Vacuum Generators - How They Work
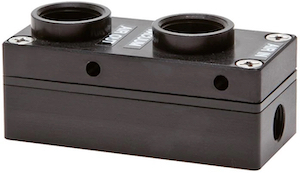
Figure 1: Vacuum generators
Vacuum generators are commonly used to create a low-pressure environment for a variety of industrial and scientific applications, for example, vacuum packing, distillation, filtration, and drying. They are essential in processes where air removal is crucial to maintain product integrity or enhance process efficiency. This article covers the working principles of pneumatic and electric vacuum generators, their pros and cons, and how to select between them.
Table of contents
- Types of vacuum generator
- Pneumatic vacuum generator
- Pros and cons of vacuum generators
- Vacuum generator applications
- Electric vacuum pump
- Pros and cons of vacuum pumps
- Vacuum pump applications
- Selection criteria
- FAQs
View our online selection of Vacuum Generators!
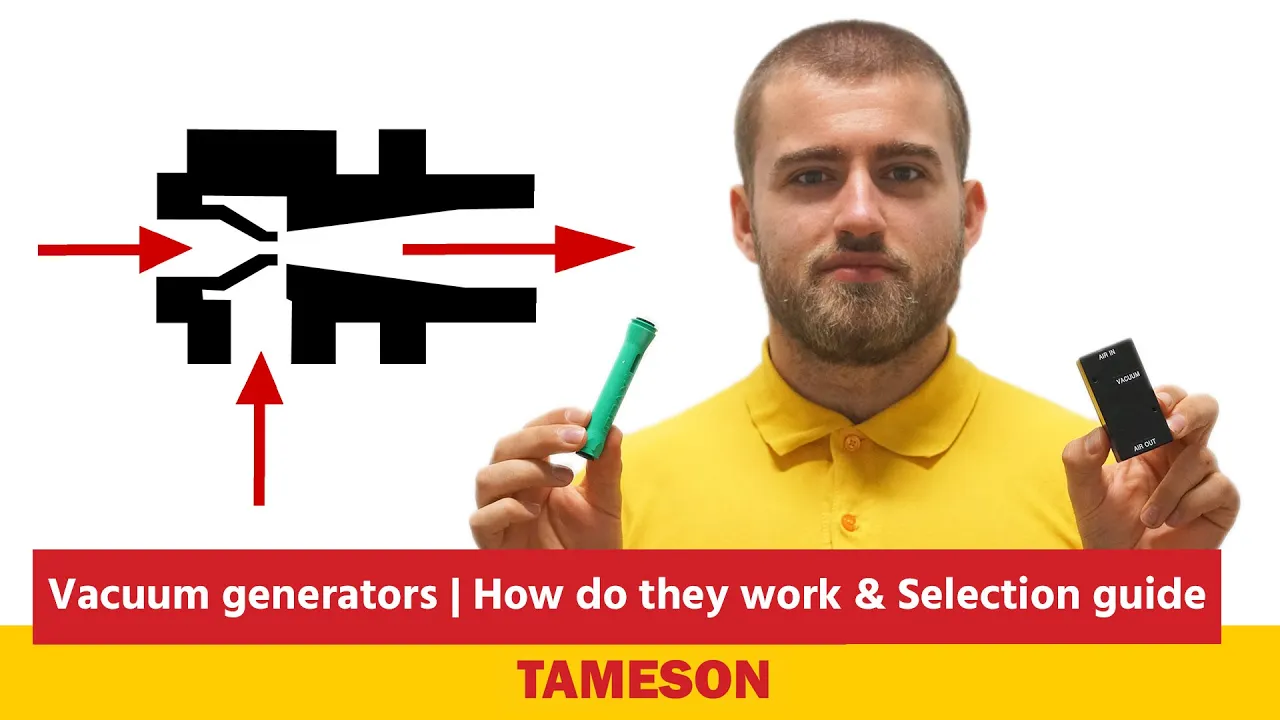
Types of vacuum generators
Vacuum generators are classified into two types: pneumatic vacuum generators (also called venturi vacuum generators) and electric vacuum pumps (also called electric vacuum generators).
Pneumatic vacuum generator
A pneumatic vacuum generator is a device that operates based on principles of fluid mechanics, specifically the Bernoulli's principle and the Venturi effect. It uses compressed air to create a low-pressure zone, which allows it to create a vacuum for various applications such as suction or filtration.
Pneumatic vacuum generator working principle
A pneumatic vacuum generator has an inlet port where compressed air enters. The air passes through a constricted space called the nozzle. The air's velocity increases due to the narrower cross-section, according to Bernoulli's principle.
The high-velocity stream of compressed air then passes through a diffuser, which has a gradually widening cross-section. The air's velocity decreases, causing its pressure to increase. This pressure increase leads to a low pressure zone adjacent to the nozzle and diffuser (Figure 2 labeled B).
The low-pressure zone can create a vacuum by connecting a suction cup or other suction device to a secondary inlet port that connects to the low-pressure zone (Figure 2 labeled A). The low-pressure zone causes atmospheric pressure to push the object towards the suction device, creating a suction force.
A pneumatic vacuum generator's operation depends on:
- the compressed air's flow rate
- the nozzle's diameter
- the diffuser's angle
- the shape and size of the secondary inlet port
Careful control of these factors can create an optimal low-pressure zone for a wide range of applications.
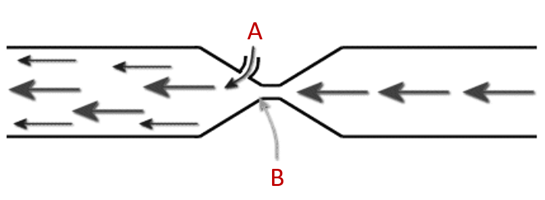
Figure 2: The working principle of a vacuum generator. Air moving through the nozzle accelerates and then decelerates on the opposite side. This causes a low-pressure zone to form (B), which leads to atmospheric pressure pushing air into the secondary inlet port (A), and creating a suction force that a suction device can take advantage of.
Single-stage
A single-stage vacuum generator has the basic operating principle discussed above.
Multi-stage
A multi-stage vacuum generator has multiple venturi nozzles (Figure 3 labeled A) arranged in a row. Compressed air enters through a connection port. As this air passes through the multiple venturi nozzles, low-pressure zones form, drawing air in through the inlet (Figure 3 labeled B). The inlet's suction capability is the sum total of suction force generated at each venturi nozzle's low pressure zone. Therefore, a multi-stage vacuum generator can provide a much higher suction rate for the same amount of compressed air than a single-stage vacuum generator.
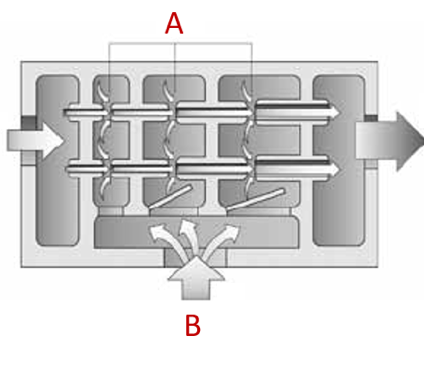
Figure 3: Multi-stage vacuum generator showing venturi nozzles (A) and inlet (B)
Single-stage vs multi-stage vacuum generators
The following factors help determine whether a single-stage or multi-stage vacuum generator is best for a given application:
- Applications: Multi-stage vacuum generators can lift heavier loads than single-stage vacuum generators. The former is more suitable for examples such as material handling in construction projects. The latter is more suitable for examples such as lifting electronic components or handling thin sheets of material.
- Vacuum level: A single-stage vacuum generator can produce a 1:1 compressed air to vacuum flow level. A multi-stage vacuum generator can produce above a 1:4 ratio.
- Power consumption: Multi-stage vacuum generators need less compressed air to create higher vacuum levels.
- Cost: Multi-stage vacuum generators typically cost more than single-stage generators.
- Maintenance: Multi-stage vacuum generators require more maintenance because they are more likely to clog than single-stage vacuum generators. Also, single-stage vacuum generators have a simpler construction and are easier to fix.
Compact
A compact vacuum generator has an integrated valve and system monitoring technology. These integrations give the ability to control suction without the use of an external valve that controls compressed air flow rate. Compact vacuum generators are most often used in completely automated handling systems.
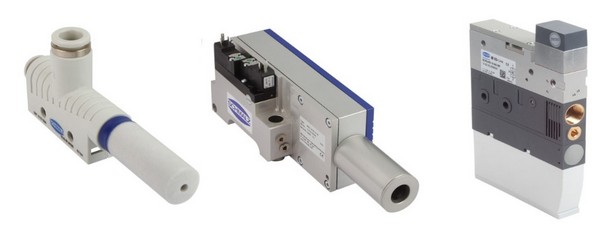
Figure 4: Single stage (left), multi-stage (middle), and compact vacuum generator (right).
Pros and cons of vacuum generators
Pros
- Vacuum generators are very compact and low-weight, which allows them to be installed close to the application.
- A vacuum is generated very fast.
- There are no moving parts, which results in low wear and practically no maintenance.
- No heat is generated.
- Relatively low initial investment.
Cons
- Compressed air must be available at the work site.
- Compressed air is relatively expensive, increasing the total cost of pneumatic vacuum generators over the long run.
Vacuum generator applications
Nearly any industry that uses pick and place robots will use vacuum generators in these robots. Some examples are feeder applications in the automotive industry and end-of-line applications such as food packaging.
Electric vacuum pump
Electric vacuum pumps, are used when high suction capacity is required or when compressed air is not available. Vacuum pumps operate by removing the air molecules from the vacuum chamber. It consists of an eccentrically mounted rotary impeller with carbon blades (Figure 5 labeled A). The impeller is pressed against the wall of the housing by the centrifugal force which provides an excellent seal. The size of each chamber (Figure 5 labeled B) changes with the rotation of the impeller. As the chamber becomes larger in size, the air inside it expands. This causes the pressure to drop in the chamber creating a partial vacuum. The air is thus drawn in, compressed, and expelled through the outlet. The high compression factor helps the vacuum pump generate a high vacuum and provide high suction capacity.
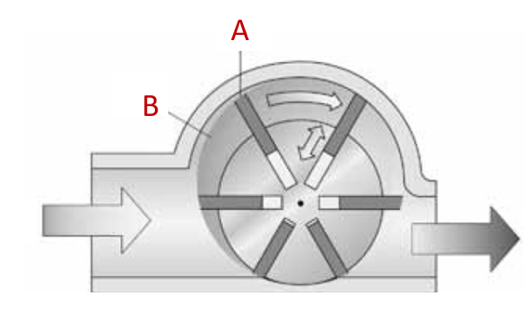
Figure 5: Vacuum pumps: carbon blades (A) and chambers (B).
Pros and cons of vacuum pumps
Pros
- Vacuum pumps can create a very high suction force.
- One vacuum pump can be used as a central location to generate a vacuum for multiple locations.
- Generally require little maintenance.
- No compressed air system is required.
Cons
- Vacuum pumps are more complex and larger than vacuum generators.
- Vacuum pumps require a higher initial investment.
Vacuum pump applications
Vacuum pumps are ideal for applications that require high suction forces or very low pressure. For example:
- Industrial processes: Vacuum pumps create low-pressure environments that are necessary for specific reactions or operations.
- Laboratory research: Distillation, filtration, and drying experiments require low-pressure environments.
- Printing industry: Vacuum pumps hold paper in place during the printing process.
Selection criteria
Selecting a pneumatic vacuum generator
- Suction rate
- Suction rate is usually given in m3/h, l/min, or cfm. The values are based on standard conditions, which means ambient temperature (20 °C) and ambient pressure at sea level (1013 mbar).
- Maximum suction rate is defined as the maximum flow rate that the vacuum generator evacuates from the environment.
- The required suction rate is a result of the internal volume of the suction pads and the piping. Furthermore, the handling of porous materials, such as cardboard, requires higher suction rates than air-tight materials. For these applications, a high suction rate is more important than a high vacuum level.
- Vacuum level
- The vacuum level is usually given as a percentage or relative value. The vacuum is specified in relation to the ambient pressure. A vacuum level of 80% means that the pressure is 80% lower than the ambient pressure. If the ambient air pressure is 1013 mbar absolute pressure (14.7 psi), an 80% vacuum means an absolute vacuum pressure of 202 mbar.
- Evacuation time
- Time in seconds that is required to create a specific vacuum level.
- Air consumption
- This is the consumption of compressed air (in l/min or scfm) by the generator to generate a specific vacuum level.
Vacuum generator vs vacuum pump
- Energy consumption: If a compressed air supply is unavailable but electricity is, use a vacuum pump.
- Application requirements: Pneumatic vacuum generators are suitable for applications that require low vacuum levels, typically up to 914 mbar. Lower vacuum levels may require a vacuum pump.
- Flow rate: Vacuum generators cannot provide as high of a flow rate as vacuum pumps.
- Maintenance: Pneumatic vacuum generators are easier to maintain than vacuum pumps.
- Cost: Pneumatic vacuum generators have lower upfront costs than vacuum pumps, but have higher long term costs due to the price of compressed air.
- Noise: Vacuum generators are quieter than vacuum pumps.
Read our vacuum suction cup article for more information on the operating principle and types of vacuum suction cups.
FAQs
Do vacuum generators require unlubricated compressed air?
We recommend unlubricated air. The reason is that dirt particles can settle in the vacuum generator and silencer when you use lubrication. This impairs the performance of the device.
What does a vacuum generator do?
Vacuum generators create a vacuum level that is required for lifting tasks.
How does an air vacuum work?
An air vacuum uses a Venturi nozzle to create a zone of low pressure that allows atmospheric pressure outside the vacuum to push air in through an inlet port, creating a suction force.
How do you make a vacuum with compressed air?
You can create a vacuum using a venturi nozzle. When the air flows through, the air is accelerated and compressed. After passing the constriction, the accelerated air expands, and a vacuum is created.