air pressure: Open the existing manual drain valve or any other release valve to release residual air pressure from the compressor and air tank.
- Use thread sealant: Apply a suitable thread sealant, such as Teflon tape or pipe dope, on the threads of the automatic drain valve to prevent air leaks. Also, if a manual drain valve is already in place, remove it using a wrench and prepare the connection point for the automatic drain valve installation.
- Install the valve: Thread the automatic drain valve into the connection point, and tighten it using a wrench. Ensure it is securely in place but avoid over-tightening, which may damage the threads.
- Connect power supply: If the automatic drain valve requires an external power supply, connect it to the appropriate voltage source per the manufacturer's instructions. For a timer-controlled valve, set the desired open and close intervals.
- Test the installation: Reconnect the power supply to the air compressor and turn it on. Allow the system to build pressure and observe the automatic drain valve functioning during its drainage cycle. Check for any leaks or issues during operation.
- Maintenance: Inspect and clean the automatic drain valve after installation to ensure proper functionality and prolong its service life.
Determining when to drain the condensate
A timer-based automatic drain valve discharges the condensate based on the interval it is set to. Consider the following factors to determine the optimal interval for draining the compressor.
- Compressor usage: The more frequently and longer the compressor is used, the more moisture it generates, necessitating shorter drain intervals.
- Ambient conditions: Humid climates and high temperatures increase condensation in the compressor, requiring more frequent draining.
- Compressed air quality requirements: Applications that demand high-quality, dry compressed air may need shorter draining intervals to maintain the desired air quality.
- Type of air compressor: Certain compressors, such as rotary screws and centrifugal compressors, have built-in cooling and air treatment systems, resulting in less moisture buildup and longer drain intervals.
- Presence of an air dryer: If the system includes an air dryer, it may reduce the amount of water in the compressed air, allowing for longer intervals between draining.
- Manufacturer's recommendations: Consult your air compressor manual for guidelines on draining intervals suggested by the manufacturer.
As a general starting point, users drain their compressors daily or after each use. However, monitoring the specific system and adjusting the draining intervals is essential. In the case of an automatic drain valve with a timer, you can set the open and close intervals based on your observations and the factors mentioned above. Begin with a conservative interval (e.g., every 2-4 hours) and adjust as needed by monitoring the amount of moisture expelled during each drain cycle. Set an appropriate 'on' duration (e.g., 5-10 seconds) for the valve to ensure sufficient time to expel the accumulated liquid.
FAQs
How do I select the right type of automatic drain valve for my air compressor?
Consider factors such as compressor size, operating pressure, condensate load, and environmental conditions. Additionally, evaluate the types available, such as electronic, timed, or float-type drains, to determine the best fit for your specific needs.
What are the benefits of using an automatic drain valve for my air compressor?
An automatic drain valve helps prevent moisture buildup, which can lead to corrosion and damage to the downstream equipment. It also ensures consistent air quality, improves compressor efficiency, and reduces maintenance requirements.