Electric Valve Actuator - How They Work
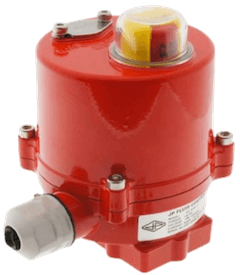
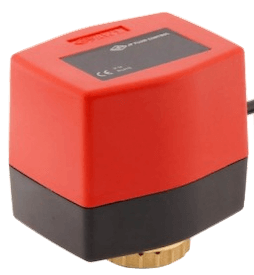
Figure 1: JP fluid control AG series (left) and AW series (right) electric valve actuator
Electric quarter-turn valve actuators are electro-mechanical devices designed to remotely operate quarter-turn valves, including ball and butterfly valves. They can be purchased as a package with the valve or separately to be installed on an existing quarter-turn valve.
Table of contents
- Electric valve actuator design
- Mounting
- Electric valve actuator features
- Electrical wiring
- Standards
- Material
- Electric valve actuator applications
- Electric valve actuator selection criteria
- FAQ
View our online selection of electric valve actuators!
Electric valve actuator design
Electric actuators for quarter-turn valves are a type of rotary motorized valve actuators. Electric rotary actuators convert electric energy into rotary force, so a quarter-turn electric actuator can only turn 90 degrees. The electric motor generates torque, which is transmitted to turn the valve through an output drive. The motor voltage options are either AC (alternating current), DC (direct current), or they are able to operate on either one. The motor is housed in a robust, compact housing that also contains other components of the actuator such as gearings, limit switches, wiring, etc. The whole assembly is connected to a valve through a compatible connection interface, such as an ISO 5211 standard. Compared to their pneumatic and hydraulic counterparts, electric valve actuators provide a more energy-efficient, clean, and quiet method of valve control.
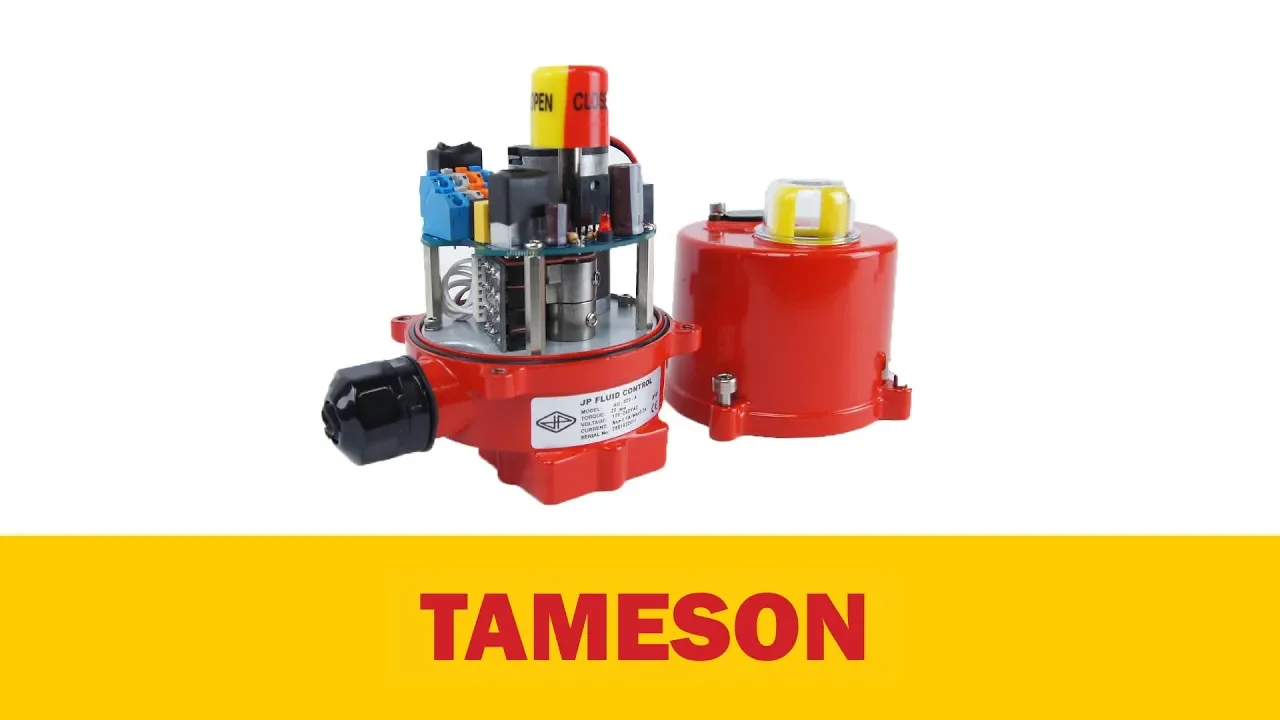
Torque
Quarter turn valves require a 90° turn to completely open or close. To turn the valve, torque (the rotational equivalent of linear force) is required. The electric actuator generates this torque and transmits it to its output shaft, which is then connected to the valve’s stem, or shaft. This, in turn, rotates the valve’s ball or disc and opens or closes the orifice to allow flow through or block the flow. The amount of torque generated by an actuator is dependent on its gearing and motor capacity. The motor capacity (torque) is an important specification for the actuator as it needs to be higher than the valve’s required torque to ensure it can open and close the valve. Usually, the breakaway torque is specified as the required torque of a valve as this is the highest torque required to rotate the valve.
Breakaway torque
When a valve is in an open or closed position, the torque required to “break free from either of these positions is called the breakaway torque. In other words, this is the amount of torque required to cause a valve to initially move from a rest position. In general, the breakaway torque is higher than the run torque. For example, the breakaway torque for a general ball valve is around 30% higher than its run torque. Breakaway torque is higher due to it being from a static position, the media can build up in the ball cavity, and/or the media can scratch the valve seat causing an increase in friction, etc. A suitable quarter-turn valve actuator should generate a torque higher than the valve’s breakaway torque.
Response time
Response time is the time needed for an actuator to turn the valve a full 90 degrees (i.e. to fully open or close a valve after the command has been given). Like torque, the speed of an actuator is related to its gearing and the power of its motor. The torque and speed of an actuator are directly related as torque is inversely proportional to speed. This relationship is affected by gear arrangements. For a given actuator motor capacity, a higher gear ratio would result in more torque and a slower response time than a lower gear ratio. Therefore, if response time is a critical application specification it needs to be looked at with the torque specification requirement.
Control method
Common electric valve actuators have either 2-point control (commonly referred to as just on/off) or 3-point control, but they both have 3 wires.
Voltage
Electric actuators may be DC or AC-powered. They are usually available in the following voltage ratings: 12, 24, and 48V for direct current and 24, 48, 120, 130, 240V for alternating current.
Mounting
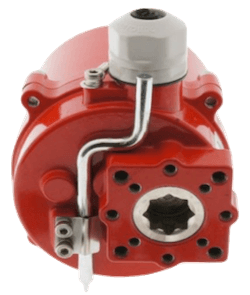
Figure 2: ISO 5211 flange type of JP fluid controls AG electric valve actuator
Quarter turn actuators have a connection interface that connects them to a valve. This comprises of an output drive, a shaft square or stem to connect the valve head, and a flange to bolt the actuator to the valve. The design and dimension of this connection interface may be brand-specific or standardized to standards such as ISO 5211. Examples of quarter-turn actuators with brand-specific connection interfaces are the AW1 series ball valve actuators by JP fluid controls. These valves are compatible with JP fluid controls' BW2 and BW3 valves. The AG quarter-turn actuator series, on the other hand, have a standardized ISO 5211 connection interface and are compatible with all valves with an ISO 5211 flange. Figure 2 below shows an ISO 5211 flange type. Regardless of brand, different valves and actuators can be interchanged as long they follow the same ISO 5211 standard. Under the ISO 5211 standard, there are different flange types that vary by maximum flange torque, dimension, and the number of screws, bolts, or studs.
Electric valve actuator features
Position indicators
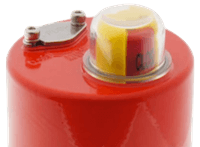
Figure 3: Valve position indicator on an electric valve actuator
Position indicators indicate the position, open or closed, of the actuator at a given time. There are visual indicators, such as in Figure 3, but there are also electric position feedback systems to send the position back to your system (i.e. controller). Position indicators have two basic switching options; mechanical switches and proximity (non-contact) switches. Mechanical limit switches are activated by internal cams on the output drive shaft. Mechanical switches might also be limit switches. Proximity switches are activated by sensors, which detect valve position. Position indicators may display only the basic on and off positions or also capable of indicating partly opened or partly closed.
Manual override
Manual override is a safety feature present in most actuators. It is usually a mechanical handwheel or handle. This wheel allows you to mechanically close or open a valve in case of power failure or any other emergency.
Limit switches
Limit switches are an electro-mechanical component of actuators. They consist of a close limit switch cam and an open limit switch cam. As the actuator moves a valve to the open or closed position, the corresponding switch cam moves. When an end position is reached, the corresponding switch cam cuts off electricity. Thereby preventing further movement and providing limit seating. Limit seating is the keeping of a valve in the desired end position. In certain actuators, the limit switch cams are adjustable. This allows you to set a position, like 75% open, as an end position. Limit switch cams can be incorporated into position indicators as a mechanical linkage between the valve and the actuator.
Duty cycle
The duty cycle specifies the usage time of an actuator between cycles. The valve opening and then closing makes one cycle. The duty cycle is a ratio of on-time to off time, expressed as a percentage. It is calculated using the formula below. An example would be if it takes an actuator 10 seconds to open, 20 seconds to close, then 30 seconds to rest after opening and closing, the duty cycle would be (10+20 / 10+20+30) × 100 = 50%.
(opening time + closing time) / (opening time + closing time + rest) × 100 = duty cycle
Fail-safe
Fail-safe is an important safety feature in some automated valve actuators. The fail-safe is designed to close or open a valve whenever there is a power failure. Such a system requires a form of energy storage, such as a spring mechanism or a battery. Typically, the fail-safe mechanism will close the valve. In a spring mechanism, a loaded spring automatically shuts off the valve when power is cut off. For a backup battery system, often called a battery safety return (BSR), a battery powers the actuator to close it. Depending on the battery and actuator size, charging time and the total amount of turns will vary. For extra redundancy, some actuators will have both versions of fail-safe incorporated into the design. As mentioned, most fail-safe operations will close the valve, but certain applications require the valve to open upon power failure. An example of such an application is the flow of cold water entering a heat exchanger. This is because cold water would be required to cool the remaining warm fluid, in order to prevent overheating.
Modulation
Certain electric valve actuators have the capability to carry out modulating control, which is often referred to as DPS (digital positioning system). This is the ability to accurately position the valve at any point between fully opened and fully closed (i.e. between 0° and 90°). This is necessary for applications that require the variation of flow rate. Typically, modulation is achieved using a control loop system and a positioning circuit board (PCB) placed in the actuator. To learn more about modulation, read our modulating valve article.
Electrical wiring
This section seeks to explain the various wiring possibilities for 2- and 3-point electric valve actuators as there are significant differences between the two.
- 2-point (on/off) control actuators: The three wires are for +, -, and a control wire. To rotate the valve, the control wire needs to be powered to open and un-powered to close or vice-versa. Without power supply to the entire unit, the valve remains in the latest position. For example, the AW1-R series from JP Fluid Control uses this open/close wiring scheme.
- 3-point control actuators: The three wires are for - and two for + (control wires). Therefore, the two control signals can open or close the valve depending on which one is powered. 3-point control also offers the ability for intermediate stops (partially open). The two control wires should never be powered at the same time, or damage will occur to the actuator. For example, the AW1 series from JP Fluid Control uses this 3-point wiring scheme.
Before installing, verify that the actuator code matches the connection diagram. Improper installation can permanently damage the actuator or lead to dangerous situations. The actuators have internal position switches, which results that only energy is consumed during opening or closing.
2-point AW1 DC electric actuator
Connecting the control wire (blue) opens the valve in 6s. Once the control wire shuts down the valve closes in 6s. The actuator only consumes energy during opening and closing.
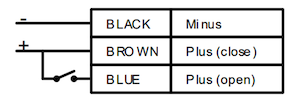
Figure 4: Wiring diagram for a 2-point DC electric actuator
3-point AW1 AC electric actuator
Connecting the blue control wire opens the valve in 16s. Connecting the brown control wire closes the valve in 16s. If both control wires are disconnected, the valve will remain In the current position. This way the position of the valve can be regulated. Never connect the blue and brown control wires at the same time, as this will damage the actuator. The actuator consumes energy only during opening and closing.
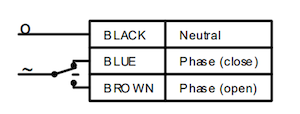
Figure 5: Wiring diagram for a 3-point AC electric actuator
2-point AW1 AC electric actuator
Connecting the control wire (black) opens the valve in 16s. Once the control wire shuts down the valve closes in 16s. The actuator consumes energy only during opening and closing.

Figure 6: Wiring diagram for a 2-point AC electric actuator
3-point AW1 DC electric actuator
By connecting the brown control wire the valve closes in 6s. Connecting the black control wire ensures the valve opens in 6s. If both control wires are connected, the valve will remain in the current position. In this way, the position of the valve can be regulated. Never connect the black and brown control wires at the same time! This will damage the actuator. The actuator consumes energy only during opening and closing.
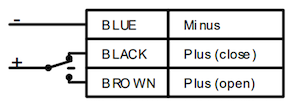
Figure 7: Wiring diagram for a 3-point DC electric actuator
Standards
IP protection grade (IEC 60529)
Electric valve actuators have a protection class IP (ingress protection) rating. The IP rating specifies the actuator''s degree of protection against dust, water, and other environmental hazards. The IP 54 rating of AW series ball valve actuators means that these actuators are partially protected from dust and can resist water spray.
Duty type (IEC 60034-1)
This is an international IEC (international electro-technical commissions) standard for rotating electric devices. For electric actuators, it specifies the duty type and duty cycle of their electric motors. An actuator rated S2 30min can continuously operate short-time duty for 30min after which the motor should be allowed to rest. It can be restarted after its temperature has returned to room temperature.
ATEX
ATEX directives specify what equipment can safely operate in an explosive atmosphere environment. An ATEX certification for an actuator means that the actuator is explosion-proof in a particular environment. See our flowchart to determine if you need an ATEX actuator or if you need further understanding of your ATEX label.
Low voltage directive (LVD) 2014/35/EU
The LVD certification ensures that low voltage electrical equipment, such as actuators, provides sufficient protection for its users.
Electromagnetic compatibility (EMC) 2014/30/EU
An EMC-certified actuator neither generates nor is affected by electromagnetic disturbance.
Material
The components on the actuator are contained in a compact housing. The most common housing materials are plastic and aluminum. Special applications may require special housing materials.
Electric valve actuator applications
Electric quarter-turn actuators are used to remotely control ball and butterfly valves. They greatly increase the ease of operating quarter-turn valves by providing remote, automated control. They also provide sufficient torque for valves that require higher torques than cannot be generated by a human. These actuators are used in industrial automation, irrigation, water supply, fluid dosing, heating systems, and fluid transportation or transfer.
Electric valve actuator selection criteria
- Torque
- Power
- Valve mounting compatibility
- Temperature
- IP rating
- ATEX requirement
- Fail-safe
- Modulation
- Duty type and duty cycle
FAQ
How to wire and install electric valve actuators?
Installation and wiring methods for electric actuators vary by model. However, detailed wiring and installation instructions for the AW and AG series actuators can be found here.