How To Actuate a Diaphragm Valve
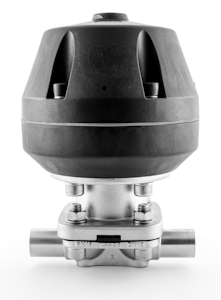
Figure 1: A diaphragm valve with a pneumatic actuator
Diaphragm valves can be actuated manually or automated (electric, pneumatic, or hydraulic) allowing them to be used in a wide array of applications. Understanding these actuation methods for chemical processing or biotechnology is critical to optimizing valve performance and system longevity.
Diaphragm valve overview
A diaphragm valve uses a flexible diaphragm to open, close, or partially obstruct a pathway for fluid. The diaphragm can be made from various materials such as rubber, plastic, or metal. This valve type is distinguished by its operation method and its unique advantages. Learn more in our diaphragm valve overview article.
The primary advantages of diaphragm valves are:
- Leak-proof seal
- Corrosion resistance
- Minimal contamination
- Ease of maintenance
- Versatility
Common applications for diaphragm valves are:
- Chemical processing
- Water treatment
- Food and beverage
- Pharmaceuticals
- Biotechnology
View our online selection of diaphragm valves!
Manual diaphragm valve
Manual actuation, involving direct manipulation of diaphragm valves through a handwheel or lever, stands out as the most straightforward operation method. This approach is reliable and simple, making it an ideal choice in scenarios where direct intervention and uncomplicated mechanisms are favored. The process works by the user turning the handwheel or moving the lever, which in turn moves the diaphragm to regulate the flow of fluid. Despite its simplicity, this manual method allows for precise control over the valve, rendering it versatile for various settings, from laboratory environments to industrial processes.
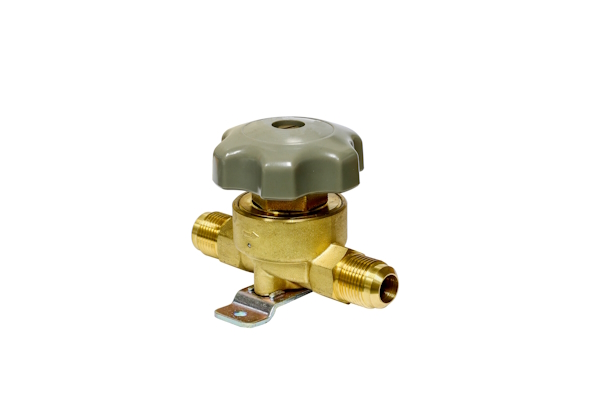
Figure 2: A diaphragm valve with a manual actuator
Electric diaphragm valve
Electric actuation controls the opening and closing of diaphragm valves through the use of electric motors, a method appreciated for its precision and the capacity to automate valve operations, seamlessly integrating into advanced control systems. In this process, the electric motor activates the valve mechanism, adjusting the diaphragm's position to regulate fluid flow. This versatility allows for operation under different voltages and offers options for remote control and feedback, making electric actuators perfectly suited for scenarios that demand exact flow regulation or where manual handling is impractical due to accessibility or safety issues.
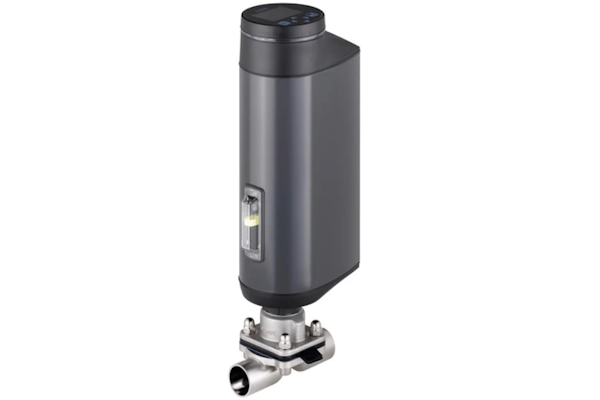
Figure 3: A diaphragm valve with an electric motor for actuation
Pneumatic diaphragm valve
Pneumatic actuation uses compressed air to open or close the diaphragm valve. This method is well-known for its efficiency and swift response time, making the air-actuated diaphragm valve exceptionally suitable for applications that require fast actuation and high cycling rates. The process involves directing compressed air into the actuator, which then applies pressure to move the diaphragm and thus control the flow of fluid through the valve. Pneumatic actuators are particularly advantageous in hazardous environments due to their lack of spark risk and explosion-proof nature, offering a safe and effective solution for controlling fluid flow in critical settings.
Hydraulic diaphragm valve
Hydraulic actuation, based on fluid dynamics, uses pressurized fluid to actuate the valve, with the actuator converting this fluid pressure into mechanical motion to open or close the valve. This method is known for its high power density and capacity to exert significant force, ideal for controlling large valves or in high-torque conditions. Hydraulic actuators maintain valve position without needing continuous power, enhancing reliability and energy efficiency. Such systems are favored in water treatment, oil and gas pipelines, and other sectors where durability and dependability are essential.
Selecting an actuator for a diaphragm valve
Choosing the right actuation method for a diaphragm valve is crucial for ensuring optimal performance, efficiency, and longevity of the valve system. The selection process involves considering several key factors that influence the suitability of each actuation type for specific applications. Below are guidelines to help in making an informed decision:
-
Evaluate the operating environment
- Consider the presence of hazardous materials or explosive atmospheres, where pneumatic actuation might be preferred due to its inherent safety features.
- Assess the availability of power sources; electric actuators require electrical power, whereas pneumatic and hydraulic systems need compressed air or fluid power, respectively.
-
Understand the application requirements
- Determine the need for precision and control. Electric actuators offer precise control and are suitable for applications requiring accurate flow regulation.
- Consider the speed of operation. Pneumatic actuators provide rapid response and are ideal for systems requiring quick actuation.
- Evaluate the force or torque requirements. Hydraulic actuators deliver high force and are suitable for large valves or applications requiring significant power.
-
Consider system integration and control
- Assess the compatibility with existing control systems. Electric actuators can be easily integrated into automated control systems for remote operation and monitoring.
- Determine the need for manual override. Some applications may benefit from manual actuation as a backup in case of power failure or for maintenance purposes.
-
Analyze maintenance and operational costs
- Consider the maintenance requirements. Manual actuators have lower maintenance needs compared to other types, which may have more complex mechanisms.
- Evaluate the total cost of ownership, including initial costs, maintenance, and operational expenses. Electric actuators may have higher initial costs but can offer savings through precise control, which leads to reduced energy consumption.
-
Assess installation constraints
- Consider space limitations. Pneumatic and hydraulic actuators may require additional equipment (e.g., air compressors or hydraulic pumps), which can increase the space needed for installation.
- Evaluate the environmental conditions, such as temperature and humidity, which can affect the performance and durability of certain actuator types.
FAQs
How does an automatic diaphragm valve work?
An automatic diaphragm valve operates without manual intervention, typically controlled by electrical, pneumatic, or hydraulic signals.
Can you manually operate a diaphragm valve?
Yes, a manual diaphragm valve is operated by hand using a wheel or handle to control flow.
What are the advantages of an electric diaphragm valve?
Electric diaphragm valves offer precise control and are suitable for applications requiring automated operation with electrical signals.