Pulse Jet Solenoid Valve - How They Work
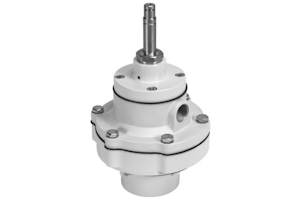
Figure 1: A pulse jet solenoid valve
Pulse valves are electromagnetic devices that rapidly release air bursts to clean filters in dust collector systems. They consist of a body, diaphragm, and solenoid coil, and are usually placed after the filter to reverse airflow and remove particles, enhancing efficiency and filter lifespan.
Pulse valve design
This section details the key components of pulse valves. Each part plays a crucial role in the efficient operation of the valve, ensuring effective filter cleaning through precise air pulse management.
- Body: The main structure that houses the internal components of the air pulse valve, typically made from durable materials like aluminum or stainless steel.
- Diaphragm: A pulse valve's diaphragm is a flexible membrane that separates the air supply from the outlet, moving up and down to open or close the valve.
- Solenoid coil: An electromagnetic coil that, when energized, moves the diaphragm to open or close the valve.
- Pilot valve: A small valve that controls the air flow to the diaphragm, assisting in the opening and closing mechanism.
- Spring: A component that returns the diaphragm to its original position when the solenoid coil is de-energized.
- Orifice: The opening through which the air pulse is released, its size affects the flow rate and pressure of the air pulse.
- Ports: Inlet and outlet connections for the air supply and the pulse air to the filters, respectively.
Pulse valve operating principle
Pulse jet valves are indirect operated solenoid valves that operate through a series of steps that ensure the efficient cleaning of filters in dust collector systems. Here is a step-by-step explanation of their operation:
- Solenoid energization: The process begins when the solenoid of the pulse jet valve is energized. This action causes the air trapped above the diaphragm within the valve to be quickly exhausted.
- Diaphragm opening: As the trapped air is released, a significant pressure difference is created across the diaphragm. This pressure difference forces the diaphragm to move suddenly, opening the valve and allowing air to pass through for cleaning.
- Solenoid de-energization: After a brief period, the solenoid is de-energized. This change allows air to flow back into the chamber above the diaphragm through a small hole, aiming to balance the pressure on both sides of the diaphragm.
- Valve closure: With the pressure balanced, the diaphragm moves back to its original position, instantly closing the valve. This rapid closure prevents the loss of compressed air and ensures that the cleaning pulse is short and powerful.
- Rapid actuation: The key to effective filter cleaning and economical compressed air usage lies in the rapid opening and closing of the valve. This is achieved by designing the moving parts of the valve, such as the diaphragm, to be lightweight, minimizing inertia and allowing for quick actuation.
- Achieving maximum flow rate: The valve is designed to reach its maximum flow rate when the air velocity through it becomes sonic (344 m/s). This design consideration ensures that the valve operates at optimal efficiency, providing the best possible cleaning performance.
- High Kv values: The valve's design allows for substantial Kv values, indicating its ability to handle a high flow rate of air. High Kv values are crucial for efficient filter cleaning and for the conservation of compressed air, making the valve more effective and economical in operation.
Pulse valve applications
Dust collectors play a crucial role in maintaining clean air and operational efficiency in various industrial environments. They utilize advanced technologies, such as pulse jet solenoid valves, to ensure effective dust removal and continuous system operation. This section provides an overview of dust collectors and offers various industrial applications as examples.
Dust collectors overview
Dust collectors are systems designed to remove or recover solid pollutants from exhaust gasses. They typically include a blower, dust filter, filter cleaning system, and dust removal system. One effective type is the fabric collector, or baghouse, where dust accumulates on fabric bags. These bags are cleaned using a pulse jet method, where a high-pressure air blast enters the bag, dislodging dust. This method allows for continuous operation without interrupting the gas flow into the baghouse. Pulse jet solenoid valves control the cleaning process, ensuring efficient dust removal and maintaining airflow. See Figures 2 and 3 to learn more about the components and operation of a baghouse.
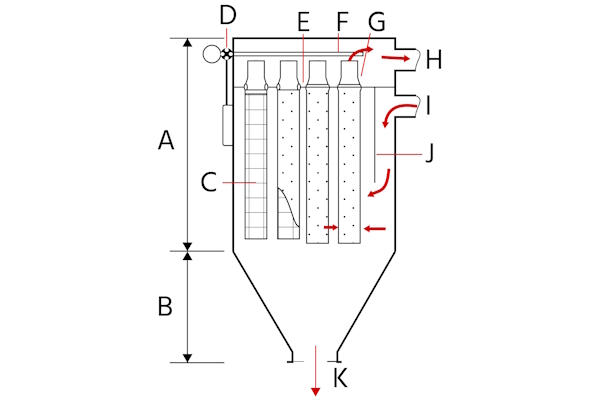
Figure 2: Typical pulse-jet baghouse with pulsing air supply: main housing (A), hopper (B), bag support cage (C), solenoid valve (D), tube sheet (E), compressed air manifold (F), venturis (G), clean gas (H), dirty gas (I), baffle plate (J), and collected solids (K).
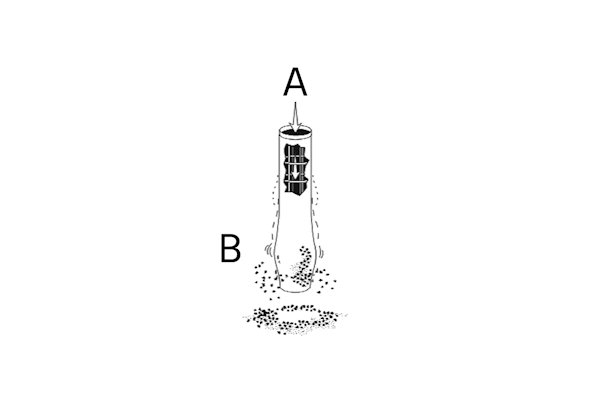
Figure 3: Tubular pulse-jet filter bag with pulsing air supply. The solenoid creates air pulses (A) which sends shock waves (B) through the filter bag.
Other applications
- Pneumatic conveying systems: Pneumatic pulse valves regulate the air shocks that move materials through pipelines efficiently.
- Air filtration systems: They clean filters by dislodging accumulated dust and debris, ensuring optimal air quality.
- Powder coating processes: Pulse valves control the release of powder in bursts for uniform application on surfaces.
- Grain and feed processing: They help in cleaning filters within the system, preventing blockages and maintaining airflow.
- Cement production: Pulse valves clear dust from filters to prevent buildup and ensure continuous operation of machinery.
- Foundry operations: They remove particulates from air filtration systems to maintain a clean working environment.
- Pharmaceutical manufacturing: Pulse valves ensure clean air filtration, critical for maintaining sterile conditions.
- Chemical processing: They prevent the accumulation of potentially hazardous dust in air filters, ensuring safety.
- Woodworking facilities: Pulse valves keep air filtration systems clear of wood dust, protecting machinery and workers.
- Metalworking and machining: They help in removing metal particles from air filters, preventing equipment damage and health hazards.
Selection criteria
Selection criteria for pulse jet valves include:
- Tank volume: The air volume in the supply tank determines the required valve size. A larger tank may require a valve that can handle higher volumes of air to ensure efficient cleaning.
- Tank pressure: This refers to the inlet pressure of the valve, which is influenced by the air pressure in the tank. It's crucial for matching the valve's capabilities with the system's needs.
- Max allowable pressure: The highest system or line pressure that the valve can safely sustain. This ensures the valve's integrity and safety during operation.
- Electrical pulse length: The duration the valve remains energized. Shorter pulses can reduce energy consumption, while longer pulses may be needed for thorough cleaning.
- Total pulse length: The interval from valve opening to closing. This affects the effectiveness of the cleaning process, with the optimal length varying based on system requirements.
- Peak pressure: The highest pressure achieved during the pulse, which generates the cleaning shock wave. This pressure dislodges particulates from filter surfaces.
- Pressure drop tank: The allowable pressure drop to maintain sonic flow, ideally not exceeding 50% of the absolute tank pressure. This ensures efficient airflow through the system.
- Performance ratio: The percentage ratio of tank pressure to peak pressure, influenced by valve Kv (flow coefficient) and opening time. A higher ratio indicates a more efficient valve performance.
- Volume per pulse: The air volume passing through the valve per pulse, affecting filter cleaning efficiency. Adequate volume ensures effective particulate removal.
- Material of construction: The choice of body and seal materials, critical for compatibility with the media. Common materials include aluminum, stainless steel, and nitrile for seals, selected based on the media's characteristics to ensure durability and reliability.
Festo VZWE pulse solenoid valves
Festo offers two primary types of pulse valves: angle pulse valves and flange pulse valves. Each type serves specific operational needs and comes with its own set of primary features.
- Angle pulse valves (Figure 4)
- direct mount on dust collector systems
- optimized flow paths for efficient dust removal
- durable diaphragms ensuring long service life
- easy to install and maintain
- suitable for a wide range of pressure applications
- FESTO VZWE flange pulse valves (Figure 5)
- designed for high-volume air flow systems
- flange connection for secure installation
- robust construction for heavy-duty applications
- extended lifespan with minimal maintenance
- compatible with various flange standards for versatility in installation
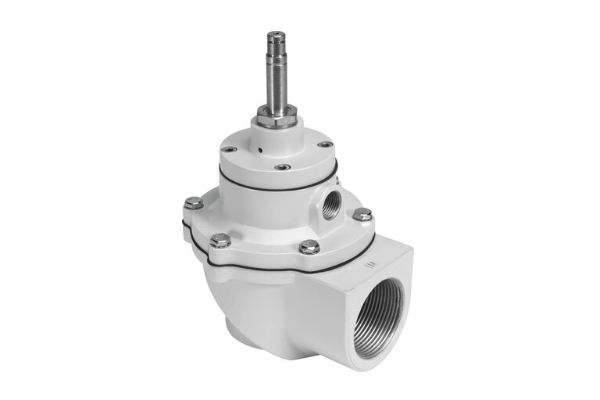
Figure 4: Festo's angle pulse valve
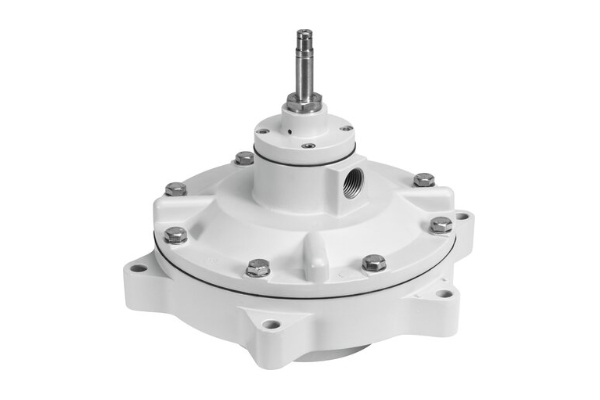
Figure 5: Festo's flange pulse valve
FAQs
What is a pulse valve?
A pulse valve is an electromagnetic valve that releases short bursts of air to clean filters in dust collector systems.
What is the purpose of an air pulse valve?
An air pulse valve dislodges accumulated particles from filter surfaces, enhancing filtration efficiency and prolonging filter lifespan.